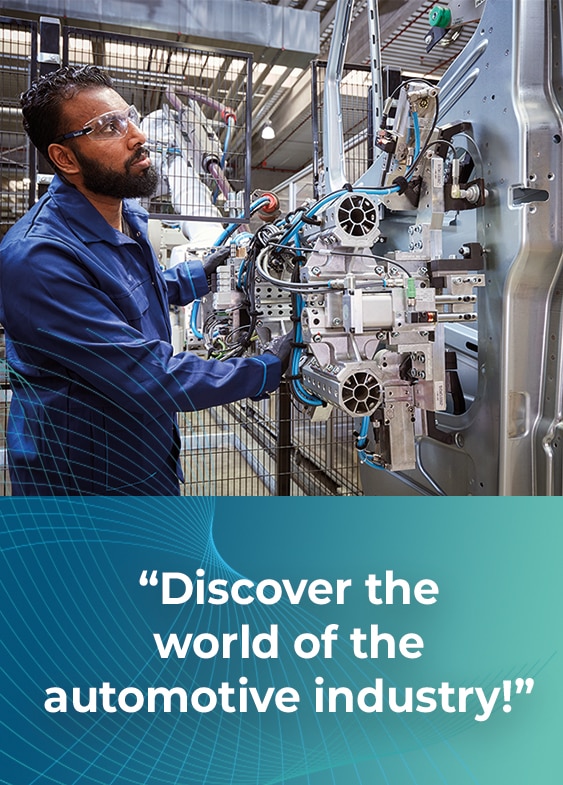
The five s's are the key to lean manufacturing. They are Standardize. Straighten. Shine. and Sustain. Here are some of the steps you should take. To maximize your lean transformation, you must train your frontline operators and team leaders.
Standardize
The first step of the 5S process is to clean and organize your work space. This may be a one-time job, but if you standardize the process, it can become a routine. To make sure you have a consistent approach when performing 5S tasks, visual cues or checklist templates are all options.
These five s's can help your workplace be more productive and efficient. This will encourage staff to be more organized and streamline their work. A clean and well-organized work environment will improve efficiency. You can improve safety in your workplace by using the five s’s of lean. A well-organized workspace will help avoid accidents, reduce mistakes, and increase the likelihood of productive work.
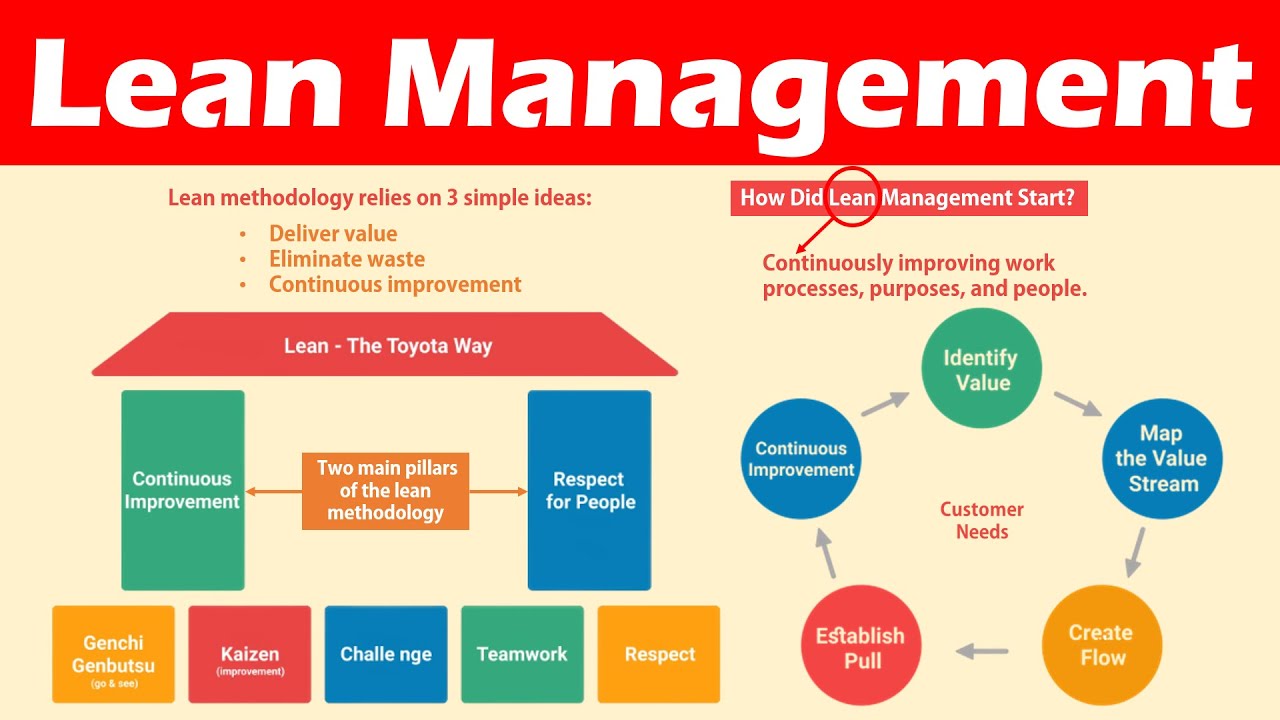
Straighten
Straightening your 5 s's of lean doesn't have to be difficult. Companies can improve their business processes by applying lean principles in a systematic way. Workers will be more likely to find the right components by organizing them in an assembly line. This will save time searching for the wrong parts and reduce company safety.
This will allow you to reduce the number items in each area. It will also help you save money on consumables. This can help you reduce your office supply bills. Straightening work cells not only helps you save money but it also increases the efficiency of your production process by improving quality, safety, and standard work.
Shine
Shine focuses on the inspection of the workspace and identifying any potential problems. Shine inspects tools and equipment to help improve flow and reduce waste. Shine helps workers identify potential problems before they hamper production. Shine helps improve productivity by standardizing the layout.
Shine is one of the 5S tools used in lean manufacturing. This technique automates work, reducing waste and increasing efficiency. It can be applied to any industry, including manufacturing. It applies the 5S principles in a business. It allows companies to reduce inventory, work-in process, and supply stock.
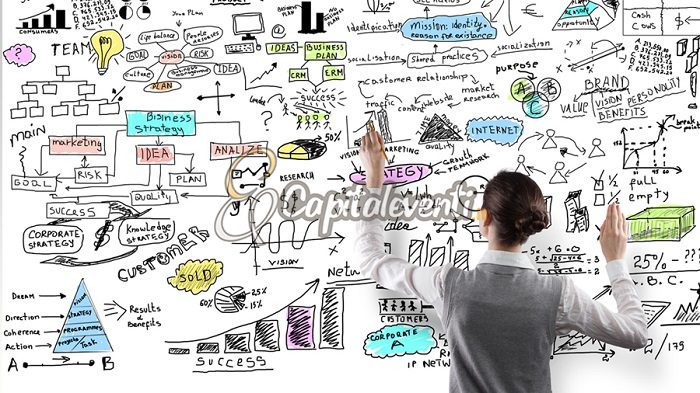
Be a good citizen
The 5 s's are about introducing a standardized system to a facility in order to maintain the 5S. This is a continuous process that should be repeated until the facility functions at its best. To do this, employees should be trained to perform 5S audits themselves.
The 5S method emphasizes reducing waste, increasing productivity, and maintaining an orderly work environment. It is basically a way to organize workplaces according to the five principles of Toyota Production System. Hiroyuki Hirano developed it in Japan post-war to improve the efficiency of manufacturing facilities.
FAQ
How does a Production Planner differ from a Project Manager?
A production planner is more involved in the planning phase of the project than a project manger.
How can we improve manufacturing efficiency?
First, we need to identify which factors are most critical in affecting production times. The next step is to identify the most important factors that affect production time. If you aren't sure where to begin, think about the factors that have the greatest impact on production time. Once you have identified the factors, then try to find solutions.
What is the role of a manager in manufacturing?
The manufacturing manager should ensure that every manufacturing process is efficient and effective. They should also be aware of any problems within the company and act accordingly.
They should also learn how to communicate effectively with other departments, including sales and marketing.
They should be informed about industry trends and be able make use of this information to improve their productivity and efficiency.
What jobs are available in logistics?
There are many jobs available in logistics. Here are some:
-
Warehouse workers: They load and unload trucks, pallets, and other cargo.
-
Transportation drivers: They drive trucks and trailers and deliver goods and make pick-ups.
-
Freight handlers: They sort and package freight in warehouses.
-
Inventory managers - They oversee the inventory of goods in warehouses.
-
Sales reps are people who sell products to customers.
-
Logistics coordinators – They plan and coordinate logistics operations.
-
Purchasing agents: They are responsible for purchasing goods and services to support company operations.
-
Customer service representatives - Answer calls and email from customers.
-
Shipping clerks - They process shipping orders and issue bills.
-
Order fillers are people who fill orders based only on what was ordered.
-
Quality control inspectors are responsible for inspecting incoming and outgoing products looking for defects.
-
Others - There are many other types of jobs available in logistics, such as transportation supervisors, cargo specialists, etc.
Do we need to know about Manufacturing Processes before learning about Logistics?
No. It doesn't matter if you don't know anything about manufacturing before you learn about logistics. But, being familiar with manufacturing processes will give you a better understanding about how logistics works.
What are the products of logistics?
Logistics refers to the movement of goods from one place to another.
They cover all aspects of transportation, such as packing, loading, transporting and unloading.
Logisticians ensure that products reach the right destination at the right moment and under safe conditions. They assist companies with their supply chain efficiency through information on demand forecasts. Stock levels, production times, and availability.
They also keep track of shipments in transit, monitor quality standards, perform inventories and order replenishment, coordinate with suppliers and vendors, and provide support services for sales and marketing.
Statistics
- [54][55] These are the top 50 countries by the total value of manufacturing output in US dollars for its noted year according to World Bank.[56] (en.wikipedia.org)
- According to a Statista study, U.S. businesses spent $1.63 trillion on logistics in 2019, moving goods from origin to end user through various supply chain network segments. (netsuite.com)
- In the United States, for example, manufacturing makes up 15% of the economic output. (twi-global.com)
- Many factories witnessed a 30% increase in output due to the shift to electric motors. (en.wikipedia.org)
- According to the United Nations Industrial Development Organization (UNIDO), China is the top manufacturer worldwide by 2019 output, producing 28.7% of the total global manufacturing output, followed by the United States, Japan, Germany, and India.[52][53] (en.wikipedia.org)
External Links
How To
How to use 5S in Manufacturing to Increase Productivity
5S stands for "Sort", 'Set In Order", 'Standardize', & Separate>. Toyota Motor Corporation invented the 5S strategy in 1954. This methodology helps companies improve their work environment to increase efficiency.
This method aims to standardize production processes so that they are repeatable, measurable and predictable. This means that every day tasks such cleaning, sorting/storing, packing, and labeling can be performed. This knowledge allows workers to be more efficient in their work because they are aware of what to expect.
Five steps are required to implement 5S: Sort, Set In Order, Standardize. Separate. Each step involves a different action which leads to increased efficiency. You can make it easy for people to find things later by sorting them. Once you have placed items in an ordered fashion, you will put them together. After you have divided your inventory into groups you can store them in easy-to-reach containers. You can also label your containers to ensure everything is properly labeled.
This requires employees to critically evaluate how they work. Employees need to be able understand their motivations and discover alternative ways to do them. They will need to develop new skills and techniques in order for the 5S system to be implemented.
In addition to increasing efficiency, the 5S method also improves morale and teamwork among employees. They are more motivated to achieve higher efficiency levels as they start to see improvement.