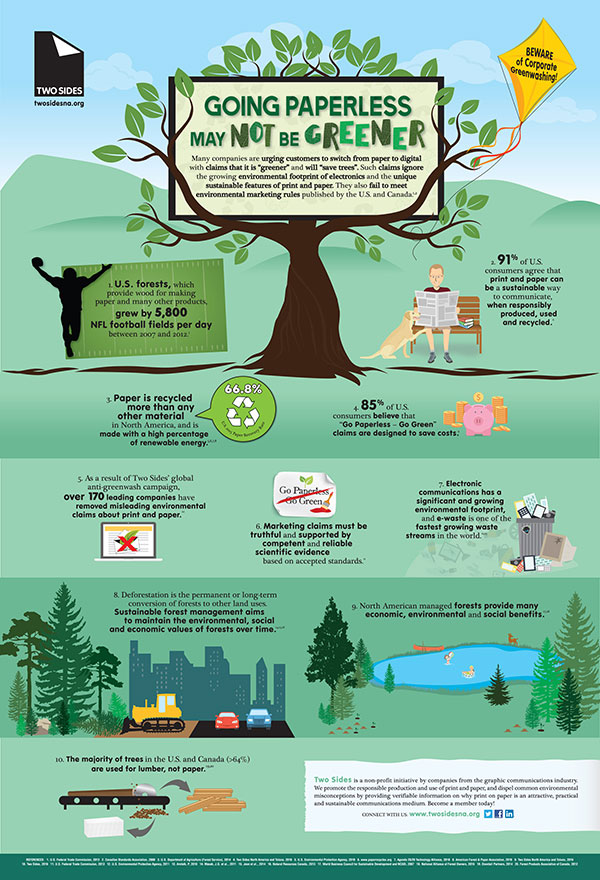
A degree in either architecture or engineering is required to be an engineer or architect manager. Although many of these professionals work in an office, others work on construction sites. Many of these professionals have a bachelor's degree or more in engineering or architecture, and extensive experience in this field. A few choose to obtain a master's degree in business administration as an addition to their education. You can also advance in this field by pursuing many different degrees. If you're interested in a career as an architectural and engineering manager, consider pursuing an MBA.
Perspective for engineers and architects
It is a good time to be an engineer or architect manager. Over the next decade, the number of job openings is expected to grow by about two percent. This is due to the rise of many industries. However, the competition for available jobs is fierce. See the O*NET website for more information on the job outlook.
Engineering and architectural managers are responsible for planning and directing activities in engineering and architectural companies. They use their architectural knowledge to plan, design the construction and manage many activities. These activities can include the design and construction of large buildings, engineering research facilities, or manufacturing sites. They also design new products. They must identify the company's technical goals, and then create detailed plans that will assist in achieving them.
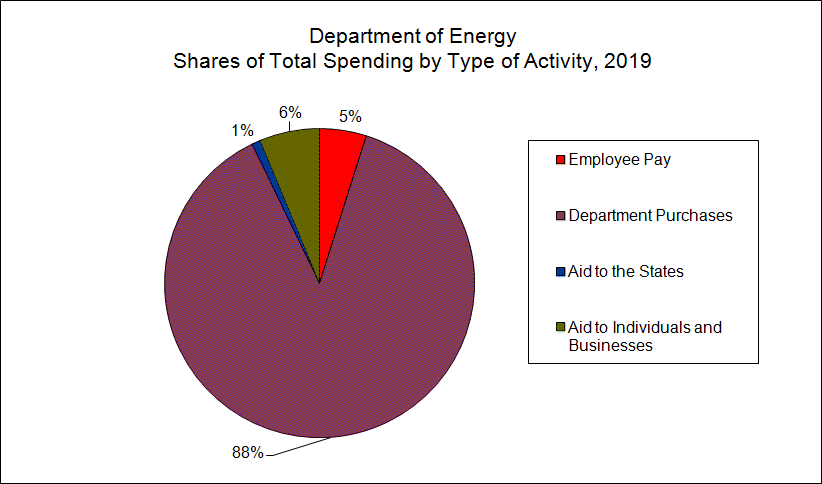
Applicants for this field usually have at least a master's degree in management. The type and level of the management job you are interested in will determine which program is the best. A master's in engineering can prepare you to work as a manager, while a masters in business administration will help you develop more managerial skills. Both types are required to be completed within a minimum of one year.
Education Required
Management in engineering and architecture requires a high level of education. These managers are responsible for overseeing the day-to-day operations of engineering teams. They are responsible for providing oversight and training to employees. They also propose budgets for specific tasks and act as mentors for other employees. However, if you're considering a career in this field, consider getting a bachelor's degree in this field.
Most of these managers have a bachelor’s degree either in architecture or engineering. However, many have advanced degrees or certificates in technology or business administration. An MsEM or engineering management graduate degree will give you the managerial skills required for the job. In addition to technical knowledge, you'll also need strong communication and analytical skills.
Engineer managers and architects have the responsibility for creating new projects and ensuring the highest quality product. They consider the impact on the environment, as well the needs and wants of users. They prepare budgets and plans based on technical specifications. They supervise teams to help them execute their projects.
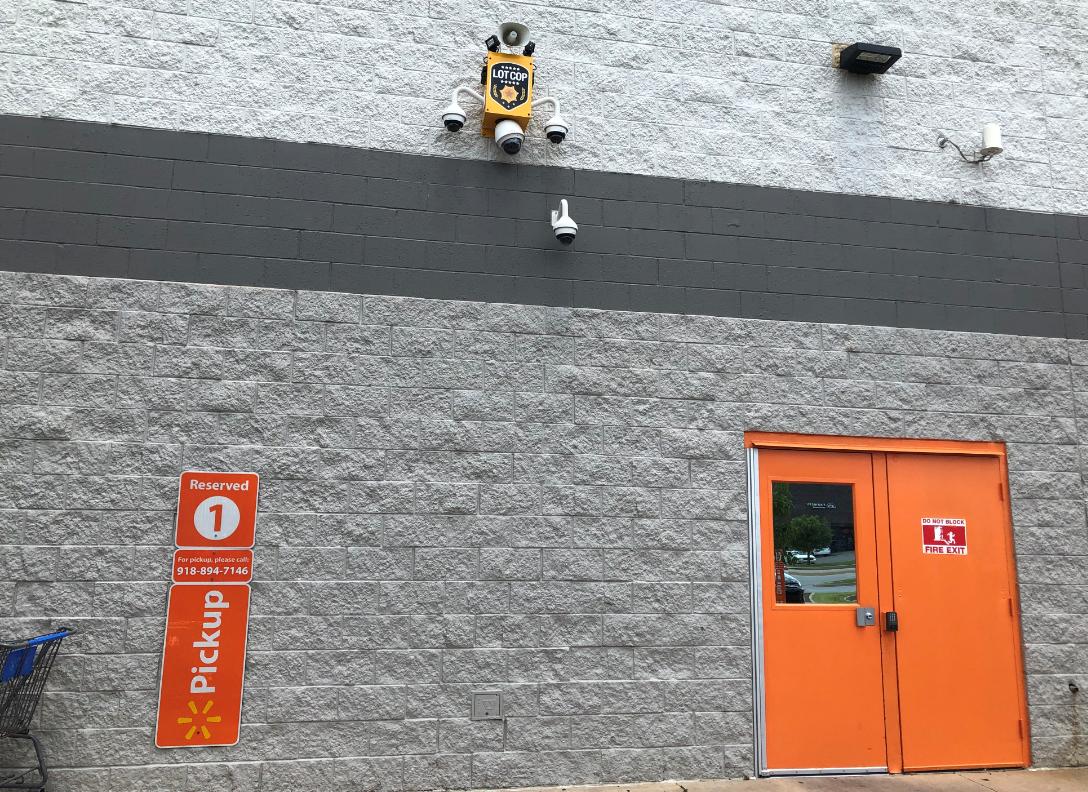
Your potential to earn
Over the next ten years, the earning potential to be an architect or engineer manager is expected increase by 13%. This field will see an increase in jobs as a result of the growing engineering industry. The industry is expected to have more jobs. However, there will be fierce competition. However, the industry's growth rate won't be as fast as that of all other occupations.
The range in salary for this job depends on education and experience. The starting salary for this job is $75,190. Those with four to five years of experience can expect to make at least $104,800. In contrast, someone with at most ten years' experience can make about $156,620 a year.
FAQ
What is the responsibility of a logistics manager?
A logistics manager ensures that all goods are delivered on time and without damage. This is done through his/her expertise and knowledge about the company's product range. He/she should ensure that sufficient stock is available in order to meet customer demand.
What are the responsibilities of a production planner
A production planner ensures all aspects of the project are delivered on time, within budget, and within scope. They also ensure that the product/service meets the client’s needs.
What are manufacturing and logistic?
Manufacturing is the act of producing goods from raw materials using machines and processes. Logistics is the management of all aspects of supply chain activities, including procurement, production planning, distribution, warehousing, inventory control, transportation, and customer service. As a broad term, manufacturing and logistics often refer to both the creation and delivery of products.
What type of jobs is there in logistics
There are different kinds of jobs available in logistics. Here are some:
-
Warehouse workers - They load and unload trucks and pallets.
-
Transportation drivers – These drivers drive trucks and wagons to transport goods and pick up the goods.
-
Freight handlers – They sort and package freight at warehouses.
-
Inventory managers - They oversee the inventory of goods in warehouses.
-
Sales representatives - They sell products to customers.
-
Logistics coordinators are responsible for organizing and planning logistics operations.
-
Purchasing agents – They buy goods or services necessary to run a company.
-
Customer service representatives are available to answer customer calls and emails.
-
Shippers clerks - They process shipping order and issue bills.
-
Order fillers: They fill orders based off what has been ordered and shipped.
-
Quality control inspectors are responsible for inspecting incoming and outgoing products looking for defects.
-
Others - There are many types of jobs in logistics such as transport supervisors and cargo specialists.
Statistics
- (2:04) MTO is a production technique wherein products are customized according to customer specifications, and production only starts after an order is received. (oracle.com)
- According to the United Nations Industrial Development Organization (UNIDO), China is the top manufacturer worldwide by 2019 output, producing 28.7% of the total global manufacturing output, followed by the United States, Japan, Germany, and India.[52][53] (en.wikipedia.org)
- Job #1 is delivering the ordered product according to specifications: color, size, brand, and quantity. (netsuite.com)
- In the United States, for example, manufacturing makes up 15% of the economic output. (twi-global.com)
- [54][55] These are the top 50 countries by the total value of manufacturing output in US dollars for its noted year according to World Bank.[56] (en.wikipedia.org)
External Links
How To
Six Sigma: How to Use it in Manufacturing
Six Sigma is "the application statistical process control (SPC), techniques for continuous improvement." It was developed by Motorola's Quality Improvement Department at their plant in Tokyo, Japan, in 1986. The basic idea behind Six Sigma is to improve quality by improving processes through standardization and eliminating defects. Many companies have adopted Six Sigma in recent years because they believe that there are no perfect products and services. Six Sigma's primary goal is to reduce variation from the average value of production. This means that if you take a sample of your product, then measure its performance against the average, you can find out what percentage of the time the process deviates from the norm. If the deviation is excessive, it's likely that something needs to be fixed.
Understanding the dynamics of variability within your business is the first step in Six Sigma. Once you have a good understanding of the basics, you can identify potential sources of variation. It is important to identify whether the variations are random or systemic. Random variations occur when people do mistakes. Symmetrical variations are caused due to factors beyond the process. These are, for instance, random variations that occur when widgets are made and some fall off the production line. It would be considered a systematic problem if every widget that you build falls apart at the same location each time.
Once you have identified the problem, you can design solutions. The solution could involve changing how you do things, or redesigning your entire process. After implementing the new changes, you should test them again to see if they worked. If they don't work, you will need to go back to the drawing boards and create a new plan.