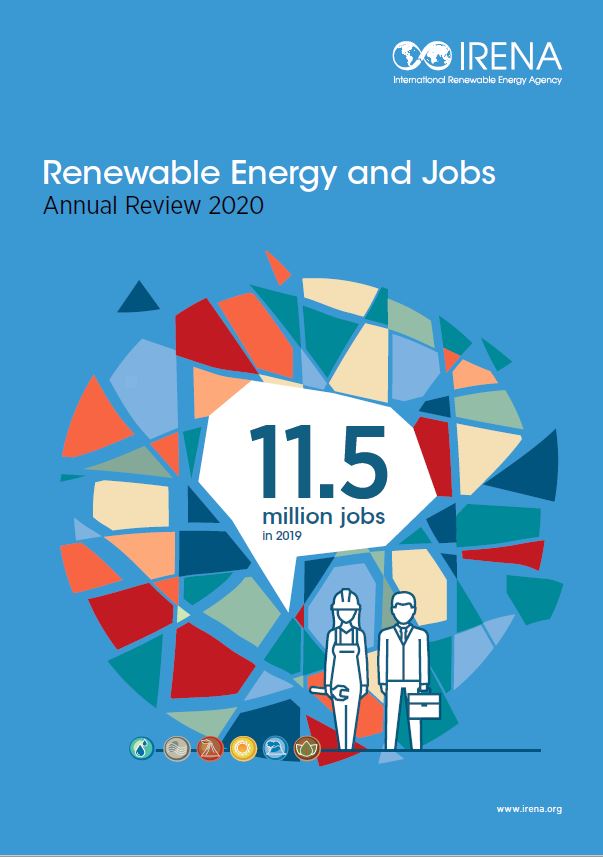
While experience is important for food manufacturers, so is OSHA compliance. These are the three main things you should consider when selecting a company that will automate your production.
Food manufacturers have to be experienced
A position as a food manufacturer often requires high levels of industry experience. However, it is possible to get a job even if you have little or no experience. Many food companies prefer to hire from their own ranks. Although high school education is a benefit, it is not necessary. Entry-level employees start out as assistants to more experienced workers. Then, they learn on the job. Some entry-level jobs can be done in just a few days. Common entry-level jobs include operating bread slicers and washing vegetables before processing. In every aspect of food manufacturing, experience is essential.
Conformance to OSHA regulations
The enforcement process for OSHA regulations for food manufacturers begins with an inspection, which is either triggered by an incident, complaint, or a "programmed inspection." A planned inspection preceded an OSHA enforcement trip to a yogurt factory. Multiple violations of the process safety standard are common in many cases. These include standards on hazard communications, guarding machines, stairs and platforms and emergency egress. Forklift operation and hearing protection are also included.
Developing a plan to prevent food safety issues
While federal regulations govern most companies, some businesses are exempt from certain requirements. While it is impossible to anticipate every food safety issue, there are ways to prevent and manage potential hazards in the food manufacturing process. Food safety is not only an issue for the health of the consumer, but it can also have negative effects on the business. Recalls can affect direct operations and others in the supply chain. There are many reasons for recalls, such as adulteration and misbranding. A food manufacturer may have to pay a lot more for recalls than the health risks.
Cost of automation
Food manufacturers face increasing automation costs as utilities rise. As a result, some regions are forced import ingredients to meet local production. Additionally, suppliers face a declining profit margin when they pass on the costs to consumers. However, automation can help lower these costs and increase production efficiency. In this article, we'll discuss how automation can help improve the overall efficiency for food manufacturers. You can also reach out to us for our industry knowledge.
Challenges of competing with dominant food companies
To preserve their market dominance, stop unwanted competition and increase their profit margins, dominant food companies use three broad strategies. These strategies include developing and acquiring valuable intangible resources, enforcing production efficiency and controlling the supply-chain. These strategies, in essence, create barriers to entry. These are the top challenges for emerging food and beverage businesses. Let's talk more about each strategy.
FAQ
What are the four types of manufacturing?
Manufacturing is the process by which raw materials are transformed into useful products through machines and processes. It includes many different activities like designing, building and testing, packaging, shipping and selling, as well as servicing.
What is the role of a logistics manager
A logistics manager makes sure that all goods are delivered on-time and in good condition. This is done by using his/her experience and knowledge of the company's products. He/she must also ensure sufficient stock to meet the demand.
How can manufacturing prevent production bottlenecks?
To avoid production bottlenecks, ensure that all processes run smoothly from the moment you receive your order to the time the product ships.
This includes planning for capacity requirements as well as quality control measures.
This can be done by using continuous improvement techniques, such as Six Sigma.
Six Sigma is a management method that helps to improve quality and reduce waste.
It focuses on eliminating variation and creating consistency in your work.
What types of jobs can you find in logistics
There are many kinds of jobs available within logistics. These are some of the jobs available in logistics:
-
Warehouse workers - They load trucks and pallets.
-
Transportation drivers - They drive trucks and trailers to deliver goods and carry out pick-ups.
-
Freight handlers, - They sort out and pack freight in warehouses.
-
Inventory managers - These are responsible for overseeing the stock of goods in warehouses.
-
Sales representatives: They sell products to customers.
-
Logistics coordinators: They plan and manage logistics operations.
-
Purchasing agents: They are responsible for purchasing goods and services to support company operations.
-
Customer service representatives – They answer emails and phone calls from customers.
-
Shipping clerks - They process shipping orders and issue bills.
-
Order fillers are people who fill orders based only on what was ordered.
-
Quality control inspectors (QCI) - They inspect all incoming and departing products for potential defects.
-
Other - Logistics has many other job opportunities, including transportation supervisors, logistics specialists, and cargo specialists.
What are the responsibilities of a manufacturing manager
A manufacturing manager must ensure that all manufacturing processes are efficient and effective. They should also be aware of any problems within the company and act accordingly.
They should also know how to communicate with other departments such as sales and marketing.
They must also keep up-to-date with the latest trends in their field and be able use this information to improve productivity and efficiency.
Statistics
- You can multiply the result by 100 to get the total percent of monthly overhead. (investopedia.com)
- Many factories witnessed a 30% increase in output due to the shift to electric motors. (en.wikipedia.org)
- (2:04) MTO is a production technique wherein products are customized according to customer specifications, and production only starts after an order is received. (oracle.com)
- In the United States, for example, manufacturing makes up 15% of the economic output. (twi-global.com)
- According to a Statista study, U.S. businesses spent $1.63 trillion on logistics in 2019, moving goods from origin to end user through various supply chain network segments. (netsuite.com)
External Links
How To
Six Sigma in Manufacturing
Six Sigma is "the application statistical process control (SPC), techniques for continuous improvement." Motorola's Quality Improvement Department, Tokyo, Japan, developed it in 1986. Six Sigma's main goal is to improve process quality by standardizing processes and eliminating defects. Many companies have adopted Six Sigma in recent years because they believe that there are no perfect products and services. Six Sigma seeks to reduce variation between the mean production value. It is possible to measure the performance of your product against an average and find the percentage of time that it differs from the norm. If it is too large, it means that there are problems.
Understanding the dynamics of variability within your business is the first step in Six Sigma. Once you understand this, you can then identify the causes of variation. It is important to identify whether the variations are random or systemic. Random variations happen when people make errors; systematic variations are caused externally. For example, if you're making widgets, and some of them fall off the assembly line, those would be considered random variations. It would be considered a systematic problem if every widget that you build falls apart at the same location each time.
Once you've identified the problem areas you need to find solutions. That solution might involve changing the way you do things or redesigning the process altogether. Test them again once you've implemented the changes. If they don’t work, you’ll need to go back and rework the plan.