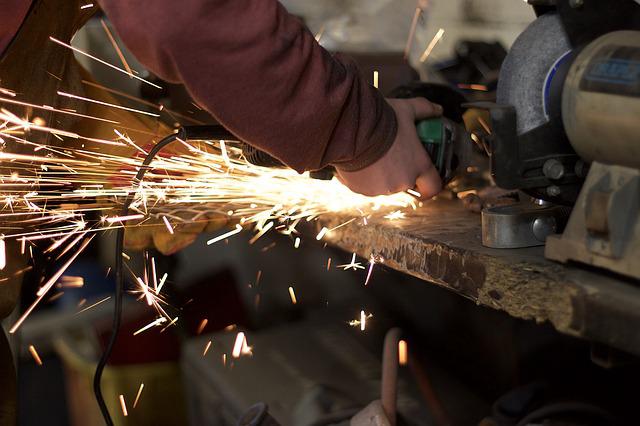
Continuous improvement is built on the principles of PDCA (Plan, Do, Check, Act). If it's done correctly, this method of improving can be highly effective and produce substantial results. Employee involvement is key to continuous improvement, and a variety of resources are required to execute the process. However, measurement and costing are just two benefits of the process. Without customers and employees, the PDCA Cycle is incomplete.
PDCA Cycle
Continuous improvement demands that you apply the PDCA Cycle to all aspects of your business. This cycle works by continuously improving a process and building on past improvements. As the team tests new processes, you might be able to spot new trends. Or, you may discover a new baseline that can help you identify areas of improvement. The PDCA cycle is a great tool to use for identifying improvement opportunities, but it also requires that you apply it carefully and in a controlled manner.
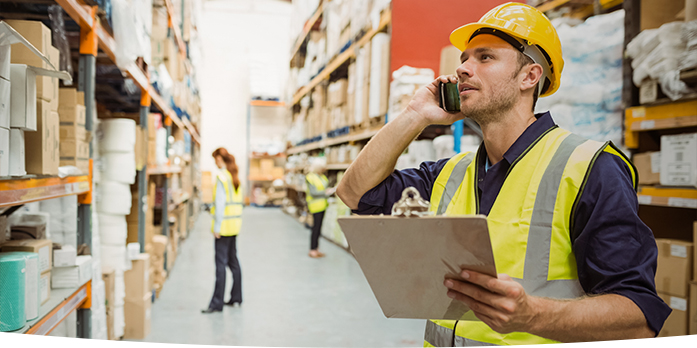
Participation by employees
There are many ways to describe employee involvement, but all successful organizations recognize its importance. Research has shown that employee engagement is directly linked to positive work outcomes. There are several types of employee involvement: direct communication, representative participation through unions and upward problem solving. These types of employee involvement can be reinforced by the culture, environment and leadership of the organization. These are some examples for employee involvement.
Measurement
Many companies now include measurements in their continuous improvements initiatives. W. Edwards Deming introduced The Deming Cycle. This cycle includes a Check phase which assesses how well an improvement program is meeting its goals. If the results fall below expectations, adjustments are made to improve them. Until the results are satisfactory, it is repeated. These are part of continuous improvement.
Costs
For CI to be considered cost-effective, it is essential that an enterprise-wide cost evaluation of CI efforts be done. The cost-benefit analysis should be based on the business imperative of achieving the highest possible customer satisfaction and employee engagement scores. To ensure success, the cost-benefit analysis must also consider the ROI of CI initiatives as well as the fine-tuning budgets. The cost-benefit analyses should concentrate on improving performance in key business processes. They should also benchmark key performance areas against industry averages and top competitors.
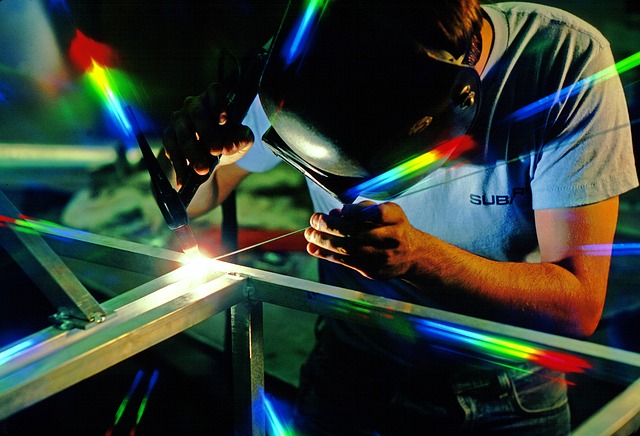
Benefits
Continuous improvement has many benefits. The likelihood of major breakthroughs is greater if you focus on learning from failure. You can encourage employees to take responsibility for their work and feel invested in the company by encouraging them to identify areas for improvement. Likewise, a team that focuses on testing new technologies or tools may also lead to more empowered employees. And the benefits of continuous improvement go beyond saving money. Successful changes can improve employee satisfaction as well as make employees' jobs easier.
FAQ
What does manufacturing industry mean?
Manufacturing Industries are businesses that produce products for sale. These products are sold to consumers. These companies use various processes such as production, distribution, retailing, management, etc., to fulfill this purpose. They create goods from raw materials, using machines and various other equipment. This covers all types of manufactured goods including clothing, food, building supplies and furniture, as well as electronics, tools, machinery, vehicles and pharmaceuticals.
How can I learn about manufacturing?
You can learn the most about manufacturing by getting involved in it. If that is not possible, you could always read books or view educational videos.
How can we reduce manufacturing overproduction?
The key to reducing overproduction lies in developing better ways to manage inventory. This would reduce the amount of time spent on unnecessary activities such as purchasing, storing, and maintaining excess stock. We could use these resources to do other productive tasks.
Kanban systems are one way to achieve this. A Kanbanboard is a visual tool that allows you to keep track of the work being done. Kanban systems allow work items to move through different states until they reach their final destination. Each state represents a different priority level.
When work is completed, it can be transferred to the next stage. If a task is still in its beginning stages, it will continue to be so until it reaches the end.
This keeps work moving and ensures no work is lost. Managers can see how much work has been done and the status of each task at any time with a Kanban Board. This allows them to adjust their workflows based on real-time information.
Lean manufacturing, another method to control inventory levels, is also an option. Lean manufacturing is about eliminating waste from all stages of the production process. Anything that does nothing to add value to a product is waste. These are some of the most common types.
-
Overproduction
-
Inventory
-
Unnecessary packaging
-
Overstock materials
Manufacturers can reduce their costs and improve their efficiency by using these ideas.
Statistics
- It's estimated that 10.8% of the U.S. GDP in 2020 was contributed to manufacturing. (investopedia.com)
- (2:04) MTO is a production technique wherein products are customized according to customer specifications, and production only starts after an order is received. (oracle.com)
- You can multiply the result by 100 to get the total percent of monthly overhead. (investopedia.com)
- In 2021, an estimated 12.1 million Americans work in the manufacturing sector.6 (investopedia.com)
- According to a Statista study, U.S. businesses spent $1.63 trillion on logistics in 2019, moving goods from origin to end user through various supply chain network segments. (netsuite.com)
External Links
How To
How to Use 5S to Increase Productivity in Manufacturing
5S stands to stand for "Sort", “Set In Order", “Standardize", and "Store". Toyota Motor Corporation was the first to develop the 5S approach in 1954. It allows companies to improve their work environment, thereby achieving greater efficiency.
The basic idea behind this method is to standardize production processes, so they become repeatable, measurable, and predictable. This means that daily tasks such as cleaning and sorting, storage, packing, labeling, and packaging are possible. These actions allow workers to perform their job more efficiently, knowing what to expect.
There are five steps that you need to follow in order to implement 5S. Each step is a different action that leads to greater efficiency. If you sort items, it makes them easier to find later. When you arrange items, you place them together. You then organize your inventory in groups. Finally, when you label your containers, you ensure everything is labeled correctly.
Employees must be able to critically examine their work practices. Employees should understand why they do the tasks they do, and then decide if there are better ways to accomplish them. They must learn new skills and techniques in order to implement the 5S system.
In addition to improving efficiency, the 5S system also increases morale and teamwork among employees. They feel more motivated to work towards achieving greater efficiency as they see the results.