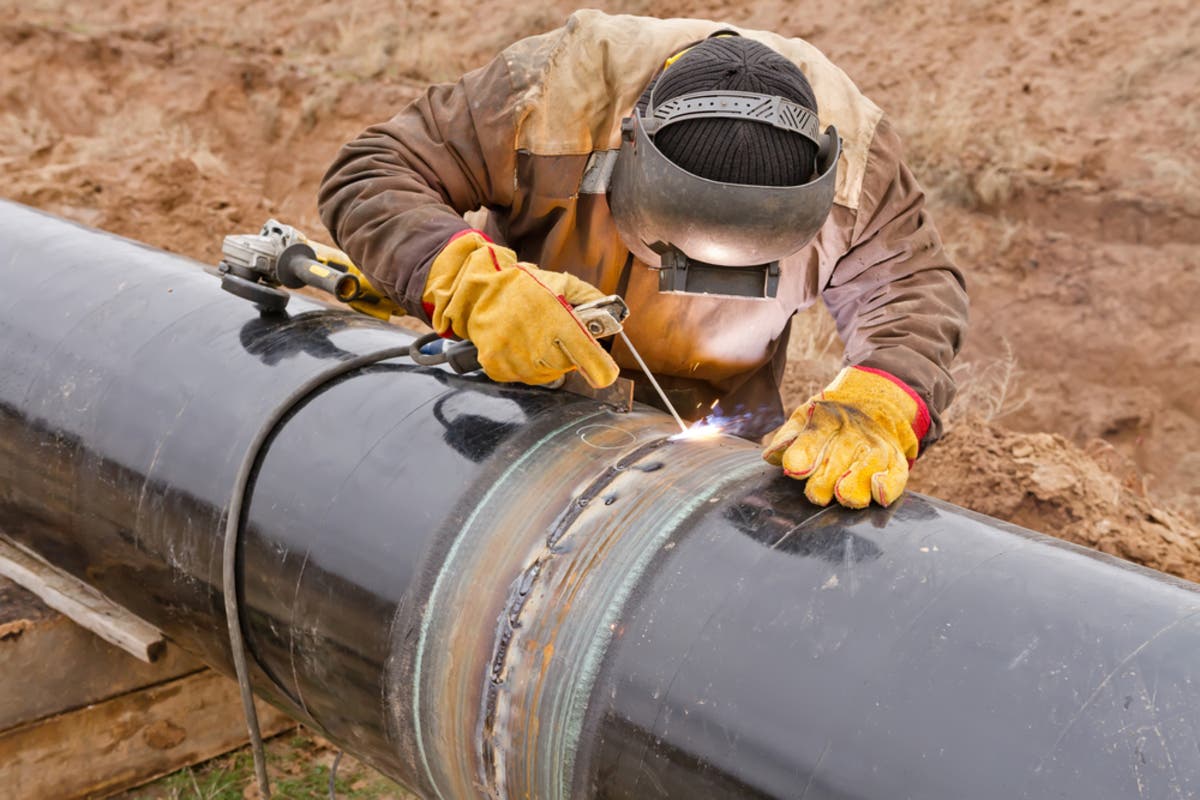
Classic economics has three basic sectors. These categories can be broken down into manufacturing, services, or financial activities. The characteristics and risk factors that go into a business' classification are important. You will find out more about each sector below. This is a brief overview of the types of businesses in each sector. If you're interested, you can continue to explore this information. You should remember that these categories can't be considered mutually exclusive.
Economic activity
The factors that affect production, inputs and outputs have a significant impact on the country's economic activities. The demand for a particular good or service is often a key factor in determining the region's economic activity. There are two types economic activity: primary or secondary. Primary economic activities are those that provide goods and services for daily human needs. Secondary economic activities add value or combine raw materials to produce a more valuable product. Manufacturing and processing are two examples of secondary activities.
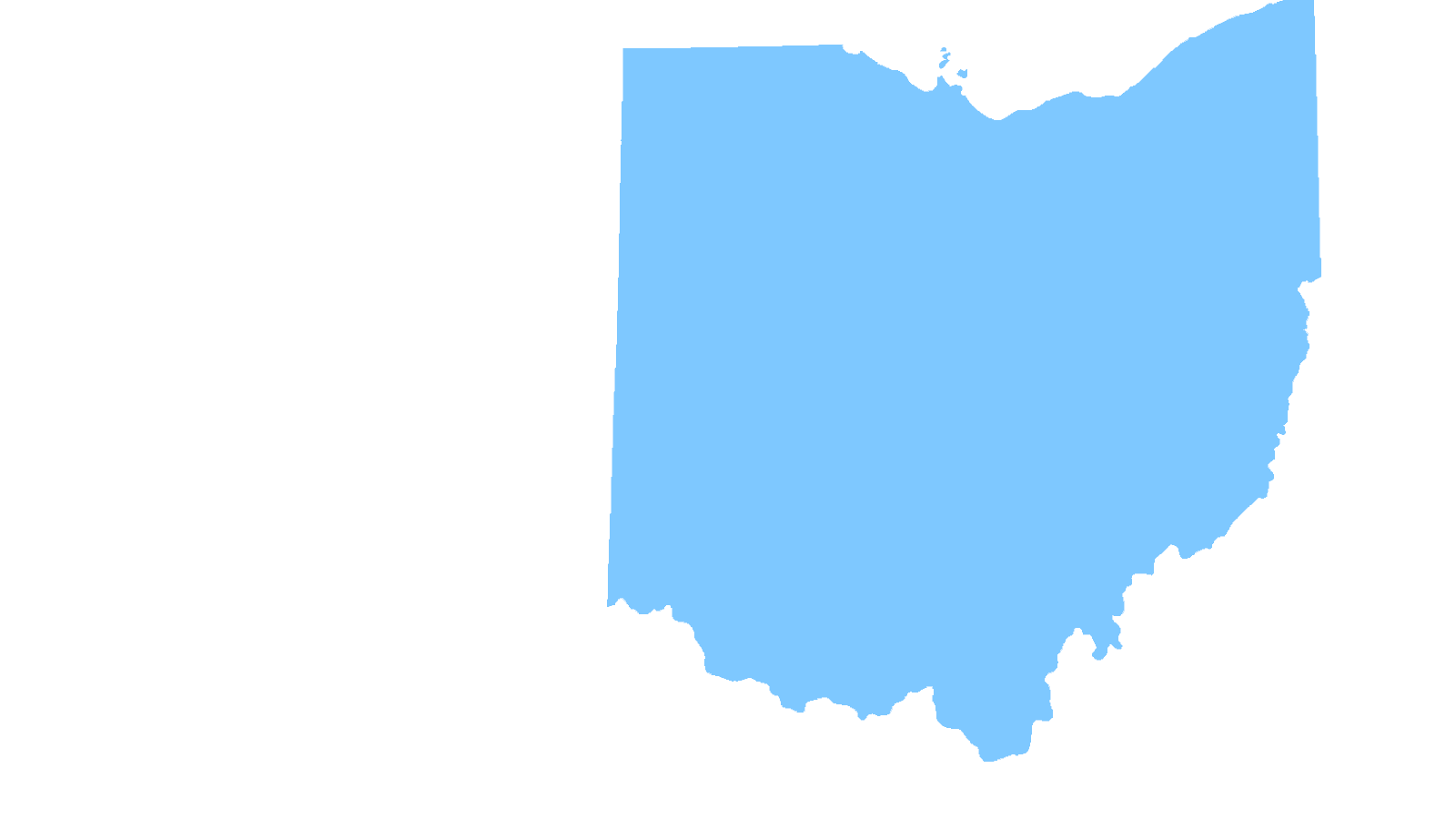
Classification of businesses
Business classification is the process of dividing businesses into groups based on the type of activities they perform. There are two main types of business classification: primary and secundary. Primary businesses are those that mine and trade natural resources. The second kind of business converts raw materials and produces products for sale. There are many differences between the two types. Below are the main differences between these two types. You can use the information from this article to help you decide which type of business is best for your company.
Characteristics
This discussion will explain the differences between primary, secondary and tertiary sector and focus on the economic impact of each. First, let's define sectors. Sectors are unique economic entities and respond differently to different factors. These conditions may occur repeatedly, like business cycles. Or they could be unique events, like technological advancements. These characteristics can be used to identify the most lucrative sectors and to determine their relative importance in an economy.
Risques
Industry risk refers to the variability in performance between industries and companies. It can be measured through assessing variances in profitability (ROE) or return on equity. This could also reflect stock market performance, depending on which industry. An example of this is a steel company, which is considered to be at high risk because there are potential earthquakes in the region. Investors may be able to identify which sectors are most volatile by studying these risks.
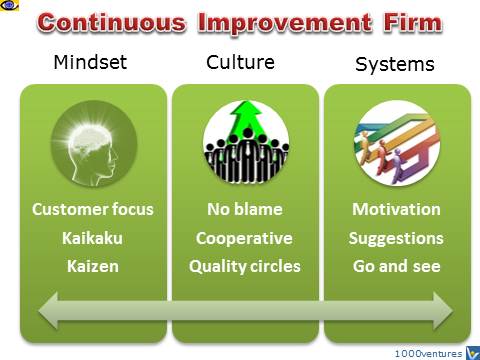
Investing
Although many investors prefer to invest in companies, it is possible to invest in sectors. Sectors are more risk-free and can be found within mutual funds and exchange traded funds. Sector investing is also becoming a popular investment strategy. This article will discuss how sector investing can help you find the right investments. Learn more by reading the following. Don't forget our free resource section to get more information.
FAQ
Is it necessary to be familiar with Manufacturing Processes before we learn about Logistics.
No. You don't have to know about manufacturing processes before learning about logistics. Understanding the manufacturing process will allow you to better understand logistics.
Why automate your warehouse
Automation has become increasingly important in modern warehousing. E-commerce has increased the demand for quicker delivery times and more efficient processes.
Warehouses must be able to quickly adapt to changing demands. In order to do this, they need to invest in technology. Automation warehouses can bring many benefits. These are just a few reasons to invest in automation.
-
Increases throughput/productivity
-
Reduces errors
-
Increases accuracy
-
Boosts safety
-
Eliminates bottlenecks
-
Companies can scale more easily
-
Makes workers more efficient
-
It gives visibility to everything that happens inside the warehouse
-
Enhances customer experience
-
Improves employee satisfaction
-
Reducing downtime and increasing uptime
-
Quality products delivered on time
-
Eliminates human error
-
It ensures compliance with regulations
What is the role of a manager in manufacturing?
A manufacturing manager must ensure that all manufacturing processes are efficient and effective. They must also be alert to any potential problems and take appropriate action.
They should also learn how to communicate effectively with other departments, including sales and marketing.
They must also keep up-to-date with the latest trends in their field and be able use this information to improve productivity and efficiency.
What is the distinction between Production Planning or Scheduling?
Production Planning (PP), is the process of deciding what production needs to take place at any given time. Forecasting and identifying production capacity are two key elements to this process.
Scheduling refers the process by which tasks are assigned dates so that they can all be completed within the given timeframe.
What is the job of a production plan?
A production planner ensures all aspects of the project are delivered on time, within budget, and within scope. A production planner ensures that the service and product meet the client's expectations.
What are the logistics products?
Logistics refers to the movement of goods from one place to another.
They include all aspects associated with transport including packaging, loading transporting, unloading storage, warehousing inventory management customer service, distribution returns and recycling.
Logisticians ensure the product reaches its destination in the most efficient manner. They help companies manage their supply chain efficiency by providing information on demand forecasts, stock levels, production schedules, and availability of raw materials.
They keep track and monitor the transit of shipments, maintain quality standards, order replenishment and inventories, coordinate with suppliers, vendors, and provide support for sales and marketing.
Statistics
- In 2021, an estimated 12.1 million Americans work in the manufacturing sector.6 (investopedia.com)
- Job #1 is delivering the ordered product according to specifications: color, size, brand, and quantity. (netsuite.com)
- Many factories witnessed a 30% increase in output due to the shift to electric motors. (en.wikipedia.org)
- According to the United Nations Industrial Development Organization (UNIDO), China is the top manufacturer worldwide by 2019 output, producing 28.7% of the total global manufacturing output, followed by the United States, Japan, Germany, and India.[52][53] (en.wikipedia.org)
- In the United States, for example, manufacturing makes up 15% of the economic output. (twi-global.com)
External Links
How To
How to use lean manufacturing in the production of goods
Lean manufacturing refers to a method of managing that seeks to improve efficiency and decrease waste. It was first developed in Japan in the 1970s/80s by Taiichi Ahno, who was awarded the Toyota Production System (TPS), award from KanjiToyoda, the founder of TPS. The first book published on lean manufacturing was titled "The Machine That Changed the World" written by Michael L. Watkins and published in 1990.
Lean manufacturing is often described as a set if principles that help improve the quality and speed of products and services. It emphasizes reducing defects and eliminating waste throughout the value chain. The five-steps of Lean Manufacturing are just-in time (JIT), zero defect and total productive maintenance (TPM), as well as 5S. Lean manufacturing seeks to eliminate non-value added activities, such as inspection, work, waiting, and rework.
Lean manufacturing is a way for companies to achieve their goals faster, improve product quality, and lower costs. Lean manufacturing is a great way to manage the entire value chain including customers, suppliers, distributors and retailers as well as employees. Lean manufacturing is widely used in many industries. Toyota's philosophy is the foundation of its success in automotives, electronics and appliances, healthcare, chemical engineers, aerospace, paper and food, among other industries.
Five fundamental principles underlie lean manufacturing.
-
Define value - Find out what your business contributes to society, and what makes it different from other competitors.
-
Reduce waste - Stop any activity that isn't adding value to the supply chains.
-
Create Flow. Ensure that your work is uninterrupted and flows seamlessly.
-
Standardize and Simplify – Make processes as consistent, repeatable, and as simple as possible.
-
Build relationships - Develop and maintain personal relationships with both your internal and external stakeholders.
Lean manufacturing, although not new, has seen renewed interest in the economic sector since 2008. To increase their competitiveness, many businesses have turned to lean manufacturing. In fact, some economists believe that lean manufacturing will be an important factor in economic recovery.
Lean manufacturing is becoming a popular practice in automotive. It has many advantages. These include higher customer satisfaction levels, reduced inventory levels as well as lower operating costs.
Lean manufacturing can be applied to almost every aspect of an organization. This is because it ensures efficiency and effectiveness in all stages of the value chain.
There are three types of lean manufacturing.
-
Just-in Time Manufacturing, (JIT): This kind of lean manufacturing is also commonly known as "pull-systems." JIT stands for a system where components are assembled on the spot rather than being made in advance. This approach reduces lead time, increases availability and reduces inventory.
-
Zero Defects Manufacturing (ZDM): ZDM focuses on ensuring that no defective units leave the manufacturing facility. Repairing a part that is damaged during assembly should be done, not scrapping. This applies to finished products, which may need minor repairs before they are shipped.
-
Continuous Improvement (CI): CI aims to improve the efficiency of operations by continuously identifying problems and making changes in order to eliminate or minimize waste. Continuous Improvement (CI) involves continuous improvement in processes, people, tools, and infrastructure.