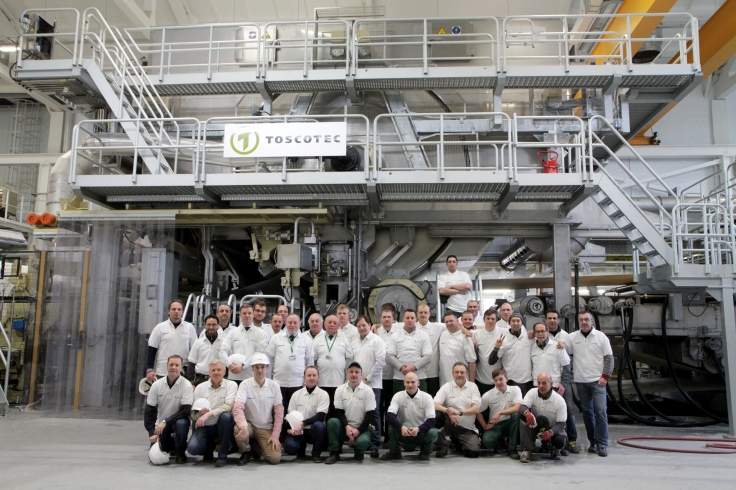
It can help improve your manufacturing processes. However, it is not an easy task. It involves mapping product family and products. To do it properly, your team needs training, and you might even have a value stream manager. Your team should get support from the leadership in order to successfully implement the strategy. Larger companies may have their own value stream managers to oversee the mapping process. While smaller businesses can work without a VSM manager for their mapping process, it can be advantageous to show leadership the improvement opportunities.
Lean Six Sigma
When you use Value Stream Mapping in Lean Six Sigma, you'll document the flow of information from customers to suppliers. Your customer should be the first thing on your value stream map. If you're in the shipping area, start there and work upstream. You should include a box containing the customer's information. This will give you an idea of how often a product needs to be manufactured in order for it to meet demand. You'll also need to know the Takt time (the amount of time it takes to produce a product), and how it compares to the cycle time of the product. A bottleneck is when Takt time exceeds the cycle time.
Value stream maps can be used to help companies identify and eliminate waste in every stage of their business processes. Value stream mapping allows you to identify non-value added activities and analyze the flow data. This can help you identify potential threats and opportunities for your business. It is also an important tool for identifying bottlenecks and determining where improvements can be made to make the entire process more efficient. Value Stream Mapping can have many benefits, beyond just improving information flow. Value Stream Maps can be a valuable tool that will help you implement Lean Six Sigma.
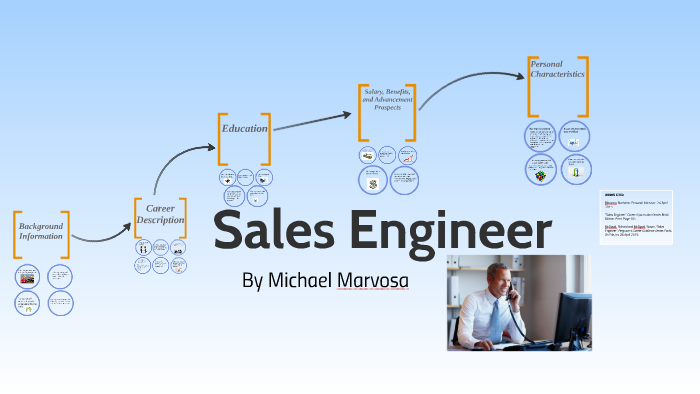
Lean Healthcare
Value stream mapping is a tool used to improve synchronization of activities in the medical field. It helps to identify areas of improvement and provides strategies for implementation. A map might show a patient’s flow from the time they arrive at the hospital up to the time they leave after their treatment. These flow paths can be visualized to create a timeline and identify waste-generating and value-added steps.
To make VSM in Lean Healthcare more efficient, the authors recommend that clear definitions be established for all terms. They also recommend establishing appropriate indicators and sharing examples of success and failure. These will allow the results to be replicated and modified for specific situations. Healthcare sector lean methods are more likely produce positive outcomes. The authors suggest that there be a common definition and use of value stream mapping within the healthcare sector to ensure that these benefits are shared across the entire health care system.
Lean Manufacturing
It is crucial to get input from all stakeholders involved in a value stream mapping process before you can begin. The people who are responsible for satisfying customer needs should be part of this team. They should also include people who perform critical tasks and activities to ensure the flow of information. This can be done by gathering input and suggestions from the key stakeholders. The scope of the value streaming mapping process must be defined.
Next, pick the product or the process that you want to improve. Finally, teach the team about value stream mapping. The mapping process begins by identifying the customer's needs. This includes all information received, as well as the communication and decision-making processes. Value stream mapping ultimately aims to eliminate waste while increasing customer satisfaction. Lean manufacturing is a sustainable and viable solution to any company's challenges by identifying what factors contribute to customer satisfaction.
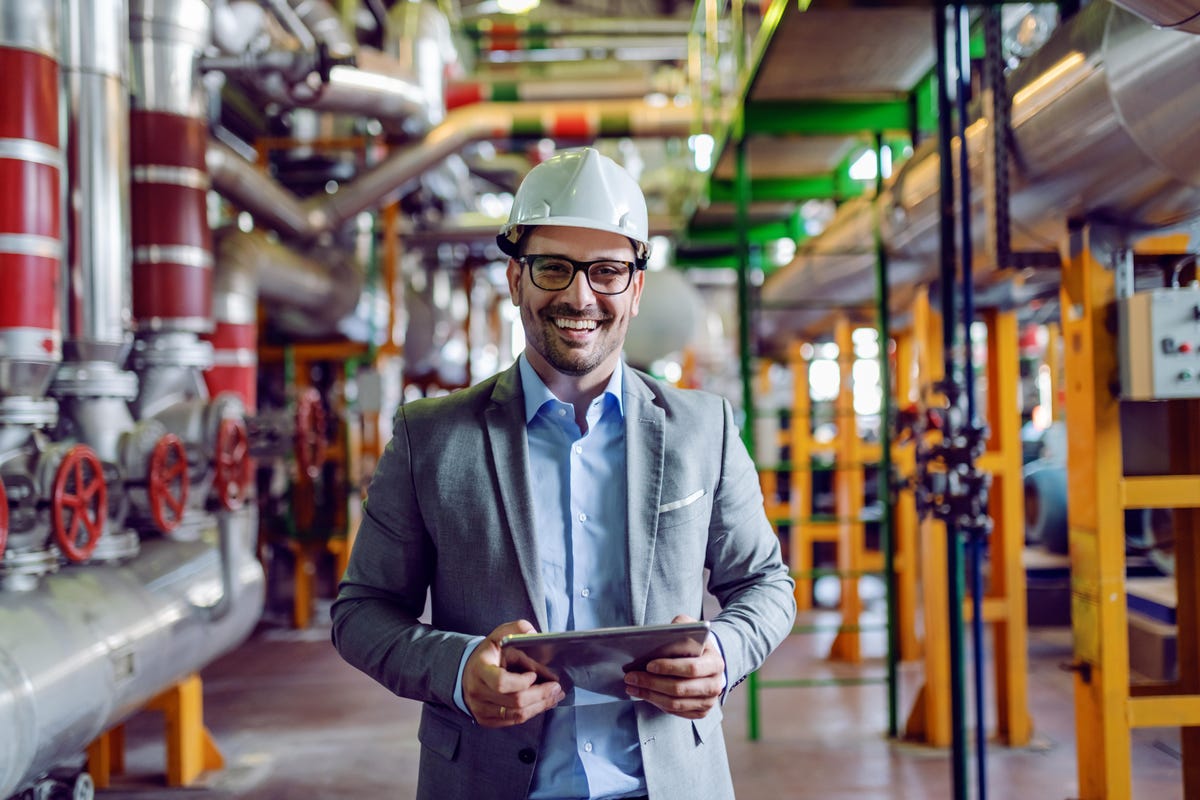
Future state value stream mapping
If you haven't heard of future state value stream mapping before, it is an excellent tool for identifying waste. The goal of this type of mapping is to identify the causes of waste and eliminate them. Future state ideas will be marked with the same symbols used in current state mapping. Future state value stream mapping should include Takt Time. It helps you efficiently allocate resources and pinpoint areas of waste. Your company can also use the future state value stream map as a powerful tool.
Once you've determined where problems are and how they relate to the future state, it's time to map the steps you need to take to get there. Teams can use a future map as a reference tool to help them complete their projects and achieve the target values. You need to keep your future state value stream map updated every six to 12 months so that you can track your progress. It is important to update the future statemap as new projects and changes are implemented.
FAQ
What is the responsibility for a logistics manager
Logistics managers are responsible for ensuring that all goods arrive in perfect condition and on time. This is achieved by using their knowledge and experience with the products of the company. He/she should also ensure enough stock is available to meet demand.
What is the role of a manager in manufacturing?
A manufacturing manager has to ensure that all manufacturing processes work efficiently and effectively. They should also be aware of any problems within the company and act accordingly.
They should also know how to communicate with other departments such as sales and marketing.
They must also keep up-to-date with the latest trends in their field and be able use this information to improve productivity and efficiency.
What is the role and responsibility of a Production Planner?
Production planners ensure all aspects of the project are delivered within time and budget. A production planner ensures that the service and product meet the client's expectations.
Do we need to know about Manufacturing Processes before learning about Logistics?
No. You don't have to know about manufacturing processes before learning about logistics. Knowing about manufacturing processes will help you understand how logistics works.
Why automate your warehouse?
Modern warehouses have become more dependent on automation. With the rise of ecommerce, there is a greater demand for faster delivery times as well as more efficient processes.
Warehouses need to adapt quickly to meet changing needs. To do so, they must invest heavily in technology. Automating warehouses has many benefits. Here are some reasons why it's worth investing in automation:
-
Increases throughput/productivity
-
Reduces errors
-
Accuracy is improved
-
Boosts safety
-
Eliminates bottlenecks
-
This allows companies to scale easily
-
Workers are more productive
-
The warehouse can be viewed from all angles.
-
Enhances customer experience
-
Improves employee satisfaction
-
Minimizes downtime and increases uptime
-
You can be sure that high-quality products will arrive on time
-
Removing human error
-
It helps ensure compliance with regulations
Statistics
- [54][55] These are the top 50 countries by the total value of manufacturing output in US dollars for its noted year according to World Bank.[56] (en.wikipedia.org)
- Job #1 is delivering the ordered product according to specifications: color, size, brand, and quantity. (netsuite.com)
- According to a Statista study, U.S. businesses spent $1.63 trillion on logistics in 2019, moving goods from origin to end user through various supply chain network segments. (netsuite.com)
- (2:04) MTO is a production technique wherein products are customized according to customer specifications, and production only starts after an order is received. (oracle.com)
- According to the United Nations Industrial Development Organization (UNIDO), China is the top manufacturer worldwide by 2019 output, producing 28.7% of the total global manufacturing output, followed by the United States, Japan, Germany, and India.[52][53] (en.wikipedia.org)
External Links
How To
How to use the Just In-Time Production Method
Just-intime (JIT), a method used to lower costs and improve efficiency in business processes, is called just-in-time. This is where you have the right resources at the right time. This means that your only pay for the resources you actually use. The term was first coined by Frederick Taylor, who developed his theory while working as a foreman in the early 1900s. He saw how overtime was paid to workers for work that was delayed. He decided that workers would be more productive if they had enough time to complete their work before they started to work.
JIT is a way to plan ahead and make sure you don't waste any money. It is important to look at your entire project from beginning to end and ensure that you have enough resources to handle any issues that may arise. You will have the resources and people to solve any problems you anticipate. You won't have to pay more for unnecessary items.
There are many JIT methods.
-
Demand-driven: This is a type of JIT where you order the parts/materials needed for your project regularly. This will enable you to keep track of how much material is left after you use it. This will let you know how long it will be to produce more.
-
Inventory-based: This allows you to store the materials necessary for your projects in advance. This allows you to predict how much you can expect to sell.
-
Project-driven : This is a method where you make sure that enough money is set aside to pay the project's cost. You will be able to purchase the right amount of materials if you know what you need.
-
Resource-based JIT : This is probably the most popular type of JIT. You assign certain resources based off demand. You will, for example, assign more staff to deal with large orders. You'll have fewer orders if you have fewer.
-
Cost-based: This is similar to resource-based, except that here you're not just concerned about how many people you have but how much each person costs.
-
Price-based: This is very similar to cost-based, except that instead of looking at how much each individual worker costs, you look at the overall price of the company.
-
Material-based is an alternative to cost-based. Instead of looking at the total cost in the company, this method focuses on the average amount of raw materials that you consume.
-
Time-based: This is another variation of resource-based JIT. Instead of focusing on how much each employee costs, you focus on how long it takes to complete the project.
-
Quality-based: This is yet another variation of resource-based JIT. Instead of focusing on the cost of each worker or how long it takes, think about how high quality your product is.
-
Value-based: This is one of the newest forms of JIT. In this scenario, you're not concerned about how products perform or whether customers expect them to meet their expectations. Instead, you focus on the added value that you provide to your market.
-
Stock-based: This stock-based method focuses on the actual quantity of products being made at any given time. It's useful when you want maximum production and minimal inventory.
-
Just-intime (JIT), planning is a combination JIT management and supply chain management. It's the process of scheduling delivery of components immediately after they are ordered. It's important as it reduces leadtimes and increases throughput.