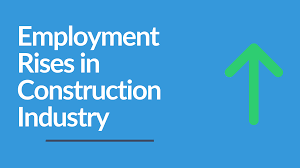
The field of manufacturing engineering is often referred to as production engineering. This type of engineering shares many common ideas and concepts with other engineering fields. A person who specializes in this area of engineering can find their own niche in an industry and become an integral part of a company's success. These engineers are capable of ensuring that a product meets high quality standards.
Duties of the job
As a production engineer, you will be responsible for coordinating and analysing the entire production process from design through implementation. This position requires careful attention to detail and a commitment to the safety of the workplace. Production engineers ensure that the company meets high quality standards and protects the environment. They also evaluate current production activities and identify ways to improve.
Production engineers are key to a company's ability to produce goods quickly and economically. They also play an important role in the implementation of automation. Their work may include analyzing current production processes, as well as focusing their attention on one aspect of the production process. They can also adjust plant software or train production workers.
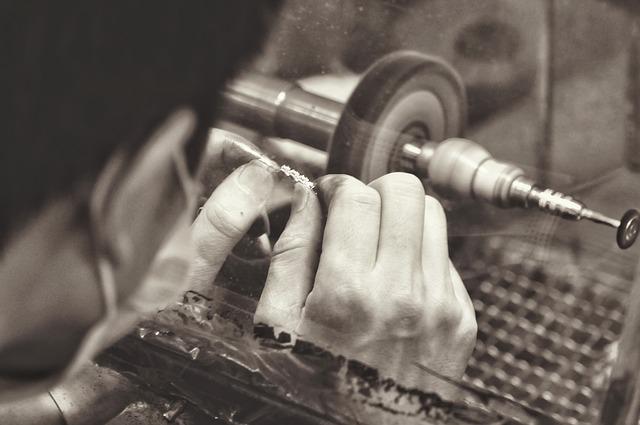
Excellent communication skills are essential for this job. Engineers must be able understand complex engineering concepts. This is because engineering can involve complex mathematics and calculations. An engineer in production may use equations to calculate the cost of a finished product or solve problems on the manufacturing line.
Education required
First, earn a bachelor’s degree in industrial or manufacturing engineering to get a job as a production engineer. Some employers may prefer a master's degree, especially for research-oriented manufacturing positions. A proficiency in one or two specialized areas is also helpful.
Industrial engineers are creative and analytical, which helps to improve production processes. They are interested in reducing waste and developing new ways to make use of equipment and workers. As they have to be able to explain complicated processes to nontechnical audiences, they also need to possess good communication skills. Good communication skills also involve being able to listen carefully and fully understand the views and opinions of others.
Manufacturing engineers get hands-on training during the degree program. They will also learn about safety procedures and regulations. A Professional Engineer license issued by the National Society of Professional Engineers is required. This license is crucial because it will show employers and clients that the credentials you have are legitimate. It's also important to renew your license according to state requirements.
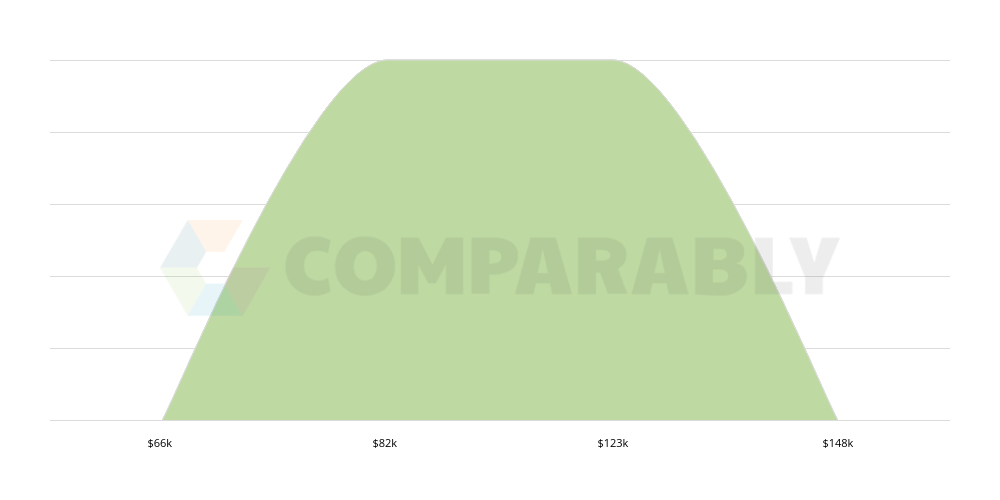
Salary
The salary of a production engineer varies greatly, depending on location and company. Production engineers typically work in an office environment but may also travel to the production site to inspect machinery and make improvements. Some production engineers work for themselves, while others are employed by larger companies. In addition to their salary, production engineers are expected to complete their work in a timely manner.
Production engineers work in collaboration with other professionals to ensure the safety and quality of the final product. To ensure the best production processes, they will work closely with designers. They may also be responsible for maintaining safety standards and training factory workers in safety procedures. This job description isn't exhaustive, but it gives an idea of the duties and responsibilities of a production engineer.
The salary of a production engineering worker depends on the amount of experience. Entry-level production engineers earn approximately Rs2.5 lakhs annually. Mid-level engineers could earn Rs3.8 Lakhs. An experienced production engineer can expect to earn Rs6.1 lakhs each year.
FAQ
What type of jobs is there in logistics
Logistics can offer many different jobs. Some examples are:
-
Warehouse workers: They load and unload trucks, pallets, and other cargo.
-
Transportation drivers: They drive trucks and trailers and deliver goods and make pick-ups.
-
Freight handlers: They sort and package freight in warehouses.
-
Inventory managers – These people oversee inventory at warehouses.
-
Sales reps - They sell products and services to customers.
-
Logistics coordinators – They plan and coordinate logistics operations.
-
Purchasing agents - They purchase goods and services needed for company operations.
-
Customer service agents - They answer phone calls and respond to emails.
-
Ship clerks - They issue bills and process shipping orders.
-
Order fillers - These people fill orders based on what has been ordered.
-
Quality control inspectors – They inspect incoming and outgoing products to ensure that there are no defects.
-
Others - There is a variety of other jobs in logistics. These include transportation supervisors and cargo specialists.
What is the job of a production plan?
Production planners ensure that all project aspects are completed on time, within budget and within the scope. They make sure that the product and services meet client expectations.
What does it mean to warehouse?
A warehouse or storage facility is where goods are stored before they are sold. It can be an outdoor or indoor area. Sometimes, it can be both an indoor and outdoor space.
What is production planning?
Production Planning involves developing a plan for all aspects of the production, including scheduling, budgeting, casting, crew, location, equipment, props, etc. This document will ensure everything is in order and ready to go when you need it. This document should include information about how to achieve the best results on-set. This includes location information, crew details, equipment specifications, and casting lists.
First, you need to plan what you want to film. You may have already decided where you would like to shoot, or maybe there are specific locations or sets that you want to use. Once you have identified the scenes and locations, you can start to determine which elements are required for each scene. For example, you might decide that you need a car but don't know exactly what model you want. To narrow your options, you can search online for available models.
Once you have found the right car, you can start thinking about extras. Are you looking for people to sit in the front seats? Perhaps you have someone who needs to be able to walk around the back of your car. Perhaps you would like to change the interior colour from black to white. These questions will help to determine the style and feel of your car. Another thing you can do is think about what type of shots are desired. Do you want to film close-ups, or wider angles? Maybe you want to show your engine or the steering wheel. This will allow you to determine the type of car you want.
Once you have determined all of the above, you can move on to creating a schedule. You will know when you should start and when you should finish shooting. The schedule will show you when to get there, what time to leave, and when to return home. This way, everyone knows what they need to do and when. Book extra staff ahead of time if you need them. There is no point in hiring someone who won't turn up because you didn't let him know.
Also, consider how many days you will be filming your schedule. Some projects can be completed in a matter of days or weeks. Others may take several days. While creating your schedule, it is important to remember whether you will require more than one shot per day. Multiplying takes in the same area will result both in increased costs and a longer time. It is better to be cautious and take fewer shots than you risk losing money if you are not sure if multiple takes are necessary.
Budgeting is another crucial aspect of production plan. A realistic budget will help you work within your means. If you have to reduce your budget due to unexpected circumstances, you can always lower it later. You shouldn't underestimate the amount you'll spend. You'll end up with less money after paying for other things if the cost is underestimated.
Planning production is a tedious process. Once you have a good understanding of how everything works together, planning future projects becomes easy.
What are the 7 R's of logistics?
The acronym "7R's" of Logistics stands for seven principles that underpin logistics management. It was developed by International Association of Business Logisticians (IABL), and published as part of their "Seven Principles of Logistics Management Series" in 2004.
The acronym is made up of the following letters:
-
Responsive - ensure all actions are legal and not harmful to others.
-
Reliable - You can have confidence that you will fulfill your promises.
-
Reasonable - use resources efficiently and don't waste them.
-
Realistic – consider all aspects of operations, from cost-effectiveness to environmental impact.
-
Respectful - treat people fairly and equitably.
-
Responsive - Look for ways to save time and increase productivity.
-
Recognizable - provide customers with value-added services.
Statistics
- Many factories witnessed a 30% increase in output due to the shift to electric motors. (en.wikipedia.org)
- According to the United Nations Industrial Development Organization (UNIDO), China is the top manufacturer worldwide by 2019 output, producing 28.7% of the total global manufacturing output, followed by the United States, Japan, Germany, and India.[52][53] (en.wikipedia.org)
- In 2021, an estimated 12.1 million Americans work in the manufacturing sector.6 (investopedia.com)
- Job #1 is delivering the ordered product according to specifications: color, size, brand, and quantity. (netsuite.com)
- According to a Statista study, U.S. businesses spent $1.63 trillion on logistics in 2019, moving goods from origin to end user through various supply chain network segments. (netsuite.com)
External Links
How To
Six Sigma: How to Use it in Manufacturing
Six Sigma is "the application statistical process control (SPC), techniques for continuous improvement." Motorola's Quality Improvement Department developed it at their Tokyo plant in Japan in 1986. The basic idea behind Six Sigma is to improve quality by improving processes through standardization and eliminating defects. Many companies have adopted Six Sigma in recent years because they believe that there are no perfect products and services. Six Sigma seeks to reduce variation between the mean production value. This means that if you take a sample of your product, then measure its performance against the average, you can find out what percentage of the time the process deviates from the norm. If this deviation is too big, you know something needs fixing.
Understanding the dynamics of variability within your business is the first step in Six Sigma. Once you understand this, you can then identify the causes of variation. These variations can also be classified as random or systematic. Random variations occur when people do mistakes. Symmetrical variations are caused due to factors beyond the process. These are, for instance, random variations that occur when widgets are made and some fall off the production line. If however, you notice that each time you assemble a widget it falls apart in exactly the same spot, that is a problem.
Once you have identified the problem, you can design solutions. That solution might involve changing the way you do things or redesigning the process altogether. After implementing the new changes, you should test them again to see if they worked. If they don’t work, you’ll need to go back and rework the plan.