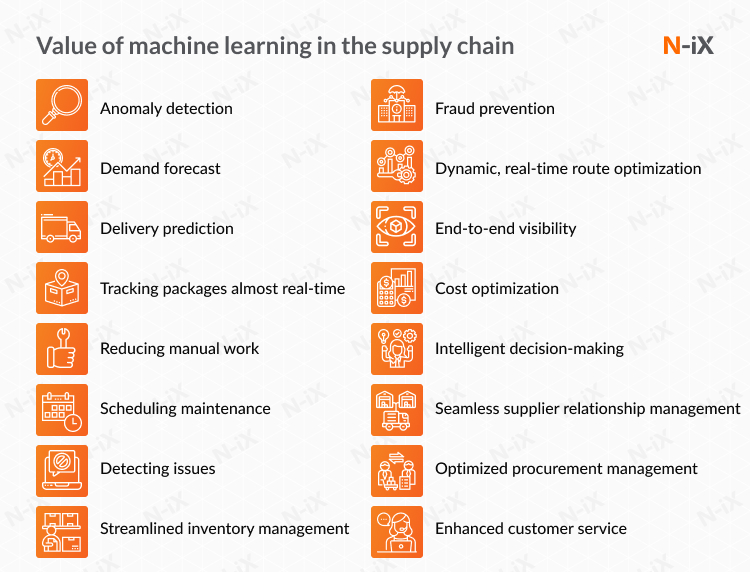
Global supply-chain Management is the term used to describe the distribution of goods and/or services across a transnational company's global network. The principle behind this concept is to maximize profit, while minimizing waste. This distribution method offers many benefits, but there are some downsides. Let's examine some of these issues. Find out more about global supply management. We will also address some of the problems associated with global supply chain management.
Resilience
It is essential to have a strategy that encourages resilience in order to be an effective global supply chain manager. The resilience of the supply chain can be strengthened by redesigning the supply chain, creating redundancies, and implementing multiple sourcing. In the short term, supply chains may be considered rigid, but with constant vigilance, creativity, and innovation, they can become resilient. One inventory management software provider, Cin7, has helped its users to build resilience in their supply chains by publishing various educational materials and advice.
Information sharing
While the role of information sharing in global supply chain management may seem ambiguous, it is vital to the survival of enterprises. This study examines how information sharing can benefit various parties in a supply chain. The benefits of information sharing are diverse, and they may vary according to the type of information shared. The value of information will vary depending on who is involved. Below are examples of information that may benefit supply chains.
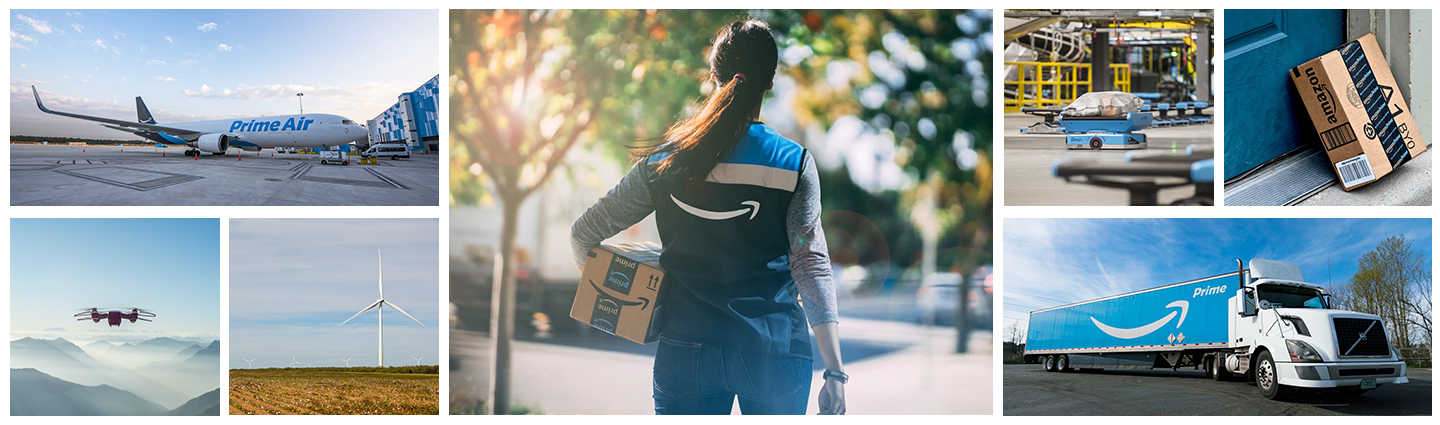
Quality management
A key part of any supply chain is addressing quality issues. Quality issues must be addressed. Companies should not only focus on quality but also address secondary issues. This will ensure that the supply chain is risk-free. This article will discuss the role of quality management in global supply chain management. It will also highlight how existing business systems can fail to meet this challenge. Let's examine how companies can overcome these obstacles and implement quality management strategies that are more efficient.
Logistics Links
As the demands and preferences of customers change, so too do the requirements for businesses. Global supply chains include a network of companies, individuals, suppliers and other entities that all work together to deliver goods in the most efficient manner to their customers. Logistics plays a vital role in global logistics management. It allows companies to lower their costs while improving their performance. The supply chain includes vendors, producers and warehouses as well as transportation companies, distribution centers and retailers.
COVID-19 pandemic
Global supply chain management will be essential in order to manage the huge COVID-19 outbreak. To respond to emergencies, global supply chains are critical. They ensure that essential supplies are available in a timely manner. But other issues such as the Chinese lockdown and uncertainty in the global economy have made it difficult for the global supply to remain open. This pandemic is proving to be a test of supply chain resilience and flexibility. In the wake of this crisis, companies will be judged not only on their response, but also on their corporate values.
The economic impact
Global supply chain management is of vital importance to the global economy. Manufacturers are becoming more dependent on one source of vital supplies as they switch to JIT (just in time) production. JIT production models do have one major problem: they leave companies open for disruptions in their supply networks. According to a recent survey, almost half of executives plan on removing some production from China while one-third intend to de-emphasize JIT Manufacturing.
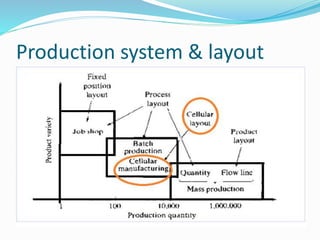
There are many career opportunities
Global supply chain management oversees all aspects of an organization's international procurement strategy. They are responsible for the management of inventory and will work closely with suppliers to ensure that high-quality products are produced. They monitor the supply chain performance and analyze the data. This role requires a lot collaboration with other departments of a company. Here are some career opportunities for those with this kind of experience. All of them offer valuable career benefits.
FAQ
What does it mean to be a manufacturer?
Manufacturing Industries refers to businesses that manufacture products. The people who buy these products are called consumers. These companies use various processes such as production, distribution, retailing, management, etc., to fulfill this purpose. These companies produce goods using raw materials and other equipment. This includes all types if manufactured goods.
What are the logistics products?
Logistics refers to all activities that involve moving goods from A to B.
These include all aspects related to transport such as packaging, loading and transporting, storing, transporting, unloading and warehousing inventory management, customer service. Distribution, returns, recycling are some of the options.
Logisticians ensure that the product is delivered to the correct place, at the right time, and under safe conditions. They help companies manage their supply chain efficiency by providing information on demand forecasts, stock levels, production schedules, and availability of raw materials.
They monitor shipments in transit, ensure quality standards, manage inventories, replenish orders, coordinate with suppliers and other vendors, and offer support services for sales, marketing, and customer service.
What is the responsibility of a logistics manager?
A logistics manager makes sure that all goods are delivered on-time and in good condition. This is accomplished by using the experience and knowledge gained from working with company products. He/she must also ensure sufficient stock to meet the demand.
Statistics
- You can multiply the result by 100 to get the total percent of monthly overhead. (investopedia.com)
- According to a Statista study, U.S. businesses spent $1.63 trillion on logistics in 2019, moving goods from origin to end user through various supply chain network segments. (netsuite.com)
- In the United States, for example, manufacturing makes up 15% of the economic output. (twi-global.com)
- In 2021, an estimated 12.1 million Americans work in the manufacturing sector.6 (investopedia.com)
- (2:04) MTO is a production technique wherein products are customized according to customer specifications, and production only starts after an order is received. (oracle.com)
External Links
How To
Six Sigma in Manufacturing
Six Sigma is "the application statistical process control (SPC), techniques for continuous improvement." It was developed by Motorola's Quality Improvement Department at their plant in Tokyo, Japan, in 1986. Six Sigma is a method to improve quality through standardization and elimination of defects. This method has been adopted by many companies in recent years as they believe there are no perfect products or services. Six Sigma seeks to reduce variation between the mean production value. If you take a sample and compare it with the average, you will be able to determine how much of the production process is different from the norm. If the deviation is excessive, it's likely that something needs to be fixed.
Understanding how your business' variability is a key step towards Six Sigma implementation is the first. Once you understand this, you can then identify the causes of variation. Also, you will need to identify the sources of variation. Random variations are caused when people make mistakes. While systematic variations are caused outside of the process, they can occur. If you make widgets and some of them end up on the assembly line, then those are considered random variations. If however, you notice that each time you assemble a widget it falls apart in exactly the same spot, that is a problem.
After identifying the problem areas, you will need to devise solutions. It might mean changing the way you do business or redesigning it entirely. You should then test the changes again after they have been implemented. If they don't work you need to rework them and come up a better plan.