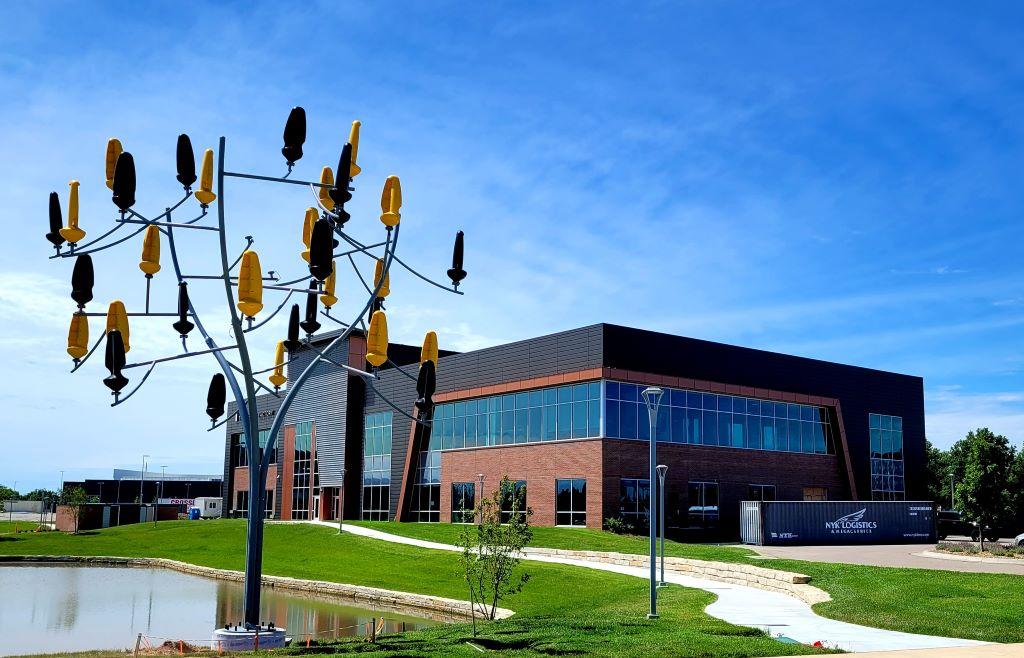
Hoshinkanri and Visual board, as well as Value Stream Mapping and Process Observation and Analy are all part of the lean arsenal. These methods use statistical data and quality control measures to reduce defects and improve process performance. The safety and well-being of employees, the cycle time, delivery times, and quality of raw materials are all improved by Lean tools. These tools are described in more detail in our articles. We also explain the basics of these tools, and give examples.
Hoshin Kanri
Communication is key when it comes down to communicating the goals of each division to one another in order to implement the principles of Hoshin Kari. It's vital to clearly communicate your company's objectives and the results that they produce. Google Images will allow you to view a sample Hoshin Kanri diagram. The main idea of the matrix is that you want to make sure that everyone is aligned on the same goals, so that everyone can work towards them.
Hoshin Kanri can be used to help identify the areas in your business that need improvement. The Hoshin Kanri method helps you identify the most important activities and help you create a clear path that leads from your general goals to specific actions. It helps you track your progress, and shows how each step links to the next. Hoshin Kanri encourages the use of a collaborative approach in order to improve the overall company.
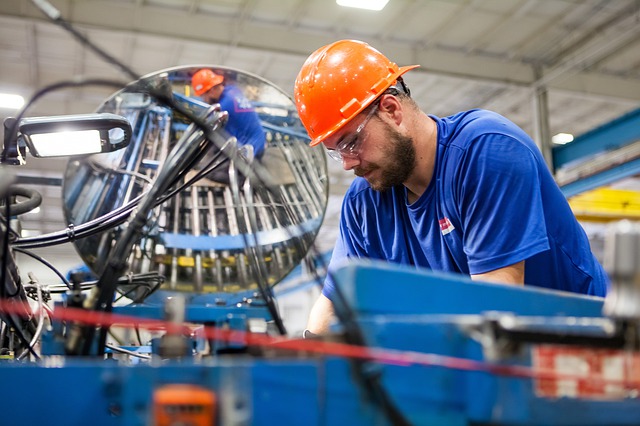
Visual board
Although the visual board is an effective tool to track the progress of a process it is not universal. It cannot be used to implement a process that involves people. A visual management board should be customized for the users in order to create a sense of emotion behind the numbers. You can use it to track performance indicators such as the number of pieces produced in a given time or the hours worked. There is no one universal code for this tool. However, there are several key elements which make it useful in a lean manufacturing environment.
A visual management board allows you to communicate quickly to your team members what is needed and who is responsible for each task. In less than 20 seconds, this information can be seen on the board. The results of these activities must also be visible to management to ensure that everyone is on the same page. A visual management board that is updated frequently can be used to ensure that everyone stays on the right page.
Value Stream Mapping
When using value stream mapping in tools lean, a facilitator must identify the bottleneck or constraint in the process. A bottleneck is the process step with the highest WIP. If a three-step procedure has a throughput speed of 60 units an hour but a potential working capital of 42 units an hour, Step 2 will be the bottleneck. A value stream map can help identify bottlenecks and find process improvements.
Understanding the customer perspective and the system or process is key to a successful value stream mapping. This is a cross-functional process that can be complex. This process may require extensive training and involvement of many people. Larger companies may hire a value stream manager for the mapping. Although value stream mapping may be a big project, smaller projects can identify areas where there are potential savings and improvements. A powerful tool in tools Lean is value stream mapping.

Process Observation and Analysis
Lean management relies on continuous improvement and process monitoring. Process observation is designed to maintain standards and ensure processes produce the expected outcomes. Processes that are abandoned will eventually fail. Process observation or analysis can have cultural implications. Therefore, managers should explain clearly why they need it and the advantages it brings. Lean management systems include process observation and analysis. Managers need to communicate the importance of this part to their teams.
To implement Lean, the first step involves verifying the process flow diagram by performing a walk-through. The next step after this step is completed is to analyze all data. The Measure phase involves gathering data on the current product, process, or service. The project leader applies statistical hypothesis-testing techniques to find the root cause. This analyze determines whether the problem has been solved or improved.
FAQ
What does it take to run a logistics business?
To be a successful businessman in logistics, you will need many skills and knowledge. Good communication skills are essential to effectively communicate with your suppliers and clients. You will need to know how to interpret data and draw conclusions. You must be able and able to handle stress situations and work under pressure. You must be creative and innovative to develop new ideas to improve efficiency. Strong leadership qualities are essential to motivate your team and help them achieve their organizational goals.
To meet tight deadlines, you must also be efficient and organized.
What are the 7 Rs of logistics management?
The acronym "7R's" of Logistics stands for seven principles that underpin logistics management. It was developed by the International Association of Business Logisticians (IABL) and published in 2004 as part of its "Seven Principles of Logistics Management" series.
The acronym consists of the following letters:
-
Responsible - ensure that actions are in compliance with legal requirements and do not cause harm to others.
-
Reliable - have confidence in the ability to deliver on commitments made.
-
Reasonable - use resources efficiently and don't waste them.
-
Realistic – Consider all aspects, including cost-effectiveness as well as environmental impact.
-
Respectful - Treat people fairly and equitably
-
Reliable - Find ways to save money and increase your productivity.
-
Recognizable - Provide value-added services to customers
What is the distinction between Production Planning or Scheduling?
Production Planning (PP) is the process of determining what needs to be produced at any given point in time. This is done through forecasting demand and identifying production capacities.
Scheduling involves the assignment of dates and times to tasks in order to complete them within the timeframe.
What does "warehouse" mean?
A warehouse, or storage facility, is where goods are stored prior to being sold. It can be indoors or out. In some cases it could be both indoors and outdoors.
What are manufacturing and logistic?
Manufacturing is the act of producing goods from raw materials using machines and processes. Logistics covers all aspects involved in managing supply chains, including procurement and production planning. Logistics and manufacturing are often referred to as one thing. It encompasses both the creation of products and their delivery to customers.
Statistics
- Many factories witnessed a 30% increase in output due to the shift to electric motors. (en.wikipedia.org)
- Job #1 is delivering the ordered product according to specifications: color, size, brand, and quantity. (netsuite.com)
- It's estimated that 10.8% of the U.S. GDP in 2020 was contributed to manufacturing. (investopedia.com)
- [54][55] These are the top 50 countries by the total value of manufacturing output in US dollars for its noted year according to World Bank.[56] (en.wikipedia.org)
- According to the United Nations Industrial Development Organization (UNIDO), China is the top manufacturer worldwide by 2019 output, producing 28.7% of the total global manufacturing output, followed by the United States, Japan, Germany, and India.[52][53] (en.wikipedia.org)
External Links
How To
How to Use the Just-In-Time Method in Production
Just-intime (JIT), which is a method to minimize costs and maximize efficiency in business process, is one way. It's a way to ensure that you get the right resources at just the right time. This means that only what you use is charged to your account. Frederick Taylor first coined this term while working in the early 1900s as a foreman. He noticed that workers were often paid overtime when they had to work late. He realized that workers should have enough time to complete their jobs before they begin work. This would help increase productivity.
JIT is an acronym that means you need to plan ahead so you don’t waste your money. The entire project should be looked at from start to finish. You need to ensure you have enough resources to tackle any issues that might arise. You'll be prepared to handle any potential problems if you know in advance. This way, you won't end up paying extra money for things that weren't really necessary.
There are different types of JIT methods:
-
Demand-driven: This JIT is where you place regular orders for the parts/materials that are needed for your project. This will allow to track how much material has been used up. It will also allow you to predict how long it takes to produce more.
-
Inventory-based : You can stock the materials you need in advance. This allows one to predict how much they will sell.
-
Project-driven: This is an approach where you set aside enough funds to cover the cost of your project. When you know how much you need, you'll purchase the appropriate amount of materials.
-
Resource-based JIT : This is probably the most popular type of JIT. You assign certain resources based off demand. For instance, if you have a lot of orders coming in, you'll assign more people to handle them. If you don't receive many orders, then you'll assign fewer employees to handle the load.
-
Cost-based: This is similar to resource-based, except that here you're not just concerned about how many people you have but how much each person costs.
-
Price-based: This is very similar to cost-based, except that instead of looking at how much each individual worker costs, you look at the overall price of the company.
-
Material-based: This approach is similar to cost-based. However, instead of looking at the total cost for the company, you look at how much you spend on average on raw materials.
-
Time-based: This is another variation of resource-based JIT. Instead of focusing on the cost of each employee, you will focus on the time it takes to complete a project.
-
Quality-based JIT - This is another form of resource-based JIT. Instead of focusing on the cost of each worker or how long it takes, think about how high quality your product is.
-
Value-based JIT : This is the newest type of JIT. This is where you don't care about how the products perform or whether they meet customers' expectations. Instead, you're focused on how much value you add to the market.
-
Stock-based. This method is inventory-based and focuses only on the actual production at any given point. It's used when you want to maximize production while minimizing inventory.
-
Just-intime (JIT), planning is a combination JIT management and supply chain management. It is the process of scheduling components' delivery as soon as they have been ordered. It's important because it reduces lead times and increases throughput.