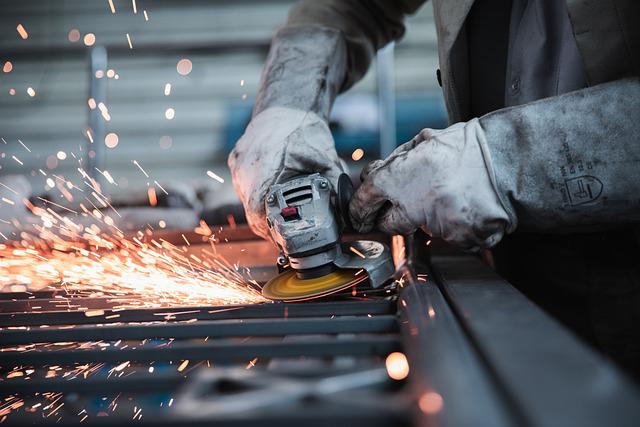
GembaWalk was initially developed by Toyota. The tool allows managers and employees to see the floor so they can gain insight into company processes. This is an integral part of any facility renovation. It allows managers to better understand the company's processes and make informed decisions. This practice can also help to identify and solve problems.
Gemba is a Japanese term that means "where the work happens." It is used to define the factory or shop floor, but it can also refer any place where a service or product is created. Gemba is the Japanese business philosophy. Gemba's main goal is to improve efficiency and gain an in-depth understanding of processes within organizations.
Companies that want to improve their processes or eliminate waste should consider Gemba walks. They also help to promote a more cooperative atmosphere in an organization. They encourage employees to exchange ideas which can lead to a better product or service. They can help executives and managers to understand the company's processes better.
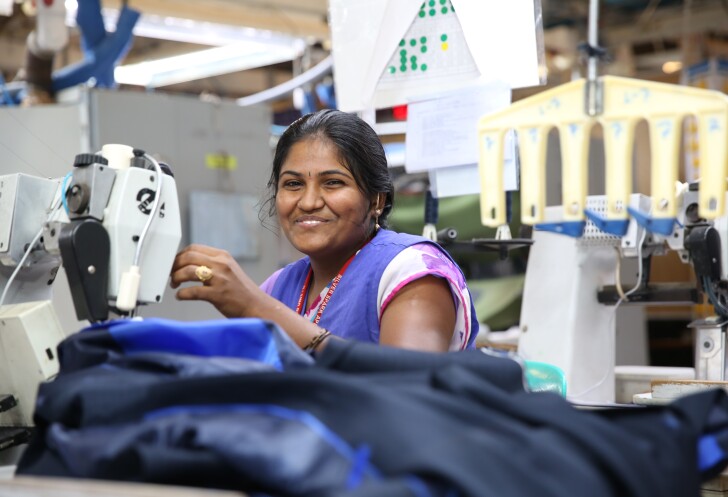
Gemba walks are usually conducted by supervisors or managers, but they can also be performed by executives on their own. Gemba walks should be conducted on a regular basis by executives. Gemba walks should be completed with a Lean teacher, Sensei, for approximately 45-60 minutes each week. These walks should be taken during work hours, since it's the best time for workers to show their skills.
Gemba Walks assist executives and managers in understanding the working of processes and identifying improvement opportunities. They are also a way to increase safety within an organization. Safety issues are the biggest part of waste in manufacturing facilities, and improved safety can help make continuous improvement possible.
Gemba Walks are an important part of the Lean process, but they should be implemented at all levels of the organization. They can help executives and leaders gain a different perspective on customers. This can help them create better products, processes and services. Gemba Walks provide a powerful way for organizations to reach their maximum potential.
Gemba Walks play an important role in Lean process designs. They are often used as part of Kaizen events by key stakeholders. Kaizen events are gatherings of key stakeholders that evaluate activities and assess activities. They are based on the Japanese term "continuous improvement."
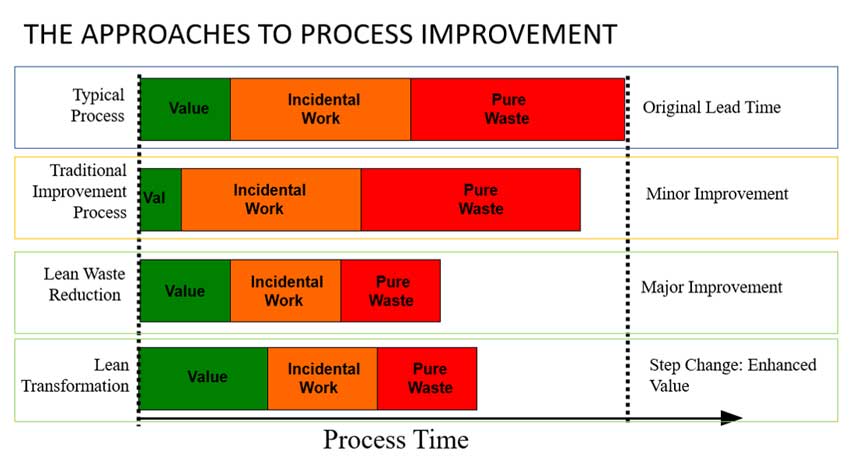
Gemba walks should be done on a regular basis. If they are done correctly, they can reduce waste and improve productivity. They are best done during the busiest periods of the day. This will give project managers and executives a fresh outlook on their businesses. It is important to note any potential improvements, such as new products and services, or any ideas from employees.
FAQ
Why automate your warehouse?
Modern warehousing has seen automation take center stage. With the rise of ecommerce, there is a greater demand for faster delivery times as well as more efficient processes.
Warehouses must adapt quickly to meet changing customer needs. To do so, they must invest heavily in technology. Automating warehouses has many benefits. Here are some of the reasons automation is worth your investment:
-
Increases throughput/productivity
-
Reduces errors
-
Increases accuracy
-
Safety enhancements
-
Eliminates bottlenecks
-
Companies can scale up more easily
-
Makes workers more efficient
-
Provides visibility into everything that happens in the warehouse
-
Enhances customer experience
-
Improves employee satisfaction
-
It reduces downtime, and increases uptime
-
Ensures quality products are delivered on time
-
Removing human error
-
Helps ensure compliance with regulations
What is the difference between Production Planning, Scheduling and Production Planning?
Production Planning (PP) refers to the process of determining how much production is needed at any given moment. Forecasting and identifying production capacity are two key elements to this process.
Scheduling involves the assignment of dates and times to tasks in order to complete them within the timeframe.
Is automation important in manufacturing?
Not only is automation important for manufacturers, but it's also vital for service providers. It enables them to provide services faster and more efficiently. It also helps to reduce costs and improve productivity.
Statistics
- [54][55] These are the top 50 countries by the total value of manufacturing output in US dollars for its noted year according to World Bank.[56] (en.wikipedia.org)
- In 2021, an estimated 12.1 million Americans work in the manufacturing sector.6 (investopedia.com)
- (2:04) MTO is a production technique wherein products are customized according to customer specifications, and production only starts after an order is received. (oracle.com)
- It's estimated that 10.8% of the U.S. GDP in 2020 was contributed to manufacturing. (investopedia.com)
- You can multiply the result by 100 to get the total percent of monthly overhead. (investopedia.com)
External Links
How To
How to Use Just-In-Time Production
Just-intime (JIT), which is a method to minimize costs and maximize efficiency in business process, is one way. It is a process where you get the right amount of resources at the right moment when they are needed. This means that you only pay for what you actually use. The term was first coined by Frederick Taylor, who developed his theory while working as a foreman in the early 1900s. Taylor observed that overtime was paid to workers if they were late in working. He decided to ensure workers have enough time to do their jobs before starting work to improve productivity.
JIT teaches you to plan ahead and prepare everything so you don’t waste time. You should also look at the entire project from start to finish and make sure that you have sufficient resources available to deal with any problems that arise during the course of your project. If you expect problems to arise, you will be able to provide the necessary equipment and personnel to address them. This way, you won't end up paying extra money for things that weren't really necessary.
There are many JIT methods.
-
Demand-driven: This is a type of JIT where you order the parts/materials needed for your project regularly. This will let you track the amount of material left over after you've used it. It will also allow you to predict how long it takes to produce more.
-
Inventory-based: This allows you to store the materials necessary for your projects in advance. This allows one to predict how much they will sell.
-
Project-driven: This approach involves setting aside sufficient funds to cover your project's costs. You will be able to purchase the right amount of materials if you know what you need.
-
Resource-based JIT is the most widespread form. This is where you assign resources based upon demand. For example, if there is a lot of work coming in, you will have more people assigned to them. You'll have fewer orders if you have fewer.
-
Cost-based: This is a similar approach to resource-based but you are not only concerned with how many people you have, but also how much each one costs.
-
Price-based: This approach is very similar to the cost-based method except that you don't look at individual workers costs but the total cost of the company.
-
Material-based is an alternative to cost-based. Instead of looking at the total cost in the company, this method focuses on the average amount of raw materials that you consume.
-
Time-based JIT: This is another variant of resource-based JIT. Instead of worrying about how much each worker costs, you can focus on how long the project takes.
-
Quality-based JIT: Another variation on resource-based JIT. Instead of thinking about how much each employee costs or how long it takes to manufacture something, you think about how good the quality of your product is.
-
Value-based JIT is the newest form of JIT. In this instance, you are not concerned about the product's performance or meeting customer expectations. Instead, you focus on the added value that you provide to your market.
-
Stock-based is an inventory-based system that measures the number of items produced at any given moment. It is used when production goals are met while inventory is kept to a minimum.
-
Just-in-time (JIT) planning: This is a combination of JIT and supply chain management. It's the process of scheduling delivery of components immediately after they are ordered. It reduces lead times and improves throughput.