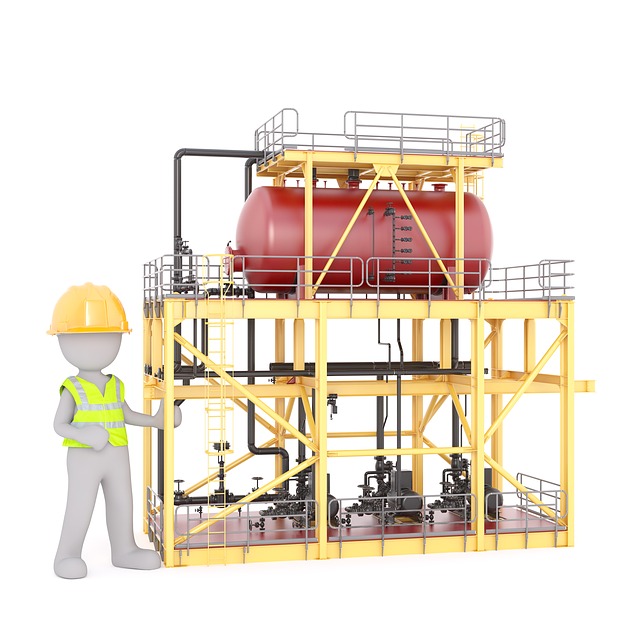
The company's manufacturing director is responsible for overseeing the entire production process. As they are responsible for managing the entire production process, their role is critical. For this job, you must have a great deal of manufacturing experience and be familiar with all new technologies. These technologies include 3D printing and robotics. A director who keeps up with these technologies is an asset to his company. The director's role in the manufacturing industry will change as it evolves. He or she will need to work closely with engineering and operations, as well as placing greater emphasis on quality control in the manufacturing plant.
Salary for a director in manufacturing
A Director of Manufacturing's salary can vary greatly, depending on the region they work in. Director of Manufacturing salaries can range from low to mid-six figures. However, some directors earn considerably more than others. The years of experience and education can have an impact on the salary of a director of manufacturing. These are the factors that will impact how much you can earn in your particular area.
While the salary for a Director In Manufacturing will vary, in general the salary you receive is higher if you have more experience. Salary can be affected depending on where you live and how much it costs to live. While you may earn more if your location is a major city, it's possible to make a living in that area. Always be willing to negotiate for a higher salary, if offered.
A Director of Manufacturing Operations can earn between $181 500 and $66,000 annually. The salary of a Director in Manufacturing Operations can vary greatly and may differ by as much as 8% depending on where you live. Fremont, CA's director for manufacturing operations can earn between $128.493 and $164.500. This is significantly more than the average national salary. However, salaries for Director of Manufacturing Operations vary depending on location, experience, and company.
Education necessary
Director of manufacturing is responsible to manage a manufacturing facility and supervise the production process. This role includes hiring new employees, overseeing quality inspection, collaborating with designers, meeting operations standards, and managing a production facility. A director in manufacturing typically reports directly to the senior management team. This person executes policies and sales initiatives. Candidates should have manufacturing experience and good communication skills. The educational requirements for becoming a director of manufacturing vary from company to company.
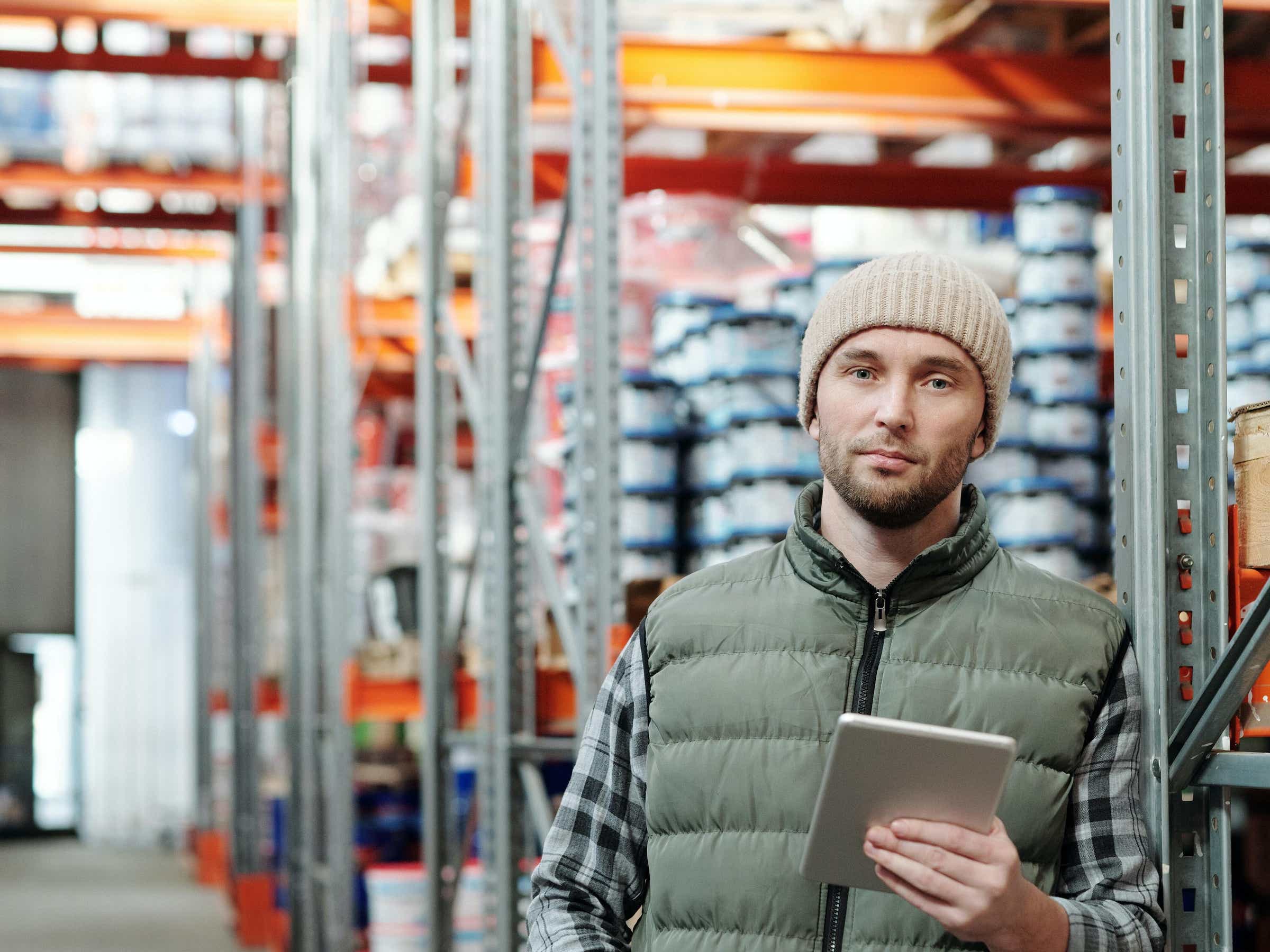
Although a master's degree in engineering does not necessarily make you a director in manufacturing, having a post-secondary education is a great way to increase your knowledge and skill set. This position is well-suited for candidates who are interested in learning about business, management and economics. In the end, you will manage a diverse team of people.
As a director manufacturing, you will closely work with designers and engineers in the product development phase. This stage will see you actively evaluate the feasibility of new processes, and ensure quality standards before committing resources for larger productions. Successful directors are also responsible for overseeing the production process and acting as coaches for their employees. They will mentor them on best practices and risk mitigation. Manufacturing directors are responsible for overseeing all aspects of production and must also have problem-solving skills.
Experience required
For this position, you will need a bachelor's or master's degree in a related field. You also need to have five to ten years of work experience. Generally, manufacturing companies prefer to hire internal employees for this role. The ideal candidate should have a solid understanding of the manufacturing process as well as business objectives. Some employers may request a graduate diploma. Additional training may be required for candidates in their chosen field.
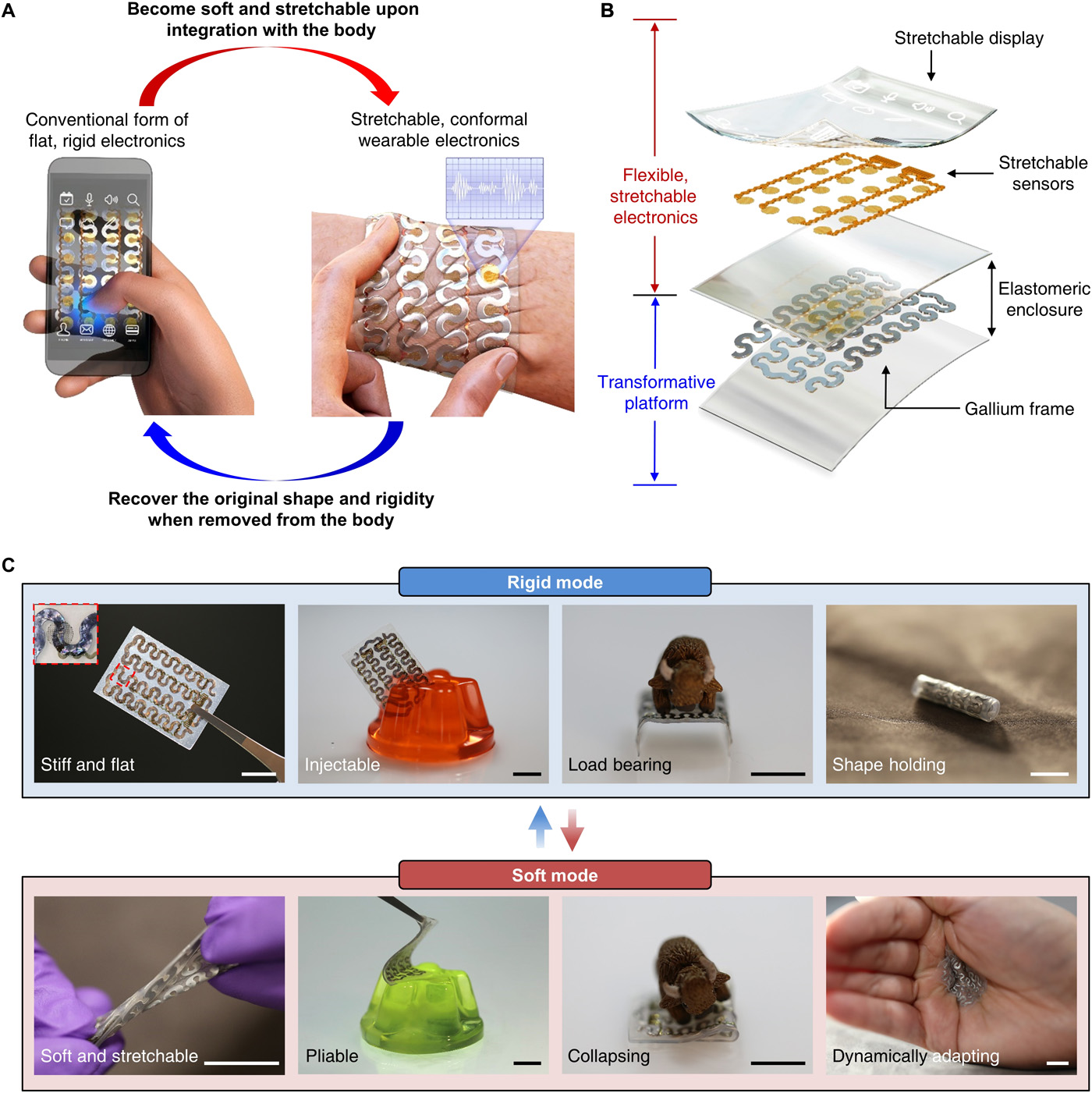
The production process is overseen by a director of manufacturing, which includes engineers, supervisors, workers, and other personnel. They may be responsible for solving problems and developing a solution for them. A director of manufacturing may not only oversee production but also develop and implement quality-control programs. The manufacturing director reports directly to the chief executive of the organization. Experience in manufacturing is essential. Manufacturing management experience can make you a success in this role.
It is important to have experience as a director in manufacturing. Directors must have at the least 10 years relevant experience working in a manufacturing environment. These individuals may have had previous experience as managers or technicians. They should also possess strong communication skills. The director of manufacturing must also be able to understand business strategy. Finally, the director of production must be able interact with other departments within the organization. As such, the director is responsible for overseeing the production process and ensuring that it meets all quality standards.
FAQ
What are the responsibilities of a production planner
A production planner ensures all aspects of the project are delivered on time, within budget, and within scope. They make sure that the product and services meet client expectations.
What are the 4 types manufacturing?
Manufacturing refers to the transformation of raw materials into useful products by using machines and processes. It includes many different activities like designing, building and testing, packaging, shipping and selling, as well as servicing.
Why automate your warehouse?
Modern warehouses are increasingly dependent on automation. E-commerce has brought increased demand for more efficient and quicker delivery times.
Warehouses should be able adapt quickly to new needs. Technology investment is necessary to enable warehouses to respond quickly to changing demands. Automating warehouses has many benefits. These are just a few reasons to invest in automation.
-
Increases throughput/productivity
-
Reduces errors
-
Improves accuracy
-
Boosts safety
-
Eliminates bottlenecks
-
Allows companies to scale more easily
-
It makes workers more efficient
-
Gives you visibility into all that is happening in your warehouse
-
Enhances customer experience
-
Improves employee satisfaction
-
Minimizes downtime and increases uptime
-
You can be sure that high-quality products will arrive on time
-
Eliminates human error
-
Assure compliance with regulations
How can we improve manufacturing efficiency?
The first step is to identify the most important factors affecting production time. We then need to figure out how to improve these variables. If you aren't sure where to begin, think about the factors that have the greatest impact on production time. Once you have identified them, it is time to identify solutions.
Statistics
- According to a Statista study, U.S. businesses spent $1.63 trillion on logistics in 2019, moving goods from origin to end user through various supply chain network segments. (netsuite.com)
- You can multiply the result by 100 to get the total percent of monthly overhead. (investopedia.com)
- [54][55] These are the top 50 countries by the total value of manufacturing output in US dollars for its noted year according to World Bank.[56] (en.wikipedia.org)
- Job #1 is delivering the ordered product according to specifications: color, size, brand, and quantity. (netsuite.com)
- Many factories witnessed a 30% increase in output due to the shift to electric motors. (en.wikipedia.org)
External Links
How To
Six Sigma: How to Use it in Manufacturing
Six Sigma refers to "the application and control of statistical processes (SPC) techniques in order to achieve continuous improvement." It was developed by Motorola's Quality Improvement Department at their plant in Tokyo, Japan, in 1986. Six Sigma's main goal is to improve process quality by standardizing processes and eliminating defects. Many companies have adopted Six Sigma in recent years because they believe that there are no perfect products and services. The main goal of Six Sigma is to reduce variation from the mean value of production. This means that if you take a sample of your product, then measure its performance against the average, you can find out what percentage of the time the process deviates from the norm. If you notice a large deviation, then it is time to fix it.
Understanding the dynamics of variability within your business is the first step in Six Sigma. Once you've understood that, you'll want to identify sources of variation. It is important to identify whether the variations are random or systemic. Random variations happen when people make errors; systematic variations are caused externally. For example, if you're making widgets, and some of them fall off the assembly line, those would be considered random variations. You might notice that your widgets always fall apart at the same place every time you put them together.
Once you identify the problem areas, it is time to create solutions. It might mean changing the way you do business or redesigning it entirely. Once you have implemented the changes, it is important to test them again to ensure they work. If they don’t work, you’ll need to go back and rework the plan.