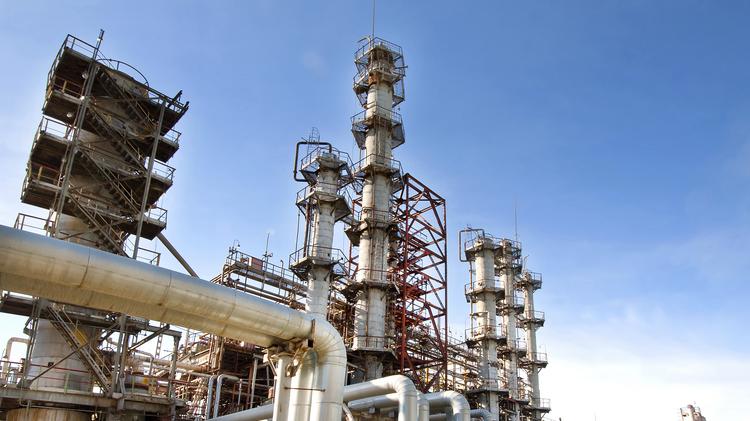
Cellular manufacturing involves dividing a production plant into segments that produce a different component of the finished product. This allows for a reduction in waste and a decrease in lead time. You can implement a cell manufacturing system in many different ways. Some methods are more straightforward, while others require complex computer models. Cellular manufacturing is one subsection of lean manufacturing.
Cellular manufacturing, an innovative and highly efficient process, can help lower the cost and time it takes to produce parts. The goal is to minimize waste while moving products along the production line as quickly possible. Cellular manufacturing can also address issues like group cohesiveness and individual management as well as employee inputs, supervision, and other issues. Cellular manufacturing can allow for greater flexibility, which can help organizations meet customer demand. Also, cellular manufacturing has been shown to increase productivity.
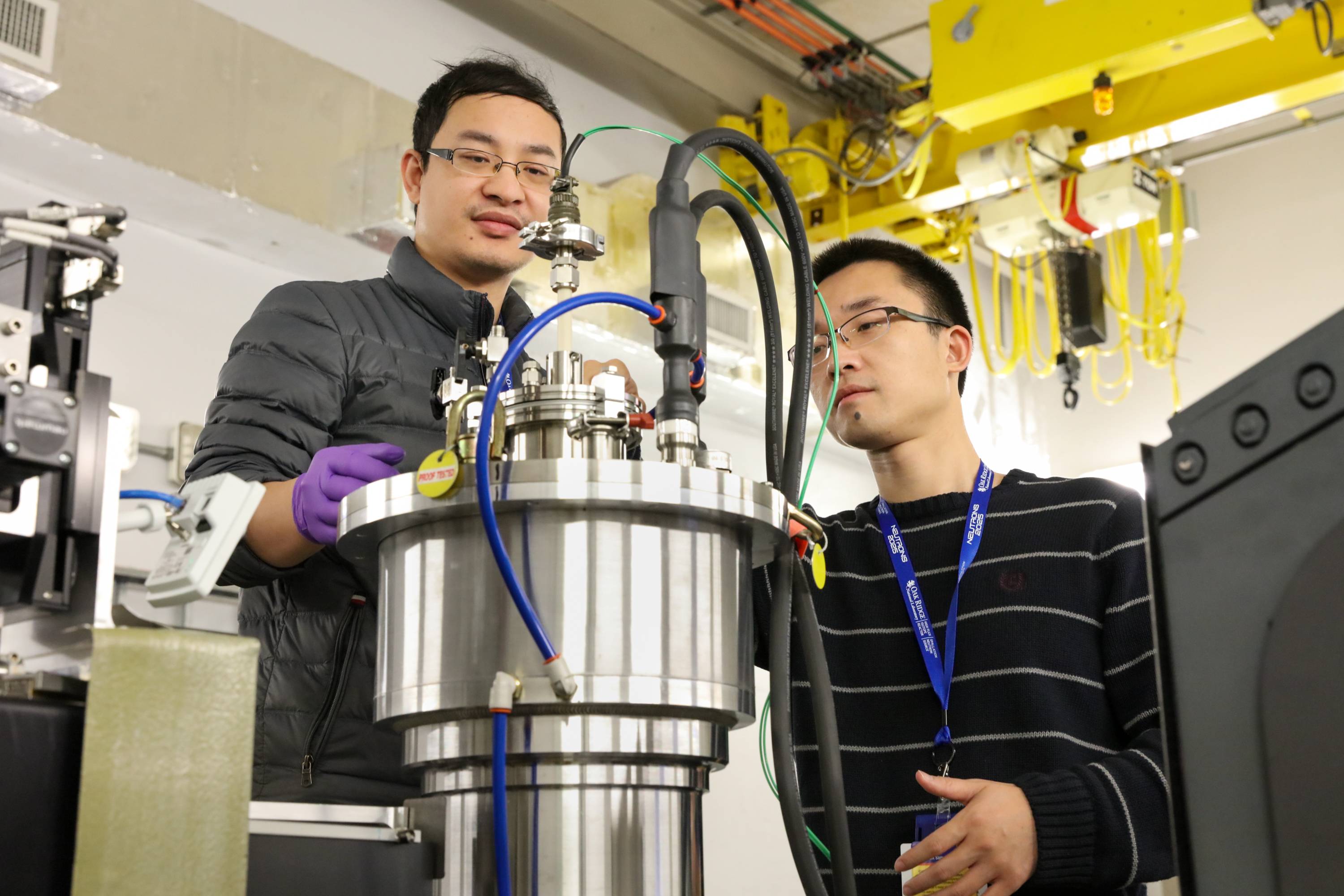
Cellular manufacturing is possible in many ways. It can be applied in a simple way like production flow analysis and more complex computer models. The goal is to produce similar products at the same time, which minimizes wasteful motion and takt time.
The overall takt time can be affected by the layout of the cell. The cells' design can impact the speed of motion. It can also affect how value is added or non-value. This reduces cycle times. Some cells are configured in a U-shape, allowing operators to move from machine to machine more quickly. Some cells can also be configured in a U-shape that allows operators to move faster between machines. This design is especially useful for companies that produce a variety products.
The first step in creating a cell is identifying the products to be made in the cell. A process map can help you determine the production rate. Engineers need to determine the number and process steps of the workcell in order to create it. Next, determine what tools and equipment are needed in the cell. Modern work cells include consideration of the number of steps and the type of holding bins. They also take into consideration how many steps each machine will require. The physical structure of the cell will determine which layout is most effective.
The cell's layout is key to the success and efficiency of cell manufacturing. Cell design can affect how much motion is lost and how many waste products are created. It can also impact fatigue. In addition to reducing motion, cellular manufacturing can also improve process efficiency and quality. Layout of cells can be used to reduce waste and ensure that defects are caught quickly.
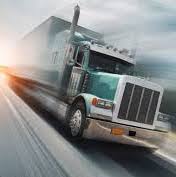
There are three most common layouts. S-shaped cell can also be used for working around obstructions. You can customize the layout of cells and reconfigure cells to suit the needs of different areas of the factory.
FAQ
What are the 7 R's of logistics?
The acronym 7R's of Logistic is an acronym that stands for seven fundamental principles of logistics management. It was created by the International Association of Business Logisticians and published in 2004 under its "Seven Principles of Logistics Management".
The following letters make up the acronym:
-
Responsible – ensure that all actions are legal and don't cause harm to anyone else.
-
Reliable - have confidence in the ability to deliver on commitments made.
-
It is reasonable to use resources efficiently and not waste them.
-
Realistic – Consider all aspects, including cost-effectiveness as well as environmental impact.
-
Respectful - show respect and treat others fairly and fairly
-
You are resourceful and look for ways to save money while increasing productivity.
-
Recognizable: Provide customers with value-added service
What are manufacturing & logistics?
Manufacturing is the production of goods using raw materials. Logistics includes all aspects related to supply chain management, such as procurement, distribution planning, inventory control and transportation. Manufacturing and logistics can often be grouped together to describe a larger term that covers both the creation of products, and the delivery of them to customers.
What can I do to learn more about manufacturing?
The best way to learn about manufacturing is through hands-on experience. If that is not possible, you could always read books or view educational videos.
How does a Production Planner differ from a Project Manager?
The main difference between a production planner and a project manager is that a project manager is usually the person who plans and organizes the entire project, whereas a production planner is mainly involved in the planning stage of the project.
Statistics
- In the United States, for example, manufacturing makes up 15% of the economic output. (twi-global.com)
- It's estimated that 10.8% of the U.S. GDP in 2020 was contributed to manufacturing. (investopedia.com)
- (2:04) MTO is a production technique wherein products are customized according to customer specifications, and production only starts after an order is received. (oracle.com)
- Many factories witnessed a 30% increase in output due to the shift to electric motors. (en.wikipedia.org)
- [54][55] These are the top 50 countries by the total value of manufacturing output in US dollars for its noted year according to World Bank.[56] (en.wikipedia.org)
External Links
How To
How to use the Just In-Time Production Method
Just-intime (JIT), a method used to lower costs and improve efficiency in business processes, is called just-in-time. It's a way to ensure that you get the right resources at just the right time. This means that you only pay for what you actually use. The term was first coined by Frederick Taylor, who developed his theory while working as a foreman in the early 1900s. He observed how workers were paid overtime if there were delays in their work. He decided to ensure workers have enough time to do their jobs before starting work to improve productivity.
The idea behind JIT is that you should plan ahead and have everything ready so you don't waste money. It is important to look at your entire project from beginning to end and ensure that you have enough resources to handle any issues that may arise. If you expect problems to arise, you will be able to provide the necessary equipment and personnel to address them. You won't have to pay more for unnecessary items.
There are several types of JIT techniques:
-
Demand-driven JIT: This is a JIT that allows you to regularly order the parts/materials necessary for your project. This will enable you to keep track of how much material is left after you use it. This will allow you to calculate how long it will take to make more.
-
Inventory-based: This allows you to store the materials necessary for your projects in advance. This allows one to predict how much they will sell.
-
Project-driven: This means that you have enough money to pay for your project. If you know the amount you require, you can buy the materials you need.
-
Resource-based JIT: This is the most popular form of JIT. Here, you allocate certain resources based on demand. You might assign more people to help with orders if there are many. You'll have fewer orders if you have fewer.
-
Cost-based: This is similar to resource-based, except that here you're not just concerned about how many people you have but how much each person costs.
-
Price-based: This approach is very similar to the cost-based method except that you don't look at individual workers costs but the total cost of the company.
-
Material-based - This is a variant of cost-based. But instead of looking at the total company cost, you focus on how much raw material you spend per year.
-
Time-based JIT: A variation on resource-based JIT. Instead of focusing on how much each employee costs, you focus on how long it takes to complete the project.
-
Quality-based JIT: This is another variation of resource based JIT. Instead of thinking about the cost of each employee or the time it takes to produce something, you focus on how good your product quality.
-
Value-based JIT : This is the newest type of JIT. In this scenario, you're not concerned about how products perform or whether customers expect them to meet their expectations. Instead, you focus on the added value that you provide to your market.
-
Stock-based. This method is inventory-based and focuses only on the actual production at any given point. It is used when production goals are met while inventory is kept to a minimum.
-
Just-in-time planning (JIT): This is a combination JIT and supply-chain management. It is the process that schedules the delivery of components within a short time of their order. It is essential because it reduces lead-times and increases throughput.