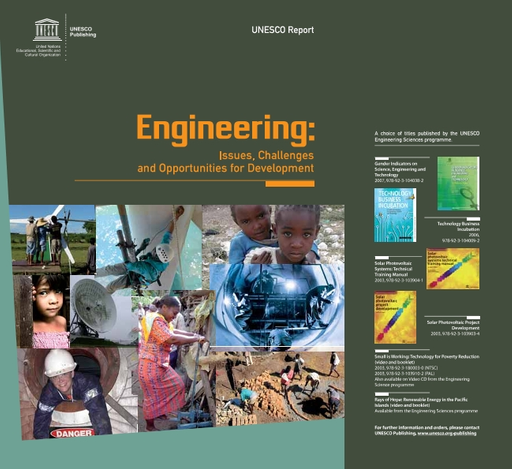
Lean manufacturing is a great way to reduce costs, improve lead times and minimize set-up and turnaround times. Lean manufacturing has clear benefits. They reduce lead times and costs while improving customer service. These are the key benefits of lean manufacturing, which can help you grow your business. If you still aren't convinced, here's three reasons.
Reduced costs
Lean manufacturing can result in significant cost savings. Lean manufacturing can help manufacturers save money by reducing labor costs and reducing defects. Because labor costs are less motivating, decision-making becomes easier. Eliminating hazardous waste is another advantage. Direct labor costs are below 15% in many industries. It is difficult to justify outsourcing manufacturing to low cost locations. This can reduce overall manufacturing costs and improve customer service.
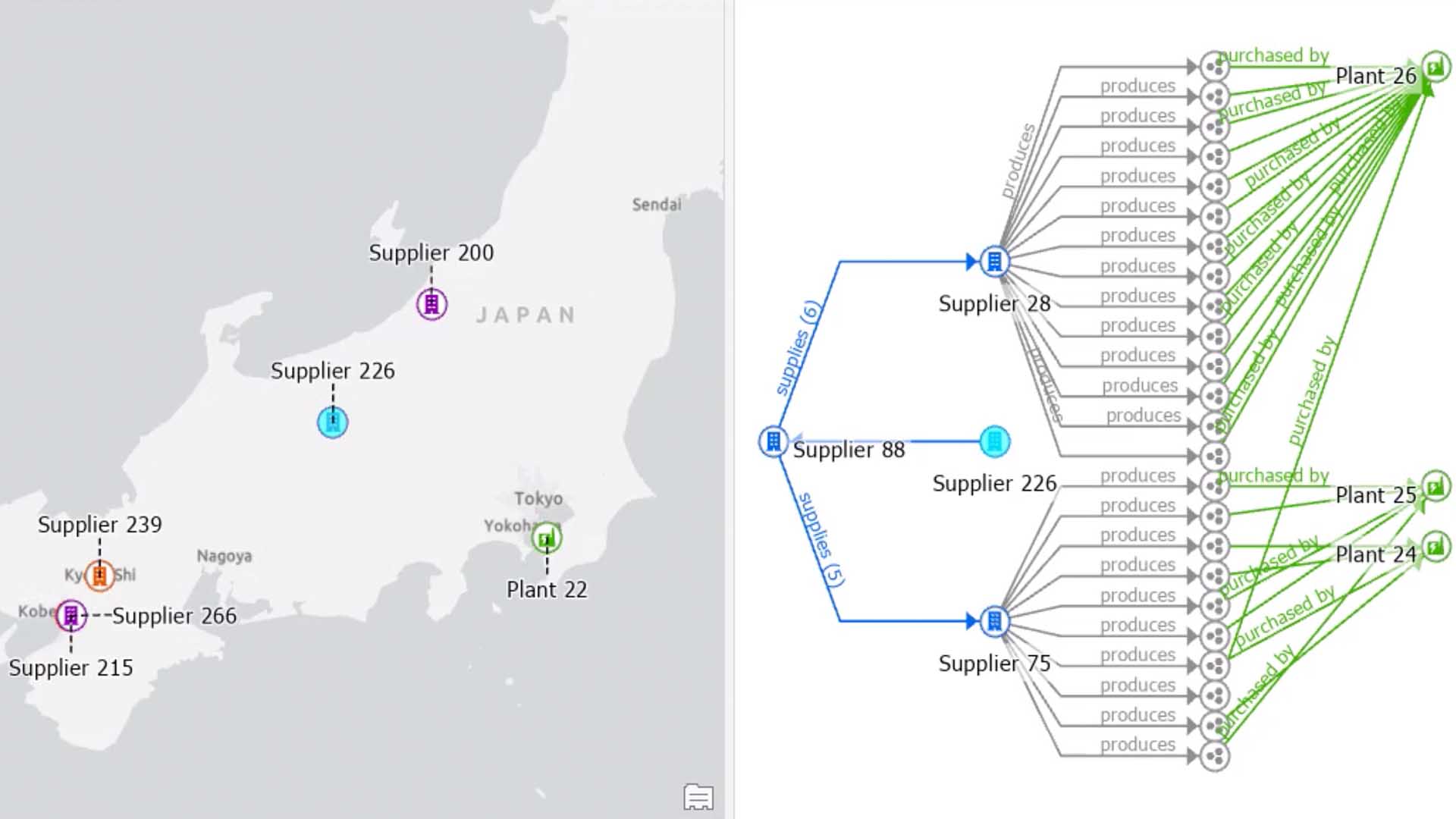
This improves lead times
Lean manufacturing can have many benefits. For example, it reduces waste and increases lead time. Lean manufacturing is a philosophy that emphasizes continuous improvement or kaizen. It unites the talents of employees, encourages accountability and collaboration, and is a way to bring out the best in them. The process can decrease lead times by as high as 20% The key aspect of lean manufacturing, however, is the ability to make small improvements often in order to improve the product's quality and efficiency.
Shortens set-up times
A significant way to reduce the amount of time required to produce a product is by reducing set-up times. Setup time refers to the amount of time required to switch from the last item on a previous order to the first good item on the next. Setup time encompasses preparation, replacement, and location activities. These activities can be internal or external. Internal activities, like moving or positioning an item, require that the process be inactive. However, external setup activities may still be possible.
Reduces time it takes to get to market
The concept of Lean manufacturing, or the process of continuous improvement, was developed in Japan during the rebuilding period after World War II. It was developed to improve competition and reduce lead time. Companies can respond to customer demand and increase profitability by shortening the time taken for a product's arrival on the market. This approach to production will not only increase the efficiency of manufacturing, but also improve the overall efficiency of the facility.
Improves product quality
Lean manufacturing's success depends on the ability to reduce waste, improve product quality, and minimize costs. Both large and small manufacturers have used it. It decreases lead times, costs, and labor. Read on for more information on how lean manufacturing can improve your business. Here are some areas that you need to be focused on. Lean principles can lower lead times by as much as 90%, improve product performance, and reduce costs.
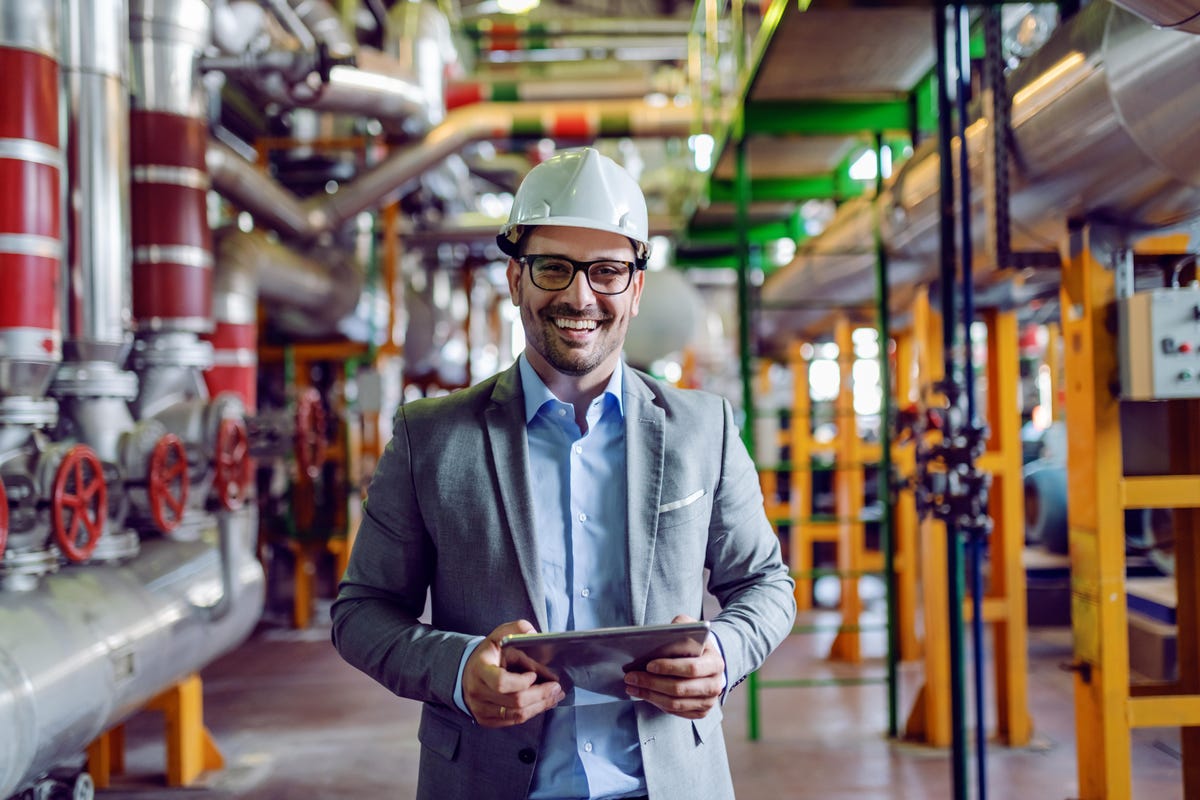
Lower indirect labor costs
Lean manufacturing's low hanging fruit is the reduction of indirect labor cost. True lean companies are not concerned with direct labor efficiency but rather look at ways to cut indirect labor cost. This means eliminating material handling and inspection jobs. It's the same approach used by Toyota and other lean manufacturing companies. In this article, we'll take a closer look at how lean manufacturing can lower indirect labor costs.
FAQ
What are the 7 Rs of logistics?
The 7R's of Logistics is an acronym for the seven basic principles of logistics management. It was created by the International Association of Business Logisticians and published in 2004 under its "Seven Principles of Logistics Management".
The following letters make up the acronym:
-
Responsible - to ensure that all actions are within the legal requirements and are not detrimental to others.
-
Reliable: Have faith in your ability or the ability to honor any promises made.
-
Be responsible - Use resources efficiently and avoid wasting them.
-
Realistic - Take into consideration all aspects of operations including cost-effectiveness, environmental impact, and other factors.
-
Respectful - Treat people fairly and equitably
-
Reliable - Find ways to save money and increase your productivity.
-
Recognizable - Provide value-added services to customers
How can manufacturing overproduction be reduced?
It is essential to find better ways to manage inventory to reduce overproduction. This would reduce the amount of time spent on unnecessary activities such as purchasing, storing, and maintaining excess stock. We could use these resources to do other productive tasks.
A Kanban system is one way to achieve this. A Kanban board, a visual display to show the progress of work, is called a Kanban board. A Kanban system allows work items to move through several states before reaching their final destination. Each state has a different priority level.
As an example, if work is progressing from one stage of the process to another, then the current task is complete and can be transferred to the next. But if a task remains in the beginning stages it will stay that way until it reaches its end.
This allows work to move forward and ensures that no work is missed. With a Kanban board, managers can see exactly how much work is being done at any given moment. This information allows them to adjust their workflow based on real-time data.
Lean manufacturing is another way to manage inventory levels. Lean manufacturing seeks to eliminate waste from every step of the production cycle. Waste includes anything that does not add value to the product. These are some of the most common types.
-
Overproduction
-
Inventory
-
Packaging that is not necessary
-
Excess materials
These ideas can help manufacturers improve efficiency and reduce costs.
What does it mean to be a manufacturer?
Manufacturing Industries are companies that manufacture products. Consumers are those who purchase these products. These companies employ many processes to achieve this purpose, such as production and distribution, retailing, management and so on. They create goods from raw materials, using machines and various other equipment. This includes all types of manufactured goods, including food items, clothing, building supplies, furniture, toys, electronics, tools, machinery, vehicles, pharmaceuticals, medical devices, chemicals, and many others.
Statistics
- In 2021, an estimated 12.1 million Americans work in the manufacturing sector.6 (investopedia.com)
- (2:04) MTO is a production technique wherein products are customized according to customer specifications, and production only starts after an order is received. (oracle.com)
- Many factories witnessed a 30% increase in output due to the shift to electric motors. (en.wikipedia.org)
- You can multiply the result by 100 to get the total percent of monthly overhead. (investopedia.com)
- Job #1 is delivering the ordered product according to specifications: color, size, brand, and quantity. (netsuite.com)
External Links
How To
How to Use lean manufacturing in the Production of Goods
Lean manufacturing (or lean manufacturing) is a style of management that aims to increase efficiency, reduce waste and improve performance through continuous improvement. It was developed in Japan between 1970 and 1980 by Taiichi Ohno. TPS founder Kanji Tyoda gave him the Toyota Production System, or TPS award. Michael L. Watkins published the book "The Machine That Changed the World", which was the first to be published about lean manufacturing.
Lean manufacturing is often described as a set if principles that help improve the quality and speed of products and services. It emphasizes the elimination and minimization of waste in the value stream. Just-in-time (JIT), zero defect (TPM), and 5S are all examples of lean manufacturing. Lean manufacturing focuses on eliminating non-value-added activities such as rework, inspection, and waiting.
Lean manufacturing improves product quality and costs. It also helps companies reach their goals quicker and decreases employee turnover. Lean manufacturing has been deemed one of the best ways to manage the entire value-chain, including customers, distributors as well retailers and employees. Many industries worldwide use lean manufacturing. Toyota's philosophy, for example, is what has enabled it to be successful in electronics, automobiles, medical devices, healthcare and chemical engineering as well as paper and food.
Five fundamental principles underlie lean manufacturing.
-
Define value - Find out what your business contributes to society, and what makes it different from other competitors.
-
Reduce waste - Get rid of any activity that does not add value to the supply chain.
-
Create Flow - Ensure work moves smoothly through the process without interruption.
-
Standardize & Simplify - Make processes as consistent and repeatable as possible.
-
Build Relationships - Establish personal relationships with both internal and external stakeholders.
Lean manufacturing is not a new concept, but it has been gaining popularity over the last few years due to a renewed interest in the economy following the global financial crisis of 2008. Many businesses are now using lean manufacturing to improve their competitiveness. Some economists even believe that lean manufacturing can be a key factor in economic recovery.
Lean manufacturing is becoming a popular practice in automotive. It has many advantages. These include higher customer satisfaction levels, reduced inventory levels as well as lower operating costs.
Any aspect of an enterprise can benefit from Lean manufacturing. This is because it ensures efficiency and effectiveness in all stages of the value chain.
There are three types principally of lean manufacturing:
-
Just-in-Time Manufacturing (JIT): This type of lean manufacturing is commonly referred to as "pull systems." JIT is a method in which components are assembled right at the moment of use, rather than being manufactured ahead of time. This approach is designed to reduce lead times and increase the availability of components. It also reduces inventory.
-
Zero Defects Manufacturing (ZDM),: ZDM is a system that ensures no defective units are left the manufacturing facility. You should repair any part that needs to be repaired during an assembly line. This is also true for finished products that require minor repairs before shipping.
-
Continuous Improvement (CI: Continuous improvement aims to increase the efficiency of operations by constantly identifying and making improvements to reduce or eliminate waste. Continuous Improvement involves continuous improvement of processes.