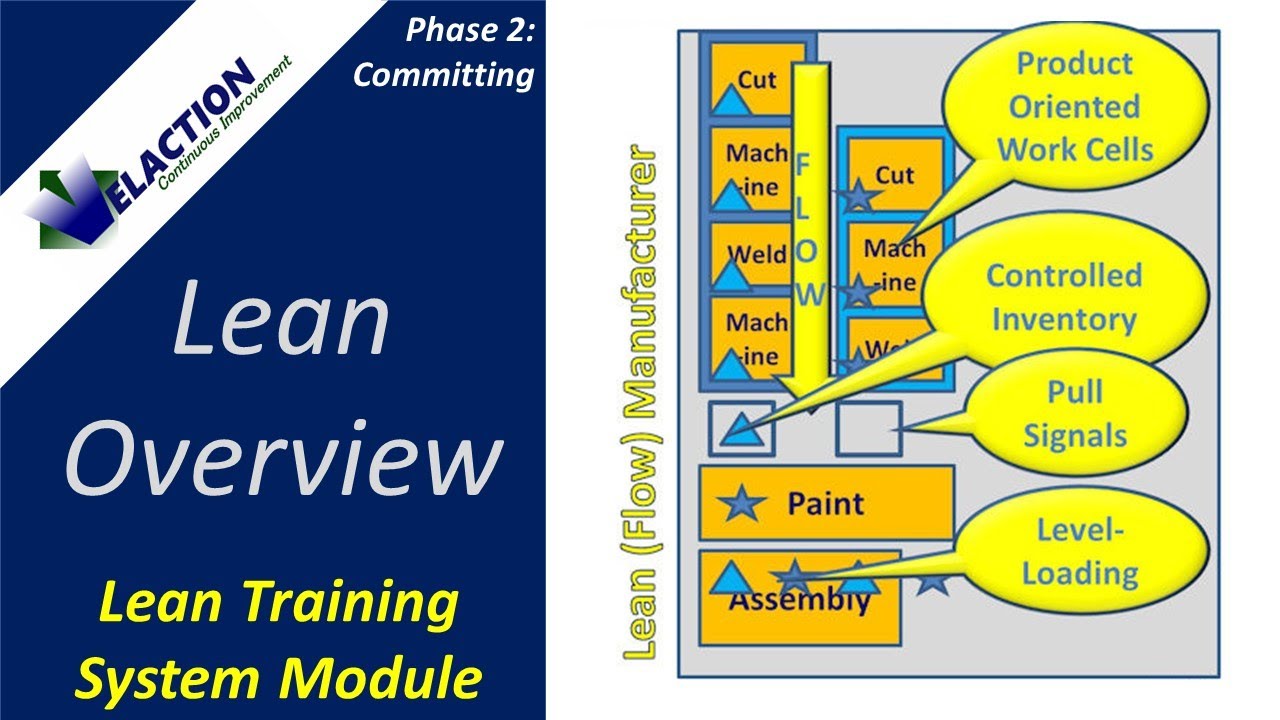
Japanese factories make high-quality products at affordable prices. They are the backbone and 5% of the GDP of Japan. However, they have struggled to cope with tighter standards as well growing competition and the rising cost pressures caused by the recent recession.
For example, last year, a government white paper found that Japanese firms were unprepared to deal with a parts procurement cutoff. The Japanese auto industry was hard hit by the recession. Traditionally, the car manufacturing industry relies on 30,000 different parts, so a disruption to the supply chain can stop production. Some parts can't be substituted.
Japanese manufacturers work closely with suppliers to resolve problems and increase efficiency in order to maintain high quality products. They welcome feedback from employees, salesmen, quality inspectors and others.
Japanese manufacturers have been concerned by the increasing number of factory floor accidents. There have been numerous safety scandals in the country's industrial sector. This has increased scrutiny over the quality of work in factories.
Non-regular staff is another problem that has impacted the production of Japanese products. While non-regular employees can help companies reduce labor costs, they also increase the risk for accidents and de-skill their production floor. To make their workers safer and more productive, companies have started to train regular employees.
Japan's increasing labor shortage is due to its declining birthrate. The proportion of companies complaining about a labor shortage has reached a 25-year peak. Japanese companies will face increased challenges if the workforce shrinks.
Despite the shortage of skilled workers, a large percentage of factories have been cutting costs. A growing number of so-called "factries" employ fewer than ten people. Many of these small workshops create the finest equipment in the entire world.
China and South Korea are increasing their competition for the Japanese manufacturing sector. Many factories are now trying to increase productivity and reduce costs. However, the Japanese government warned that the industry would suffer if it loses its competitive advantage in foreign markets.
Japan is facing increasing competition from Asia and elsewhere, and the question of whether it can adapt its processes to keep up with demand and adapt fast enough. Even if it is able to adapt, skilled workers are expected to increase.
Japanese factories are a major source of components for global markets. They are also a source of advanced materials, such as silicon chips, that are used in computers and smart phones. Although Chinese factories are skilled in low-cost assembly, the Japanese supply essential components.
Despite their efforts to improve productivity and quality, Japanese companies have been subject to increased competition from overseas. They have had to lower their product's value in the domestic marketplace due to the recession. Despite these difficulties, the Japanese managed to continue producing high quality products.
FAQ
What is the importance of logistics in manufacturing?
Logistics are an essential part of any business. They help you achieve great results by helping you manage all aspects of product flow, from raw materials to finished goods.
Logistics also play a major role in reducing costs and increasing efficiency.
Is automation important in manufacturing?
Automating is not just important for manufacturers, but also for service providers. It enables them to provide services faster and more efficiently. It reduces human errors and improves productivity, which in turn helps them lower their costs.
How can we reduce manufacturing overproduction?
It is essential to find better ways to manage inventory to reduce overproduction. This would reduce time spent on activities such as purchasing, stocking, and maintaining excess stock. This would allow us to use our resources for more productive tasks.
Kanban systems are one way to achieve this. A Kanban Board is a visual display that tracks work progress. Kanban systems are where work items travel through a series of states until reaching their final destination. Each state has a different priority level.
As an example, if work is progressing from one stage of the process to another, then the current task is complete and can be transferred to the next. It is possible to keep a task in the beginning stages until it gets to the end.
This keeps work moving and ensures no work is lost. Managers can see how much work has been done and the status of each task at any time with a Kanban Board. This allows them the ability to adjust their workflow using real-time data.
Lean manufacturing, another method to control inventory levels, is also an option. Lean manufacturing works to eliminate waste throughout every stage of the production chain. Any product that isn't adding value can be considered waste. The following are examples of common waste types:
-
Overproduction
-
Inventory
-
Unnecessary packaging
-
Excess materials
These ideas will help manufacturers increase efficiency and lower costs.
What is the difference between manufacturing and logistics
Manufacturing is the act of producing goods from raw materials using machines and processes. Logistics manages all aspects of the supply chain, including procurement, production planning and distribution, inventory control, transportation, customer service, and transport. As a broad term, manufacturing and logistics often refer to both the creation and delivery of products.
What are the 7 Rs of logistics management?
The 7R's of Logistics is an acronym for the seven basic principles of logistics management. It was developed by International Association of Business Logisticians (IABL), and published as part of their "Seven Principles of Logistics Management Series" in 2004.
The acronym is made up of the following letters:
-
Responsive - ensure all actions are legal and not harmful to others.
-
Reliable - Have confidence in your ability to fulfill all of your commitments.
-
Reasonable - make sure you use your resources well and don't waste them.
-
Realistic - Take into consideration all aspects of operations including cost-effectiveness, environmental impact, and other factors.
-
Respectful - treat people fairly and equitably.
-
Reliable - Find ways to save money and increase your productivity.
-
Recognizable - provide customers with value-added services.
How can manufacturing avoid production bottlenecks
To avoid production bottlenecks, ensure that all processes run smoothly from the moment you receive your order to the time the product ships.
This includes planning for capacity requirements as well as quality control measures.
Continuous improvement techniques like Six Sigma are the best way to achieve this.
Six Sigma is a management method that helps to improve quality and reduce waste.
It seeks to eliminate variation and create consistency in your work.
How does a production planner differ from a project manager?
The primary difference between a producer planner and a manager of a project is that the manager usually plans and organizes the whole project, while a production planner is only involved in the planning stage.
Statistics
- Many factories witnessed a 30% increase in output due to the shift to electric motors. (en.wikipedia.org)
- According to the United Nations Industrial Development Organization (UNIDO), China is the top manufacturer worldwide by 2019 output, producing 28.7% of the total global manufacturing output, followed by the United States, Japan, Germany, and India.[52][53] (en.wikipedia.org)
- It's estimated that 10.8% of the U.S. GDP in 2020 was contributed to manufacturing. (investopedia.com)
- In the United States, for example, manufacturing makes up 15% of the economic output. (twi-global.com)
- In 2021, an estimated 12.1 million Americans work in the manufacturing sector.6 (investopedia.com)
External Links
How To
How to use 5S in Manufacturing to Increase Productivity
5S stands for "Sort", 'Set In Order", 'Standardize', & Separate>. The 5S methodology was developed at Toyota Motor Corporation in 1954. This methodology helps companies improve their work environment to increase efficiency.
This method aims to standardize production processes so that they are repeatable, measurable and predictable. This means that every day tasks such cleaning, sorting/storing, packing, and labeling can be performed. Because workers know what they can expect, this helps them perform their jobs more efficiently.
There are five steps to implementing 5S, including Sort, Set In Order, Standardize, Separate and Store. Each step is a different action that leads to greater efficiency. If you sort items, it makes them easier to find later. When items are ordered, they are put together. After you have divided your inventory into groups you can store them in easy-to-reach containers. Finally, when you label your containers, you ensure everything is labeled correctly.
Employees must be able to critically examine their work practices. Employees must be able to see why they do what they do and find a way to achieve them without having to rely on their old methods. To implement the 5S system, employees must acquire new skills and techniques.
The 5S Method not only improves efficiency, but it also helps employees to be more productive and happier. They feel more motivated to work towards achieving greater efficiency as they see the results.