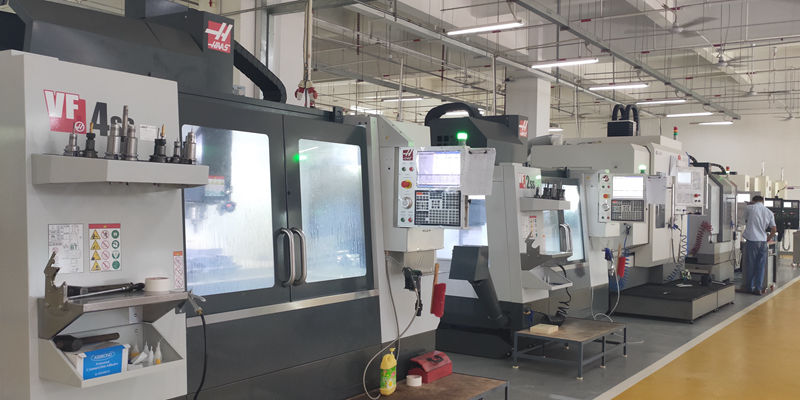
A validation engineer salary is a person's pay for working as a validity engineer. This amount is usually based upon their experience, skills and education. This amount is also influenced by what type of job the employee holds and which company they work for.
What Is A Validation Engineer?
A validation engineer is an engineer who monitors the quality of a product using equipment, processes, and procedures. They are employed in environments such as manufacturing, testing, and research and development to ensure all systems function as expected.
What is the role of a validation engineer?
A validation engineer monitors the performance of equipment and systems used in the production of pharmaceutical products. In order to do so, the engineers analyze, inspect and test equipment and machines. They investigate any anomalies or malfunctions in equipment that could lead to a product failure.
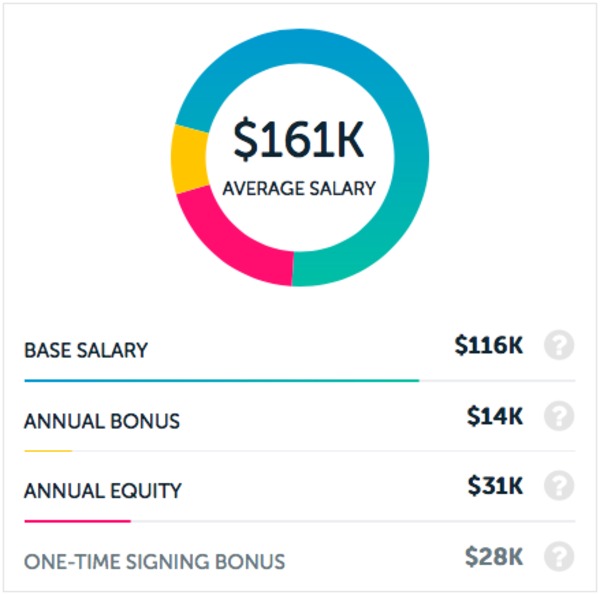
What is the Salary of a Validation Engineer?
A Validation engineer salary is generally high, but it depends on the type of company you work for. Apple and Google often pay the highest salaries. In the pharmaceutical industries, engineers can expect to earn on average $89,130 per annum.
What are some of the most important skills for this profession?
The skills needed for a validation engineer career include an ability to write, execute and coordinate commissioning and qualification protocols. A validation engineer should have solid technical knowledge in manufacturing, process, and software engineering.
How to Become a Validation Engineer
There are a few different routes into a validation engineer role, either by gaining a degree or through an apprenticeship scheme. Employers usually require that applicants have a Bachelor's Degree in a relevant engineering field, such as Electrical, Mechanical or Software.
Then, you can gain experience through an internship or placement in a graduate program for engineers. You can find work through recruitment agencies and careers services, newspapers, or online.
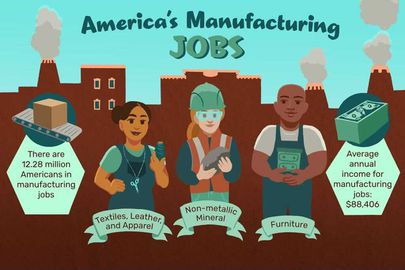
How to Become a Pharmaceutical Validation Engineer
A career as a validation engineer requires the right combination of academic qualifications and practical experience. A degree in science, engineering or pharmacology is required. This can be a challenging path, but it is worth persevering to develop your skills and find a job that suits your qualifications and ambitions.
How to Become an Engineer in Pharma Validation
As a validation engineer, you can choose from a variety of positions with varying degrees of responsibility. As a senior engineer, you can have management-level responsibilities and the opportunity to travel internationally. You can also take on roles that will allow you to specialize in a certain field, like CSV or drugs delivery technologies.
Salary can vary for a validation engineer in pharmaceuticals depending on what industry they are working in and which products they deal with. Although the average national salary for a pharmaceutical validity engineer is $98,150 some cities pay more. Hayward, CA, for example, beats the national average by $18,034 while San Jose, CA is at the top of the list with $21,856.
FAQ
What is the role of a manager in manufacturing?
A manufacturing manager has to ensure that all manufacturing processes work efficiently and effectively. They should also be aware of any problems within the company and act accordingly.
They should also be able and comfortable communicating with other departments like sales and marketing.
They should be up to date on the latest trends and be able apply this knowledge to increase productivity and efficiency.
What is the responsibility of a production planner?
Production planners ensure all aspects of the project are delivered within time and budget. A production planner ensures that the service and product meet the client's expectations.
What are the 7 Rs of logistics?
The acronym 7R's for Logistics stands to represent the seven basic principles in logistics management. It was created by the International Association of Business Logisticians and published in 2004 under its "Seven Principles of Logistics Management".
The following letters make up the acronym:
-
Responsible - ensure that actions are in compliance with legal requirements and do not cause harm to others.
-
Reliable - have confidence in the ability to deliver on commitments made.
-
It is reasonable to use resources efficiently and not waste them.
-
Realistic - Consider all aspects of operations, including environmental impact and cost effectiveness.
-
Respectful – Treat others fairly and equitably.
-
Be resourceful: Look for opportunities to save money or increase productivity.
-
Recognizable is a company that provides customers with value-added solutions.
What are manufacturing and logistic?
Manufacturing is the process of creating goods from raw materials by using machines and processes. Logistics is the management of all aspects of supply chain activities, including procurement, production planning, distribution, warehousing, inventory control, transportation, and customer service. Sometimes manufacturing and logistics are combined to refer to a wider term that includes both the process of creating products as well as their delivery to customers.
What is it like to manage a logistics company?
You need to have a lot of knowledge and skills to manage a successful logistic business. You must have good communication skills to interact effectively with your clients and suppliers. You must be able analyze data and draw out conclusions. You must be able and able to handle stress situations and work under pressure. You must be creative and innovative to develop new ideas to improve efficiency. To motivate and guide your team towards reaching organizational goals, you must have strong leadership skills.
It is important to be organized and efficient in order to meet tight deadlines.
How can excess manufacturing production be reduced?
Improved inventory management is the key to reducing overproduction. This would reduce time spent on activities such as purchasing, stocking, and maintaining excess stock. This will allow us to free up resources for more productive tasks.
One way to do this is to adopt a Kanban system. A Kanban Board is a visual display that tracks work progress. In a Kanban system, work items move through a sequence of states until they reach their final destination. Each state represents a different priority.
For instance, when work moves from one stage to another, the current task is complete enough to be moved to the next stage. But if a task remains in the beginning stages it will stay that way until it reaches its end.
This keeps work moving and ensures no work is lost. Managers can monitor the work being done by Kanban boards to see what is happening at any given time. This data allows them adjust their workflow based upon real-time data.
Lean manufacturing is another option to control inventory levels. Lean manufacturing emphasizes eliminating waste in all phases of production. Any product that isn't adding value can be considered waste. There are several types of waste that you might encounter:
-
Overproduction
-
Inventory
-
Unnecessary packaging
-
Materials in excess
These ideas will help manufacturers increase efficiency and lower costs.
Statistics
- Job #1 is delivering the ordered product according to specifications: color, size, brand, and quantity. (netsuite.com)
- It's estimated that 10.8% of the U.S. GDP in 2020 was contributed to manufacturing. (investopedia.com)
- According to the United Nations Industrial Development Organization (UNIDO), China is the top manufacturer worldwide by 2019 output, producing 28.7% of the total global manufacturing output, followed by the United States, Japan, Germany, and India.[52][53] (en.wikipedia.org)
- Many factories witnessed a 30% increase in output due to the shift to electric motors. (en.wikipedia.org)
- [54][55] These are the top 50 countries by the total value of manufacturing output in US dollars for its noted year according to World Bank.[56] (en.wikipedia.org)
External Links
How To
How to use the Just In-Time Production Method
Just-in time (JIT), is a process that reduces costs and increases efficiency in business operations. It's a way to ensure that you get the right resources at just the right time. This means that you only pay for what you actually use. Frederick Taylor, a 1900s foreman, first coined the term. After observing how workers were paid overtime for late work, he realized that overtime was a common practice. He then concluded that if he could ensure that workers had enough time to do their job before starting to work, this would improve productivity.
JIT is a way to plan ahead and make sure you don't waste any money. It is important to look at your entire project from beginning to end and ensure that you have enough resources to handle any issues that may arise. You will have the resources and people to solve any problems you anticipate. This way, you won't end up paying extra money for things that weren't really necessary.
There are many JIT methods.
-
Demand-driven JIT: This is a JIT that allows you to regularly order the parts/materials necessary for your project. This will allow for you to track the material that you have left after using it. This will allow to you estimate the time it will take for more to be produced.
-
Inventory-based: This allows you to store the materials necessary for your projects in advance. This allows you to forecast how much you will sell.
-
Project-driven: This is an approach where you set aside enough funds to cover the cost of your project. If you know the amount you require, you can buy the materials you need.
-
Resource-based: This is the most common form of JIT. Here, you allocate certain resources based on demand. You will, for example, assign more staff to deal with large orders. If you don't receive many orders, then you'll assign fewer employees to handle the load.
-
Cost-based: This approach is very similar to resource-based. However, you don't just care about the number of people you have; you also need to consider how much each person will cost.
-
Price-based: This is very similar to cost-based, except that instead of looking at how much each individual worker costs, you look at the overall price of the company.
-
Material-based: This approach is similar to cost-based. However, instead of looking at the total cost for the company, you look at how much you spend on average on raw materials.
-
Time-based: This is another variation of resource-based JIT. Instead of focusing only on how much each employee is costing, you should focus on how long it takes to complete your project.
-
Quality-based: This is yet another variation of resource-based JIT. Instead of thinking about the cost of each employee or the time it takes to produce something, you focus on how good your product quality.
-
Value-based JIT : This is the newest type of JIT. In this scenario, you're not concerned about how products perform or whether customers expect them to meet their expectations. Instead, you're focused on how much value you add to the market.
-
Stock-based is an inventory-based system that measures the number of items produced at any given moment. This method is useful when you want to increase production while decreasing inventory.
-
Just-in time (JIT), planning: This is a combination JIT/supply chain management. It's the process of scheduling delivery of components immediately after they are ordered. It's important as it reduces leadtimes and increases throughput.