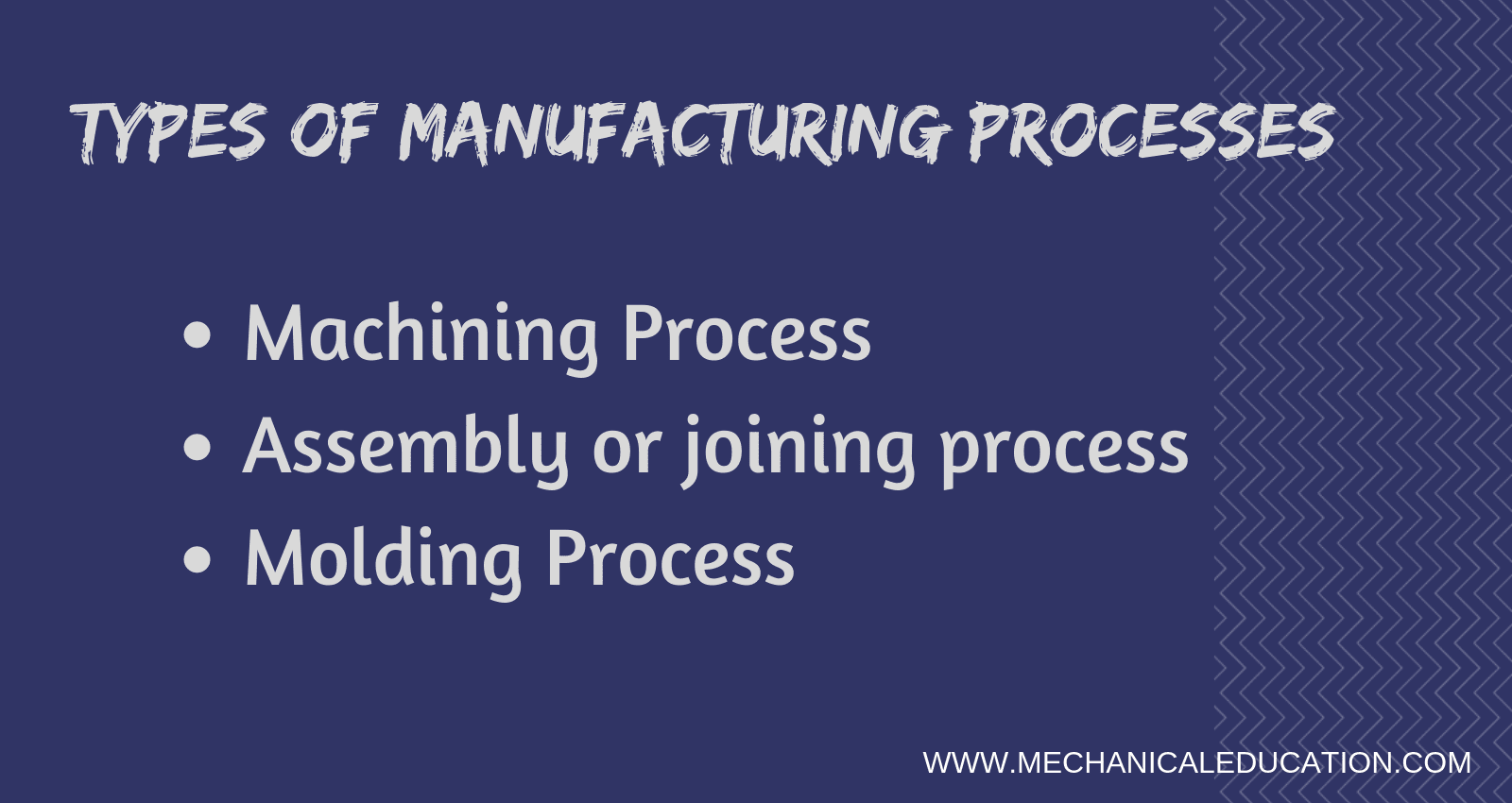
A sustainable supply chain is not easy to establish. Transport logistics and packaging can lead to waste and greenhouse gas emissions. By investing in compact packaging, you can reduce the shipment size and decrease costs. It can also reduce waste, and preserve the bottom line.
Supply chain sustainability requires a combination of processes, policies, and technology. Many companies are seeking ways to make their supply chains more sustainable, improve performance and use sustainable materials. To make their suppliers more sustainable, some companies offer training.
Both the company as well as the community can benefit from a sustainable supply chain. It is possible for companies to choose suppliers that are focused on recycled and renewable materials. This will allow them to reduce the number and quality of their offerings. They can choose suppliers that use sustainable materials. Additionally, they can adopt a code for conduct that emphasizes the integrity of their suppliers as well as their operations.
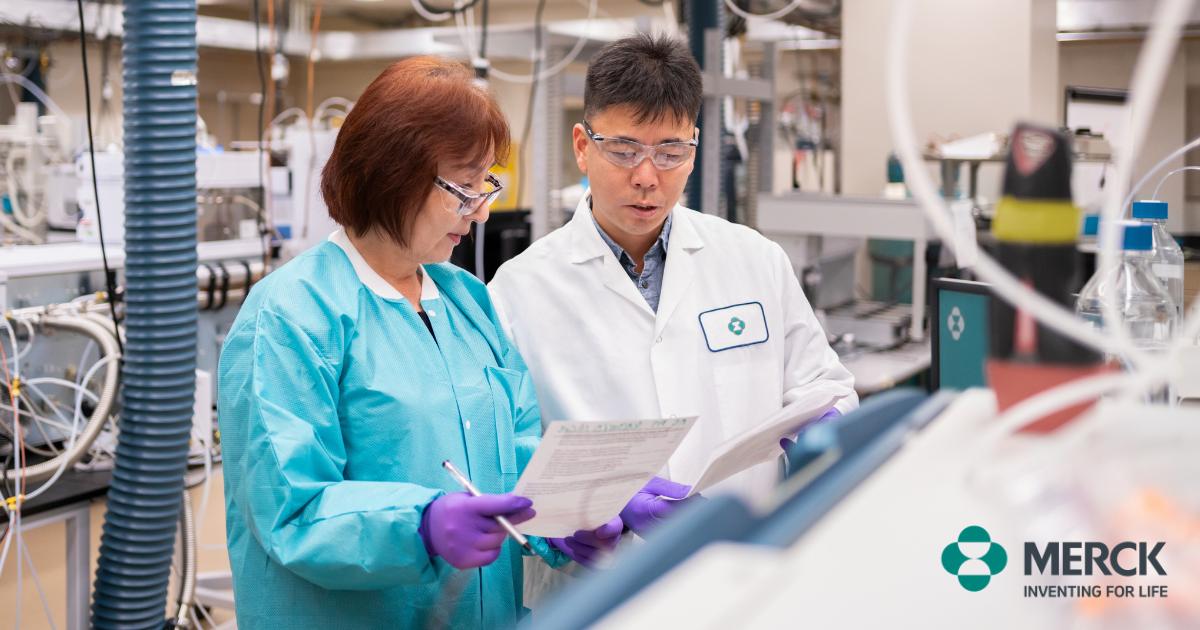
Remarketing used products can help companies reduce their waste. They can also recycle the water that they use. They can also set clear goals and involve all stakeholders in order to make a difference. They can also establish strong governance, which can help ensure that they are meeting their sustainability goals.
Many companies have taken steps toward reducing the carbon emissions of their facilities, purchased energy and transport partners. However, most companies have yet to tackle the indirect emissions that arise from their supply chain partners. These include transportation and distribution partners. Carbon Disclosure Project has reported on some progress made by companies in reducing greenhouse emissions. However, more work remains.
Companies should establish measurable goals and engage all stakeholders to improve their supply chain sustainability. To ensure they meet their goals, they should engage with their customers and suppliers. They should use data to make their decisions and should outline a clear course of action.
Companies can also enhance their supply chain resilience and establish robust risk management processes. They can also diversify or nearshoot their suppliers. Bed Bath & Beyond, for example, has eight brands it owns and has increased its control over the supply chain. It claims at least half its wood and cotton are sustainably sourced. It has also identified key locations for warehousing.
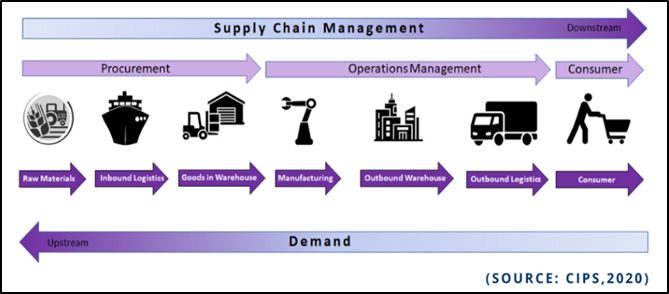
Companies need to be aware of the environmental impacts packaging can have on the environment. Some innovations can allow products to be recycled or reused, and they can also reduce the size of shipments and the number of trips they make. Also, companies have the option to invest in smaller packaging and upgrade their refrigeration equipment. These innovations can help reduce carbon emissions, and have long-lasting benefits.
Many companies are adopting circular economy models. They are creating products that can be recycled or reused, and they are also focusing on limited resources. This will help to reduce greenhouse gas emissions, and also reduce waste.
FAQ
How can manufacturing reduce production bottlenecks?
Avoiding production bottlenecks is as simple as keeping all processes running smoothly, from the time an order is received until the product ships.
This includes both quality control and capacity planning.
Continuous improvement techniques like Six Sigma are the best way to achieve this.
Six Sigma is a management system used to improve quality and reduce waste in every aspect of your organization.
It focuses on eliminating variation and creating consistency in your work.
What is the role and responsibility of a Production Planner?
Production planners make sure that every aspect of the project is delivered on-time, within budget, and within schedule. They make sure that the product and services meet client expectations.
What are the responsibilities for a manufacturing manager
A manufacturing manager must ensure that all manufacturing processes are efficient and effective. They should also be aware and responsive to any company problems.
They should also be able communicate with other departments, such as sales or marketing.
They should also be aware of the latest trends in their industry and be able to use this information to help improve productivity and efficiency.
What does it take for a logistics enterprise to succeed?
You need to have a lot of knowledge and skills to manage a successful logistic business. You must have good communication skills to interact effectively with your clients and suppliers. You should be able analyse data and draw inferences. You must be able to work well under pressure and handle stressful situations. In order to innovate and create new ways to improve efficiency, creativity is essential. You need to have strong leadership qualities to motivate team members and direct them towards achieving organizational goals.
You should also be organized and efficient to meet tight deadlines.
What are the 7 Rs of logistics?
The acronym 7R's of Logistic is an acronym that stands for seven fundamental principles of logistics management. It was developed and published by the International Association of Business Logisticians in 2004 as part of the "Seven Principles of Logistics Management".
The acronym is made up of the following letters:
-
Responsible – ensure that all actions are legal and don't cause harm to anyone else.
-
Reliable - You can have confidence that you will fulfill your promises.
-
Be responsible - Use resources efficiently and avoid wasting them.
-
Realistic - Consider all aspects of operations, including environmental impact and cost effectiveness.
-
Respectful - Treat people fairly and equitably
-
Resourceful - look for opportunities to save money and increase productivity.
-
Recognizable: Provide customers with value-added service
What are the 4 types manufacturing?
Manufacturing is the process by which raw materials are transformed into useful products through machines and processes. Manufacturing involves many activities, including designing, building, testing and packaging, shipping, selling, service, and so on.
Statistics
- [54][55] These are the top 50 countries by the total value of manufacturing output in US dollars for its noted year according to World Bank.[56] (en.wikipedia.org)
- According to a Statista study, U.S. businesses spent $1.63 trillion on logistics in 2019, moving goods from origin to end user through various supply chain network segments. (netsuite.com)
- It's estimated that 10.8% of the U.S. GDP in 2020 was contributed to manufacturing. (investopedia.com)
- In 2021, an estimated 12.1 million Americans work in the manufacturing sector.6 (investopedia.com)
- You can multiply the result by 100 to get the total percent of monthly overhead. (investopedia.com)
External Links
How To
How to use 5S to increase Productivity in Manufacturing
5S stands for "Sort", "Set In Order", "Standardize", "Separate" and "Store". The 5S methodology was developed at Toyota Motor Corporation in 1954. It improves the work environment and helps companies to achieve greater efficiency.
This method aims to standardize production processes so that they are repeatable, measurable and predictable. This means that daily tasks such as cleaning and sorting, storage, packing, labeling, and packaging are possible. Because workers know what they can expect, this helps them perform their jobs more efficiently.
Implementing 5S requires five steps. These are Sort, Set In Order, Standardize. Separate. And Store. Each step requires a different action to increase efficiency. If you sort items, it makes them easier to find later. You arrange items by placing them in an order. Then, after you separate your inventory into groups, you store those groups in containers that are easy to access. Finally, when you label your containers, you ensure everything is labeled correctly.
Employees need to reflect on how they do their jobs. Employees must understand why they do certain tasks and decide if there's another way to accomplish them without relying on the old ways of doing things. They will need to develop new skills and techniques in order for the 5S system to be implemented.
In addition to increasing efficiency, the 5S method also improves morale and teamwork among employees. They are more motivated to achieve higher efficiency levels as they start to see improvement.