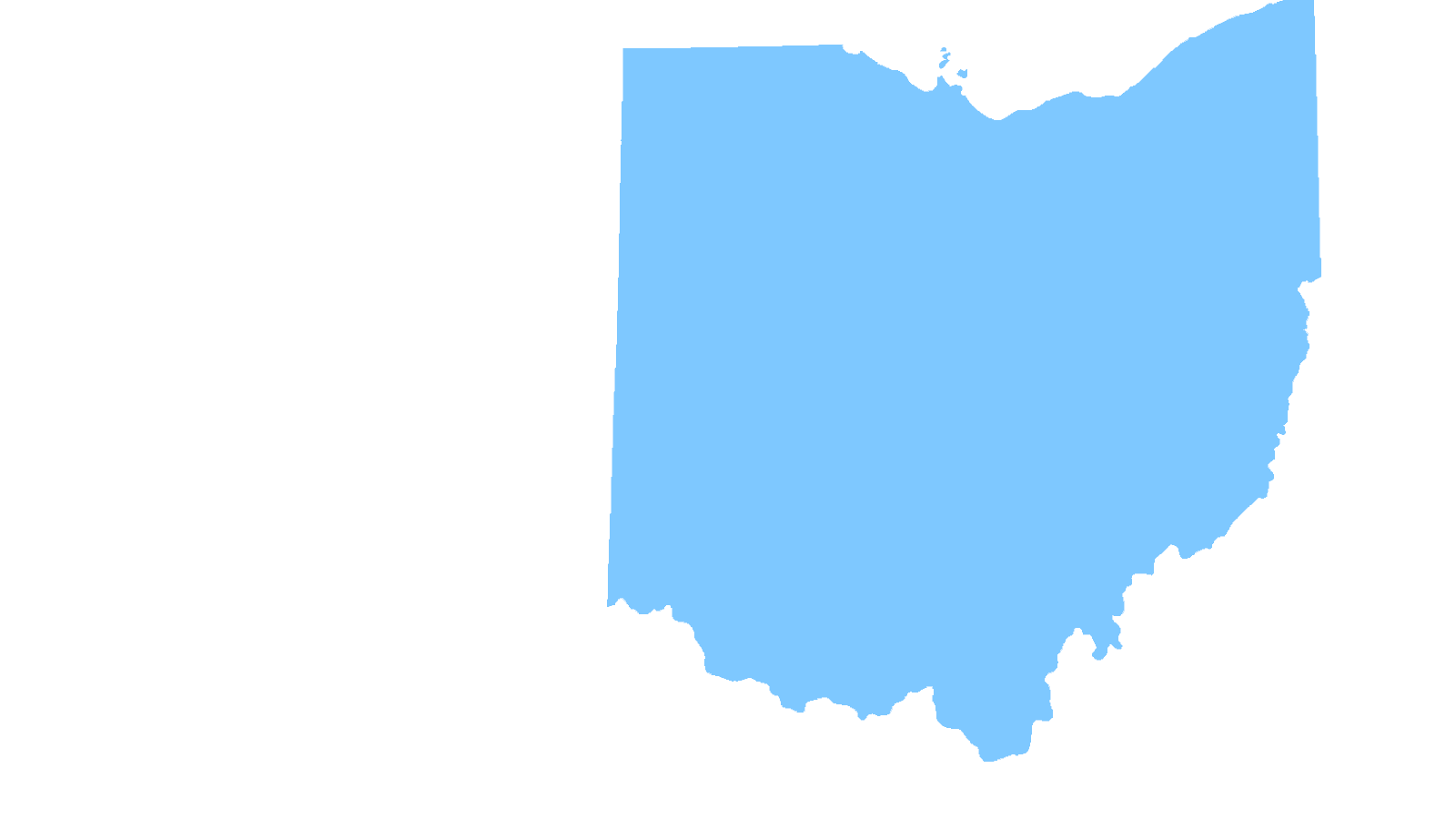
Businesses are never-ending processes, and to remain competitive they must constantly look for new ways to improve. The many things a company can change to improve their business operations range from operations to productivity.
Operational efficiency is a type of management technique which seeks to improve a business in all areas. Reduce waste, improve processes and develop efficient workflows.
Operational excellence comes from the scientific management theory, which was developed in the 18th Century and influenced by Adam Smith, Frederick Winslow Taylor, and Henry Ford. It is a process that takes years to implement and requires a lot of trial and error, but it is worth the effort.
What is Operational excellence?
The Institute for Operational Excellence defines operational excellence as the ability of an organization to monitor information and product flow. The ability to track product flow is essential for everyone in the organization, including senior executives and plant workers.
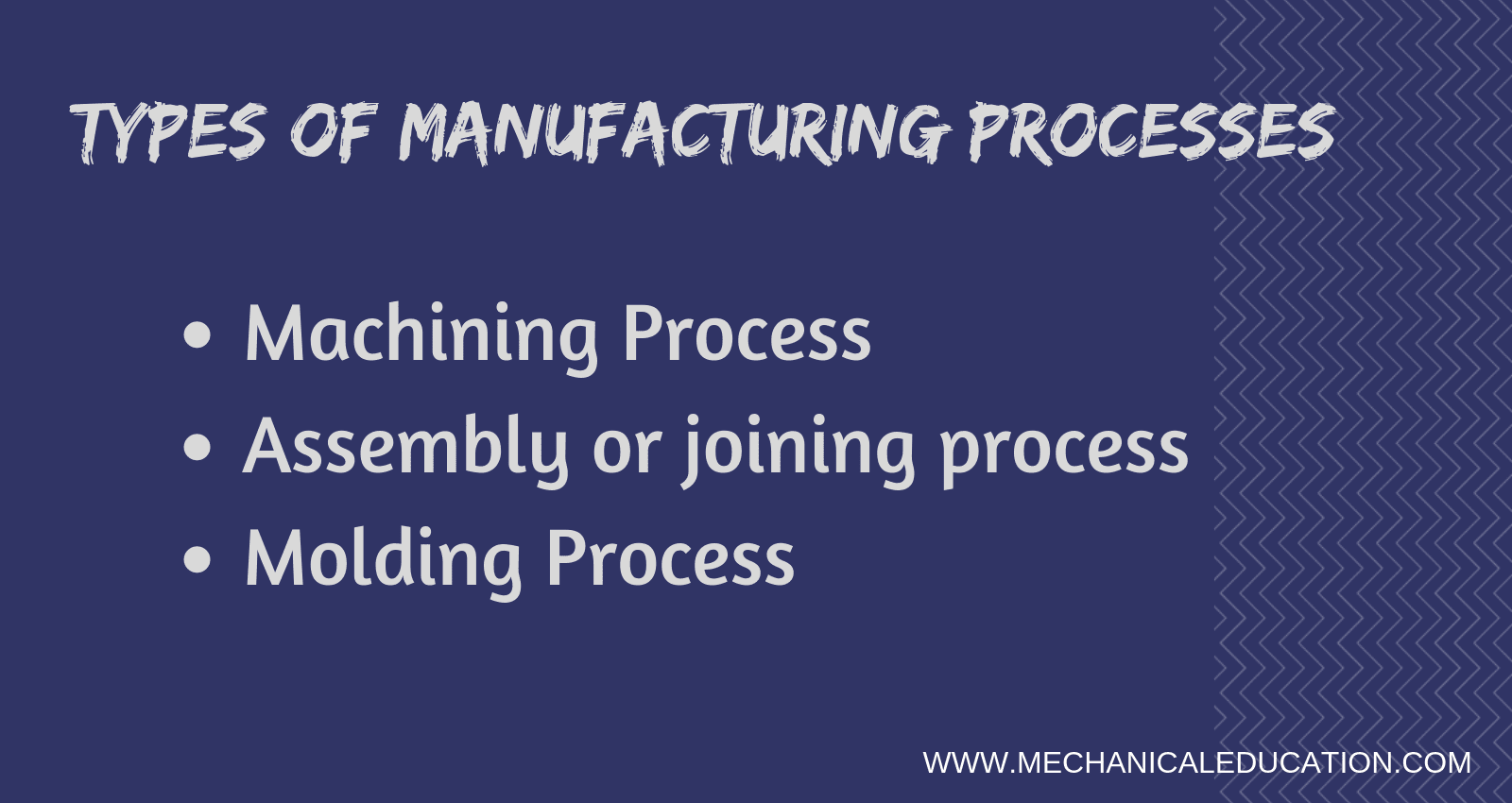
To create a culture that is based on operational excellence, a cultural change is needed. It is a process that requires time and effort to develop employee trust. It also involves a change in leadership styles and behavior, but it's an important step that can lead to long-term results.
What Is The Role Of Operational Excellence Staffs
Operational excellence staff are responsible for implementing the strategy of the organization. Their responsibilities include managing process improvement, participating on cross-functional teams, defining and tracking performance metrics, creating a culture, and mentorship of frontline operational leaders.
They may also lead projects based on improvement methodologies such as Six Sigma and Kaizen. These methods can be very effective at improving operations and increasing efficiency. However, they require staff that are trained in project management, business intelligence and other areas.
How to Create Operational Excellence Plan
A plan of operational excellence must include a set of methodologies that will enable you to achieve your goals in the shortest time possible. It is important to consider this if you're looking to improve customer satisfaction, reduce waste and streamline your processes.
To track your progress, you can use different KPIs. These KPIs should be in line with your goals and achievable, to encourage your employees to continue striving for excellence.
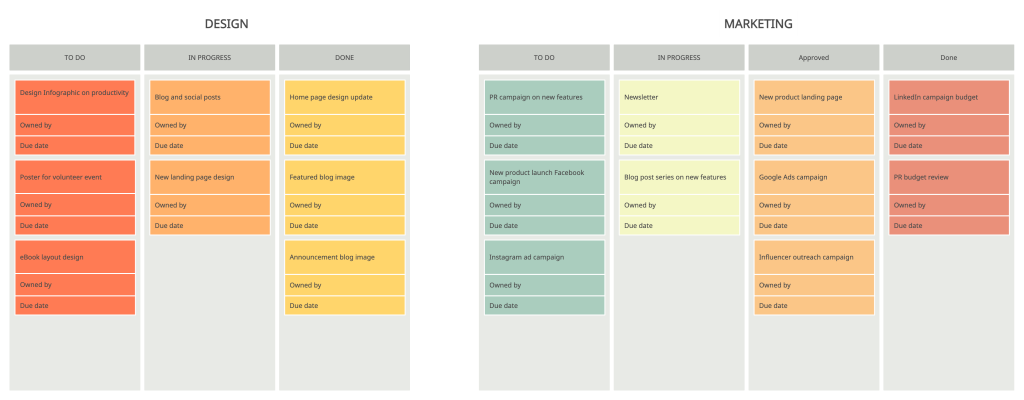
These tools will help to make your operation as efficient as it can be. The tools also allow you to collect feedback from your staff on the front lines so that you may continue to improve.
How to Measure Your Operational Excellence Goals
Most Directors of Operations will measure a combination of high-level financial and operational numbers, alongside common-sense qualitative data from employee and client surveys. This will provide them with a clearer view of their progress and the distance they have to travel before they reach their objectives.
This is because operational excellence works at every level of the company, so it's vital to make sure that all of the individual team members have their own targets. For example, a Director of Operations needs to have a profit target around what they spend on people, while a project manager should have their own targets around billable and non-billable work. This way, operational excellence can be measured at all levels of the business, ensuring that costs and revenue balance out.
FAQ
What does it mean to warehouse?
A warehouse is a place where goods are stored until they are sold. It can be either an indoor or outdoor space. Sometimes, it can be both an indoor and outdoor space.
How can efficiency in manufacturing be improved?
First, identify the factors that affect production time. Next, we must find ways to improve those factors. You can start by identifying the most important factors that impact production time. Once you've identified them all, find solutions to each one.
What is the responsibility for a logistics manager
A logistics manager makes sure that all goods are delivered on-time and in good condition. This is accomplished by using the experience and knowledge gained from working with company products. He/she should ensure that sufficient stock is available in order to meet customer demand.
How can manufacturing overproduction be reduced?
The key to reducing overproduction lies in developing better ways to manage inventory. This would reduce time spent on activities such as purchasing, stocking, and maintaining excess stock. This will allow us to free up resources for more productive tasks.
Kanban systems are one way to achieve this. A Kanbanboard is a visual tool that allows you to keep track of the work being done. Work items are moved through various states to reach their destination in a Kanban system. Each state is assigned a different priority.
As an example, if work is progressing from one stage of the process to another, then the current task is complete and can be transferred to the next. It is possible to keep a task in the beginning stages until it gets to the end.
This allows for work to continue moving forward, while also ensuring that there is no work left behind. Managers can view the Kanban board to see how much work they have done. This information allows managers to adjust their workflow based off real-time data.
Lean manufacturing is another way to manage inventory levels. Lean manufacturing focuses on eliminating waste throughout the entire production chain. Anything that does not contribute to the product's value is considered waste. Some common types of waste include:
-
Overproduction
-
Inventory
-
Packaging not required
-
Exceed materials
These ideas can help manufacturers improve efficiency and reduce costs.
Statistics
- According to the United Nations Industrial Development Organization (UNIDO), China is the top manufacturer worldwide by 2019 output, producing 28.7% of the total global manufacturing output, followed by the United States, Japan, Germany, and India.[52][53] (en.wikipedia.org)
- In the United States, for example, manufacturing makes up 15% of the economic output. (twi-global.com)
- [54][55] These are the top 50 countries by the total value of manufacturing output in US dollars for its noted year according to World Bank.[56] (en.wikipedia.org)
- According to a Statista study, U.S. businesses spent $1.63 trillion on logistics in 2019, moving goods from origin to end user through various supply chain network segments. (netsuite.com)
- It's estimated that 10.8% of the U.S. GDP in 2020 was contributed to manufacturing. (investopedia.com)
External Links
How To
How to Use 5S to Increase Productivity in Manufacturing
5S stands as "Sort", Set In Order", Standardize", Separate" and "Store". Toyota Motor Corporation developed the 5S method in 1954. It improves the work environment and helps companies to achieve greater efficiency.
This method aims to standardize production processes so that they are repeatable, measurable and predictable. This means that daily tasks such as cleaning and sorting, storage, packing, labeling, and packaging are possible. Workers can be more productive by knowing what to expect.
There are five steps to implementing 5S, including Sort, Set In Order, Standardize, Separate and Store. Each step is a different action that leads to greater efficiency. By sorting, for example, you make it easy to find the items later. Once you have placed items in an ordered fashion, you will put them together. Next, organize your inventory into categories and store them in containers that are easily accessible. You can also label your containers to ensure everything is properly labeled.
Employees need to reflect on how they do their jobs. Employees should understand why they do the tasks they do, and then decide if there are better ways to accomplish them. In order to use the 5S system effectively, they must be able to learn new skills.
The 5S method increases efficiency and morale among employees. They are more motivated to achieve higher efficiency levels as they start to see improvement.