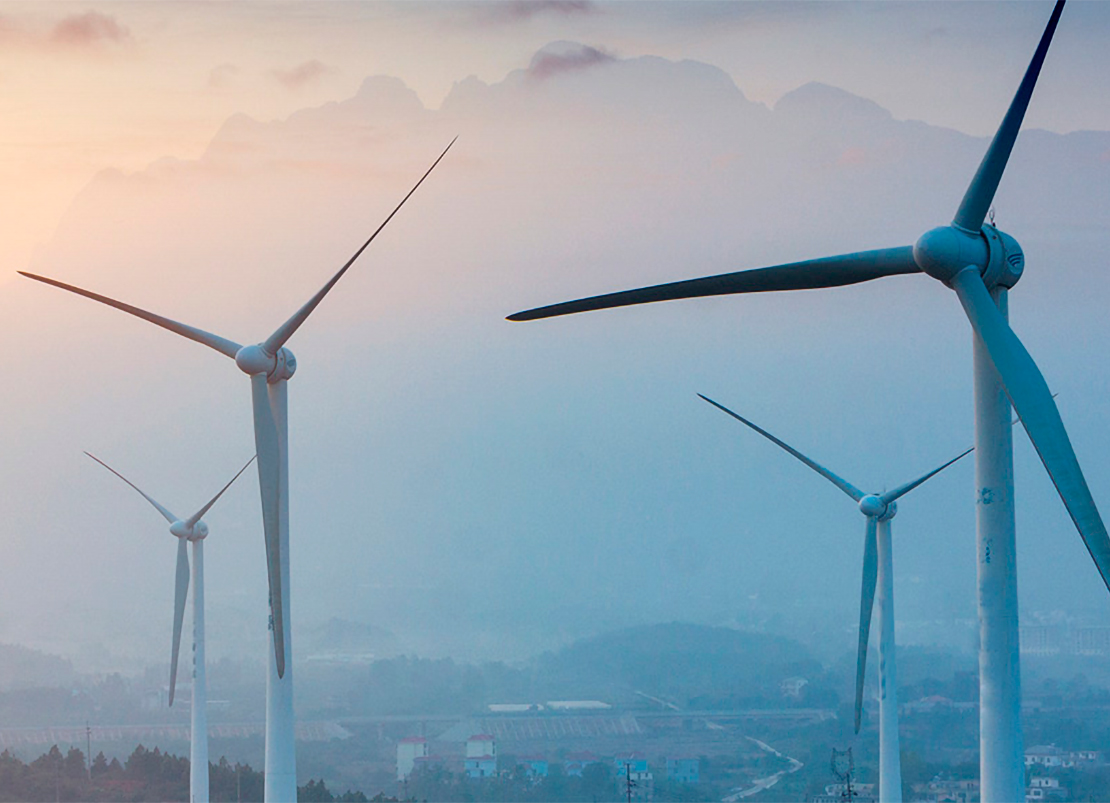
It can be difficult to get started in the manufacturing industry. Besides getting the right funding, manufacturing startups face some unique challenges when raising capital. These challenges can be overcome and the manufacturing industry will succeed.
As a startup, you need to build a strong value proposition. Also, you need to establish a competitive position. To improve your chances of success, it is important to partner with other manufacturers, universities, and non-profits. Also, it is crucial to meet with your customers early in order to fully understand their needs.
The manufacturing industry needs fresh, technology-driven upstarts. The government has pledged to be an enabler. Along with creating a policy framework for startups, the government also offers grants to help you get bank loan loans. These grants do not carry a monetary obligation, so they are not repaid. Venture capital can be used to co-finance investments.
The average American startup receives funding of around 22 million dollars. Around 75 percent of this funding goes to software startups. The remaining 15 percent go to additive manufacturing startups. Angel investors provide the majority of the funding for the most innovative startups. Most venture capitalists fund software solutions, data analytics, and innovative service delivery.
Entrepreneurs complain about not being able to find the right talent. You also need to find ways to protect your intellectual property rights. These include trademarks, copyright and design protection. Y Combinator will allow you to connect with a powerful group of investors early in your venture.
You may also wish to partner with nonprofits and universities, as you do with local civic infrastructure. A laundry aggregator may want to offer customers faster turnaround times, better quality and less water. These are all value-added service. Another option is to use a low overhead recurring revenue model and high revenue multipliers.
Startups offer a unique way to establish industry standards and create network effects. As a result, you can improve your chances of success by bringing a diverse range of talent to your company. Startups may also be able to help you obtain debt financing. You will have enough time to build a prototype, and to demonstrate your value proposition.
If you want to take advantage of these opportunities, you need to act quickly. Manufacturing is experiencing rapid innovation and manufacturers have to adapt in order to keep up. To do so, you need to take a risk and act quickly. This opens new avenues of funding, including venture capital and private-equity.
Grant funding is available for manufacturing startups. This grants them the ability to get bank loans, do more R&D and create prototypes. They also have the option to use incubators which offer them free access and a lot of flexibility.
FAQ
Why is logistics important for manufacturing?
Logistics are an integral part any business. They enable you to achieve outstanding results by helping manage product flow from raw materials through to finished goods.
Logistics play an important role in reducing costs as well as increasing efficiency.
How can manufacturing efficiency improved?
The first step is to identify the most important factors affecting production time. Next, we must find ways to improve those factors. You can start by identifying the most important factors that impact production time. Once you've identified them, try to find solutions for each of those factors.
Why automate your factory?
Modern warehouses have become more dependent on automation. The rise of e-commerce has led to increased demand for faster delivery times and more efficient processes.
Warehouses must adapt quickly to meet changing customer needs. To do so, they must invest heavily in technology. Automation warehouses can bring many benefits. These are some of the benefits that automation can bring to warehouses:
-
Increases throughput/productivity
-
Reduces errors
-
Increases accuracy
-
Safety increases
-
Eliminates bottlenecks
-
Companies can scale up more easily
-
It makes workers more efficient
-
Provides visibility into everything that happens in the warehouse
-
Enhances customer experience
-
Improves employee satisfaction
-
It reduces downtime, and increases uptime
-
Quality products delivered on time
-
Human error can be eliminated
-
Assure compliance with regulations
What are the 7 R's of logistics?
The acronym 7Rs of Logistics refers to the seven core principles of logistics management. It was developed and published by the International Association of Business Logisticians in 2004 as part of the "Seven Principles of Logistics Management".
The following letters form the acronym:
-
Responsive - ensure all actions are legal and not harmful to others.
-
Reliable - You can have confidence that you will fulfill your promises.
-
Reasonable - make sure you use your resources well and don't waste them.
-
Realistic – Consider all aspects, including cost-effectiveness as well as environmental impact.
-
Respectful – Treat others fairly and equitably.
-
Responsive - Look for ways to save time and increase productivity.
-
Recognizable: Provide customers with value-added service
Statistics
- It's estimated that 10.8% of the U.S. GDP in 2020 was contributed to manufacturing. (investopedia.com)
- (2:04) MTO is a production technique wherein products are customized according to customer specifications, and production only starts after an order is received. (oracle.com)
- In 2021, an estimated 12.1 million Americans work in the manufacturing sector.6 (investopedia.com)
- [54][55] These are the top 50 countries by the total value of manufacturing output in US dollars for its noted year according to World Bank.[56] (en.wikipedia.org)
- Job #1 is delivering the ordered product according to specifications: color, size, brand, and quantity. (netsuite.com)
External Links
How To
Six Sigma: How to Use it in Manufacturing
Six Sigma is defined by "the application SPC (statistical process control) techniques to achieve continuous improvements." Motorola's Quality Improvement Department, Tokyo, Japan, developed it in 1986. Six Sigma is a method to improve quality through standardization and elimination of defects. Many companies have adopted Six Sigma in recent years because they believe that there are no perfect products and services. Six Sigma aims to reduce variation in the production's mean value. This means that you can take a sample from your product and then compare its performance to the average to find out how often the process differs from the norm. If there is a significant deviation from the norm, you will know that something needs to change.
Understanding how variability works in your company is the first step to Six Sigma. Once you understand that, it is time to identify the sources of variation. These variations can also be classified as random or systematic. Random variations occur when people make mistakes; systematic ones are caused by factors outside the process itself. If you make widgets and some of them end up on the assembly line, then those are considered random variations. But if you notice that every widget you make falls apart at the exact same place each time, this would indicate that there is a problem.
Once you identify the problem areas, it is time to create solutions. The solution could involve changing how you do things, or redesigning your entire process. You should then test the changes again after they have been implemented. If they don't work, you will need to go back to the drawing boards and create a new plan.