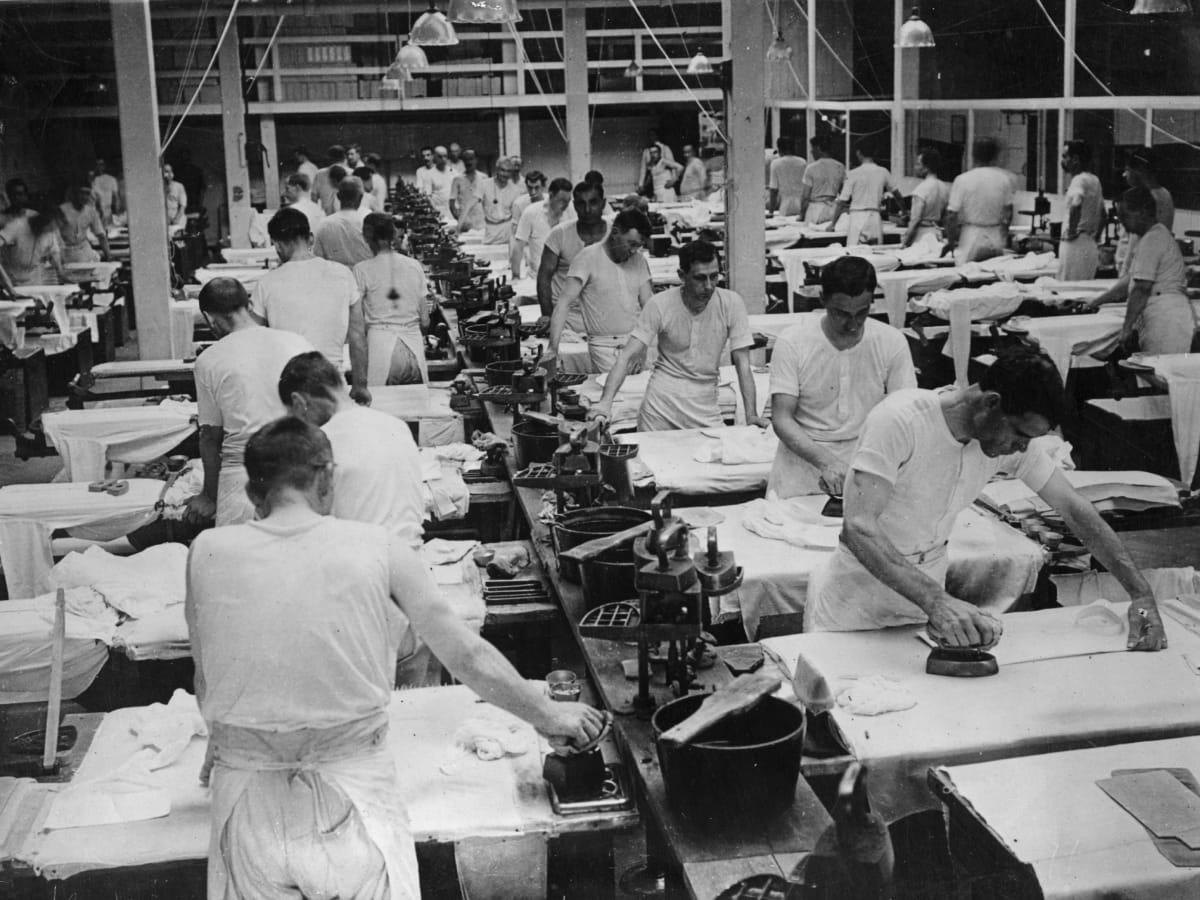
Durable goods have items that don't wear out quickly and can provide utility for a prolonged period. These products can be used repeatedly, unlike nondurable items, which are only useful for one purpose. This means that they will continue to provide the same or greater utility for years to come. A durable car, for example, will last many years.
Nondurable goods can be consumed immediately
Nondurable goods can be consumed right away, in contrast to durable goods which last a long time. In recessions consumers tend not to spend money on durable goods, but instead purchase nondurable products. These items often have low prices, and can be purchased using cash. Nondurable goods include meats, fruits, vegetables and dairy products. Detergent, dish soap, cosmetics are just a few examples.
Nondurable goods generally last less than three years and are therefore the most affordable. They can also be bought frequently, meaning consumers can purchase them regularly without worrying about their future price. Most nondurable goods are also disposable and can be bought only one time, such as packaged food and laundry detergent. However, service goods are tangible and are made to meet consumer demands. Customers plan their purchases based upon how they perceive the product. This can differ depending on its price.
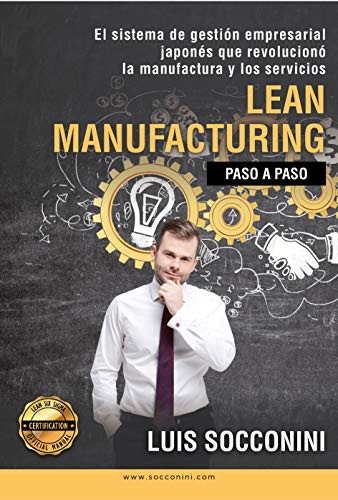
Durable goods are, in contrast, products that are expected provide a steady flow of utility over a time period. These products are also known as consumer durables. They include automobiles. Durables are most commonly purchased during periods when economic growth is occurring, while nondurables will be purchased during economic recession.
Durable goods last more that a year
Durable goods, tangible commodities, are those that last for at minimum one year in normal usage. You can divide them into two groups: consumer durables or producer durables. Consumer durables are household goods like cars, boats, and furniture. Producer durables are machinery, appliances and fine jewelry.
Durable goods are expected last for at least 3 years but may require repair or servicing. Durable goods have been designed so that there is very little chance of breaking during their first few years of usage. With proper care and maintenance, durable goods can last up to 20 years.
In times of economic growth, durable goods demand is often a key indicator. A rise in sales of durable goods may lead to more employment and higher returns on investments. However, a drop in durable goods sales may indicate a decrease of economic activity. This is because consumers use their money to repair and service existing products rather than spending it on new items. This could result in a decline in durable goods, which may cause a recession.
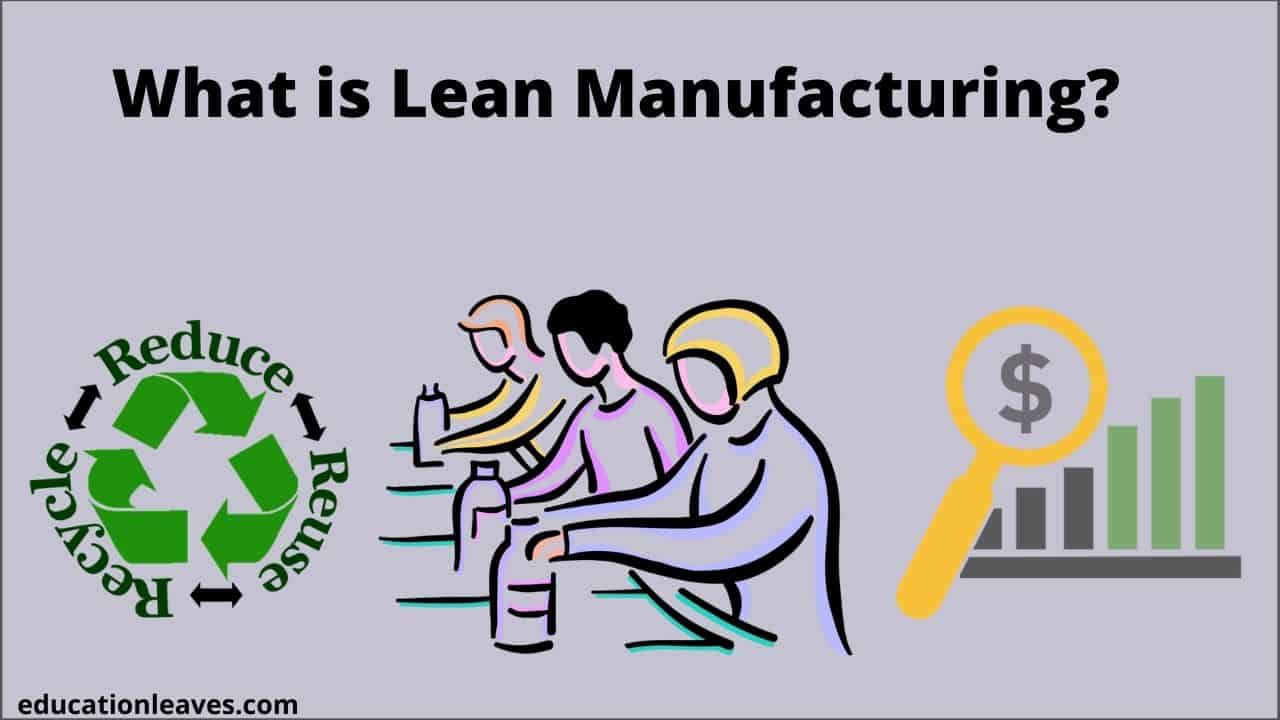
Impact of COVID-19-pandemic pandemics on durable goods
COVID-19 caused widespread illness and has affected consumer spending on durable goods as well. People became more cautious about going to the gym and avoiding social gatherings as a result. People also stopped hailing taxis, which led to a decrease in consumer spending. Instead, people decided to spend more time at home producing and enjoying leisure activities. This in turn reduced consumer spending on restaurants and other services.
The US economy was impacted by the COVID-19 Pandemic in a significant way. In addition to the increased demand for durable goods, the disease also spurred strong fiscal policies that raised household disposable income. This could account for about half of the increase in consumer durable goods spending by 2020.
The COVID-19 Pandemic has impacted individuals, communities, as well as businesses. The impact of the disease upon fast-moving goods has been well covered, but less attention has been given to the effects on durable goods. NielsenIQ BASES just released a new survey showing that over 33% of Americans have made durable goods purchases to combat the disease. Many people's purchasing habits have been affected by the disease, which is a result of more time spent at home with their kids.
FAQ
How can overproduction in manufacturing be reduced?
The key to reducing overproduction lies in developing better ways to manage inventory. This would decrease the time that is spent on inefficient activities like purchasing, storing, or maintaining excess stock. By doing this, we could free up resources for other productive tasks.
This can be done by using a Kanban system. A Kanbanboard is a visual tool that allows you to keep track of the work being done. Kanban systems are where work items travel through a series of states until reaching their final destination. Each state represents a different priority.
To illustrate, work can move from one stage or another when it is complete enough for it to be moved to a new stage. A task that is still in the initial stages of a process will be considered complete until it moves on to the next stage.
This keeps work moving and ensures no work is lost. A Kanban board allows managers to monitor how much work is being completed at any given moment. This information allows managers to adjust their workflow based off real-time data.
Lean manufacturing can also be used to reduce inventory levels. Lean manufacturing works to eliminate waste throughout every stage of the production chain. Anything that does nothing to add value to a product is waste. There are several types of waste that you might encounter:
-
Overproduction
-
Inventory
-
Packaging not required
-
Materials in excess
Manufacturers can increase efficiency and decrease costs by implementing these ideas.
What does it take to run a logistics business?
You need to have a lot of knowledge and skills to manage a successful logistic business. Good communication skills are essential to effectively communicate with your suppliers and clients. You should be able analyse data and draw inferences. You will need to be able handle pressure well and work in stressful situations. To improve efficiency, you must be innovative and creative. You will need strong leadership skills to motivate and direct your team members towards achieving their organizational goals.
It is important to be organized and efficient in order to meet tight deadlines.
What is the responsibility of a logistics manager?
A logistics manager makes sure that all goods are delivered on-time and in good condition. This is achieved by using their knowledge and experience with the products of the company. He/she should make sure that enough stock is on hand to meet the demands.
How can manufacturing prevent production bottlenecks?
You can avoid bottlenecks in production by making sure that everything runs smoothly throughout the production cycle, from the moment you receive an order to the moment the product is shipped.
This includes planning to meet capacity requirements and quality control.
Continuous improvement techniques such Six Sigma can help you achieve this.
Six Sigma is a management system used to improve quality and reduce waste in every aspect of your organization.
It seeks to eliminate variation and create consistency in your work.
What are the responsibilities of a production planner
A production planner ensures all aspects of the project are delivered on time, within budget, and within scope. They make sure that the product and services meet client expectations.
Statistics
- Job #1 is delivering the ordered product according to specifications: color, size, brand, and quantity. (netsuite.com)
- According to a Statista study, U.S. businesses spent $1.63 trillion on logistics in 2019, moving goods from origin to end user through various supply chain network segments. (netsuite.com)
- [54][55] These are the top 50 countries by the total value of manufacturing output in US dollars for its noted year according to World Bank.[56] (en.wikipedia.org)
- (2:04) MTO is a production technique wherein products are customized according to customer specifications, and production only starts after an order is received. (oracle.com)
- Many factories witnessed a 30% increase in output due to the shift to electric motors. (en.wikipedia.org)
External Links
How To
How to use the Just In-Time Production Method
Just-intime (JIT), which is a method to minimize costs and maximize efficiency in business process, is one way. It's a way to ensure that you get the right resources at just the right time. This means that you only pay for what you actually use. Frederick Taylor developed the concept while working as foreman in early 1900s. He saw how overtime was paid to workers for work that was delayed. He concluded that if workers were given enough time before they start work, productivity would increase.
JIT is about planning ahead. You should have all the necessary resources ready to go so that you don’t waste money. Also, you should look at the whole project from start-to-finish and make sure you have the resources necessary to address any issues. You can anticipate problems and have enough equipment and people available to fix them. You won't have to pay more for unnecessary items.
There are several types of JIT techniques:
-
Demand-driven: This type of JIT allows you to order the parts/materials required for your project on a regular basis. This will allow you to track how much material you have left over after using it. It will also allow you to predict how long it takes to produce more.
-
Inventory-based : You can stock the materials you need in advance. This allows you to predict how much you can expect to sell.
-
Project-driven: This method allows you to set aside enough funds for your project. You will be able to purchase the right amount of materials if you know what you need.
-
Resource-based: This is the most common form of JIT. Here you can allocate certain resources based purely on demand. You will, for example, assign more staff to deal with large orders. If there aren't many orders, you will assign fewer people.
-
Cost-based: This is similar to resource-based, except that here you're not just concerned about how many people you have but how much each person costs.
-
Price-based: This approach is very similar to the cost-based method except that you don't look at individual workers costs but the total cost of the company.
-
Material-based: This is very similar to cost-based but instead of looking at total costs of the company you are concerned with how many raw materials you use on an average.
-
Time-based: Another variation of resource-based JIT. Instead of focusing solely on the amount each employee costs, focus on how long it takes for the project to be completed.
-
Quality-based JIT is another variant of resource-based JIT. Instead of thinking about the cost of each employee or the time it takes to produce something, you focus on how good your product quality.
-
Value-based JIT: One of the most recent forms of JIT. In this case, you're not concerned with how well the products perform or whether they meet customer expectations. Instead, you focus on the added value that you provide to your market.
-
Stock-based: This inventory-based approach focuses on how many items are being produced at any one time. It's used when you want to maximize production while minimizing inventory.
-
Just-in-time planning (JIT): This is a combination JIT and supply-chain management. It refers to the process of scheduling the delivery of components as soon as they are ordered. It is essential because it reduces lead-times and increases throughput.