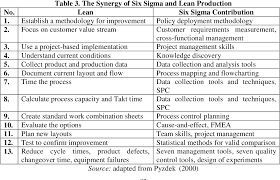
Federal and state government logistics jobs are available in both part time and full time capacities. They offer a number of advantages for job seekers. These include stable incomes, good benefits and good income. Government careers can also be a great way to obtain experience in the industry.
A Logistics Management Specialist, for example, is responsible for coordinating the supply chain. They manage suppliers and track deliveries. They are also responsible for identifying supply chain issues and creating contingency plan. You will need to have strong communication skills, good typing skills, and knowledge about government procurement regulations.
Supply Chain Managers can either work for the Department of Veterans Affairs (DVA) or the Department of Homeland Security. The first requires an in-depth knowledge of the federal government's procurement regulations. While the second position involves managing logistics operations, sourcing supplies and managing supply chain management. Candidates must have a bachelor's degree, depending on the job. Candidates should also be familiar with the regulations and business culture in the state they are applying for. Some positions require security clearances, and a candidate may be required to undergo a background check.
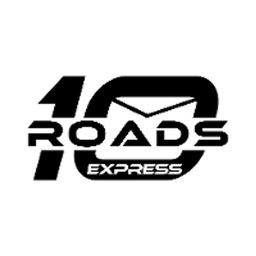
Other jobs for government logistics specialists involve deploying materials quickly after an incident occurs. The North Carolina Department of Public Safety provides a distribution position in disaster logistics. Candidates must have at minimum four years relevant experience. The position requires the candidate to be able manage people under stress.
The departmental level also requires Logistics Management Specialists. The Federal Aviation Administration has a similar role to the logistics specialist. An advanced degree and experience in operations management or project management are required.
You'll need to have the ability to handle large volumes of international travel if your goal is to become a government logistics manager. A background in procurement negotiations and supplier bid writing is also required. Candidates should have at least two years' relevant experience.
You can also apply for a variety other supply chain management roles in the federal government. These positions include those in transportation, warehousing, distribution, and air transport. Nearly one quarter of these jobs are offered by federal government. The states offer another eight percent.
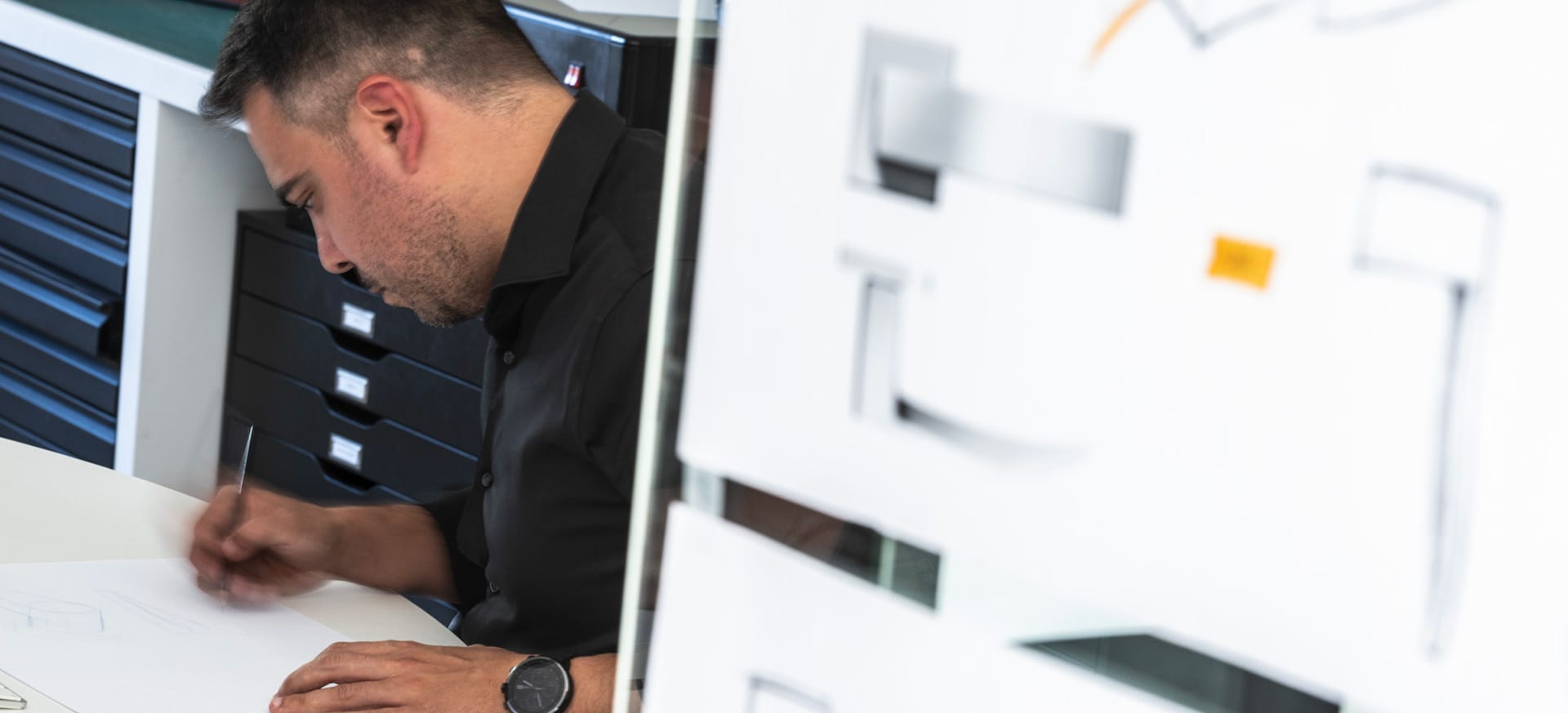
The federal government's website USAJOBS has many jobs. You can also search for a title or degree type. The majority of these positions require a minimum of a bachelor's, although some may require master's degrees. You can also find jobs as supply chain specialists in smaller organizations. A majority of supply chain professionals must have at least one (1) year of specialized experience in order to apply for a job.
Various positions for data scientists are available. Data Scientists support government programs and assist in the creation of strategic plans.
FAQ
Why automate your warehouse
Modern warehousing is becoming more automated. E-commerce has increased the demand for quicker delivery times and more efficient processes.
Warehouses should be able adapt quickly to new needs. They must invest heavily in technology to do this. The benefits of automating warehouses are numerous. These are just a few reasons to invest in automation.
-
Increases throughput/productivity
-
Reduces errors
-
Improves accuracy
-
Safety is boosted
-
Eliminates bottlenecks
-
Allows companies to scale more easily
-
Makes workers more efficient
-
The warehouse can be viewed from all angles.
-
Enhances customer experience
-
Improves employee satisfaction
-
It reduces downtime, and increases uptime
-
Ensures quality products are delivered on time
-
Human error can be eliminated
-
Helps ensure compliance with regulations
What are the essential elements of running a logistics firm?
You need to have a lot of knowledge and skills to manage a successful logistic business. Good communication skills are essential to effectively communicate with your suppliers and clients. You will need to know how to interpret data and draw conclusions. You must be able manage stress and pressure under pressure. To increase efficiency and creativity, you need to be creative. To motivate and guide your team towards reaching organizational goals, you must have strong leadership skills.
You must be organized to meet tight deadlines.
What kind of jobs are there in logistics?
There are many jobs available in logistics. Here are some examples:
-
Warehouse workers - They load trucks and pallets.
-
Transportation drivers – They drive trucks or trailers to transport goods and perform pick-ups.
-
Freight handlers - They sort and pack freight in warehouses.
-
Inventory managers - They oversee the inventory of goods in warehouses.
-
Sales representatives - They sell products.
-
Logistics coordinators - They plan and organize logistics operations.
-
Purchasing agents - They purchase goods and services needed for company operations.
-
Customer service representatives are available to answer customer calls and emails.
-
Shippers clerks - They process shipping order and issue bills.
-
Order fillers are people who fill orders based only on what was ordered.
-
Quality control inspectors are responsible for inspecting incoming and outgoing products looking for defects.
-
Others - There are many other types of jobs available in logistics, such as transportation supervisors, cargo specialists, etc.
How can manufacturing prevent production bottlenecks?
Avoiding production bottlenecks is as simple as keeping all processes running smoothly, from the time an order is received until the product ships.
This includes both quality control and capacity planning.
Continuous improvement techniques such Six Sigma can help you achieve this.
Six Sigma can be used to improve the quality and decrease waste in all areas of your company.
It is focused on creating consistency and eliminating variation in your work.
What makes a production planner different from a project manger?
The major difference between a Production Planner and a Project Manager is that a Project Manager is often the person responsible for organizing and planning the entire project. While a Production Planner is involved mainly in the planning stage,
What are the logistics products?
Logistics are the activities involved in moving goods from point A to point B.
They include all aspects associated with transport including packaging, loading transporting, unloading storage, warehousing inventory management customer service, distribution returns and recycling.
Logisticians make sure that the right product arrives at the right place at the correct time and in safe conditions. They help companies manage their supply chain efficiency by providing information on demand forecasts, stock levels, production schedules, and availability of raw materials.
They monitor shipments in transit, ensure quality standards, manage inventories, replenish orders, coordinate with suppliers and other vendors, and offer support services for sales, marketing, and customer service.
What are the 4 types of manufacturing?
Manufacturing refers the process of turning raw materials into useful products with machines and processes. It can involve many activities like designing, manufacturing, testing packaging, shipping, selling and servicing.
Statistics
- According to a Statista study, U.S. businesses spent $1.63 trillion on logistics in 2019, moving goods from origin to end user through various supply chain network segments. (netsuite.com)
- Job #1 is delivering the ordered product according to specifications: color, size, brand, and quantity. (netsuite.com)
- [54][55] These are the top 50 countries by the total value of manufacturing output in US dollars for its noted year according to World Bank.[56] (en.wikipedia.org)
- You can multiply the result by 100 to get the total percent of monthly overhead. (investopedia.com)
- (2:04) MTO is a production technique wherein products are customized according to customer specifications, and production only starts after an order is received. (oracle.com)
External Links
How To
How to Use the 5S to Increase Productivity In Manufacturing
5S stands in for "Sort", the "Set In Order", "Standardize", or "Separate". Toyota Motor Corporation developed the 5S method in 1954. It improves the work environment and helps companies to achieve greater efficiency.
This method aims to standardize production processes so that they are repeatable, measurable and predictable. This means that every day tasks such cleaning, sorting/storing, packing, and labeling can be performed. This knowledge allows workers to be more efficient in their work because they are aware of what to expect.
Implementing 5S requires five steps. These are Sort, Set In Order, Standardize. Separate. And Store. Each step requires a different action, which increases efficiency. By sorting, for example, you make it easy to find the items later. Once you have placed items in an ordered fashion, you will put them together. After you have divided your inventory into groups you can store them in easy-to-reach containers. Finally, label all containers correctly.
Employees need to reflect on how they do their jobs. Employees must be able to see why they do what they do and find a way to achieve them without having to rely on their old methods. They must learn new skills and techniques in order to implement the 5S system.
The 5S method not only increases efficiency but also boosts morale and teamwork. They will feel motivated to strive for higher levels of efficiency once they start to see results.