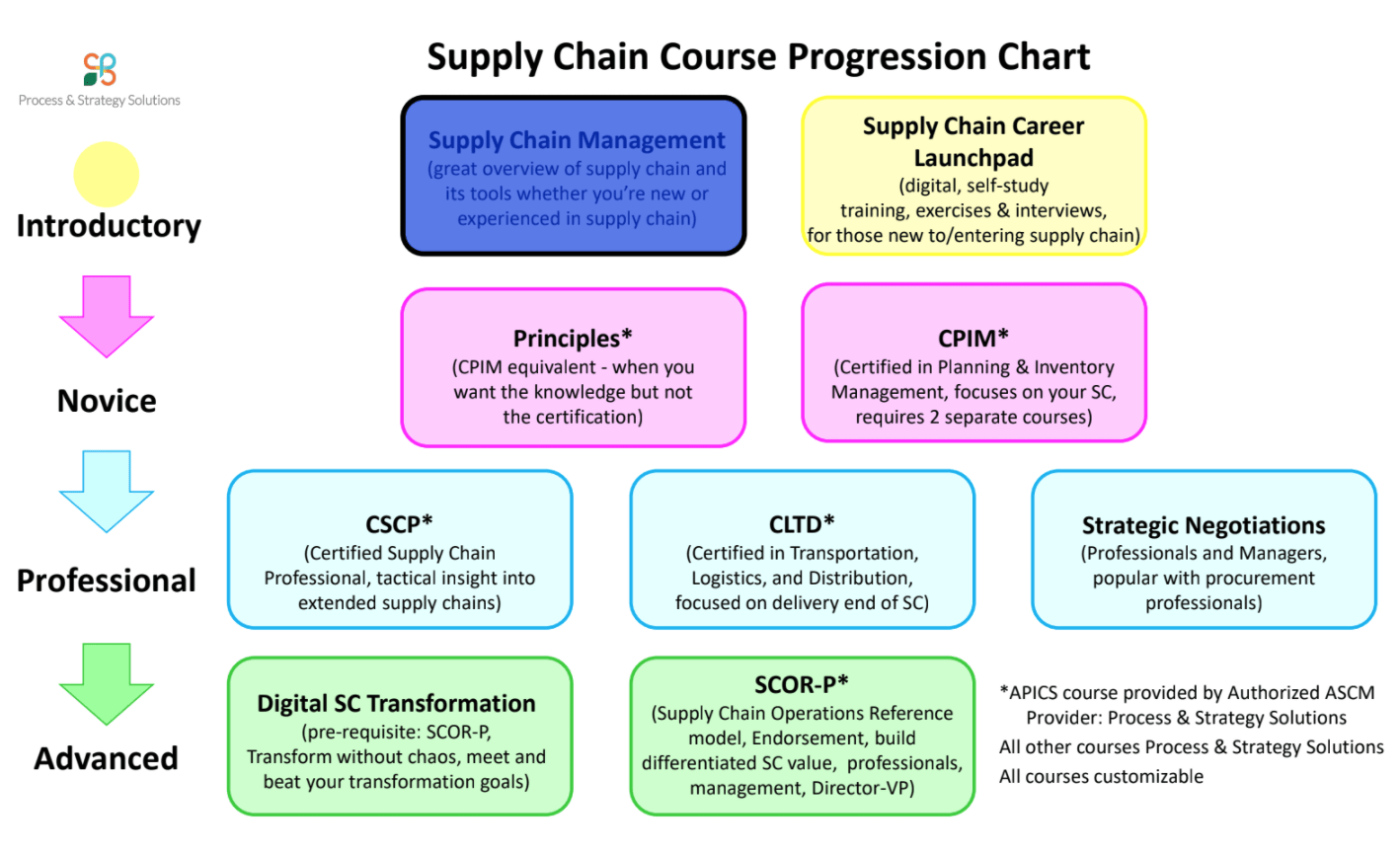
But value stream mapping can make your manufacturing processes more efficient. It's not simple. It involves mapping product products and product families. Training is essential for the team. You might also need a value-stream manager. Your team should get support from the leadership in order to successfully implement the strategy. Larger companies may have their own value stream managers to oversee the mapping process. While smaller businesses can work without a VSM manager for their mapping process, it can be advantageous to show leadership the improvement opportunities.
Lean Six Sigma
Value Stream Mapping, which is Lean Six Sigma's Lean Six Sigma tool, allows you to record the flow and information that flows from customers into suppliers. Your customer should be your first item on your Value Stream Mapping. Start at the shipping point and work your way upstream. Include a box that contains customer's data. This will show you how often the product must be made to meet the demand. You'll also need to know the Takt time (the amount of time it takes to produce a product), and how it compares to the cycle time of the product. If Takt is longer than the cycle times, it means that there is a bottleneck.
Value stream maps are a tool that can help companies find waste at every stage of their process. Value stream mapping helps you to identify and analyze non-value-added activity and the flow information. It is also useful in identifying bottlenecks or determining how to improve the efficiency of the whole process. The benefits of using Value Stream Mapping in Lean Six Sigma go beyond simply improving the flow of information - a Value Stream Map can be a valuable tool in helping you implement Lean Six Sigma and improve your bottom line.
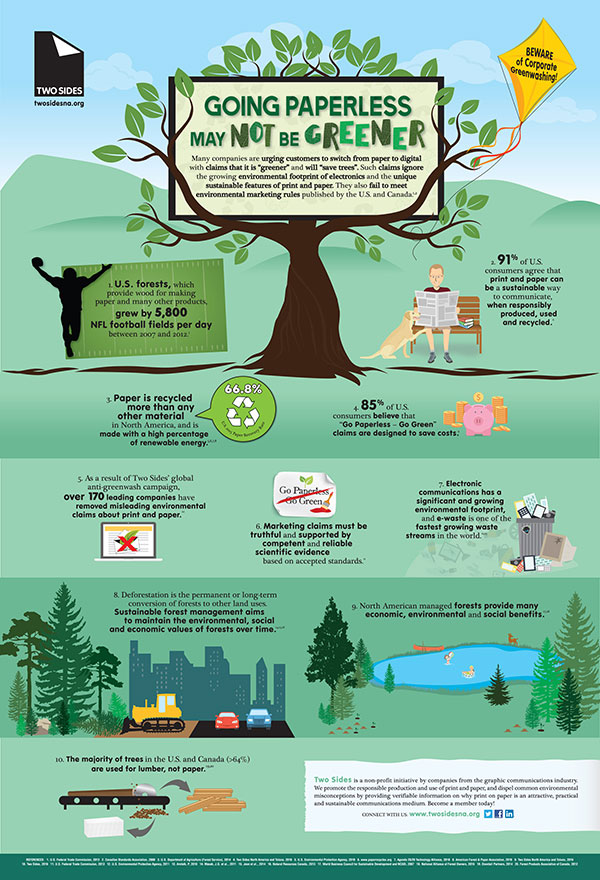
Lean Healthcare
Value stream mapping can be used to improve the synchronization between activities within the medical field. It helps identify areas that need improvement and recommends ways to implement them. A map could show a patient's flow, from their arrival at the hospital to when they leave after treatment. By visualizing these flow paths, you can create a timeline for the whole process and identify value-added activities and waste-generating steps.
In order to make VSM in Lean Healthcare more effective, the authors recommend setting up clear definitions of the terms used in the process. They recommend sharing success stories and sharing failures as indicators. These will allow the results to be replicated and modified for specific situations. Lean methodologies in healthcare are more likely than not to lead to positive outcomes. The authors recommend that healthcare professionals agree on a common definition for value stream mapping to ensure that this methodology is widely used.
Lean Manufacturing
You need to have input from the key stakeholders in order to start value stream mapping. The team should include all people responsible to fulfill customer needs. These people should include those who are responsible for ensuring information flows and materials flow. This can be done by gathering input and suggestions from the key stakeholders. To begin, define the scope of the value stream mapping process.
Next, you will need to choose the product/process that needs improvement and then train the team in value stream modeling. The mapping process begins with customer needs. It includes everything from when the customer is contacted to the decision making and communication that follows. Ultimately, value stream mapping aims to eliminate waste and make the process more efficient, while improving customer satisfaction. Lean manufacturing can provide a viable, sustainable solution that addresses the unique challenges faced by any company by identifying and eliminating those elements.
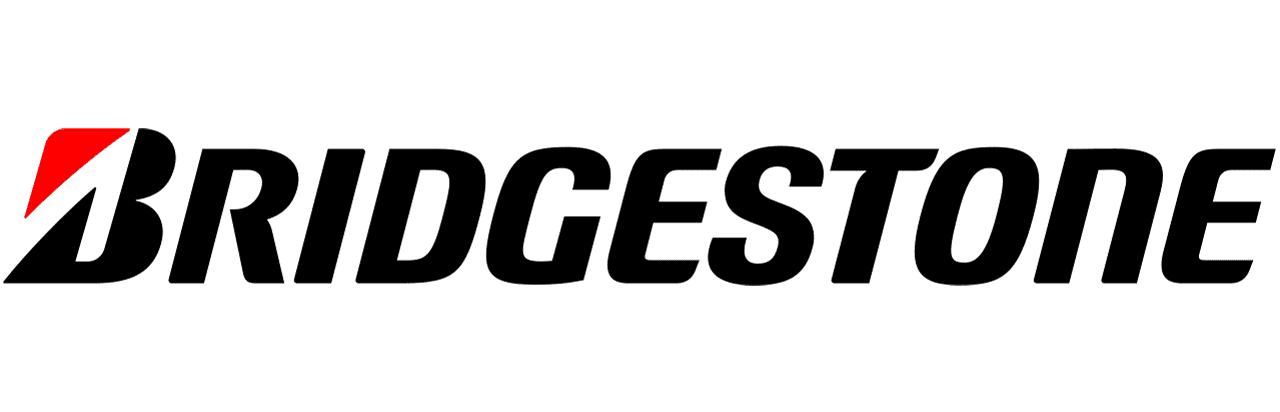
Future state value stream mapping
Future state value stream mapping is a great tool to identify waste. This type of mapping helps to identify the causes and eliminate them. Future state ideas are marked by the same symbols of current state mapping. Takt Time is a key concept in future state value stream mapping. It allows you to allocate resources effectively and to identify areas of waste. Your company can also use the future state value stream map as a powerful tool.
Once you have identified the problems and their relationship to the future state it is time to map out the steps that you will need to take. The future state map can be used by teams as a guideline for completing projects and reaching the target value. It's essential to update your future state value stream mapping every six to twelve months, so you can measure your progress as it occurs. You should update your future state map as new projects are launched and modifications made.
FAQ
What skills should a production planner have?
To become a successful production planner, you need to be organized, flexible, and able to multitask. Communication skills are essential to ensure that you can communicate effectively with clients, colleagues, and customers.
What can I do to learn more about manufacturing?
The best way to learn about manufacturing is through hands-on experience. But if that is not possible you can always read books and watch educational videos.
How can overproduction in manufacturing be reduced?
Better inventory management is key to reducing excess production. This would reduce time spent on activities such as purchasing, stocking, and maintaining excess stock. This would allow us to use our resources for more productive tasks.
Kanban systems are one way to achieve this. A Kanban board is a visual display used to track work in progress. A Kanban system allows work items to move through several states before reaching their final destination. Each state is assigned a different priority.
When work is completed, it can be transferred to the next stage. It is possible to keep a task in the beginning stages until it gets to the end.
This allows work to move forward and ensures that no work is missed. Managers can monitor the work being done by Kanban boards to see what is happening at any given time. This allows them the ability to adjust their workflow using real-time data.
Lean manufacturing, another method to control inventory levels, is also an option. Lean manufacturing is about eliminating waste from all stages of the production process. Any product that isn't adding value can be considered waste. These are some of the most common types.
-
Overproduction
-
Inventory
-
Unnecessary packaging
-
Overstock materials
These ideas can help manufacturers improve efficiency and reduce costs.
Is it possible to automate certain parts of manufacturing
Yes! Since ancient times, automation has been in existence. The Egyptians invented the wheel thousands of years ago. Today, robots assist in the assembly of lines.
There are many applications for robotics in manufacturing today. These include:
-
Line robots
-
Robot welding
-
Robot painting
-
Robotics inspection
-
Robots that create products
Automation could also be used to improve manufacturing. 3D printing makes it possible to produce custom products in a matter of days or weeks.
What are the four types in manufacturing?
Manufacturing refers the process of turning raw materials into useful products with machines and processes. It can involve many activities like designing, manufacturing, testing packaging, shipping, selling and servicing.
Is automation necessary in manufacturing?
Automation is important not only for manufacturers but also for service providers. It allows them provide faster and more efficient services. It reduces human errors and improves productivity, which in turn helps them lower their costs.
Statistics
- Many factories witnessed a 30% increase in output due to the shift to electric motors. (en.wikipedia.org)
- You can multiply the result by 100 to get the total percent of monthly overhead. (investopedia.com)
- In the United States, for example, manufacturing makes up 15% of the economic output. (twi-global.com)
- Job #1 is delivering the ordered product according to specifications: color, size, brand, and quantity. (netsuite.com)
- It's estimated that 10.8% of the U.S. GDP in 2020 was contributed to manufacturing. (investopedia.com)
External Links
How To
How to use Lean Manufacturing in the production of goods
Lean manufacturing (or lean manufacturing) is a style of management that aims to increase efficiency, reduce waste and improve performance through continuous improvement. It was first developed in Japan in the 1970s/80s by Taiichi Ahno, who was awarded the Toyota Production System (TPS), award from KanjiToyoda, the founder of TPS. Michael L. Watkins published the original book on lean manufacturing, "The Machine That Changed the World," in 1990.
Lean manufacturing can be described as a set or principles that are used to improve quality, speed and cost of products or services. It emphasizes eliminating waste and defects throughout the value stream. Lean manufacturing can be described as just-in–time (JIT), total productive maintenance, zero defect (TPM), or even 5S. Lean manufacturing is about eliminating activities that do not add value, such as inspection, rework, and waiting.
Lean manufacturing can help companies improve their product quality and reduce costs. Additionally, it helps them achieve their goals more quickly and reduces employee turnover. Lean manufacturing is considered one of the most effective ways to manage the entire value chain, including suppliers, customers, distributors, retailers, and employees. Many industries worldwide use lean manufacturing. For example, Toyota's philosophy underpins its success in automobiles, electronics, appliances, healthcare, chemical engineering, aerospace, paper, food, etc.
Five fundamental principles underlie lean manufacturing.
-
Define Value - Identify the value your business adds to society and what makes you different from competitors.
-
Reduce waste - Get rid of any activity that does not add value to the supply chain.
-
Create Flow: Ensure that the work process flows without interruptions.
-
Standardize and simplify – Make processes as repeatable and consistent as possible.
-
Build Relationships- Develop personal relationships with both internal as well as external stakeholders.
Although lean manufacturing has always been around, it is gaining popularity in recent years because of a renewed interest for the economy after 2008's global financial crisis. Many companies have adopted lean manufacturing methods to increase their marketability. Some economists even believe that lean manufacturing can be a key factor in economic recovery.
Lean manufacturing is now becoming a common practice in the automotive industry, with many benefits. These include higher customer satisfaction, lower inventory levels, lower operating expenses, greater productivity, and improved overall safety.
Any aspect of an enterprise can benefit from Lean manufacturing. This is because it ensures efficiency and effectiveness in all stages of the value chain.
There are three types of lean manufacturing.
-
Just-in Time Manufacturing (JIT), also known as "pull system": This form of lean manufacturing is often referred to simply as "pull". JIT is a method in which components are assembled right at the moment of use, rather than being manufactured ahead of time. This approach reduces lead time, increases availability and reduces inventory.
-
Zero Defects Manufacturing - ZDM: ZDM focuses its efforts on making sure that no defective units leave a manufacturing facility. Repairing a part that is damaged during assembly should be done, not scrapping. This is also true for finished products that require minor repairs before shipping.
-
Continuous Improvement (CI: Continuous improvement aims to increase the efficiency of operations by constantly identifying and making improvements to reduce or eliminate waste. It involves continuous improvement of processes, people, and tools.