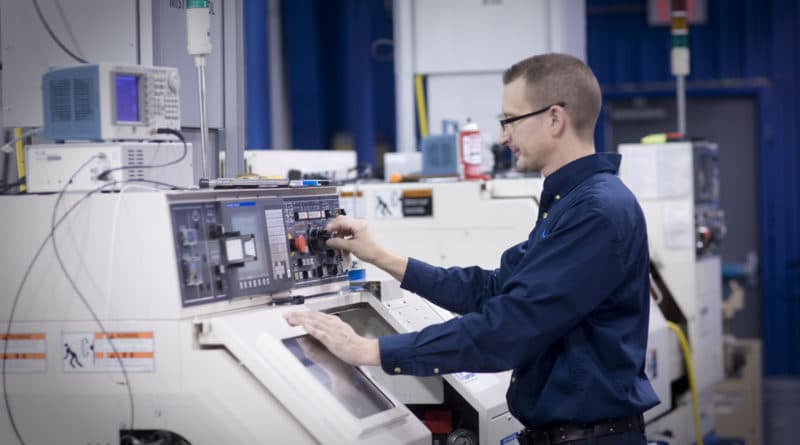
When you want to ensure that your product is profitable, you need to think about the manufacturing cost. You may need to buy wood, adhesives and other materials if your plan is to sell wooden tabletop furnishings. For your products to last, you will need to be able find reliable suppliers of high quality raw materials. If you do not use high quality materials, you could be left with a broken item and lost revenue.
The most effective way to understand manufacturing cost is to break it down into three main categories. Each one of these costs will influence the final product price. One of the most important components in a manufacturing cost is its unit cost. This is the price it takes to produce an item. This number is a good way to begin, but it is not easy to determine.
For determining the most cost effective manufacturing process for your business, it is best to use units-per-hour (or unit per-unit ratio). For example, if you are planning on making 5,000 wooden tables, you can figure out the average cost of making each unit by calculating the number of hours it takes to complete the project.
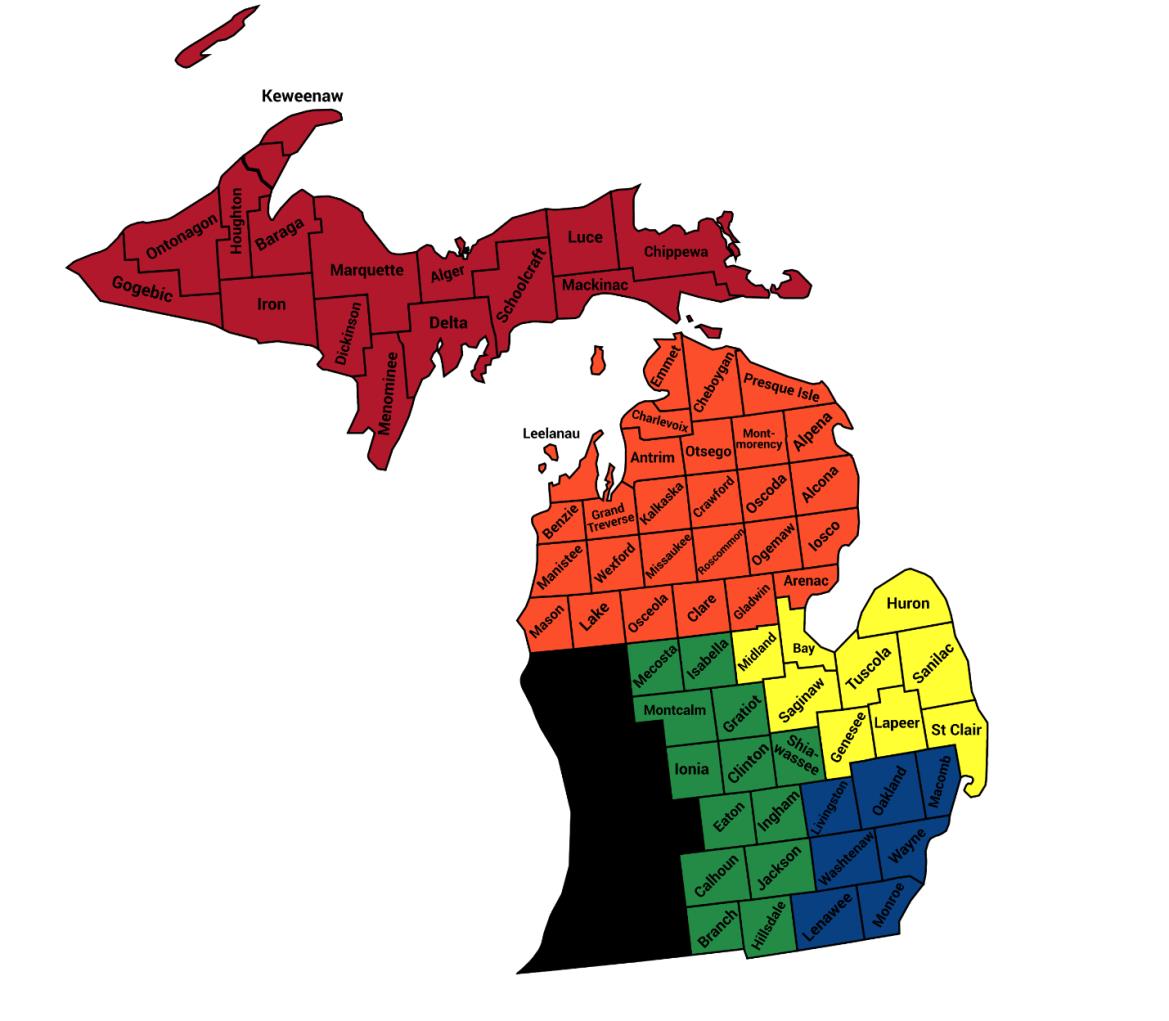
Apart from direct labor and production equipment, budgeting will also be necessary for administrative and other general expenses. These expenses can include advertising costs and office supplies, rent, or sales commissions. To comply with regulatory requirements, you will need to spend significant amounts of money. However, you can minimize the cost of these expenses by using online inventory control software to track production and forecast production.
Direct labor costs include wages paid to factory workers and employees involved in the preparation of goods for manufacturing. They may also include maintenance staff, sanitation personnel, and bookkeepers. In general, the hourly wage for direct labor is around $150.
Indirect costs are a part of manufacturing, and they include costs for utility bills and equipment maintenance. You will need to determine the costs of the preparation and assembly of the materials, as well as the costs to deliver the product to the customer. A manufacturing overhead account is a tool that will allow you calculate the total cost for your operation and give you an estimate of your overhead in the coming fiscal year.
The manufacturing cost of a product should also be considered when calculating its manufacturing cost. The materials used to manufacture a product include thread, wood, and cotton. You should not use low-quality materials. If you are a food producer in certain regions of the globe, you will need to test your products for safety.
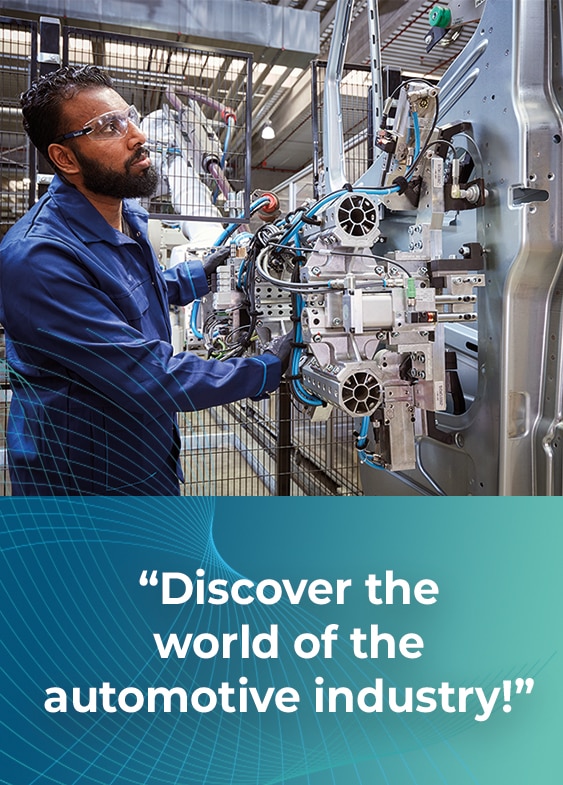
It is important to determine whether you should begin producing new products by knowing how much each unit costs. It's also a smart idea to figure out how much you should be charging for your products, so that your business is more profitable.
FAQ
What is the responsibility for a logistics manager
A logistics manager ensures that all goods are delivered on time and without damage. This is accomplished by using the experience and knowledge gained from working with company products. He/she also needs to ensure adequate stock to meet demand.
What skills is required for a production planner?
A production planner must be organized, flexible, and able multitask to succeed. Communication skills are essential to ensure that you can communicate effectively with clients, colleagues, and customers.
What are the 4 types manufacturing?
Manufacturing is the process of transforming raw materials into useful products using machines and processes. It involves many different activities such as designing, building, testing, packaging, shipping, selling, servicing, etc.
Why automate your factory?
Modern warehousing has seen automation take center stage. E-commerce has increased the demand for quicker delivery times and more efficient processes.
Warehouses have to be flexible to meet changing requirements. They must invest heavily in technology to do this. The benefits of automating warehouses are numerous. Here are some reasons why it's worth investing in automation:
-
Increases throughput/productivity
-
Reduces errors
-
Increases accuracy
-
Safety enhancements
-
Eliminates bottlenecks
-
This allows companies to scale easily
-
It makes workers more efficient
-
Gives you visibility into all that is happening in your warehouse
-
Enhances customer experience
-
Improves employee satisfaction
-
It reduces downtime, and increases uptime
-
Ensures quality products are delivered on time
-
Human error can be eliminated
-
Assure compliance with regulations
Statistics
- According to the United Nations Industrial Development Organization (UNIDO), China is the top manufacturer worldwide by 2019 output, producing 28.7% of the total global manufacturing output, followed by the United States, Japan, Germany, and India.[52][53] (en.wikipedia.org)
- [54][55] These are the top 50 countries by the total value of manufacturing output in US dollars for its noted year according to World Bank.[56] (en.wikipedia.org)
- You can multiply the result by 100 to get the total percent of monthly overhead. (investopedia.com)
- It's estimated that 10.8% of the U.S. GDP in 2020 was contributed to manufacturing. (investopedia.com)
- According to a Statista study, U.S. businesses spent $1.63 trillion on logistics in 2019, moving goods from origin to end user through various supply chain network segments. (netsuite.com)
External Links
How To
How to Use Just-In-Time Production
Just-in-time (JIT) is a method that is used to reduce costs and maximize efficiency in business processes. It allows you to get the right amount resources at the right time. This means you only pay what you use. The term was first coined by Frederick Taylor, who developed his theory while working as a foreman in the early 1900s. Taylor observed that overtime was paid to workers if they were late in working. He realized that workers should have enough time to complete their jobs before they begin work. This would help increase productivity.
The idea behind JIT is that you should plan ahead and have everything ready so you don't waste money. Look at your entire project, from start to end. Make sure you have enough resources in place to deal with any unexpected problems. You will have the resources and people to solve any problems you anticipate. This will prevent you from spending extra money on unnecessary things.
There are many types of JIT methods.
-
Demand-driven: This is a type of JIT where you order the parts/materials needed for your project regularly. This will allow for you to track the material that you have left after using it. It will also allow you to predict how long it takes to produce more.
-
Inventory-based: This type allows you to stock the materials needed for your projects ahead of time. This allows one to predict how much they will sell.
-
Project-driven: This method allows you to set aside enough funds for your project. You will be able to purchase the right amount of materials if you know what you need.
-
Resource-based: This is the most common form of JIT. You allocate resources based on the demand. If you have many orders, you will assign more people to manage them. If there aren't many orders, you will assign fewer people.
-
Cost-based: This approach is very similar to resource-based. However, you don't just care about the number of people you have; you also need to consider how much each person will cost.
-
Price-based pricing: This is similar in concept to cost-based but instead you look at how much each worker costs, it looks at the overall company's price.
-
Material-based: This is quite similar to cost-based, but instead of looking at the total cost of the company, you're concerned with how much raw materials you spend on average.
-
Time-based: Another variation of resource-based JIT. Instead of worrying about how much each worker costs, you can focus on how long the project takes.
-
Quality-based JIT is another variant of resource-based JIT. Instead of thinking about the cost of each employee or the time it takes to produce something, you focus on how good your product quality.
-
Value-based JIT : This is the newest type of JIT. In this case, you're not concerned with how well the products perform or whether they meet customer expectations. Instead, you are focused on adding value to the marketplace.
-
Stock-based: This inventory-based approach focuses on how many items are being produced at any one time. This is used to increase production and minimize inventory.
-
Just-intime (JIT), planning is a combination JIT management and supply chain management. It is the process that schedules the delivery of components within a short time of their order. It's important because it reduces lead times and increases throughput.