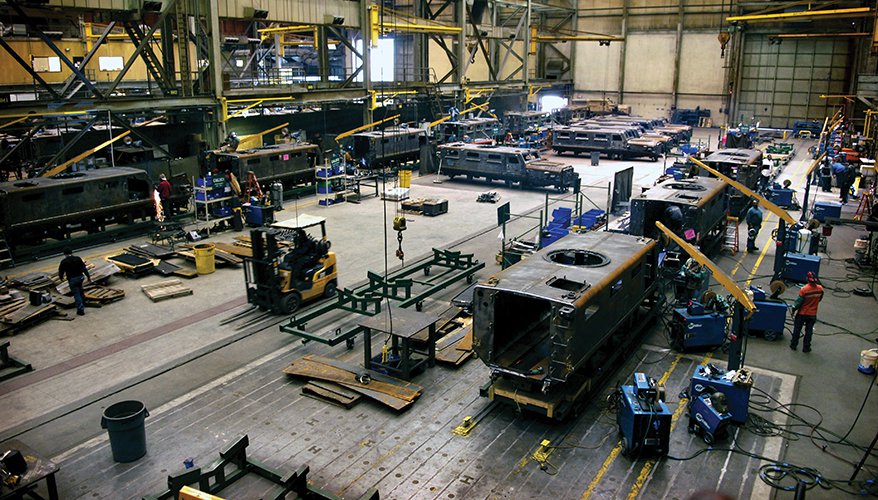
Flow describes the state of being in which all steps of a manufacturing process flow seamlessly without interruption. Every step adds value to the product and goods can flow without being impeded. Many companies plan out the production of a certain quantity of stock to ensure that production orders are fulfilled as efficiently and effectively as possible. This is Lean Manufacturing's push production. Here are the key elements that make flow work:
Manufacturing in real-time
In the 1970s, the dominant paradigm in American manufacturing was "just-in time". While the concept has its benefits, it is not the most practical way to run a company. Many new skills and mindsets are required to lower costs and improve efficiency. You will reap the full benefits if it is something you enjoy.
Standardizing processes and working with smaller quantities are two of the most important aspects in just-in-time production. A well-planned facility layout is critical in promoting a just-in-time mindset. Cellular manufacturing, for instance, can facilitate production flow. Cellular organization can make it easier to move materials around. Just-in-time producers should avoid lengthy changeovers.
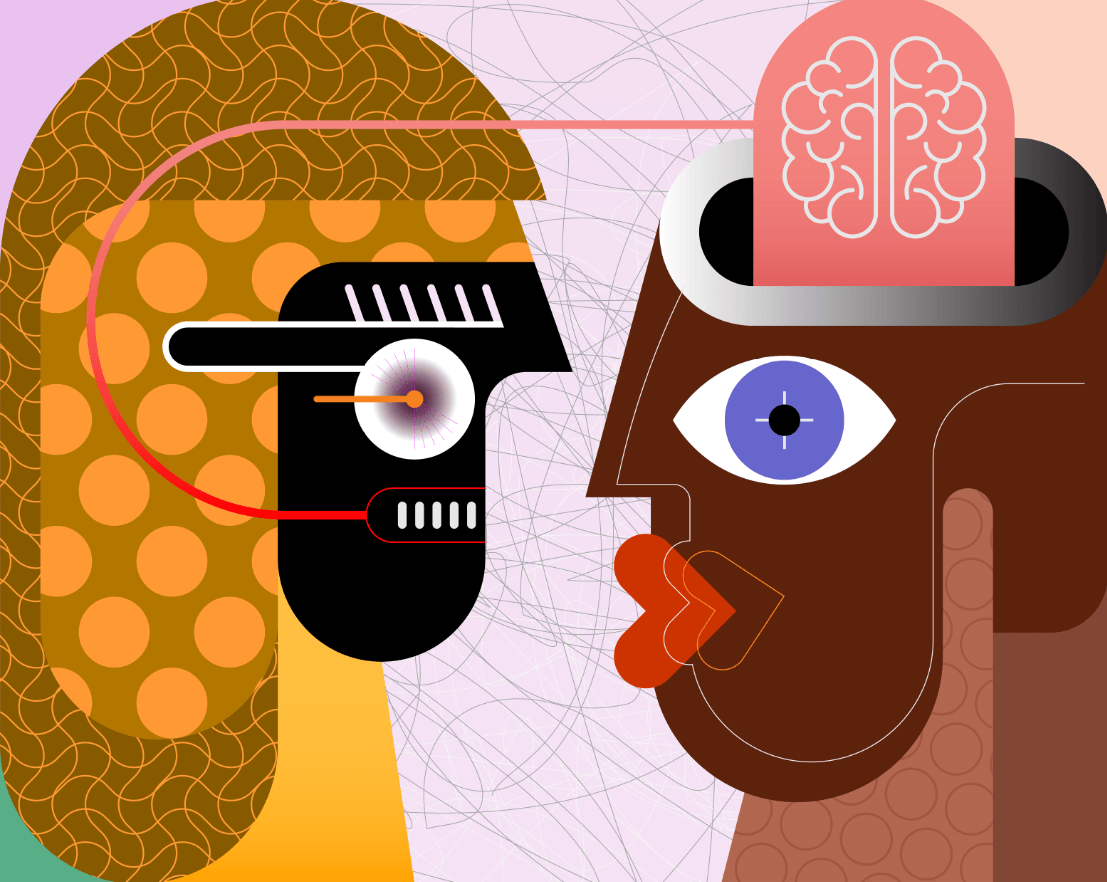
Standardized work
You must first create standardized work in order to apply lean manufacturing principles to manufacturing processes. This system of work is about the workers and the steps that they must complete to make a product. It also refers to the process of continuously improving the system through kaizen. Standardized work documents are the responsibility of the cell leader and are updated when takt time changes. Standardized work documentation is a foundation for improvement activities.
Standardized work processes can help organizations improve their productivity and service quality. They can reduce the time it takes to develop products and help reduce human error. It also enables the organization to fix problems faster, as people understand the process better. This allows the organization to increase customer satisfaction and continuous improvement. It is easy to implement these processes within a company when they are standardized. A mission statement is a great idea.
Continuous improvement
Lean principles are a way to improve your company's performance. This leads to a number of benefits. Although the benefits are often additive in nature, one common thread ties them all: lower costs, increased productivity, shorter lead times, and less waste. Lean continuous improvements are aimed at increasing value creation. But how does continuous improving work? This article will discuss some of the most common benefits of continuous improving. It's simple: Continuous Improvement helps companies save money.
In continuous improvement, a company focuses on incremental improvements rather than sweeping changes. While individual improvements may be small and seemingly insignificant, the sum is significant. The slow process of improvement is not about making big leaps. Continuous improvement in lean manufacturing environments focuses on aligning goals. This helps the business achieve maximum productivity and profitability. Continuous improvement methods can streamline production and make it easier for all involved to reach a common goal.
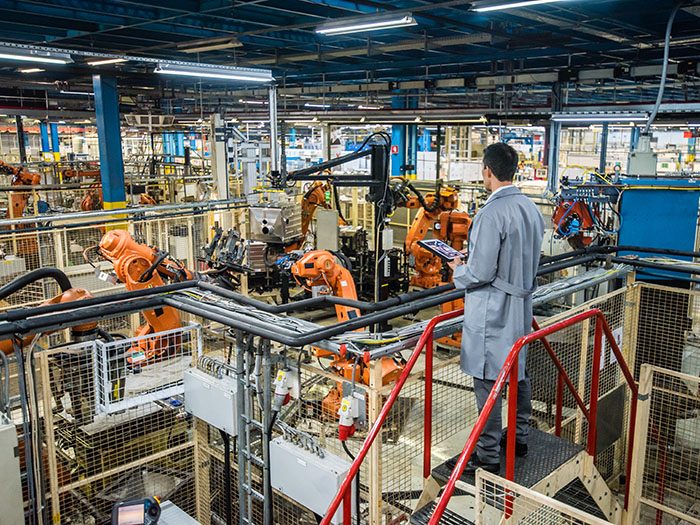
Kaizen
Kaizen in lean manufacturing is about reducing waste. In some cases, it is used to improve production yield, decrease lead time, and improve quality. A team of employees is assigned a specific role to study the problem and propose solutions. The creation of a flow map that demonstrates the value of the process is often the first step of a kaizen project. The team then conducts time studies on the relevant operations. This process is repeated until each step has been improved and the overall process is leaner and more efficient.
One example: A manufacturing plant may choose to buy a new forklift after identifying inefficiencies. The operator may be able to move inventory around faster, making loading and unloading easier. Similar to the value stream, it is a map of all processes that produce products or services. Five S's will be used during the mapping to increase employee productivity as well as workplace practices. There are seven types. Each of these types focuses on a different aspect of a manufacturing process.
FAQ
What are the 7 Rs of logistics?
The acronym "7R's" of Logistics stands for seven principles that underpin logistics management. It was developed by the International Association of Business Logisticians (IABL) and published in 2004 as part of its "Seven Principles of Logistics Management" series.
The acronym is composed of the following letters.
-
Responsible - ensure that actions are in compliance with legal requirements and do not cause harm to others.
-
Reliable: Have faith in your ability or the ability to honor any promises made.
-
Be responsible - Use resources efficiently and avoid wasting them.
-
Realistic - Take into consideration all aspects of operations including cost-effectiveness, environmental impact, and other factors.
-
Respectful - treat people fairly and equitably.
-
Resourceful - look for opportunities to save money and increase productivity.
-
Recognizable - provide customers with value-added services.
What is the job of a manufacturer manager?
Manufacturing managers must ensure that manufacturing processes are efficient, effective, and cost-effective. They should be aware of any issues within the company and respond accordingly.
They should also learn how to communicate effectively with other departments, including sales and marketing.
They should also be aware of the latest trends in their industry and be able to use this information to help improve productivity and efficiency.
Is it necessary to be familiar with Manufacturing Processes before we learn about Logistics.
No. You don't have to know about manufacturing processes before learning about logistics. Knowing about manufacturing processes will help you understand how logistics works.
How does a Production Planner differ from a Project Manager?
The difference between a product planner and project manager is that a planer is typically the one who organizes and plans the entire project. A production planner, however, is mostly involved in the planning stages.
What does manufacturing industry mean?
Manufacturing Industries are companies that manufacture products. Consumers are the people who purchase these products. These companies use various processes such as production, distribution, retailing, management, etc., to fulfill this purpose. They create goods from raw materials, using machines and various other equipment. This includes all types manufactured goods such as clothing, building materials, furniture, electronics, tools and machinery.
Statistics
- In 2021, an estimated 12.1 million Americans work in the manufacturing sector.6 (investopedia.com)
- According to the United Nations Industrial Development Organization (UNIDO), China is the top manufacturer worldwide by 2019 output, producing 28.7% of the total global manufacturing output, followed by the United States, Japan, Germany, and India.[52][53] (en.wikipedia.org)
- Many factories witnessed a 30% increase in output due to the shift to electric motors. (en.wikipedia.org)
- Job #1 is delivering the ordered product according to specifications: color, size, brand, and quantity. (netsuite.com)
- You can multiply the result by 100 to get the total percent of monthly overhead. (investopedia.com)
External Links
How To
How to use 5S to increase Productivity in Manufacturing
5S stands as "Sort", Set In Order", Standardize", Separate" and "Store". Toyota Motor Corporation invented the 5S strategy in 1954. It improves the work environment and helps companies to achieve greater efficiency.
This approach aims to standardize production procedures, making them predictable, repeatable, and easily measurable. Cleaning, sorting and packing are all done daily. These actions allow workers to perform their job more efficiently, knowing what to expect.
There are five steps that you need to follow in order to implement 5S. Each step requires a different action, which increases efficiency. If you sort items, it makes them easier to find later. You arrange items by placing them in an order. After you have divided your inventory into groups you can store them in easy-to-reach containers. Make sure everything is correctly labeled when you label your containers.
Employees must be able to critically examine their work practices. Employees should understand why they do the tasks they do, and then decide if there are better ways to accomplish them. To be successful in the 5S system, employees will need to acquire new skills and techniques.
In addition to improving efficiency, the 5S system also increases morale and teamwork among employees. They feel more motivated to work towards achieving greater efficiency as they see the results.