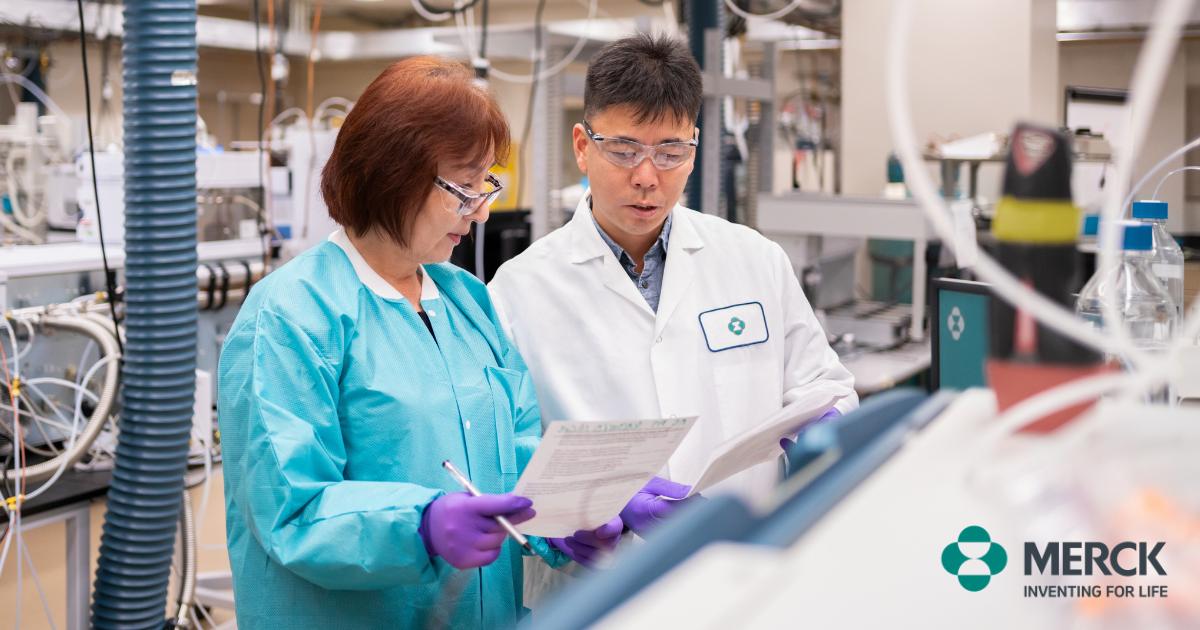
Columbus, Ohio is central Ohio's largest city has a wide range of activities and attractions. Columbus is a destination that attracts both locals as well as tourists. The city boasts four top-class golf courses, an internationally acclaimed park system and plenty of entertainment and arts. It is also ranked among America's most charming metropolitan areas. It also has a lot of high-tech firms that make it stand out on the corporate radar. The Columbus Tech Council website has a list listing all the local tech companies. The council offers everything tech-related, including networking opportunities and job opportunities. Whether you're in the market for a career move, or just looking for a change of scenery, the Columbus tech scene is sure to please. Columbus is home to both entry-level and seasoned executives. Many employers are looking for you, including JP Morgan, Limited Brands, Time Warner, and JP Morgan. Other than the obvious perks, Columbus has many notable museums and art galleries. These include the Franklin Park Conservatory, Columbus Museum of Art, and the Columbus Museum of Art. There are many theatres and casinos. Moreover, the city is home to one of the largest public transportation systems in the country.
FAQ
What are the 7 Rs of logistics management?
The acronym 7R's of Logistic is an acronym that stands for seven fundamental principles of logistics management. It was created by the International Association of Business Logisticians and published in 2004 under its "Seven Principles of Logistics Management".
The following letters make up the acronym:
-
Responsive - ensure all actions are legal and not harmful to others.
-
Reliable – have faith in your ability and capability to keep promises.
-
Reasonable - make sure you use your resources well and don't waste them.
-
Realistic – consider all aspects of operations, from cost-effectiveness to environmental impact.
-
Respectful - show respect and treat others fairly and fairly
-
Be resourceful: Look for opportunities to save money or increase productivity.
-
Recognizable provides value-added products and services to customers
What is the responsibility of a logistics manager?
Logistics managers make sure all goods are delivered on schedule and without damage. This is done through his/her expertise and knowledge about the company's product range. He/she should also ensure enough stock is available to meet demand.
Is it necessary to be familiar with Manufacturing Processes before we learn about Logistics.
No. You don't have to know about manufacturing processes before learning about logistics. But, being familiar with manufacturing processes will give you a better understanding about how logistics works.
What is the role of a production manager?
A production planner ensures all aspects of the project are delivered on time, within budget, and within scope. They ensure that the product or service is of high quality and meets client requirements.
What are the logistics products?
Logistics refers to the movement of goods from one place to another.
They encompass all aspects transport, including packaging and loading, transporting, storage, unloading.
Logisticians ensure that the product is delivered to the correct place, at the right time, and under safe conditions. Logisticians assist companies in managing their supply chains by providing information such as demand forecasts, stock levels and production schedules.
They can also track shipments in transit and monitor quality standards.
What is the job of a manufacturer manager?
Manufacturing managers must ensure that manufacturing processes are efficient, effective, and cost-effective. They must also be alert to any potential problems and take appropriate action.
They should also be able and comfortable communicating with other departments like sales and marketing.
They should be informed about industry trends and be able make use of this information to improve their productivity and efficiency.
How can manufacturing efficiency be improved?
The first step is to determine the key factors that impact production time. We must then find ways that we can improve these factors. You can start by identifying the most important factors that impact production time. Once you've identified them all, find solutions to each one.
Statistics
- In the United States, for example, manufacturing makes up 15% of the economic output. (twi-global.com)
- You can multiply the result by 100 to get the total percent of monthly overhead. (investopedia.com)
- [54][55] These are the top 50 countries by the total value of manufacturing output in US dollars for its noted year according to World Bank.[56] (en.wikipedia.org)
- In 2021, an estimated 12.1 million Americans work in the manufacturing sector.6 (investopedia.com)
- It's estimated that 10.8% of the U.S. GDP in 2020 was contributed to manufacturing. (investopedia.com)
External Links
How To
Six Sigma and Manufacturing
Six Sigma refers to "the application and control of statistical processes (SPC) techniques in order to achieve continuous improvement." It was developed by Motorola's Quality Improvement Department at their plant in Tokyo, Japan, in 1986. Six Sigma's basic concept is to improve quality and eliminate defects through standardization. Many companies have adopted Six Sigma in recent years because they believe that there are no perfect products and services. Six Sigma aims to reduce variation in the production's mean value. You can calculate the percentage of deviation from the norm by taking a sample of your product and comparing it to the average. If this deviation is too big, you know something needs fixing.
Understanding the dynamics of variability within your business is the first step in Six Sigma. Once you understand that, it is time to identify the sources of variation. You'll also want to determine whether these variations are random or systematic. Random variations are caused by human errors. Systematic variations can be caused by outside factors. If you make widgets and some of them end up on the assembly line, then those are considered random variations. You might notice that your widgets always fall apart at the same place every time you put them together.
After identifying the problem areas, you will need to devise solutions. It might mean changing the way you do business or redesigning it entirely. Once you have implemented the changes, it is important to test them again to ensure they work. If they fail, you can go back to the drawing board to come up with a different plan.