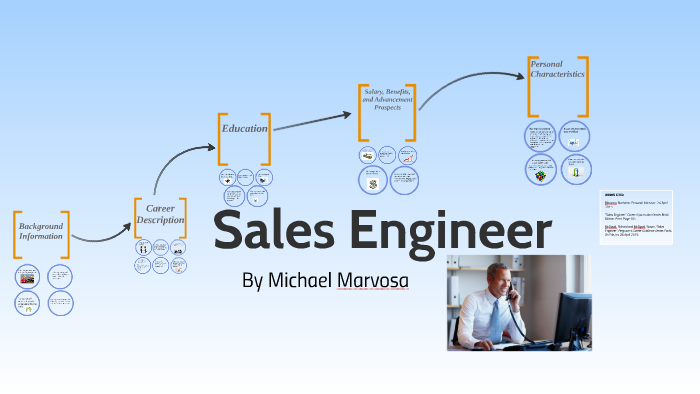
Advanced manufacturing can help increase productivity and cut costs in many ways, whether the product is a process or a part of the production line. Advanced manufacturing allows manufacturers quickly to produce prototypes, and to adjust production lines to suit design changes. It also allows manufacturers the ability to scale up or decrease based upon customer demand. It can also level the playing field between small and large manufacturers.
The definition of advanced manufacturing will vary from company to company. It depends on the industry, the process, and the application. Advanced manufacturing covers a broad range of activities. This includes research and development as well as design, manufacture, and post-sales. Innovative technologies can also be used. The main benefit of advanced manufacturing is that it offers a higher level of quality and efficiency in the production process. This can be achieved through the use of new technologies such as 3-D printers. Because of their low cost, they can be used in many industries. This type of manufacturing is also flexible and allows manufacturers to produce customized products in small batches. Advanced manufacturing also speeds up time to market.
Manufacturing is one of the largest sources of growth in the world. As such, the sector's economic impact is important to the economy, and the ripple effect can extend worldwide. As such, companies must invest in efficiency in all aspects of their business. This requires rapid piloting new technologies. The manufacturing sector is constantly changing and manufacturers must be ready to respond.
Safety, quality, precision are the most important aspects of manufacturing. Advanced manufacturing aims to produce high-quality products at a reasonable price. This includes innovative technologies as well as creative production methods. It is designed to produce a low-cost, efficient production line. Advanced manufacturing technology includes information communication technology and high-tech production system, as well as a variety processes.
The manufacturing sector continuously keeps up with advances in computer technology, materials, and electronic information. Nanotechnology has enabled advanced manufacturing systems to become more flexible, less intrusive and increased the functionality of production lines. It has also reduced the footprint of devices. It also includes automation which allows workers to be more focused on strategic tasks and less mundane work. It is possible to reduce production costs and improve efficiency through network communications.
Office of Counterterrorism and Emerging Threats, (OCET), has created a new website section to provide information on advanced manufacturing. The website will continue to provide news, funding opportunities and information. OCET collaborates with NIST to develop monoclonal antibodies that can be thermal stable.
As the manufacturing industry continues to develop, it is becoming more dependent upon information communication technology. This technology allows manufacturers to interact with each other and their machines and provides real-time alerts regarding any issues. It also allows manufacturers the ability to make precise tuning and close-loop feedback at the factory floor. This will improve manufacturing efficiency and reduce maintenance cost.
FAQ
How can efficiency in manufacturing be improved?
First, we need to identify which factors are most critical in affecting production times. Next, we must find ways to improve those factors. If you aren't sure where to begin, think about the factors that have the greatest impact on production time. Once you've identified them, try to find solutions for each of those factors.
What is the responsibility for a logistics manager
Logistics managers are responsible for ensuring that all goods arrive in perfect condition and on time. This is done by using his/her experience and knowledge of the company's products. He/she should make sure that enough stock is on hand to meet the demands.
How does a Production Planner differ from a Project Manager?
A production planner is more involved in the planning phase of the project than a project manger.
Why is logistics important for manufacturing?
Logistics are an essential part of any business. Logistics can help you achieve amazing results by helping to manage product flow from raw materials to finished products.
Logistics plays a significant role in reducing cost and increasing efficiency.
What skills do production planners need?
You must be flexible and organized to become a productive production planner. You must also be able to communicate effectively with clients and colleagues.
How can overproduction in manufacturing be reduced?
It is essential to find better ways to manage inventory to reduce overproduction. This would reduce the time needed to manage inventory. This would allow us to use our resources for more productive tasks.
This can be done by using a Kanban system. A Kanban board is a visual display used to track work in progress. A Kanban system allows work items to move through several states before reaching their final destination. Each state represents an individual priority level.
For instance, when work moves from one stage to another, the current task is complete enough to be moved to the next stage. However, if a task is still at the beginning stages, it will remain so until it reaches the end of the process.
This allows work to move forward and ensures that no work is missed. Managers can see how much work has been done and the status of each task at any time with a Kanban Board. This allows them to adjust their workflows based on real-time information.
Another way to control inventory levels is to implement lean manufacturing. Lean manufacturing works to eliminate waste throughout every stage of the production chain. Anything that does not contribute to the product's value is considered waste. The following are examples of common waste types:
-
Overproduction
-
Inventory
-
Unnecessary packaging
-
Material surplus
These ideas will help manufacturers increase efficiency and lower costs.
Statistics
- (2:04) MTO is a production technique wherein products are customized according to customer specifications, and production only starts after an order is received. (oracle.com)
- [54][55] These are the top 50 countries by the total value of manufacturing output in US dollars for its noted year according to World Bank.[56] (en.wikipedia.org)
- In 2021, an estimated 12.1 million Americans work in the manufacturing sector.6 (investopedia.com)
- According to the United Nations Industrial Development Organization (UNIDO), China is the top manufacturer worldwide by 2019 output, producing 28.7% of the total global manufacturing output, followed by the United States, Japan, Germany, and India.[52][53] (en.wikipedia.org)
- According to a Statista study, U.S. businesses spent $1.63 trillion on logistics in 2019, moving goods from origin to end user through various supply chain network segments. (netsuite.com)
External Links
How To
Six Sigma in Manufacturing:
Six Sigma is defined by "the application SPC (statistical process control) techniques to achieve continuous improvements." Motorola's Quality Improvement Department, Tokyo, Japan, developed it in 1986. Six Sigma's basic concept is to improve quality and eliminate defects through standardization. Many companies have adopted this method in recent years. They believe there is no such thing a perfect product or service. Six Sigma seeks to reduce variation between the mean production value. This means that if you take a sample of your product, then measure its performance against the average, you can find out what percentage of the time the process deviates from the norm. If the deviation is excessive, it's likely that something needs to be fixed.
Understanding how variability works in your company is the first step to Six Sigma. Once you have this understanding, you will need to identify sources and causes of variation. These variations can also be classified as random or systematic. Random variations happen when people make errors; systematic variations are caused externally. You could consider random variations if some widgets fall off the assembly lines. You might notice that your widgets always fall apart at the same place every time you put them together.
After identifying the problem areas, you will need to devise solutions. You might need to change the way you work or completely redesign the process. After implementing the new changes, you should test them again to see if they worked. If they don't work you need to rework them and come up a better plan.