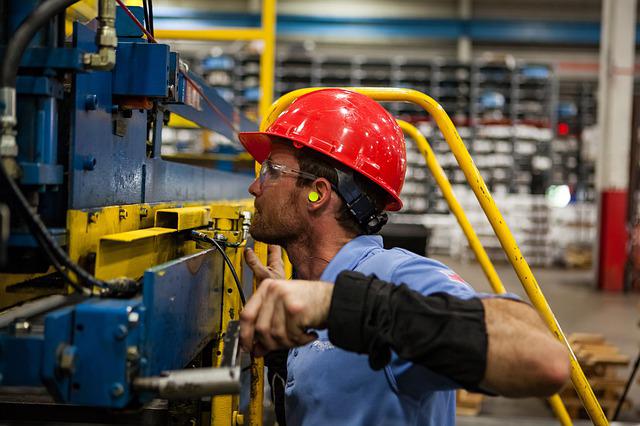
Six-Sigma (and lean) are complementary approaches to improving processes. Although they both have the same tools for problem solving, each has its strengths and weaknesses. Six-Sigma refers to a statistical control technique. Lean, on the other hand, starts with the assumption that a product should add value to its customers, not just make it. Lean's key principle is to eliminate waste while improving the product's quality.
Problem solving with PDCA
While there are differences between DMAIC and PDCA, both approaches are based on DMAIC. The PDCA cycle is more complex and requires more analysis. PDCA cannot be used to solve urgent problems, as DMAIC can. This approach requires a problem solver with technical skills. Six Sigma will require a problem-solving team lead who is a Six Sigma "green belt" certified practitioner.
Six Sigma's problem-solving cycle was introduced in the 1950s by W. Edwards Deming. It was developed to be used alongside continuous improvement methods to aid in rebuilding Japan's economy. At the P (Plan), real data must first be gathered. A clear mission statement must then be developed. After the PDCA stage, the team must decide on a recommended solution.
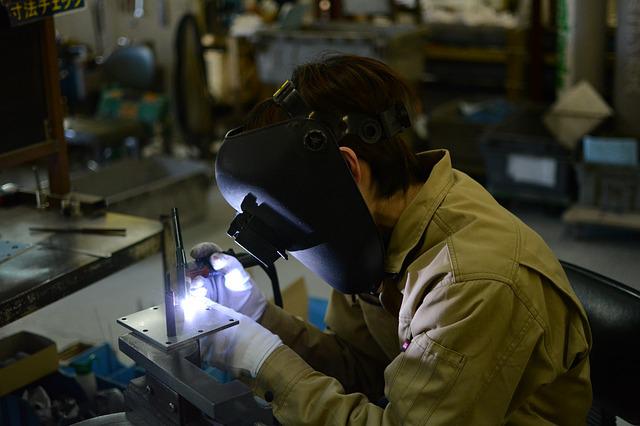
Process maps
The way that each approach describes the process is a key difference between Six Sigma and Lean processes maps. Both emphasize defining a process in detail, but each methodology focuses on different aspects of the process. Lean, on the other hand, is about mapping actual processes rather than standard operating procedures. Consider the main activities, decisions, as well as sources of approval, when creating process mappings. Include areas that require multiple methods and factors. Check the process flow and match roles.
A process map should have steps, symbols and arrows that show the flow of a particular process. Each process should be reviewed by several people to ensure that it accurately reflects the actual process. A process map should also include the date of its creation and contact information for any questions. Process maps are an excellent way to improve processes. They can be too complex.
Analyse Cause and Effect
Six Sigma and lean project managing techniques use statistical analysis and stochastic optimising. The Cause and Effect Matrix (CAE) relates the steps of a process to their inputs and outputs. Customers' requirements are listed in order they are most important to them. Inputs and outputs are then ranked according to their impact on the outcome. It is necessary to identify key process input variables and rank them.
Although each technique may have its own set of benefits they are not all the same. Lean Six Sigma is based on Frederick Winslow Taylor’s Principles of Scientific Management. Taylor saw business processes as interconnected processes and workflows. Taylor advocated reducing variation and also minimizing waste. Six-Sigma (and lean) are complementary in the effort to reduce waste.
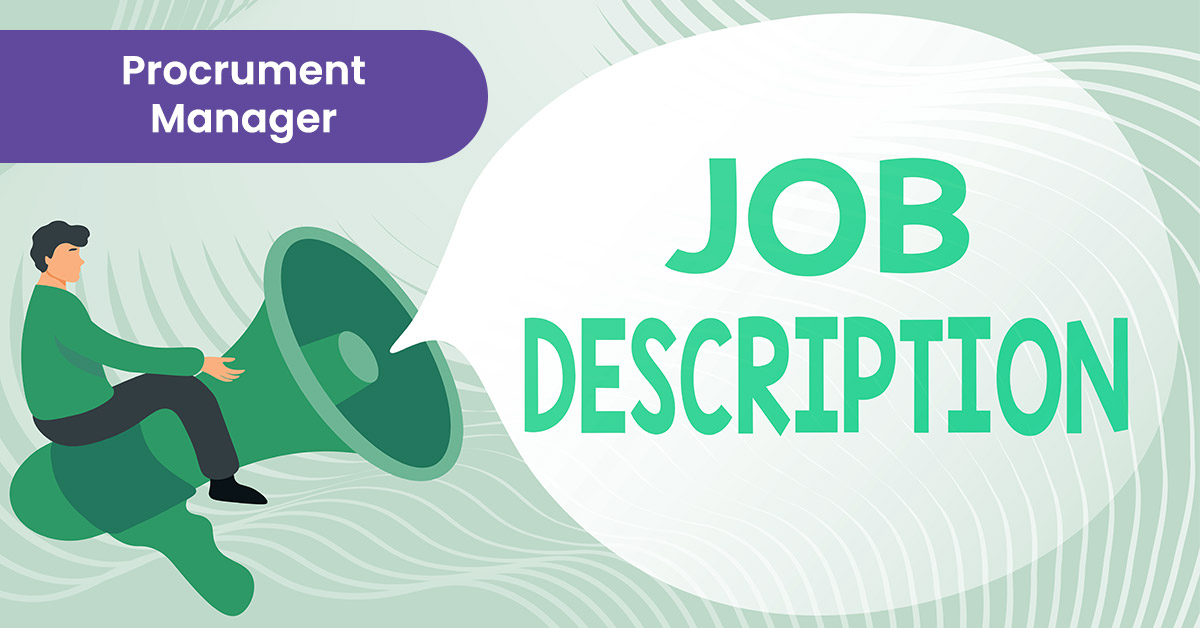
Elimination of variation
Variation is a natural part of any manufacturing process. This variability causes uncertainty in the outcome. It is important to maintain consistency in order to deliver professional results. Six Sigma and Lean manufacturing methods are designed to reduce variation. A certain amount of variation is okay, but excessive variation can cause costly repairs, rework and even business consequences. The best way to deal with variation is to identify its underlying causes.
The decision points are the best place to search for variations. Process maps use diamonds to represent decision points. Six Sigma teams have the ability to identify decision points and start eliminating variation. This information can be obtained from the Six Sigma team or the process owner. The Six Sigma group cannot focus on a process that is not governed by a standard process if it's owner. If the Six Sigma team does not have sufficient technical ability to make adjustments, a process diagram may not be useful.
FAQ
How can we reduce manufacturing overproduction?
It is essential to find better ways to manage inventory to reduce overproduction. This would reduce the time spent on unproductive activities like purchasing, storing and maintaining excess stock. This would allow us to use our resources for more productive tasks.
One way to do this is to adopt a Kanban system. A Kanban board can be used to monitor work progress. In a Kanban system, work items move through a sequence of states until they reach their final destination. Each state represents a different priority.
When work is completed, it can be transferred to the next stage. If a task is still in its beginning stages, it will continue to be so until it reaches the end.
This allows work to move forward and ensures that no work is missed. A Kanban board allows managers to monitor how much work is being completed at any given moment. This allows them the ability to adjust their workflow using real-time data.
Lean manufacturing is another way to manage inventory levels. Lean manufacturing seeks to eliminate waste from every step of the production cycle. Waste includes anything that does not add value to the product. The following are examples of common waste types:
-
Overproduction
-
Inventory
-
Packaging that is not necessary
-
Excess materials
Manufacturers can reduce their costs and improve their efficiency by using these ideas.
What do you mean by warehouse?
A warehouse is an area where goods are stored before being sold. It can be indoors or out. Sometimes, it can be both an indoor and outdoor space.
What are the main products of logistics?
Logistics is the process of moving goods from one point to another.
They cover all aspects of transportation, such as packing, loading, transporting and unloading.
Logisticians ensure the product reaches its destination in the most efficient manner. Logisticians help companies improve their supply chain efficiency by providing information about demand forecasts and stock levels, production schedules, as well as availability of raw materials.
They can also track shipments in transit and monitor quality standards.
What skills do production planners need?
To become a successful production planner, you need to be organized, flexible, and able to multitask. Communication skills are essential to ensure that you can communicate effectively with clients, colleagues, and customers.
What are the 7 Rs of logistics?
The acronym 7R's for Logistics stands to represent the seven basic principles in logistics management. It was created by the International Association of Business Logisticians and published in 2004 under its "Seven Principles of Logistics Management".
The acronym is composed of the following letters.
-
Responsive - ensure all actions are legal and not harmful to others.
-
Reliable - Have confidence in your ability to fulfill all of your commitments.
-
Use resources effectively and sparingly.
-
Realistic - consider all aspects of operations, including cost-effectiveness and environmental impact.
-
Respectful: Treat others with fairness and equity
-
Responsive - Look for ways to save time and increase productivity.
-
Recognizable - Provide value-added services to customers
Is automation important in manufacturing?
Not only is automation important for manufacturers, but it's also vital for service providers. It allows them to offer services faster and more efficiently. It reduces human errors and improves productivity, which in turn helps them lower their costs.
What does it mean to be a manufacturer?
Manufacturing Industries are those businesses that make products for sale. Consumers are the people who purchase these products. These companies use various processes such as production, distribution, retailing, management, etc., to fulfill this purpose. They make goods from raw materials with machines and other equipment. This includes all types if manufactured goods.
Statistics
- Many factories witnessed a 30% increase in output due to the shift to electric motors. (en.wikipedia.org)
- According to the United Nations Industrial Development Organization (UNIDO), China is the top manufacturer worldwide by 2019 output, producing 28.7% of the total global manufacturing output, followed by the United States, Japan, Germany, and India.[52][53] (en.wikipedia.org)
- (2:04) MTO is a production technique wherein products are customized according to customer specifications, and production only starts after an order is received. (oracle.com)
- It's estimated that 10.8% of the U.S. GDP in 2020 was contributed to manufacturing. (investopedia.com)
- [54][55] These are the top 50 countries by the total value of manufacturing output in US dollars for its noted year according to World Bank.[56] (en.wikipedia.org)
External Links
How To
How to Use 5S for Increasing Productivity in Manufacturing
5S stands for "Sort", "Set In Order", "Standardize", "Separate" and "Store". Toyota Motor Corporation developed the 5S method in 1954. It assists companies in improving their work environments and achieving higher efficiency.
This method has the basic goal of standardizing production processes to make them repeatable. It means tasks like cleaning, sorting or packing, labeling, and storing are done every day. Through these actions, workers can perform their jobs more efficiently because they know what to expect from them.
There are five steps that you need to follow in order to implement 5S. Each step has a different action and leads to higher efficiency. By sorting, for example, you make it easy to find the items later. Once you have placed items in an ordered fashion, you will put them together. Then, after you separate your inventory into groups, you store those groups in containers that are easy to access. Finally, label all containers correctly.
Employees need to reflect on how they do their jobs. Employees need to be able understand their motivations and discover alternative ways to do them. They will need to develop new skills and techniques in order for the 5S system to be implemented.
In addition to increasing efficiency, the 5S method also improves morale and teamwork among employees. They will feel motivated to strive for higher levels of efficiency once they start to see results.