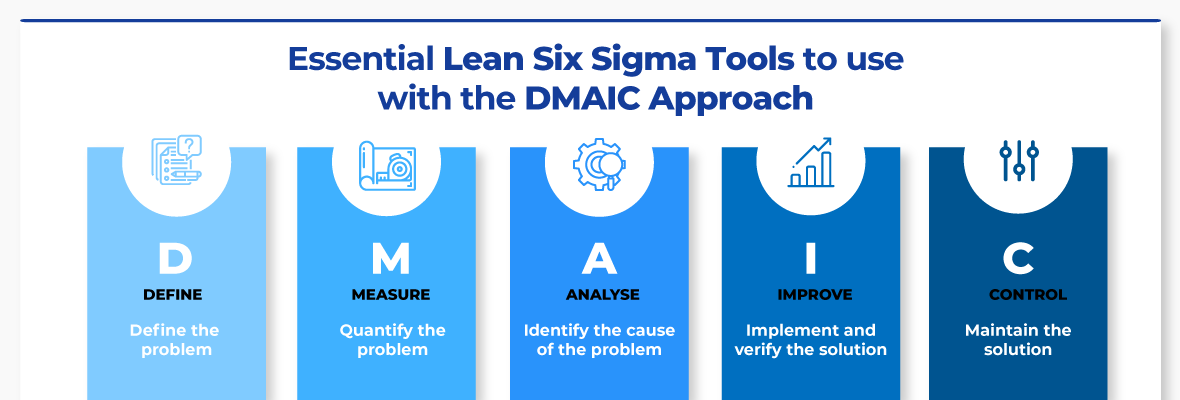
DMAIC, or the DMAIC model, is a process improvement method that includes five steps. It is commonly used by Six Sigma professionals to make quality improvements in a company, but it can also be implemented independently as an effective and structured continuous improvement process.
Dmaic, a quality method that reduces defects, costs and rework. It is a method that has been proven to improve customer satisfaction by ensuring products of high-quality, are efficient and perform consistently.
DMAIC can be an effective way to resolve issues within a company. It can also be used to improve processes that impact customer satisfaction, quality of products, cost reductions and cycle times. This is a key component of any quality improvement programme.
The DMAIC approach is a structured solution to problems that can help an organization identify and eliminate the root issues of any problem. The DMAIC model is a structured approach to problem-solving that helps an organization eliminate the root causes of a given issue.
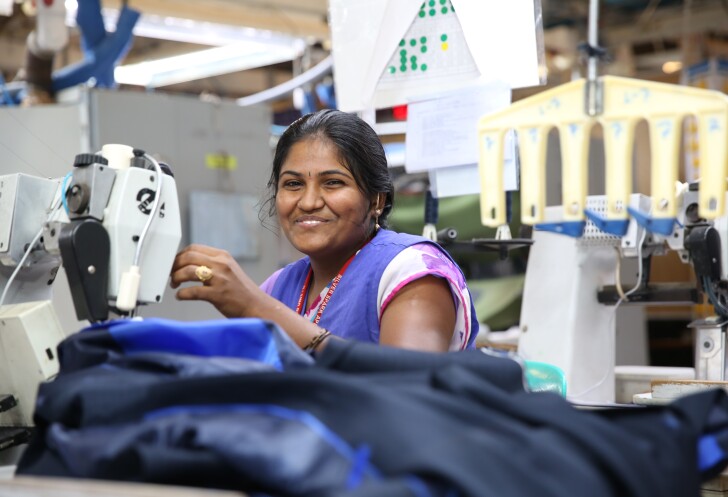
It is a powerful tool in Lean Six Sigma because it gives teams a defined and structured path to follow to find and fix quality problems. It is particularly important when dealing with complex problems that have unclear causes or involve risks from inaction.
Before selecting a DMAIC project, it is important to understand the criteria that should be met. Also, it is important to know the tools which can be utilized during the process.
You can begin the DMAIC process once you've identified a project that meets DMAIC criteria. The best projects to choose are those that relate to the current status of the business, and also meet the DMAIC requirements.
In the Define phase, DMAIC requires that the problem to be solved and the scope of improvement are clearly defined. This can either be a formal charter for the project or it can also take a more informal form. The document identifies CTQ issues (critical to the quality), the core business processes and the scope.
This step is crucial in the DMAIC method because it helps teams understand what issues they need to address first, how long they will have to work and which metrics they can use to measure their success. The DMAIC process allows teams identify their project leader and to set up the conditions for a DMAIC success.
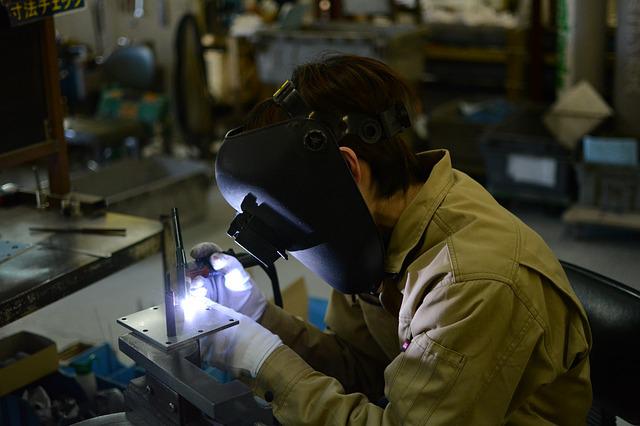
In the Measure phase, teams collect data from the current state and compare it to the goal state. They use this data to determine the gap between the two states, and identify improvement opportunities. It is possible to do this using different tools like scatterplots (or frequency plots), statistical analysis, or even scatterplots.
After analyzing all the data collected, the team identifies potential solutions and tests them to see if they work. The teams also test the solutions and implement them to verify that they are sustainable and measurable.
FAQ
Why automate your warehouse
Automation has become increasingly important in modern warehousing. The rise of e-commerce has led to increased demand for faster delivery times and more efficient processes.
Warehouses must be able to quickly adapt to changing demands. Technology investment is necessary to enable warehouses to respond quickly to changing demands. Automating warehouses is a great way to save money. Here are some of the reasons automation is worth your investment:
-
Increases throughput/productivity
-
Reduces errors
-
Increases accuracy
-
Safety Boosts
-
Eliminates bottlenecks
-
Allows companies to scale more easily
-
Workers are more productive
-
Gives you visibility into all that is happening in your warehouse
-
Enhances customer experience
-
Improves employee satisfaction
-
This reduces downtime while increasing uptime
-
Ensures quality products are delivered on time
-
Removing human error
-
It ensures compliance with regulations
What is the job of a manufacturer manager?
The manufacturing manager should ensure that every manufacturing process is efficient and effective. They should also be aware of any problems within the company and act accordingly.
They should also know how to communicate with other departments such as sales and marketing.
They should also be knowledgeable about the latest trends in the industry so they can use this information for productivity and efficiency improvements.
What are the 7 R's of logistics?
The acronym 7R's for Logistics stands to represent the seven basic principles in logistics management. It was developed by International Association of Business Logisticians (IABL), and published as part of their "Seven Principles of Logistics Management Series" in 2004.
The following letters make up the acronym:
-
Responsible – ensure that all actions are legal and don't cause harm to anyone else.
-
Reliable - have confidence in the ability to deliver on commitments made.
-
Be responsible - Use resources efficiently and avoid wasting them.
-
Realistic - Take into consideration all aspects of operations including cost-effectiveness, environmental impact, and other factors.
-
Respectful - Treat people fairly and equitably
-
Reliable - Find ways to save money and increase your productivity.
-
Recognizable is a company that provides customers with value-added solutions.
Are there any Manufacturing Processes that we should know before we can learn about Logistics?
No. You don't have to know about manufacturing processes before learning about logistics. It is important to know about the manufacturing processes in order to understand how logistics works.
Is automation important in manufacturing?
Automation is important not only for manufacturers but also for service providers. It enables them to provide services faster and more efficiently. In addition, it helps them reduce costs by reducing human errors and improving productivity.
Statistics
- Many factories witnessed a 30% increase in output due to the shift to electric motors. (en.wikipedia.org)
- (2:04) MTO is a production technique wherein products are customized according to customer specifications, and production only starts after an order is received. (oracle.com)
- It's estimated that 10.8% of the U.S. GDP in 2020 was contributed to manufacturing. (investopedia.com)
- You can multiply the result by 100 to get the total percent of monthly overhead. (investopedia.com)
- According to the United Nations Industrial Development Organization (UNIDO), China is the top manufacturer worldwide by 2019 output, producing 28.7% of the total global manufacturing output, followed by the United States, Japan, Germany, and India.[52][53] (en.wikipedia.org)
External Links
How To
Six Sigma in Manufacturing
Six Sigma is defined as "the application of statistical process control (SPC) techniques to achieve continuous improvement." Motorola's Quality Improvement Department developed it at their Tokyo plant in Japan in 1986. Six Sigma is a method to improve quality through standardization and elimination of defects. In recent years, many companies have adopted this method because they believe there is no such thing as perfect products or services. Six Sigma's primary goal is to reduce variation from the average value of production. This means that if you take a sample of your product, then measure its performance against the average, you can find out what percentage of the time the process deviates from the norm. If it is too large, it means that there are problems.
The first step toward implementing Six Sigma is understanding how variability works in your business. Once you've understood that, you'll want to identify sources of variation. These variations can also be classified as random or systematic. Random variations occur when people do mistakes. Symmetrical variations are caused due to factors beyond the process. These are, for instance, random variations that occur when widgets are made and some fall off the production line. However, if you notice that every time you assemble a widget, it always falls apart at exactly the same place, then that would be a systematic problem.
Once you've identified where the problems lie, you'll want to design solutions to eliminate those problems. You might need to change the way you work or completely redesign the process. Once you have implemented the changes, it is important to test them again to ensure they work. If they didn't work, then you'll need to go back to the drawing board and come up with another plan.