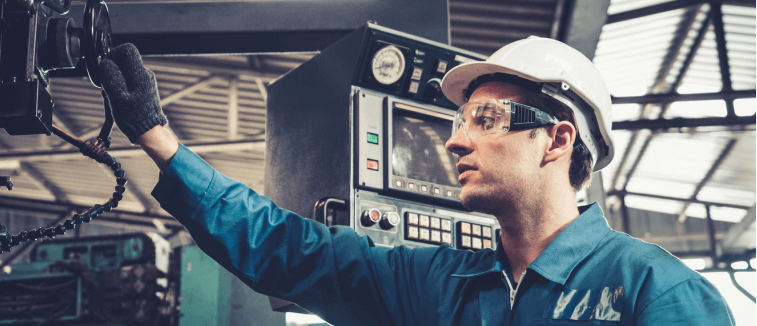
Integrated supply chain management (ISCM) is a process that allows companies to monitor and optimize their supply chain performance. It results in a more responsive and efficient production network. The more streamlined and responsive your supply chain is, the more efficient your operations will be. Integrated supply chain management is a great way to increase your profits, and decrease waste. This will ensure that your products are more reliable, of higher quality, and cost-effective to produce.
Integrated supply chain management is a great way to increase your order reliability. Your production schedule can be more responsive, inventory levels more accurate, and your delivery dates more flexible. Integrated supply chains also increase risk management. This can reduce greenhouse gas emissions. This helps you reach your environmental goals.
Drafting a contract with preferred vendors is the first step to integration. These agreements must be tailored to the needs of your company. It should detail your production schedule, what materials you need, and the associated costs. Your preferred suppliers should be able to show you how their services can benefit your business. You may also find lower prices by purchasing a greater number of goods and services.
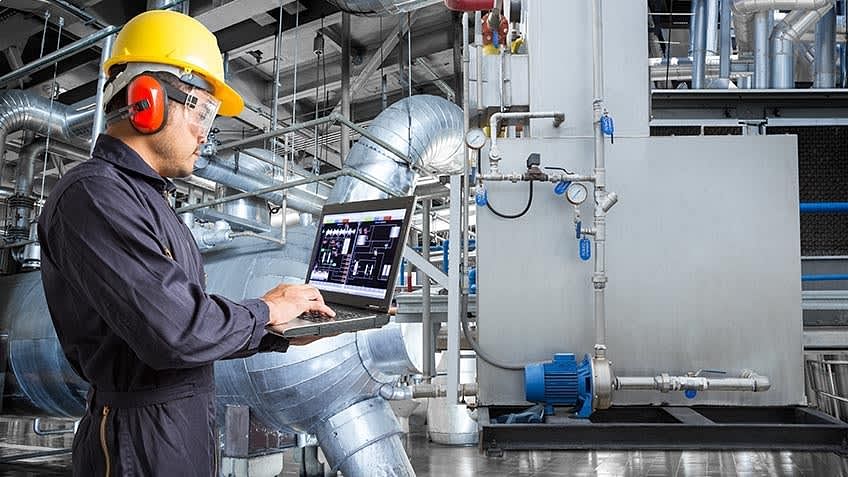
Having a solid understanding of your connections, and how they affect your business, is an important component of integrated supply chain management. This will allow you to avoid costly mistakes and identify potential opportunities for improving performance. You should also have a comprehensive end-to-end plan to meet your needs. This plan should be flexible enough for any production differences. This will help avoid delays.
Just-in time distribution is an example of an integrated supply system. This strategy can reduce operational costs and warehouse space requirements. This strategy can also help with forecasting. It is essential to use an integrated supply network in order to reduce greenhouse gas emissions. Reduce your use of large, fixed assets to achieve this.
Vertical integration means that all necessary elements are present for a particular product. This includes a manufacturer, a vendor, and a supplier. This could result in a higher share of profits for the manufacturer. You might also decide to purchase a widget manufacturer or a firm that manufactures widgets. This can help you control your competitor's business, and allow you to set a fair price on widgets.
Container management strategies are another example of an integrated supply chains. This allows you to view inventory levels and make adjustments to your container pull strategies as needed. You can also make changes to the production schedule right away.
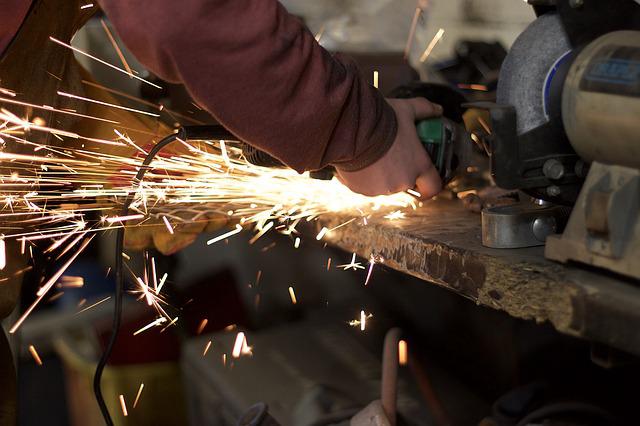
A supply chain management strategy that is clearly defined will make it more effective. Integrated supply chains aim to improve performance and provide customers with the best possible products. An integrated supply system can help reduce the amount plastic and other waste that is produced during the manufacturing process. This can improve your profit margins as well as reduce greenhouse gas emissions.
FAQ
What do you mean by warehouse?
Warehouses and storage facilities are where goods are kept before being sold. It can be an indoor space or an outdoor area. It could be one or both.
What are the 7 Rs of logistics.
The acronym 7R's of Logistic is an acronym that stands for seven fundamental principles of logistics management. It was developed by the International Association of Business Logisticians (IABL) and published in 2004 as part of its "Seven Principles of Logistics Management" series.
The following letters form the acronym:
-
Responsible – ensure that all actions are legal and don't cause harm to anyone else.
-
Reliable - Have confidence in your ability to fulfill all of your commitments.
-
Be responsible - Use resources efficiently and avoid wasting them.
-
Realistic – Consider all aspects, including cost-effectiveness as well as environmental impact.
-
Respectful: Treat others with fairness and equity
-
Reliable - Find ways to save money and increase your productivity.
-
Recognizable: Provide customers with value-added service
Is automation necessary in manufacturing?
Automating is not just important for manufacturers, but also for service providers. It allows them provide faster and more efficient services. It reduces human errors and improves productivity, which in turn helps them lower their costs.
What skills does a production planner need?
Being a production planner is not easy. You need to be organized and flexible. Also, you must be able and willing to communicate with clients and coworkers.
What are the four types of manufacturing?
Manufacturing refers the process of turning raw materials into useful products with machines and processes. It involves many different activities such as designing, building, testing, packaging, shipping, selling, servicing, etc.
What is production management?
Production Planning involves developing a plan for all aspects of the production, including scheduling, budgeting, casting, crew, location, equipment, props, etc. This document aims to ensure that everything is planned and ready when you are ready to shoot. This document should include information about how to achieve the best results on-set. This includes shooting schedules, locations, cast lists, crew details, and equipment requirements.
The first step is to decide what you want. You may have decided where to shoot or even specific locations you want to use. Once you have determined your scenes and locations, it is time to start figuring out the elements that you will need for each scene. If you decide you need a car and don't know what model to choose, this could be an example. To narrow your options, you can search online for available models.
After you have selected the car you want, you can begin to think about additional features. What about additional seating? Or maybe you just need someone to push the car around. Perhaps you would like to change the interior colour from black to white. These questions can help you decide the right look for your car. You can also think about the type of shots you want to get. What type of shots will you choose? Maybe you want to show the engine and the steering wheel. These factors will help you determine which car style you want to film.
Once you have all the information, you are ready to create a plan. A schedule will tell you when you need to start shooting and when you need to finish. Every day will have a time for you to arrive at the location, leave when you are leaving and return home when you are done. It will help everyone know exactly what they have to do and when. You can also make sure to book extra staff in advance if you have to hire them. It is not worth hiring someone who won’t show up because you didn’t tell him.
Your schedule will also have to be adjusted to reflect the number of days required to film. Some projects only take one or two days, while others may last weeks. When you are creating your schedule, you should always keep in mind whether you need more than one shot per day or not. Shooting multiple takes over the same location will increase costs and take longer to complete. It's better to be safe than sorry and shoot less takes if you're not certain whether you need more takes.
Budgeting is another important aspect of production planning. As it will allow you and your team to work within your financial means, setting a realistic budget is crucial. If you have to reduce your budget due to unexpected circumstances, you can always lower it later. It is important to not overestimate how much you will spend. If you underestimate the cost of something, you will have less money left after paying for other items.
Production planning is a very detailed process, but once you understand how everything works together, it becomes easier to plan future projects.
Statistics
- Job #1 is delivering the ordered product according to specifications: color, size, brand, and quantity. (netsuite.com)
- According to the United Nations Industrial Development Organization (UNIDO), China is the top manufacturer worldwide by 2019 output, producing 28.7% of the total global manufacturing output, followed by the United States, Japan, Germany, and India.[52][53] (en.wikipedia.org)
- [54][55] These are the top 50 countries by the total value of manufacturing output in US dollars for its noted year according to World Bank.[56] (en.wikipedia.org)
- Many factories witnessed a 30% increase in output due to the shift to electric motors. (en.wikipedia.org)
- You can multiply the result by 100 to get the total percent of monthly overhead. (investopedia.com)
External Links
How To
Six Sigma in Manufacturing:
Six Sigma refers to "the application and control of statistical processes (SPC) techniques in order to achieve continuous improvement." Motorola's Quality Improvement Department created Six Sigma at their Tokyo plant, Japan in 1986. The basic idea behind Six Sigma is to improve quality by improving processes through standardization and eliminating defects. Many companies have adopted this method in recent years. They believe there is no such thing a perfect product or service. Six Sigma seeks to reduce variation between the mean production value. You can calculate the percentage of deviation from the norm by taking a sample of your product and comparing it to the average. If you notice a large deviation, then it is time to fix it.
Understanding the nature of variability in your business is the first step to Six Sigma. Once you have a good understanding of the basics, you can identify potential sources of variation. Also, you will need to identify the sources of variation. Random variations happen when people make errors; systematic variations are caused externally. Random variations would include, for example, the failure of some widgets to fall from the assembly line. But if you notice that every widget you make falls apart at the exact same place each time, this would indicate that there is a problem.
Once you've identified the problem areas you need to find solutions. That solution might involve changing the way you do things or redesigning the process altogether. After implementing the new changes, you should test them again to see if they worked. If they fail, you can go back to the drawing board to come up with a different plan.