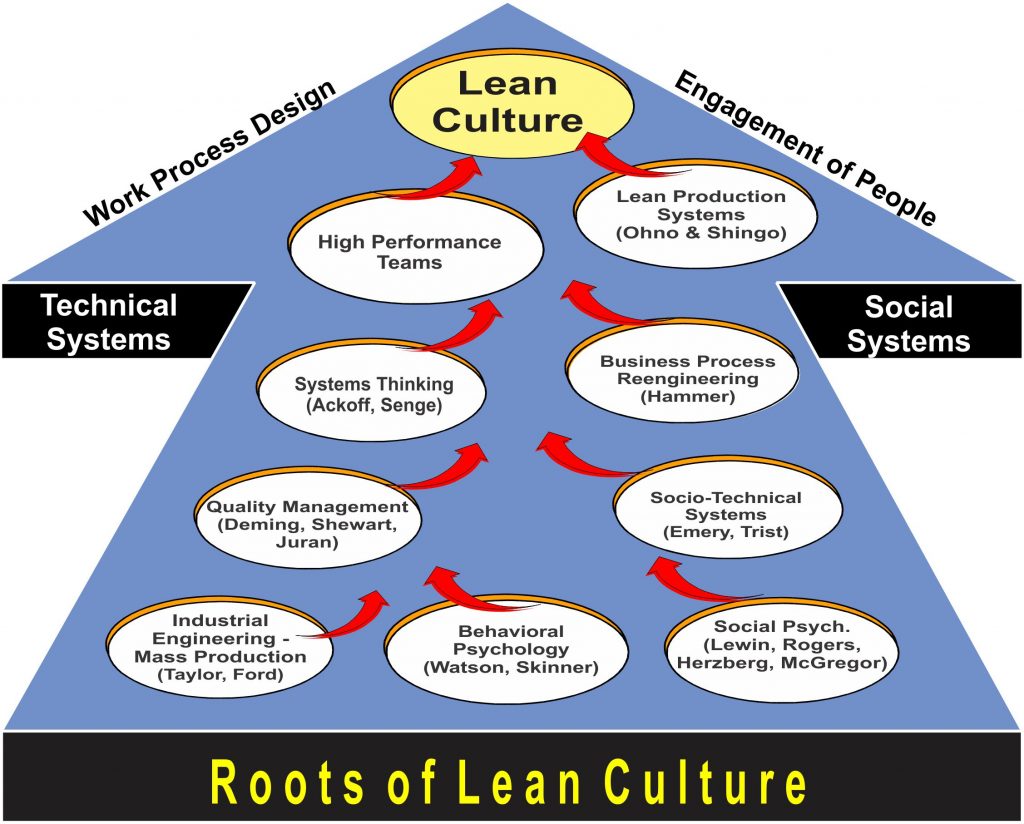
The employment industry provides a variety of jobs to both individuals and businesses. It is expected that the employment industry will continue to grow because many employers prefer to use external agencies to screen potential employees. Many of these agencies operate online, which allows them to lower their administrative costs as well as staff. They are also vulnerable to competition from job postings found on employer Web pages and job-matching websites run by educational institutions and professional associations.
Jobs in the employment services industry
The employment services industry is made up of a variety of occupations. These professionals are specialized in different areas, such as recruiting, placement, and executive search. They also provide temporary staff for clients. These professionals are also able to provide human resources services. Companies located in different parts the world dominate the industry of employment services.
This industry employs millions, with a wide range of education, experience, as well as skills. There are many occupations, from secretary to computer systems analyst and general laborer to nurse. Some jobs in this industry are permanent such as marketing representatives, employment interviewers, and office managers.
Labor market
The labor market is where demand and supply of jobs meet. Employers pay employees for their services. An employer is any individual or organization that seeks a worker. A worker and an employer can be thought of as sellers and buyers.
There are many federal agencies that collect information on the labor markets. For example, the Bureau of Labor Statistics collects and analyses data on unemployment, wages, and employment. It also collects and analyses data on industrial relations, occupational safety, and family expenditure. These data can aid economists in understanding trends in the labour market.
Industry size
The number workers employed in an employment industry determines the industry's size. There are approximately 6.1 million employers in the United States. The largest employers are large companies. Small businesses employ fewer people. According to the U.S. Census Bureau 99.7% percent of total businesses are smaller than 500 employees. While smaller industries may not have large numbers of employees, they could still create jobs.
Industry: Recession's Impact
Employment will decline when the economy goes into recession. In turn, unemployment rates will rise. Also, the duration of unemployment will rise. Each sector of the employment industry will suffer a loss in jobs, but this loss will be different in scale. Each sector lost jobs in the Great Recession. But, the scale of the job losses was different for different sectors.
The resulting reductions in payroll will be reflected in the premium. Premiums will increase by 1% in cases of mild recession. In the case of the Severe recession, the increase will be larger. The decrease in payrolls for Goods & Services is about half as large as that of other industries. The result is that premiums for Goods & Services are expected to rise.
Impact of COVID-19 (coronavirus pandemic) on the industry
Industries that have a high proportion of older workers were most affected by the COVID-19 (coronavirus epidemic) on the employment industry. Professional and business service were the most affected, followed by social assistance and health care. Younger workers suffered more job losses, but not in a significant way. The likelihood of younger workers working in more face-to–face industries was higher.
Both high- and low-paying industries were affected by the pandemic. While most workers lost their jobs because of the virus, the number of people in these sectors was smaller than in other sectors. Many information and management workers were able to work remotely, which allowed them to recover the majority of their jobs. The most significant impact on the employment sector was in the higher-paying areas. The number of workers in these sectors decreased by 15% in the second quarter 2019 compared to the same period last year.
FAQ
What is the best way to learn about manufacturing?
Practical experience is the best way of learning about manufacturing. But if that is not possible you can always read books and watch educational videos.
What does manufacturing industry mean?
Manufacturing Industries are those businesses that make products for sale. These products are sold to consumers. This is accomplished by using a variety of processes, including production, distribution and retailing. They produce goods from raw materials by using machines and other machinery. This includes all types if manufactured goods.
What are the goods of logistics?
Logistics involves the transportation of goods from point A and point B.
They encompass all aspects transport, including packaging and loading, transporting, storage, unloading.
Logisticians ensure the product reaches its destination in the most efficient manner. They assist companies with their supply chain efficiency through information on demand forecasts. Stock levels, production times, and availability.
They coordinate with vendors and suppliers, keep track of shipments, monitor quality standards and perform inventory and order replenishment.
Statistics
- In 2021, an estimated 12.1 million Americans work in the manufacturing sector.6 (investopedia.com)
- Job #1 is delivering the ordered product according to specifications: color, size, brand, and quantity. (netsuite.com)
- (2:04) MTO is a production technique wherein products are customized according to customer specifications, and production only starts after an order is received. (oracle.com)
- According to a Statista study, U.S. businesses spent $1.63 trillion on logistics in 2019, moving goods from origin to end user through various supply chain network segments. (netsuite.com)
- [54][55] These are the top 50 countries by the total value of manufacturing output in US dollars for its noted year according to World Bank.[56] (en.wikipedia.org)
External Links
How To
How to Use the Just In Time Method in Production
Just-in-time is a way to cut costs and increase efficiency in business processes. It's a way to ensure that you get the right resources at just the right time. This means that your only pay for the resources you actually use. Frederick Taylor was the first to coin this term. He developed it while working as a foreman during the early 1900s. He saw how overtime was paid to workers for work that was delayed. He concluded that if workers were given enough time before they start work, productivity would increase.
JIT teaches you to plan ahead and prepare everything so you don’t waste time. Also, you should look at the whole project from start-to-finish and make sure you have the resources necessary to address any issues. If you anticipate that there might be problems, you'll have enough people and equipment to fix them. This will ensure that you don't spend more money on things that aren't necessary.
There are many JIT methods.
-
Demand-driven: This type of JIT allows you to order the parts/materials required for your project on a regular basis. This will let you track the amount of material left over after you've used it. You'll also be able to estimate how long it will take to produce more.
-
Inventory-based : You can stock the materials you need in advance. This allows you to predict how much you can expect to sell.
-
Project-driven: This is an approach where you set aside enough funds to cover the cost of your project. If you know the amount you require, you can buy the materials you need.
-
Resource-based JIT: This type of JIT is most commonly used. You allocate resources based on the demand. You will, for example, assign more staff to deal with large orders. You'll have fewer orders if you have fewer.
-
Cost-based: This is similar to resource-based, except that here you're not just concerned about how many people you have but how much each person costs.
-
Price-based: This is a variant of cost-based. However, instead of focusing on the individual workers' costs, this looks at the total price of the company.
-
Material-based: This is quite similar to cost-based, but instead of looking at the total cost of the company, you're concerned with how much raw materials you spend on average.
-
Time-based: Another variation of resource-based JIT. Instead of focusing only on how much each employee is costing, you should focus on how long it takes to complete your project.
-
Quality-based JIT is another variant of resource-based JIT. Instead of worrying about the costs of each employee or how long it takes for something to be made, you should think about how quality your product is.
-
Value-based: This is one of the newest forms of JIT. In this scenario, you're not concerned about how products perform or whether customers expect them to meet their expectations. Instead, your focus is on the value you bring to the market.
-
Stock-based is an inventory-based system that measures the number of items produced at any given moment. It is used when production goals are met while inventory is kept to a minimum.
-
Just-in-time planning (JIT): This is a combination JIT and supply-chain management. It is the process that schedules the delivery of components within a short time of their order. It's important because it reduces lead times and increases throughput.