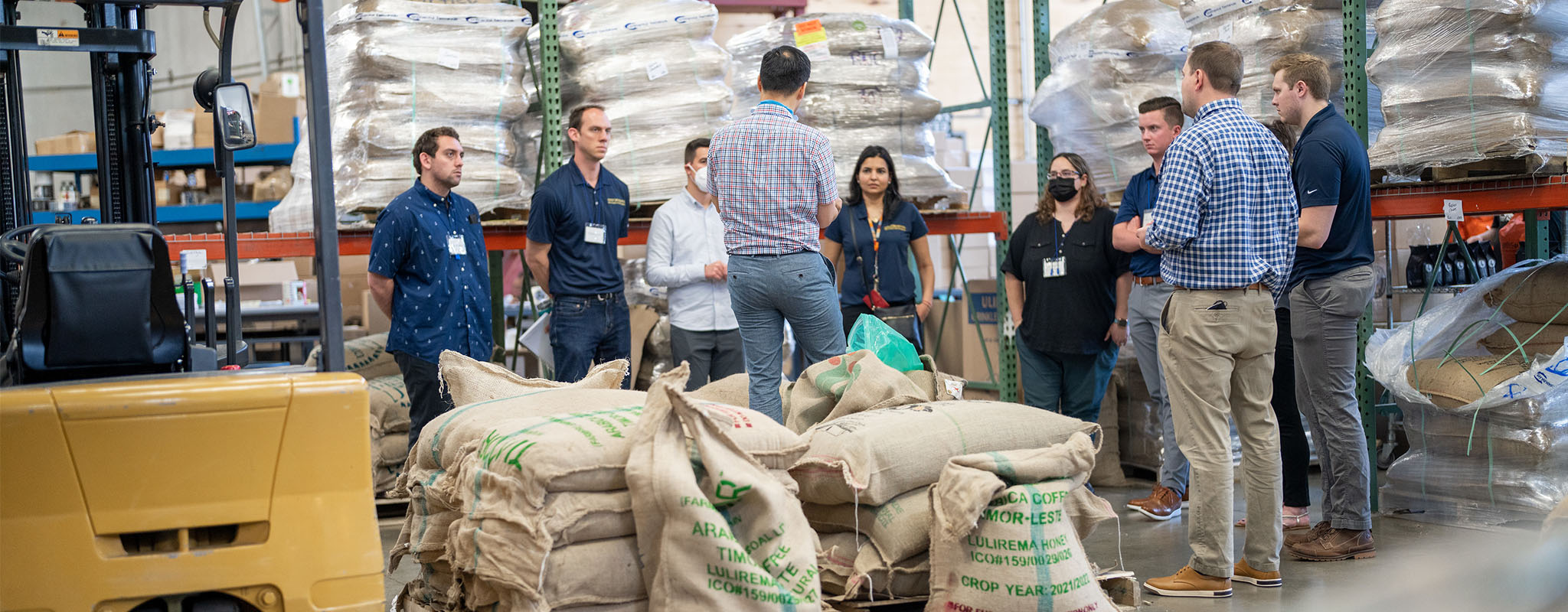
Demand management is a method that ensures that customers are satisfied. It basically involves bridging between supply and marketing, allowing companies to predict the demand. The process can help companies improve the speed and quality of delivery, reduce the amount of invoice disputes, and lower the cost of running the business.
Companies that have a robust demand management process are more open to market changes. They have a process in place to identify the ideal client, which can help with marketing.
Businesses can use demand management to plan for future demand and improve customer satisfaction. It can also help reduce the number invoice disputes and improve asset usage if done right. A proper demand management strategy can also improve operational flexibility and operational resiliency.
Project management software can help improve demand management. These software programs can be used by teams to coordinate their work and avoid silos. Companies can also use change management plans to quickly address supply chain issues.
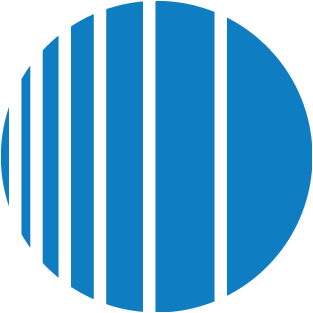
ILOG's PowerOps Suite, for example, integrates manufacturing scheduling functions. Similarly, QAD and Dynasys offer applications that allow organizations to create a demand and supply plan. These applications allow organizations to visualize the effects of changes on their supply chain. Optiant also offers ERP solutions that enable organizations to create efficient, consistent and effective order and supply management processes.
Similarly, tools like CDC Software, Terra Technology and Real-Time Inventory offer real-time forecasting solutions that can reduce the number of supply chain disruptions. Companies can also benefit from the collaborative management strategy which allows them to share information. It includes performance indicators, knowledge sharing, and planning joint actions.
It is important to take into account a few things before you start to implement a demand-management strategy. These factors can help professionals better understand the process and focus on the most important aspects.
One of the most critical factors in a demand management process is leadership buy-in. Demand management is an extremely collaborative process that involves multiple levels of management. Among the highest-level players are top executives and managers who are responsible for ensuring that all members are on the same page. The success of the initiative is also dependent on the participation of those at lower levels.
There are many tools that can help you implement a demand/supply plan. But here are some things to keep in mind.
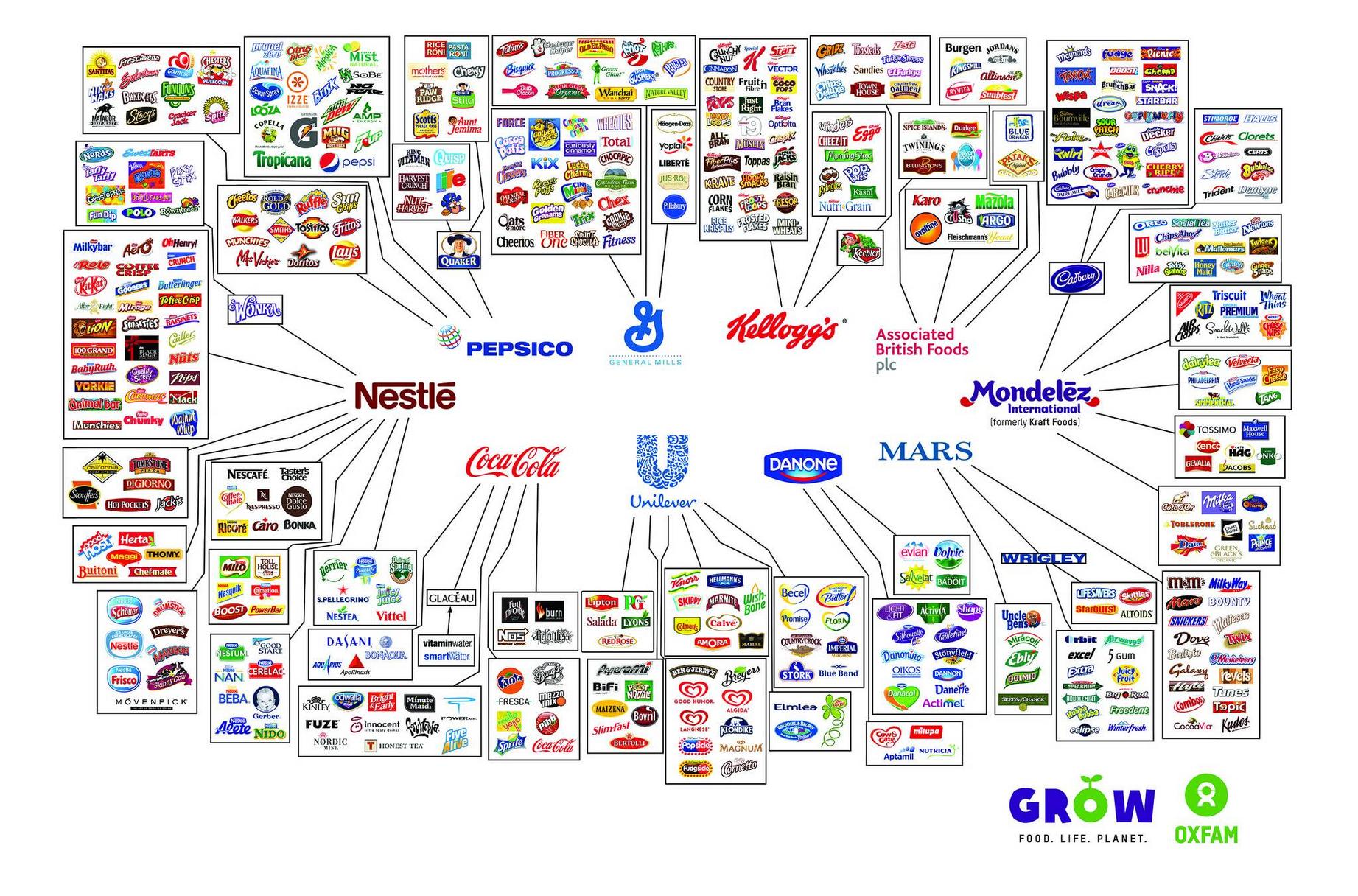
It is crucial to understand the market and identify the ideal customer. An organization must be able to accurately measure and analyze the outcomes of its efforts, in addition to knowing which customers to target.
Businesses need to be more agile in order to develop a demand management plan that is easily adaptable to changing circumstances. An effective plan can reduce the tactical forecast error and the number of supply chain disruptions. Last but not least, demand management is an important tool for helping to create and implement portfolios and strategic plans.
FAQ
What's the difference between Production Planning & Scheduling?
Production Planning (PP), or production planning, is the process by which you determine what products are needed at any given time. This can be done by forecasting demand and identifying production capabilities.
Scheduling refers the process by which tasks are assigned dates so that they can all be completed within the given timeframe.
How can we reduce manufacturing overproduction?
In order to reduce excess production, you need to develop better inventory management methods. This would reduce the time needed to manage inventory. This would allow us to use our resources for more productive tasks.
Kanban systems are one way to achieve this. A Kanban board is a visual display used to track work in progress. Work items are moved through various states to reach their destination in a Kanban system. Each state has a different priority level.
For instance, when work moves from one stage to another, the current task is complete enough to be moved to the next stage. A task that is still in the initial stages of a process will be considered complete until it moves on to the next stage.
This keeps work moving and ensures no work is lost. Managers can monitor the work being done by Kanban boards to see what is happening at any given time. This allows them to adjust their workflows based on real-time information.
Lean manufacturing is another option to control inventory levels. Lean manufacturing is about eliminating waste from all stages of the production process. Anything that does not contribute to the product's value is considered waste. These are some of the most common types.
-
Overproduction
-
Inventory
-
Unnecessary packaging
-
Exceed materials
Manufacturers can increase efficiency and decrease costs by implementing these ideas.
How important is automation in manufacturing?
Not only are service providers and manufacturers important, but so is automation. Automation allows them to deliver services quicker and more efficiently. It reduces human errors and improves productivity, which in turn helps them lower their costs.
Can some manufacturing processes be automated?
Yes! Yes. The Egyptians discovered the wheel thousands and years ago. We now use robots to help us with assembly lines.
There are many applications for robotics in manufacturing today. These include:
-
Automation line robots
-
Robot welding
-
Robot painting
-
Robotics inspection
-
Robots that create products
Automation could also be used to improve manufacturing. 3D printing, for example, allows us to create custom products without waiting for them to be made.
How can I find out more about manufacturing?
Hands-on experience is the best way to learn more about manufacturing. You can read books, or watch instructional videos if you don't have the opportunity to do so.
What are the responsibilities of a manufacturing manager
A manufacturing manager must make sure that all manufacturing processes run smoothly and effectively. They should be alert for any potential problems in the company and react accordingly.
They should also be able communicate with other departments, such as sales or marketing.
They must also keep up-to-date with the latest trends in their field and be able use this information to improve productivity and efficiency.
What kind of jobs are there in logistics?
There are many jobs available in logistics. Here are some examples:
-
Warehouse workers – They load, unload and transport pallets and trucks.
-
Transportation drivers – They drive trucks or trailers to transport goods and perform pick-ups.
-
Freight handlers are people who sort and pack freight into warehouses.
-
Inventory managers - They oversee the inventory of goods in warehouses.
-
Sales representatives - They sell products.
-
Logistics coordinators – They plan and coordinate logistics operations.
-
Purchasing agents - They purchase goods and services needed for company operations.
-
Customer service representatives - They answer calls and emails from customers.
-
Ship clerks - They issue bills and process shipping orders.
-
Order fillers – They fill orders based upon what was ordered and shipped.
-
Quality control inspectors are responsible for inspecting incoming and outgoing products looking for defects.
-
Others - There are many other types of jobs available in logistics, such as transportation supervisors, cargo specialists, etc.
Statistics
- (2:04) MTO is a production technique wherein products are customized according to customer specifications, and production only starts after an order is received. (oracle.com)
- You can multiply the result by 100 to get the total percent of monthly overhead. (investopedia.com)
- Many factories witnessed a 30% increase in output due to the shift to electric motors. (en.wikipedia.org)
- In 2021, an estimated 12.1 million Americans work in the manufacturing sector.6 (investopedia.com)
- It's estimated that 10.8% of the U.S. GDP in 2020 was contributed to manufacturing. (investopedia.com)
External Links
How To
Six Sigma: How to Use it in Manufacturing
Six Sigma refers to "the application and control of statistical processes (SPC) techniques in order to achieve continuous improvement." Motorola's Quality Improvement Department in Tokyo, Japan developed Six Sigma in 1986. Six Sigma's basic concept is to improve quality and eliminate defects through standardization. Many companies have adopted this method in recent years. They believe there is no such thing a perfect product or service. Six Sigma seeks to reduce variation between the mean production value. This means that you can take a sample from your product and then compare its performance to the average to find out how often the process differs from the norm. If this deviation is too big, you know something needs fixing.
Understanding the nature of variability in your business is the first step to Six Sigma. Once you have this understanding, you will need to identify sources and causes of variation. Also, you will need to identify the sources of variation. Random variations occur when people make mistakes; systematic ones are caused by factors outside the process itself. For example, if you're making widgets, and some of them fall off the assembly line, those would be considered random variations. It would be considered a systematic problem if every widget that you build falls apart at the same location each time.
Once you have identified the problem, you can design solutions. That solution might involve changing the way you do things or redesigning the process altogether. You should then test the changes again after they have been implemented. If they don't work you need to rework them and come up a better plan.