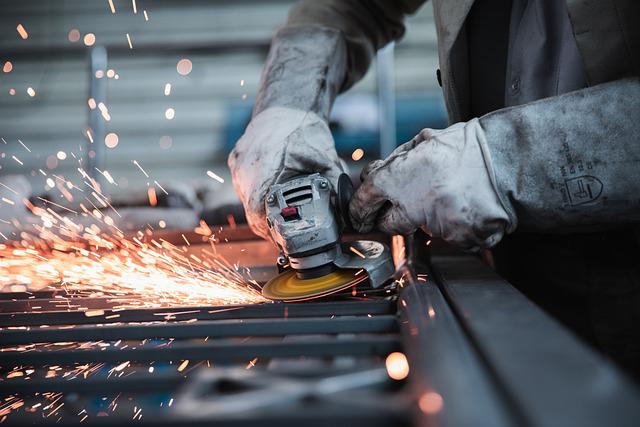
The biggest steel companies have played an important role in the development of the US economy. These companies produce metals that are essential for industrial and construction projects. These companies produce a variety metal fabrication services like cutting, bending, stamping, welding, and gallvanizing.
The Biggest Steel Companies in Usa
A number of factors contribute to the size of the steel industry, from raw materials availability and prices to the amount of smelting and casting facilities. The top five US steel companies produce over 87 millions tons of steel each year.
Nucor (X) is the largest US-based steelmaker based on the number of shipments to outside customers. It shipped 3.6M tons of steel during Q3 2019. This is down from the 3.9M tons it shipped in the same quarter in 2018.
It is a large and highly integrated company, with operations in multiple industries including smelting, manufacturing, steel, mining, and petroleum. The company owns a large majority stake in an coal-fired energy plant.
Commercial Metals Corporation (CMC) was the third-largest manufacturer of steel, based on shipments. The company shipped 2.1million tons of steel during Q4-2018. This vertically integrated firm also produces and sells aluminum, stainless steel and expanded metals in different sizes, thicknesses and alloys.
The company is making large investments in its mines of iron ore in the Great Lakes Region. It also invests in EAFs for existing mills and expands capacity in flat-rolls. It is also planning a phase-two expansion at its Ohio flat-roll mill.
It is one of the few diversified steelmakers, and its main operations are in the United States and Europe. It is also the world's largest producer of high performance and specialty steels.
Another significant player in the steel industry is ArcelorMittal, which produces more than half of the world's steel. It has operations in the United States of America, Canada, Brazil, Europe, and other markets. Its global presence gives it an advantage in a highly competitive market.
China is the world's biggest steel producer and produces more than two-thirds the global supply. The country has also a long tradition of innovation in the steel industry.
Even though the industry is cyclical in nature, it remains vital to the US economic development. It is necessary to undertake massive construction projects in order to replace outdated infrastructure. Also, there are many demands for new structures, including roads, bridges, buildings and other structures.
The US government's $1.2 Trillion infrastructure spending bill approved in 2021 is expected to be a key factor in driving the US steel market. This will be the largest construction in US history, and it will help to boost the economy at home and create jobs. The project is expected to increase the country's GDP in 2021 by $1.3 trillion, and also boost demand for steel.
FAQ
What does it mean to warehouse?
A warehouse or storage facility is where goods are stored before they are sold. You can have it indoors or outdoors. It may also be an indoor space or an outdoor area.
How can manufacturing overproduction be reduced?
Improved inventory management is the key to reducing overproduction. This would reduce the time spent on unproductive activities like purchasing, storing and maintaining excess stock. This could help us free up our time for other productive tasks.
One way to do this is to adopt a Kanban system. A Kanban board is a visual display used to track work in progress. In a Kanban system, work items move through a sequence of states until they reach their final destination. Each state represents a different priority.
To illustrate, work can move from one stage or another when it is complete enough for it to be moved to a new stage. However, if a task is still at the beginning stages, it will remain so until it reaches the end of the process.
This keeps work moving and ensures no work is lost. Managers can monitor the work being done by Kanban boards to see what is happening at any given time. This information allows them to adjust their workflow based on real-time data.
Lean manufacturing is another way to manage inventory levels. Lean manufacturing works to eliminate waste throughout every stage of the production chain. Anything that does nothing to add value to a product is waste. There are several types of waste that you might encounter:
-
Overproduction
-
Inventory
-
Unnecessary packaging
-
Excess materials
By implementing these ideas, manufacturers can improve efficiency and cut costs.
What are manufacturing and logistic?
Manufacturing refers to the process of making goods using raw materials and machines. Logistics includes all aspects related to supply chain management, such as procurement, distribution planning, inventory control and transportation. As a broad term, manufacturing and logistics often refer to both the creation and delivery of products.
What is the responsibility for a logistics manager
Logistics managers are responsible for ensuring that all goods arrive in perfect condition and on time. This is done using his/her knowledge of the company's products. He/she should make sure that enough stock is on hand to meet the demands.
Statistics
- According to the United Nations Industrial Development Organization (UNIDO), China is the top manufacturer worldwide by 2019 output, producing 28.7% of the total global manufacturing output, followed by the United States, Japan, Germany, and India.[52][53] (en.wikipedia.org)
- (2:04) MTO is a production technique wherein products are customized according to customer specifications, and production only starts after an order is received. (oracle.com)
- Job #1 is delivering the ordered product according to specifications: color, size, brand, and quantity. (netsuite.com)
- In the United States, for example, manufacturing makes up 15% of the economic output. (twi-global.com)
- [54][55] These are the top 50 countries by the total value of manufacturing output in US dollars for its noted year according to World Bank.[56] (en.wikipedia.org)
External Links
How To
Six Sigma and Manufacturing
Six Sigma is defined as "the application of statistical process control (SPC) techniques to achieve continuous improvement." It was developed by Motorola's Quality Improvement Department at their plant in Tokyo, Japan, in 1986. Six Sigma's basic concept is to improve quality and eliminate defects through standardization. Many companies have adopted Six Sigma in recent years because they believe that there are no perfect products and services. Six Sigma's primary goal is to reduce variation from the average value of production. You can calculate the percentage of deviation from the norm by taking a sample of your product and comparing it to the average. If the deviation is excessive, it's likely that something needs to be fixed.
Understanding the nature of variability in your business is the first step to Six Sigma. Once you have this understanding, you will need to identify sources and causes of variation. It is important to identify whether the variations are random or systemic. Random variations are caused when people make mistakes. While systematic variations are caused outside of the process, they can occur. Random variations would include, for example, the failure of some widgets to fall from the assembly line. It would be considered a systematic problem if every widget that you build falls apart at the same location each time.
Once you've identified where the problems lie, you'll want to design solutions to eliminate those problems. You might need to change the way you work or completely redesign the process. You should then test the changes again after they have been implemented. If they fail, you can go back to the drawing board to come up with a different plan.