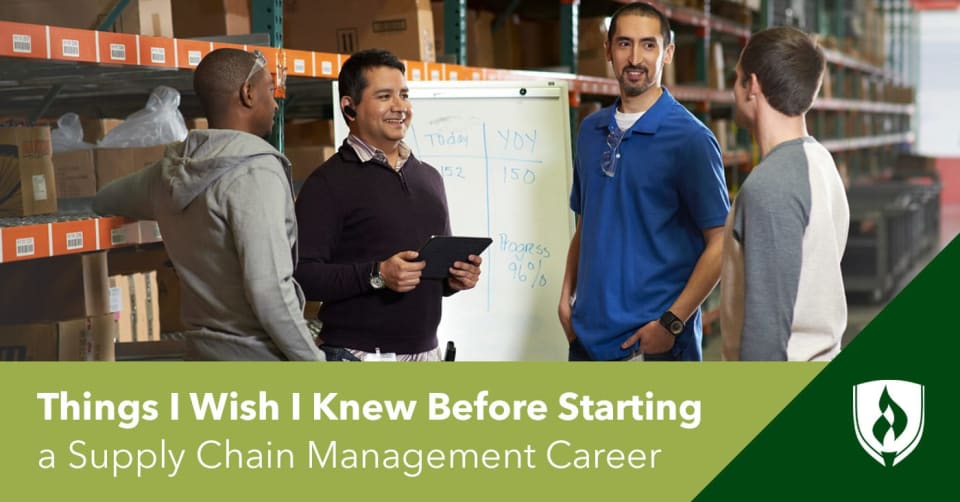
During Manufacturing Day, manufacturers across the nation celebrate the contributions of the modern manufacturing sector to the United States economy. This celebration is held the first Friday of every month. This celebration is also an opportunity to encourage the next generation to pursue careers in manufacturing.
Manufacturing Day can celebrated through many events. These events can be organized by schools, corporations, and other organizations. Some events can include factory tours and presentations. Others might provide virtual content on local manufacturers. Many of these events provide hands-on opportunities for students.
The economic vitality of manufacturers is essential. Every dollar spent on manufacturing produces $2.79 in the economic economy. Noting that manufacturing is a skilled industry, it is important to point out that they require skilled workers. Small manufacturers spend 2.5 times as much as large manufacturers.
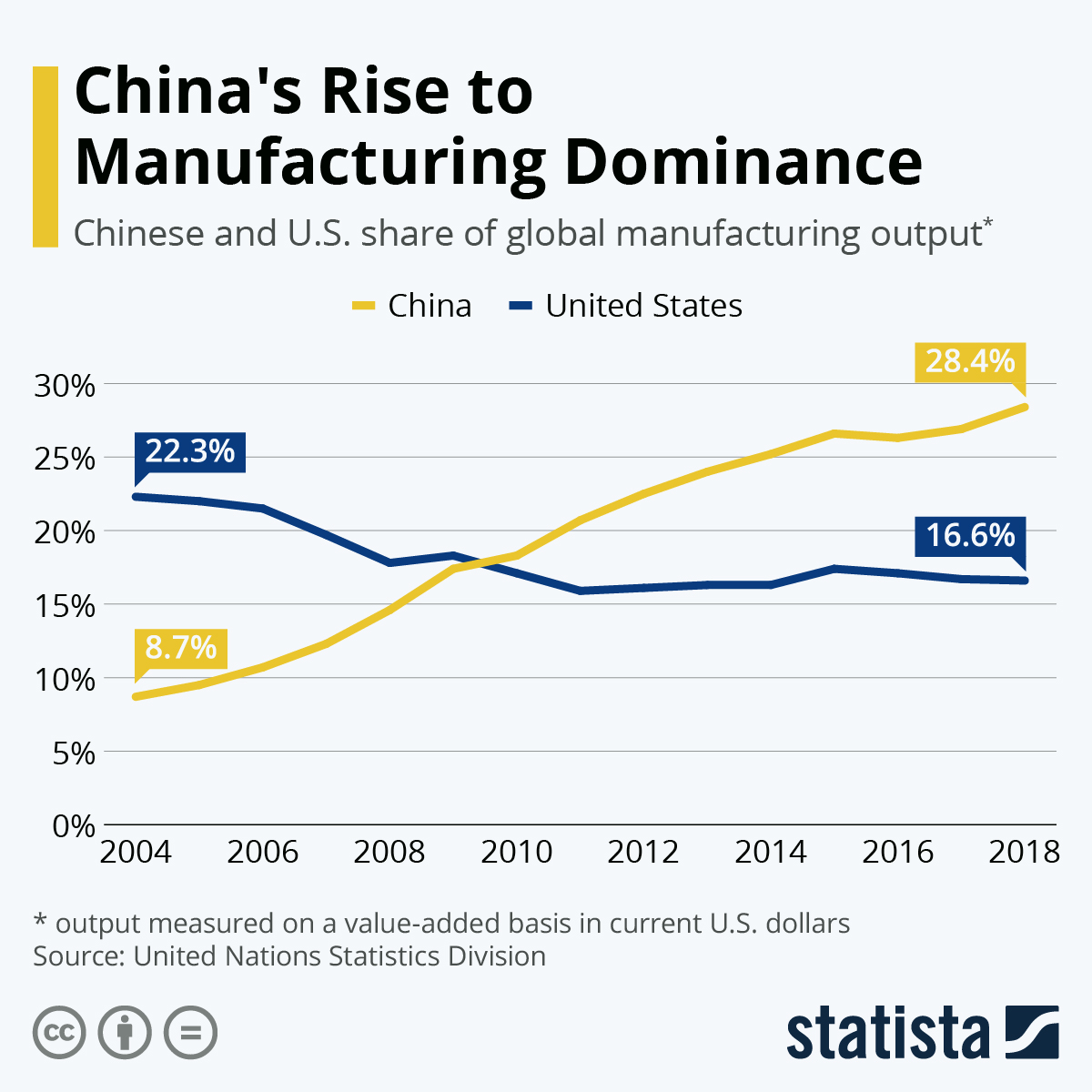
Manufacturing Day has been supported by many federal agencies including the Department of Education, Advanced Manufacturing Office and the National Association of Manufacturers. Manufacturers have the opportunity to network with their local communities and schools on this special day. These agencies provide support and resources for planning events. They can also help with factory tours and official proclamations.
Some companies organize special seminars to inspire youth to pursue a career in manufacturing. These initiatives are also supported by The Manufacturing Institute, a National Association of Manufacturers workforce development partner. The Institute offers resources to assist manufacturers in addressing industry challenges and building stronger communities. The Institute supports veterans and women in manufacturing.
The Biden/Harris administration aims to revive the manufacturing sector. They will be focusing on creating strong supply chains, investing in R&D, and also investing in manufacturing education.
AIM's 3D Virtual Reality Headsets offer students the opportunity to get an immersive experience in advanced manufacturing jobs. AIM is also working with schools around Detroit to get students to visit factories that manufacture products. The virtual tours of these facilities will provide students with an understanding of how these facilities are able to produce high-quality products. Students will have the opportunity to participate in virtual panels.
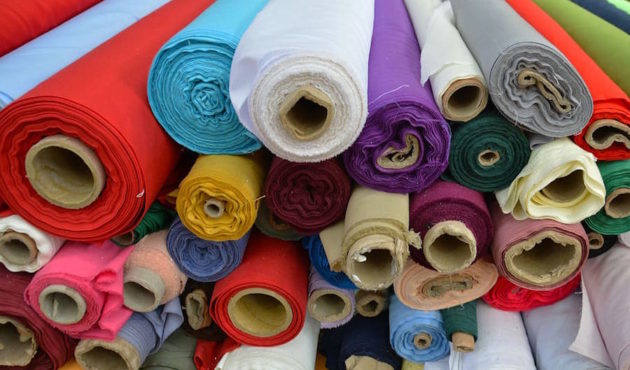
Manufacturing Day events are not the only thing that are celebrated. The National Strategy for Advanced Manufacturing is also a big deal. The Strategy encourages all manufacturers to be involved in educational opportunities and training programs that are beneficial to the local economy. To help people find manufacturing jobs, manufacturers can host job fairs.
By attending an event organized by the Manufacturing Institute, students can learn more about career options in manufacturing. This event is also intended to promote inclusion and diversity in manufacturing. Some events feature testimonials from individuals who work in manufacturing.
The National Association of Manufacturers (Factorators and Manufacturers Association) and the National Retail Federation (National Retail Federation) will offer many educational opportunities and demonstrate the importance of manufactured goods. Students will have the opportunity to learn more about manufacturing and explore the many career options in this sector.
FAQ
How can manufacturing overproduction be reduced?
Better inventory management is key to reducing excess production. This would decrease the time that is spent on inefficient activities like purchasing, storing, or maintaining excess stock. By doing this, we could free up resources for other productive tasks.
Kanban systems are one way to achieve this. A Kanban Board is a visual display that tracks work progress. Kanban systems are where work items travel through a series of states until reaching their final destination. Each state represents a different priority.
For instance, when work moves from one stage to another, the current task is complete enough to be moved to the next stage. A task that is still in the initial stages of a process will be considered complete until it moves on to the next stage.
This allows you to keep work moving along while making sure that no work gets neglected. Managers can monitor the work being done by Kanban boards to see what is happening at any given time. This information allows them to adjust their workflow based on real-time data.
Lean manufacturing is another way to manage inventory levels. Lean manufacturing works to eliminate waste throughout every stage of the production chain. Anything that does not contribute to the product's value is considered waste. There are several types of waste that you might encounter:
-
Overproduction
-
Inventory
-
Packaging not required
-
Material surplus
By implementing these ideas, manufacturers can improve efficiency and cut costs.
What are the 7 Rs of logistics.
The 7R's of Logistics is an acronym for the seven basic principles of logistics management. It was developed by the International Association of Business Logisticians (IABL) and published in 2004 as part of its "Seven Principles of Logistics Management" series.
The acronym consists of the following letters:
-
Responsive - ensure all actions are legal and not harmful to others.
-
Reliable - You can have confidence that you will fulfill your promises.
-
Reasonable - use resources efficiently and don't waste them.
-
Realistic - consider all aspects of operations, including cost-effectiveness and environmental impact.
-
Respectful - Treat people fairly and equitably
-
Reliable - Find ways to save money and increase your productivity.
-
Recognizable: Provide customers with value-added service
What is the difference between Production Planning and Scheduling?
Production Planning (PP), or production planning, is the process by which you determine what products are needed at any given time. This is done through forecasting demand and identifying production capacities.
Scheduling refers the process by which tasks are assigned dates so that they can all be completed within the given timeframe.
Statistics
- You can multiply the result by 100 to get the total percent of monthly overhead. (investopedia.com)
- According to a Statista study, U.S. businesses spent $1.63 trillion on logistics in 2019, moving goods from origin to end user through various supply chain network segments. (netsuite.com)
- It's estimated that 10.8% of the U.S. GDP in 2020 was contributed to manufacturing. (investopedia.com)
- Job #1 is delivering the ordered product according to specifications: color, size, brand, and quantity. (netsuite.com)
- According to the United Nations Industrial Development Organization (UNIDO), China is the top manufacturer worldwide by 2019 output, producing 28.7% of the total global manufacturing output, followed by the United States, Japan, Germany, and India.[52][53] (en.wikipedia.org)
External Links
How To
How to Use lean manufacturing in the Production of Goods
Lean manufacturing is a management system that aims at increasing efficiency and reducing waste. It was created in Japan by Taiichi Ohno during the 1970s and 80s. He received the Toyota Production System award (TPS), from Kanji Toyoda, founder of TPS. The first book published on lean manufacturing was titled "The Machine That Changed the World" written by Michael L. Watkins and published in 1990.
Lean manufacturing refers to a set of principles that improve the quality, speed and costs of products and services. It emphasizes eliminating waste and defects throughout the value stream. Just-in-time (JIT), zero defect (TPM), and 5S are all examples of lean manufacturing. Lean manufacturing eliminates non-value-added tasks like inspection, rework, waiting.
Lean manufacturing can help companies improve their product quality and reduce costs. Additionally, it helps them achieve their goals more quickly and reduces employee turnover. Lean Manufacturing is one of the most efficient ways to manage the entire value chains, including suppliers and customers as well distributors and retailers. Many industries worldwide use lean manufacturing. Toyota's philosophy has been a key driver of success in many industries, including automobiles and electronics.
Five basic principles of Lean Manufacturing are included in lean manufacturing
-
Define Value- Identify the added value your company brings to society. What makes you stand out from your competitors?
-
Reduce Waste - Remove any activity which doesn't add value to your supply chain.
-
Create Flow - Ensure work moves smoothly through the process without interruption.
-
Standardize & Simplify - Make processes as consistent and repeatable as possible.
-
Building Relationships – Establish personal relationships with both external and internal stakeholders.
Lean manufacturing is not a new concept, but it has been gaining popularity over the last few years due to a renewed interest in the economy following the global financial crisis of 2008. Many businesses are now using lean manufacturing to improve their competitiveness. Economists think that lean manufacturing is a crucial factor in economic recovery.
Lean manufacturing, which has many benefits, is now a standard practice in the automotive industry. These include higher customer satisfaction, lower inventory levels, lower operating expenses, greater productivity, and improved overall safety.
Any aspect of an enterprise can benefit from Lean manufacturing. However, it is particularly useful when applied to the production side of an organization because it ensures that all steps in the value chain are efficient and effective.
There are three types of lean manufacturing.
-
Just-in-Time Manufacturing (JIT): This type of lean manufacturing is commonly referred to as "pull systems." JIT is a method in which components are assembled right at the moment of use, rather than being manufactured ahead of time. This method reduces lead times, increases availability, and decreases inventory.
-
Zero Defects Manufacturing: ZDM ensures that no defective units leave the manufacturing plant. Repairing a part that is damaged during assembly should be done, not scrapping. This applies to finished goods that may require minor repairs before shipment.
-
Continuous Improvement (CI): CI aims to improve the efficiency of operations by continuously identifying problems and making changes in order to eliminate or minimize waste. Continuous Improvement (CI) involves continuous improvement in processes, people, tools, and infrastructure.