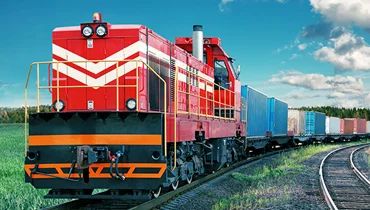
The Census Bureau collects important statistics about the economy every five years. These are called the Economic Census and are the basis for all other business and industry statistics.
The Economic Census covers business establishments, which are surveyed according to their primary business activity. The establishments can be classified according to their primary business activity and geographical location. This classification derives from the North American Industry Classification System.
Business Owners and Firms
Surveys of business owners and firms are conducted on a company or firm rather than an establishment basis. Companies and firms are defined by businesses with paid employees who report annual receipts at least $1,000. This survey includes sole proprietorships and nonfarm partnerships that are subject to the Internal Revenue Service tax, as well as reimbursable non-employer firms.
Characteristics Business Owners and Firms
The Census Bureau’s Survey of Business Owners, or SBO, is its largest survey of all business owners. This includes women and minority owners. It began as a special project for minority-owned businesses in 1969, and was incorporated into the economic census in 1972 along with the Survey of Women-Owned Businesses.
This is a relational database with information on 6 million single units and 1.8million multi-units. The Bureau uses the information in its economic data programs including the Census Bureau’s Economic Census and the County Business Patterns Program, as well as special summary and reimbursable statistics for non-employers.
Business Register and the Census Bureau's Statistical Abstract of Business Enterprises
SBO or the Statistical Abstract of Business Enterprises is the Census Bureau's principal source of non-employer firm information. It is a comprehensive database of paid employees for all known US establishments. The data are collected according to the type of firm, or by the owner of the firm, and are then used for many Census Bureau economic data programs.
SBO provides a variety of statistical measures not found in other census programs. This includes establishment deaths and births, firm start-ups and shutdowns as well job creations and destructions. SBO includes information on demographics of business owners such as their age and educational background, and also provides details about home-based businesses and franchise participation.
SBO Data for Minority- and Women-Owned Businesses
The Survey of Minority and Women-Owned Business (SMWOB) is an annual survey of businesses other than farms. It includes firms that file income tax as sole proprietorships, partnerships, corporations or individual proprietorships as well as those with at least $1,000 in receipts per year. This survey provides statistics on women and minorities-owned firms and an estimate of total annual receipts.
Researchers interested in women-owned and minority businesses should find it useful. It is also useful in studying the effects that discrimination has on the economy.
FAQ
What is the difference between manufacturing and logistics
Manufacturing is the production of goods using raw materials. Logistics includes all aspects related to supply chain management, such as procurement, distribution planning, inventory control and transportation. Logistics and manufacturing are often referred to as one thing. It encompasses both the creation of products and their delivery to customers.
What do you mean by warehouse?
A warehouse is a place where goods are stored until they are sold. It can be indoors or out. In some cases it could be both indoors and outdoors.
What are the 7 Rs of logistics?
The acronym 7R's of Logistic is an acronym that stands for seven fundamental principles of logistics management. It was developed and published by the International Association of Business Logisticians in 2004 as part of the "Seven Principles of Logistics Management".
The acronym consists of the following letters:
-
Responsible - ensure that actions are in compliance with legal requirements and do not cause harm to others.
-
Reliable - Have confidence in your ability to fulfill all of your commitments.
-
Use resources effectively and sparingly.
-
Realistic - Take into consideration all aspects of operations including cost-effectiveness, environmental impact, and other factors.
-
Respectful - treat people fairly and equitably.
-
Be resourceful: Look for opportunities to save money or increase productivity.
-
Recognizable - provide customers with value-added services.
What is the responsibility of a logistics manager?
A logistics manager makes sure that all goods are delivered on-time and in good condition. This is done through his/her expertise and knowledge about the company's product range. He/she should also ensure enough stock is available to meet demand.
Statistics
- According to the United Nations Industrial Development Organization (UNIDO), China is the top manufacturer worldwide by 2019 output, producing 28.7% of the total global manufacturing output, followed by the United States, Japan, Germany, and India.[52][53] (en.wikipedia.org)
- It's estimated that 10.8% of the U.S. GDP in 2020 was contributed to manufacturing. (investopedia.com)
- [54][55] These are the top 50 countries by the total value of manufacturing output in US dollars for its noted year according to World Bank.[56] (en.wikipedia.org)
- In the United States, for example, manufacturing makes up 15% of the economic output. (twi-global.com)
- According to a Statista study, U.S. businesses spent $1.63 trillion on logistics in 2019, moving goods from origin to end user through various supply chain network segments. (netsuite.com)
External Links
How To
How to Use 5S for Increasing Productivity in Manufacturing
5S stands for "Sort", "Set In Order", "Standardize", "Separate" and "Store". Toyota Motor Corporation created the 5S methodology in 1954. This methodology helps companies improve their work environment to increase efficiency.
This method has the basic goal of standardizing production processes to make them repeatable. It means tasks like cleaning, sorting or packing, labeling, and storing are done every day. These actions allow workers to perform their job more efficiently, knowing what to expect.
Implementing 5S requires five steps. These are Sort, Set In Order, Standardize. Separate. And Store. Each step is a different action that leads to greater efficiency. Sorting things makes it easier to find them later. When items are ordered, they are put together. Once you have separated your inventory into groups and organized them, you will store these groups in easily accessible containers. Finally, label all containers correctly.
Employees need to reflect on how they do their jobs. Employees need to understand the reasons they do certain jobs and determine if there is a better way. They must learn new skills and techniques in order to implement the 5S system.
The 5S method increases efficiency and morale among employees. As they begin to see improvements, they feel motivated to continue working towards the goal of achieving higher levels of efficiency.