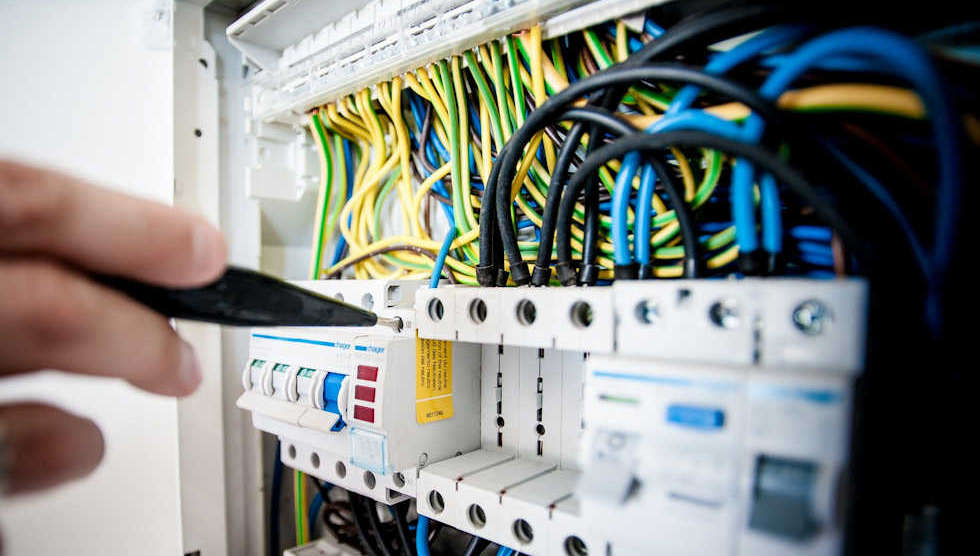
Given the number of articles on supply chain management published, it is difficult to know which ones are most popular. The topic is covered in a lot of academic research, so this is not an easy question. But, cocitation analysis can be used to narrow down the field. We were able to identify the most popular supply chain articles using the cocitation of a Supply Chain Management Association database. The International Journal of Supply Chain Management had the highest number of citations with 25,476. Based on the most cited article, the citations can be divided into five categories. The order of the articles is not predictable because International Journal of Supply Chain Management features a much higher number of citations that other journals.
Amazon's Supply Chain Practices Review is the most-cited article. This article links buyers to sellers and is often the most quoted. The goal of the review is to identify what works and not. The article provides some practical solutions and outlines the potential pitfalls and opportunities Amazon has.
Cross-sectional studies of supply chain risk and performance are the most popular. The study uses panel data and regression to assess the effect of supply risk on performance. The results are impressive. It is clear that supply chain risk management is the best approach to improving performance over the long term. This study has implications in other areas of corporate life like procurement and customer services.
Not all notable accomplishments of the same calibre are the most frequently cited. The Supply Chain Management Association database contains many publications. It's not surprising that the journals with the highest number of citations have the best. The International Journal of Supply Chain Management (the flagship journal of Supply Chain Management Association) has the highest number of citations with 25,476. This is more than double the tally of the Supply Chain Management Association's sister journal, the International Journal of Logistics Research and Applications.
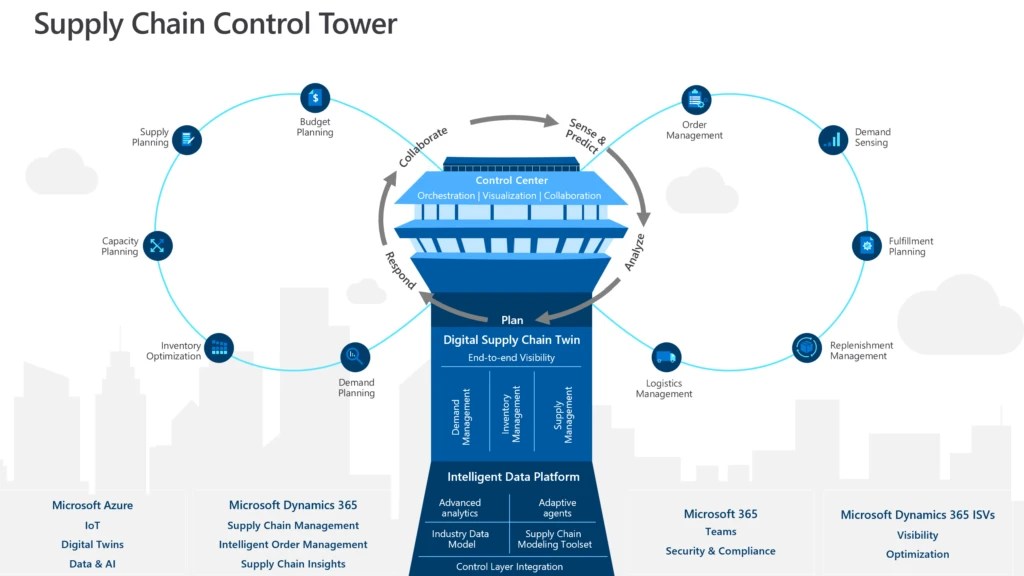
FAQ
What do we need to know about Manufacturing Processes in order to learn more about Logistics?
No. It doesn't matter if you don't know anything about manufacturing before you learn about logistics. It is important to know about the manufacturing processes in order to understand how logistics works.
What does warehouse mean?
A warehouse is a place where goods are stored until they are sold. You can have it indoors or outdoors. In some cases it could be both indoors and outdoors.
How can manufacturing overproduction be reduced?
It is essential to find better ways to manage inventory to reduce overproduction. This would reduce time spent on activities such as purchasing, stocking, and maintaining excess stock. We could use these resources to do other productive tasks.
This can be done by using a Kanban system. A Kanbanboard is a visual tool that allows you to keep track of the work being done. A Kanban system allows work items to move through several states before reaching their final destination. Each state is assigned a different priority.
If work is moving from one stage to the other, then the current task can be completed and moved on to the next. However, if a task is still at the beginning stages, it will remain so until it reaches the end of the process.
This helps to keep work moving forward while ensuring that no work is left behind. Managers can monitor the work being done by Kanban boards to see what is happening at any given time. This allows them to adjust their workflows based on real-time information.
Lean manufacturing can also be used to reduce inventory levels. Lean manufacturing emphasizes eliminating waste in all phases of production. Any product that isn't adding value can be considered waste. There are several types of waste that you might encounter:
-
Overproduction
-
Inventory
-
Packaging that is not necessary
-
Excess materials
Manufacturers can reduce their costs and improve their efficiency by using these ideas.
What is production planning?
Production Planning is the creation of a plan to cover all aspects, such as scheduling, budgeting. Location, crew, equipment, props and other details. This document is designed to make sure everything is ready for when you're ready to shoot. It should also contain information on achieving the best results on set. This includes information on shooting times, locations, cast lists and crew details.
First, you need to plan what you want to film. You may already know where you want the film to be shot, or perhaps you have specific locations and sets you wish to use. Once you have identified the scenes and locations, you can start to determine which elements are required for each scene. Perhaps you have decided that you need to buy a car but aren't sure which model. If this is the case, you might start searching online for car models and then narrow your options by selecting from different makes.
After you have selected the car you want, you can begin to think about additional features. Are you looking for people to sit in the front seats? Maybe you need someone to move around in the back. Maybe you want to change the interior color from black to white? These questions will help to determine the style and feel of your car. Another thing you can do is think about what type of shots are desired. You will be filming close-ups and wide angles. Maybe you want the engine or the steering wheels to be shown. These details will help identify the exact car you wish to film.
Once you've determined the above, it is time to start creating a calendar. You can use a schedule to determine when and where you need it to be shot. Each day will include the time when you need to arrive at the location, when you need to leave and when you need to return home. This way, everyone knows what they need to do and when. Book extra staff ahead of time if you need them. You should not hire anyone who doesn't show up because of your inaction.
When creating your schedule, you will also need to consider the number of days you need to film. Some projects take only a few days while others can last several weeks. You should consider whether you will need more than one shot per week when creating your schedule. Multiple takes of the same location will lead to higher costs and take more time. You can't be certain if you will need multiple takes so it is better not to shoot too many.
Budget setting is another important aspect in production planning. It is important to set a realistic budget so you can work within your budget. You can always lower the budget if you encounter unexpected problems. However, it is important not to overestimate the amount that you will spend. If you underestimate the cost of something, you will have less money left after paying for other items.
Production planning can be a complex process. However, once you know how everything works together it will become easier to plan future projects.
What is the difference between Production Planning and Scheduling?
Production Planning (PP) refers to the process of determining how much production is needed at any given moment. Forecasting demand is one way to do this.
Scheduling involves the assignment of dates and times to tasks in order to complete them within the timeframe.
Statistics
- Many factories witnessed a 30% increase in output due to the shift to electric motors. (en.wikipedia.org)
- Job #1 is delivering the ordered product according to specifications: color, size, brand, and quantity. (netsuite.com)
- (2:04) MTO is a production technique wherein products are customized according to customer specifications, and production only starts after an order is received. (oracle.com)
- You can multiply the result by 100 to get the total percent of monthly overhead. (investopedia.com)
- It's estimated that 10.8% of the U.S. GDP in 2020 was contributed to manufacturing. (investopedia.com)
External Links
How To
Six Sigma and Manufacturing
Six Sigma is defined as "the application of statistical process control (SPC) techniques to achieve continuous improvement." Motorola's Quality Improvement Department developed it at their Tokyo plant in Japan in 1986. Six Sigma's basic concept is to improve quality and eliminate defects through standardization. Many companies have adopted this method in recent years. They believe there is no such thing a perfect product or service. Six Sigma aims to reduce variation in the production's mean value. This means that you can take a sample from your product and then compare its performance to the average to find out how often the process differs from the norm. If this deviation is too big, you know something needs fixing.
Understanding the nature of variability in your business is the first step to Six Sigma. Once you have a good understanding of the basics, you can identify potential sources of variation. You'll also want to determine whether these variations are random or systematic. Random variations occur when people do mistakes. Symmetrical variations are caused due to factors beyond the process. If you make widgets and some of them end up on the assembly line, then those are considered random variations. You might notice that your widgets always fall apart at the same place every time you put them together.
Once you have identified the problem, you can design solutions. You might need to change the way you work or completely redesign the process. After implementing the new changes, you should test them again to see if they worked. If they didn't work, then you'll need to go back to the drawing board and come up with another plan.