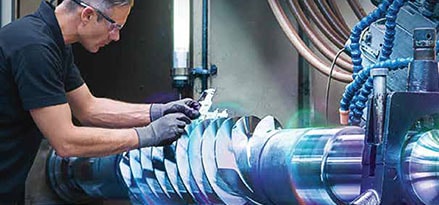
The manufacturing sector is experiencing rapid changes. This shift requires new skills and cutting-edge expertise. The factory of the future is digital, flexible, responsive, efficient and responsible. The factory of the future will be digital, flexible, responsible, efficient, and sustainable. Manufacturing engineers will be at the forefront. Here are three areas of expertise that you need to master. These skills will have a major impact on the future of your industry.
Analyst perspectives
Analyst perspectives on industry future are important for understanding current trends and assessing the industry's competitive dynamics. These insights provide insights into the changing consumer landscape, including attitudes and intentions, as well as purchase behavior. NPD conducts an annual survey to provide a complete picture of the industry's outlook. The categories forecasted for each industry are different depending on the country. This chapter examines what industry analysts do to validate and generate market-based intelligence.
Consumer survey data
Prosper collects responses from approximately seven thousand adult respondents each month. The data is correlated and trended and contains questions on the emotional mindset of consumers, purchasing patterns, and future intentions. The archive also contains monthly data over 18 years on hundreds of major retailers. It's the best tool to find out the true attitudes and spending habits within a specific market. Business owners and marketers can use consumer survey data for invaluable information.
Trends in industry growth
This chapter discusses the growth patterns for industries and businesses. The growth rate of industries is affected by the progress of financial markets in developed nations. Financially-hungry industries grow faster in countries that have developed financial markets. Sectors that depend on foreign finance also grow faster during periods of high stock market performance. These patterns are consistent in trade and development theories that suggest that a country's product mixture reflects its economic stage. Here we discuss the key drivers and trends affecting industry growth.
Automation
Gartner estimates that automation will be a major factor in almost every occupation over the next ten years. Although only five percent can be fully automated with the current technologies, many other occupations have component activities that can be automated. Most occupations are likely to be affected in some fashion, and the nature or job description of these jobs could change. The workplace will determine whether or not they adapt to change. Here are five examples of how automation will impact manufacturing.
Hybrid Work Environment
To create a successful hybrid workplace, companies must listen to their employees and provide many ways to share that feedback. These valuable insights can be gathered through focus groups, surveys of human resources, and one-on-one conversations. They can also offer employees incentives like financial rewards, food deliveries, and tokens of appreciation. By listening to employee feedback, companies can ensure a smooth transition to this new work environment and create a positive employee experience.
Streaming media
The streaming media industry represents a new business model. It is uncertain what the future holds. Many media conglomerates are now selling short-term streaming rights to three services. Although streaming was initially a niche market, it is expected to grow rapidly and surpass linear TV as the most popular viewing option over the next few years. In 2025, almost every production of the four media conglomerates should only be available through their streaming services.
Automotive industry
What are the prospects for the Automotive Industry's future? Many experts believe that the industry will slowly recover in the coming decade. Automakers face many problems right now. The latest technologies, like connected cars, may open up new revenue streams. The government can reduce emissions laws. Automobile companies can improve resilience and accelerate R&D. There are several reasons why the Automotive Industry could start to recover slowly over the coming decade.
FAQ
How can manufacturing reduce production bottlenecks?
The key to avoiding bottlenecks in production is to keep all processes running smoothly throughout the entire production cycle, from the time you receive an order until the time when the product ships.
This includes both quality control and capacity planning.
Continuous improvement techniques like Six Sigma are the best way to achieve this.
Six Sigma management is a system that improves quality and reduces waste within your organization.
It is focused on creating consistency and eliminating variation in your work.
What are the differences between these four types?
Manufacturing is the process that transforms raw materials into useful products. It can involve many activities like designing, manufacturing, testing packaging, shipping, selling and servicing.
What skills is required for a production planner?
Production planners must be flexible, organized, and able handle multiple tasks. You must also be able to communicate effectively with clients and colleagues.
Statistics
- In the United States, for example, manufacturing makes up 15% of the economic output. (twi-global.com)
- Many factories witnessed a 30% increase in output due to the shift to electric motors. (en.wikipedia.org)
- According to the United Nations Industrial Development Organization (UNIDO), China is the top manufacturer worldwide by 2019 output, producing 28.7% of the total global manufacturing output, followed by the United States, Japan, Germany, and India.[52][53] (en.wikipedia.org)
- Job #1 is delivering the ordered product according to specifications: color, size, brand, and quantity. (netsuite.com)
- According to a Statista study, U.S. businesses spent $1.63 trillion on logistics in 2019, moving goods from origin to end user through various supply chain network segments. (netsuite.com)
External Links
How To
How to Use Just-In-Time Production
Just-in time (JIT), is a process that reduces costs and increases efficiency in business operations. It's a way to ensure that you get the right resources at just the right time. This means you only pay what you use. The term was first coined by Frederick Taylor, who developed his theory while working as a foreman in the early 1900s. After observing how workers were paid overtime for late work, he realized that overtime was a common practice. He concluded that if workers were given enough time before they start work, productivity would increase.
JIT is about planning ahead. You should have all the necessary resources ready to go so that you don’t waste money. Look at your entire project, from start to end. Make sure you have enough resources in place to deal with any unexpected problems. If you anticipate that there might be problems, you'll have enough people and equipment to fix them. This way, you won't end up paying extra money for things that weren't really necessary.
There are many JIT methods.
-
Demand-driven: This JIT is where you place regular orders for the parts/materials that are needed for your project. This will allow to track how much material has been used up. You'll also be able to estimate how long it will take to produce more.
-
Inventory-based : You can stock the materials you need in advance. This allows for you to anticipate how much you can sell.
-
Project-driven: This method allows you to set aside enough funds for your project. If you know the amount you require, you can buy the materials you need.
-
Resource-based JIT : This is probably the most popular type of JIT. Here, you allocate certain resources based on demand. For instance, if you have a lot of orders coming in, you'll assign more people to handle them. If you don't receive many orders, then you'll assign fewer employees to handle the load.
-
Cost-based: This is similar to resource-based, except that here you're not just concerned about how many people you have but how much each person costs.
-
Price-based: This approach is very similar to the cost-based method except that you don't look at individual workers costs but the total cost of the company.
-
Material-based is an alternative to cost-based. Instead of looking at the total cost in the company, this method focuses on the average amount of raw materials that you consume.
-
Time-based JIT: This is another variant of resource-based JIT. Instead of focusing on how much each employee costs, you focus on how long it takes to complete the project.
-
Quality-based JIT - This is another form of resource-based JIT. Instead of worrying about the costs of each employee or how long it takes for something to be made, you should think about how quality your product is.
-
Value-based JIT: This is the latest form of JIT. This is where you don't care about how the products perform or whether they meet customers' expectations. Instead, you're focused on how much value you add to the market.
-
Stock-based. This method is inventory-based and focuses only on the actual production at any given point. It's used when you want to maximize production while minimizing inventory.
-
Just-in time (JIT), planning: This is a combination JIT/supply chain management. It is the process of scheduling components' delivery as soon as they have been ordered. This is important as it reduces lead time and increases throughput.