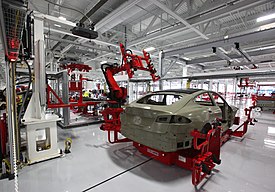
A validation engineer salary is the amount an individual receives for their work as a validator. This amount will be based on the individual's experience, their education and their skills. However, it can also be influenced by the type of job they hold and the company they work for.
What is a Validation engineer?
A validation engineer is an engineer who monitors the quality of a product using equipment, processes, and procedures. They work in manufacturing and testing environments, as well as research and development.
What does a Validation Engineer do?
A validation engineer monitors equipment and system performance used in manufacturing pharmaceutical products. To do so, they analyze, inspect, test and calibrate equipment and machinery. They also investigate equipment malfunctions and anomalies which may lead to failure of the product.
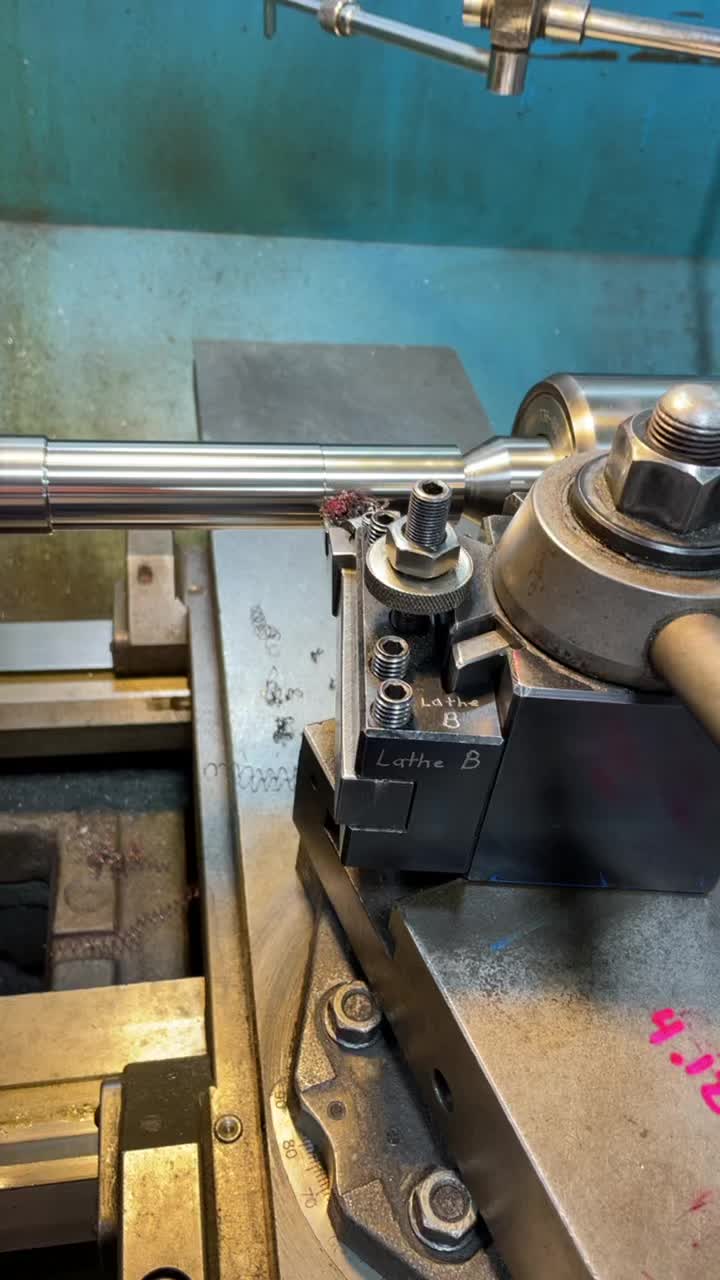
What is the Salary of a Validation Engineer?
The salary of a Validation engineer is high in general, but depends on what type of company you are employed by. The highest salaries are often found in the technology industry, such as Apple and Google. Engineers in the pharmaceutical industry can expect to earn an average salary of $89 130 per year.
What are the most common skills required for this career?
Qualifications for validation engineers include writing, executing and coordinating commissioning/qualification protocols. The validation engineer must have a strong technical background in manufacturing, software and process engineering. They should also be able to demonstrate a track record for developing and delivering high-quality processes.
How to become a Validation Engineer
There are a few different routes into a validation engineer role, either by gaining a degree or through an apprenticeship scheme. Employers require that candidates hold a bachelor's in a relevant discipline of engineering, such electrical, mechanical or computer software.
You can then gain experience by working in a graduate engineering program, or on an internship or a placement. You can find work through recruitment agencies and careers services, newspapers, or online.
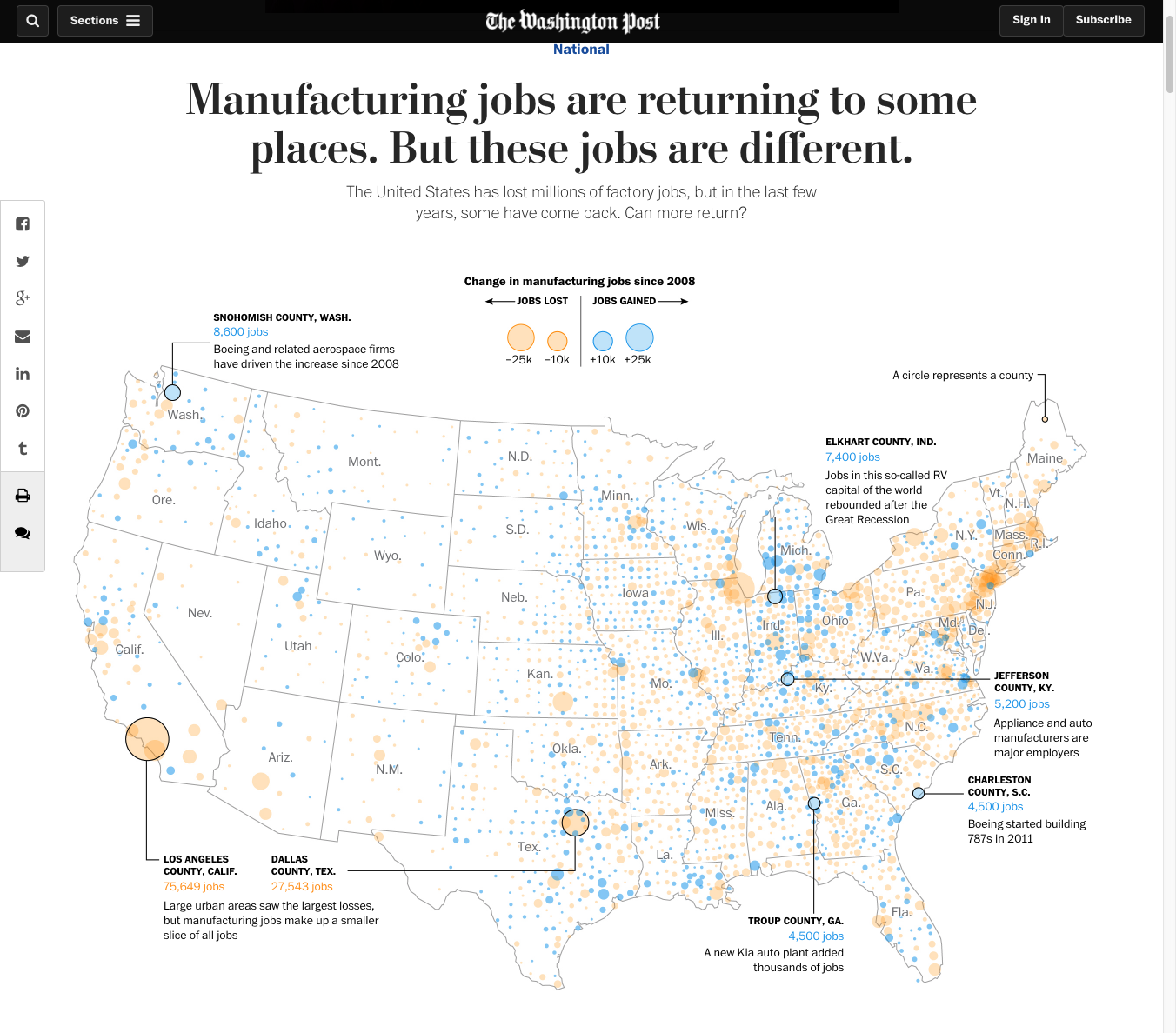
How to become a Pharmaceutical Validation Engineer
To be a validator engineer, you need to have the right combination between academic credentials and practical experience. You must have a relevant engineering or science degree, and you should also be familiar with the pharmaceutical industry. This is a challenging career path but it's well worth the effort to learn new skills and land a position that suits you.
How to Become A Pharma Validation Engineer
For validation engineers, there is a clearly defined career path with positions available in varying levels. As a Senior Engineer, you will have the ability to manage and travel internationally. You can also move into roles that allow you to become an expert in a specific field, such as CSV or drug delivery technologies.
Salary for a Pharmaceutical Validation Engineer can vary depending on their industry and type of product they work with. While the national average for a pharmaceutical validation engineer is $98,150, some cities are more lucrative than others. Hayward CA, for instance, has a salary that is higher than the average at $18,034; San Jose CA, on the other hand, comes out tops with a salary of $21,856.
FAQ
Is there anything we should know about Manufacturing Processes prior to learning about Logistics.
No. You don't have to know about manufacturing processes before learning about logistics. But, being familiar with manufacturing processes will give you a better understanding about how logistics works.
Why is logistics important in manufacturing
Logistics are essential to any business. They are essential to any business's success.
Logistics are also important in reducing costs and improving efficiency.
What is the job of a manufacturer manager?
The manufacturing manager should ensure that every manufacturing process is efficient and effective. They should be aware of any issues within the company and respond accordingly.
They should also learn how to communicate effectively with other departments, including sales and marketing.
They should be informed about industry trends and be able make use of this information to improve their productivity and efficiency.
How can overproduction in manufacturing be reduced?
It is essential to find better ways to manage inventory to reduce overproduction. This would decrease the time that is spent on inefficient activities like purchasing, storing, or maintaining excess stock. We could use these resources to do other productive tasks.
You can do this by adopting a Kanban method. A Kanbanboard is a visual tool that allows you to keep track of the work being done. Kanban systems allow work items to move through different states until they reach their final destination. Each state has a different priority level.
When work is completed, it can be transferred to the next stage. It is possible to keep a task in the beginning stages until it gets to the end.
This allows for work to continue moving forward, while also ensuring that there is no work left behind. Managers can see how much work has been done and the status of each task at any time with a Kanban Board. This allows them to adjust their workflows based on real-time information.
Lean manufacturing is another option to control inventory levels. Lean manufacturing works to eliminate waste throughout every stage of the production chain. Anything that does not contribute to the product's value is considered waste. Some common types of waste include:
-
Overproduction
-
Inventory
-
Unnecessary packaging
-
Excess materials
Manufacturers can reduce their costs and improve their efficiency by using these ideas.
What are the four types in manufacturing?
Manufacturing refers the process of turning raw materials into useful products with machines and processes. It includes many different activities like designing, building and testing, packaging, shipping and selling, as well as servicing.
How can manufacturing avoid production bottlenecks
Production bottlenecks can be avoided by ensuring that processes are running smoothly during the entire production process, starting with the receipt of an order and ending when the product ships.
This includes planning to meet capacity requirements and quality control.
The best way to do this is to use continuous improvement techniques such as Six Sigma.
Six Sigma management is a system that improves quality and reduces waste within your organization.
It focuses on eliminating variation and creating consistency in your work.
Statistics
- [54][55] These are the top 50 countries by the total value of manufacturing output in US dollars for its noted year according to World Bank.[56] (en.wikipedia.org)
- According to a Statista study, U.S. businesses spent $1.63 trillion on logistics in 2019, moving goods from origin to end user through various supply chain network segments. (netsuite.com)
- You can multiply the result by 100 to get the total percent of monthly overhead. (investopedia.com)
- In the United States, for example, manufacturing makes up 15% of the economic output. (twi-global.com)
- (2:04) MTO is a production technique wherein products are customized according to customer specifications, and production only starts after an order is received. (oracle.com)
External Links
How To
How to Use the Just-In-Time Method in Production
Just-intime (JIT), a method used to lower costs and improve efficiency in business processes, is called just-in-time. It's a way to ensure that you get the right resources at just the right time. This means that you only pay for what you actually use. Frederick Taylor developed the concept while working as foreman in early 1900s. He saw how overtime was paid to workers for work that was delayed. He then concluded that if he could ensure that workers had enough time to do their job before starting to work, this would improve productivity.
The idea behind JIT is that you should plan ahead and have everything ready so you don't waste money. You should also look at the entire project from start to finish and make sure that you have sufficient resources available to deal with any problems that arise during the course of your project. You can anticipate problems and have enough equipment and people available to fix them. You won't have to pay more for unnecessary items.
There are many types of JIT methods.
-
Demand-driven: This type of JIT allows you to order the parts/materials required for your project on a regular basis. This will enable you to keep track of how much material is left after you use it. This will let you know how long it will be to produce more.
-
Inventory-based: This type allows you to stock the materials needed for your projects ahead of time. This allows you to forecast how much you will sell.
-
Project-driven: This is an approach where you set aside enough funds to cover the cost of your project. Knowing how much money you have available will help you purchase the correct amount of materials.
-
Resource-based JIT is the most widespread form. You allocate resources based on the demand. You will, for example, assign more staff to deal with large orders. If there aren't many orders, you will assign fewer people.
-
Cost-based : This is similar in concept to resource-based. But here, you aren't concerned about how many people your company has but how much each individual costs.
-
Price-based: This approach is very similar to the cost-based method except that you don't look at individual workers costs but the total cost of the company.
-
Material-based is an alternative to cost-based. Instead of looking at the total cost in the company, this method focuses on the average amount of raw materials that you consume.
-
Time-based JIT is another form of resource-based JIT. Instead of focusing only on how much each employee is costing, you should focus on how long it takes to complete your project.
-
Quality-based: This is yet another variation of resource-based JIT. Instead of thinking about how much each employee costs or how long it takes to manufacture something, you think about how good the quality of your product is.
-
Value-based JIT: One of the most recent forms of JIT. In this case, you're not concerned with how well the products perform or whether they meet customer expectations. Instead, your focus is on the value you bring to the market.
-
Stock-based is an inventory-based system that measures the number of items produced at any given moment. This method is useful when you want to increase production while decreasing inventory.
-
Just-in-time (JIT) planning: This is a combination of JIT and supply chain management. It's the process of scheduling delivery of components immediately after they are ordered. It's important as it reduces leadtimes and increases throughput.