
Lean management is an effective way to reduce waste in the workplace. The belief is that each activity or process within a company must add value to a product or service provided for the customer. This can only be achieved by eliminating the activities that are not adding value and working on a systematic basis to create even more value.
A lean business management system is meant to enhance the performance of any company. It helps employees to understand their purpose and goals.
In lean system management, the first step is to determine what value is. The first step is to identify what the customer wants, and then create a solution which provides this value. This can be achieved by ensuring everything, from the manufacturing process to customer services is efficient and consistent.
You can reduce costs and improve efficiency by applying lean manufacturing principles when making products. But, your staff must be on board. The results of the program could be disastrous if the staff is not committed.
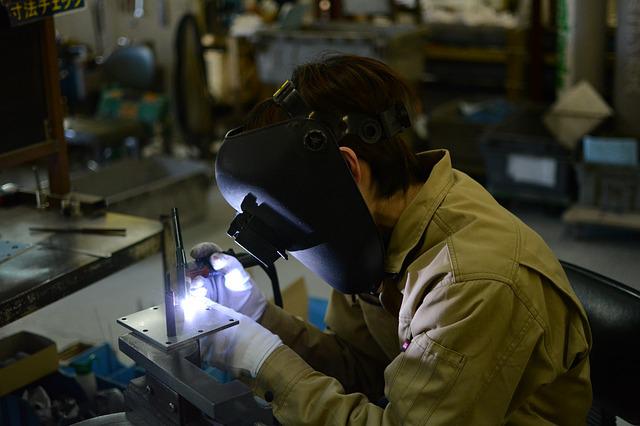
You must also ensure that the supply chain of your company is healthy. It's because many lean initiatives involve retooling the supply-chain to make it function well.
You can help by ensuring that your employees are properly trained in lean principles. This can include making sure your employees understand what waste is and why it's important to remove it from the production process.
You should also take into account the need for teamwork when you implement lean principles. It may be hard to achieve but is an important aspect of the lean system.
This will allow your team to produce better quality products and services and increase your company's bottom line in the long run. Encourage them to do this by allowing them to meet together regularly and talk about ways to reduce waste in their work.
A lean manager will be able to help you by ensuring all your workers are properly trained in these techniques. By keeping your team informed, they can also ensure that production runs smoothly.
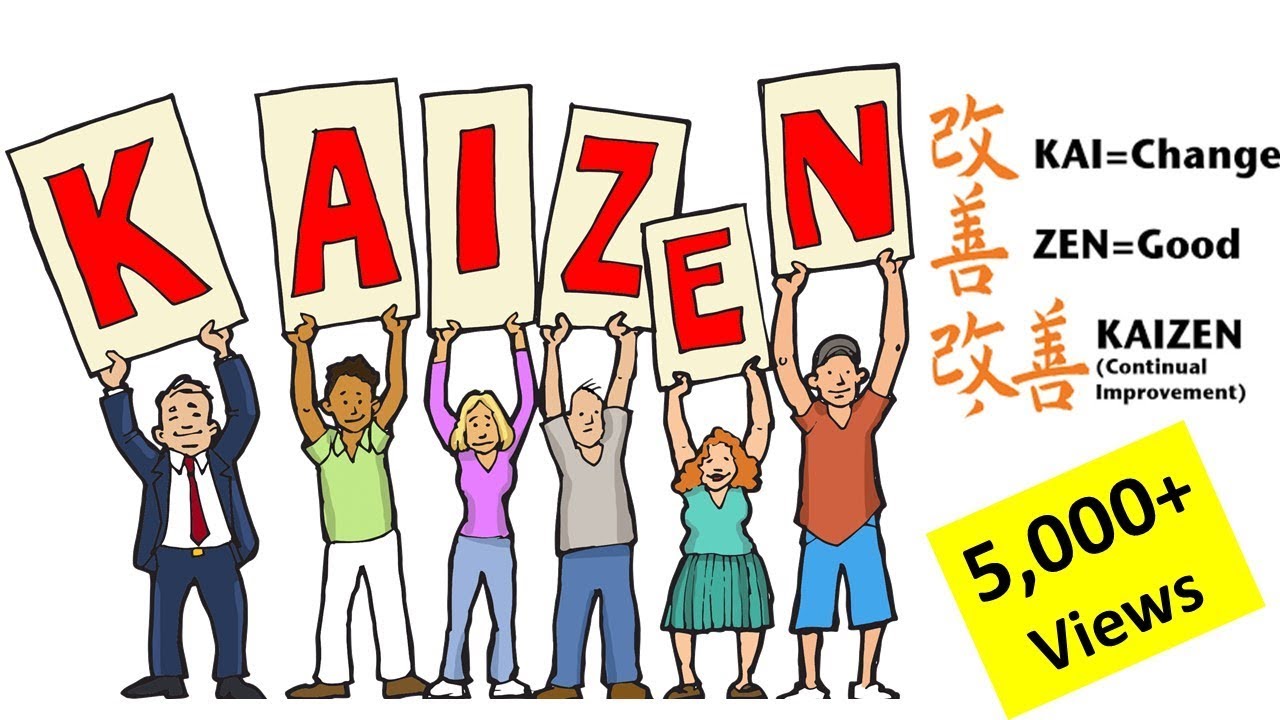
The final step in lean system management is to monitor and improve each of the procedures that are being implemented. You can do this by tracking each project's progress and making sure that all necessary changes are made.
According to the size of your company, you may have to hire someone to oversee your lean operations. If you search for jobs in lean management or look at job boards, you can find candidates who fit this role.
FAQ
What is the difference between Production Planning and Scheduling?
Production Planning (PP), is the process of deciding what production needs to take place at any given time. Forecasting and identifying production capacity are two key elements to this process.
Scheduling is the process that assigns dates to tasks so they can get completed within a given timeframe.
What is production planning?
Production Planning includes planning for all aspects related to production. It is important to have everything ready and planned before you start shooting. You should also have information to ensure the best possible results on set. This information includes locations, crew details and equipment requirements.
The first step is to outline what you want to film. You may have already decided where you would like to shoot, or maybe there are specific locations or sets that you want to use. Once you have identified your locations and scenes, you can start working out which elements you require for each scene. One example is if you are unsure of the exact model you want but decide that you require a car. In this case, you could start looking up cars online to find out what models are available and then narrow your choices by choosing between different makes and models.
After you have selected the car you want, you can begin to think about additional features. You might need to have people in the front seats. Or perhaps you need someone walking around the back of the car? Maybe you'd like to change the interior from black to a white color. These questions will help determine the look and feel you want for your car. It is also worth considering the types of shots that you wish to take. What type of shots will you choose? Maybe you want to show your engine or the steering wheel. These details will help identify the exact car you wish to film.
Once you've determined the above, it is time to start creating a calendar. You can use a schedule to determine when and where you need it to be shot. You will need to know when you have to be there, what time you have to leave and when your return home. It will help everyone know exactly what they have to do and when. If you need to hire extra staff, you can make sure you book them in advance. It is not worth hiring someone who won’t show up because you didn’t tell him.
Your schedule will also have to be adjusted to reflect the number of days required to film. Some projects can be completed in a matter of days or weeks. Others may take several days. When you are creating your schedule, you should always keep in mind whether you need more than one shot per day or not. Multiple takes of the same location will lead to higher costs and take more time. You can't be certain if you will need multiple takes so it is better not to shoot too many.
Budgeting is another important aspect of production planning. Setting a realistic budget is essential as it will allow you to work within your means. It is possible to reduce the budget at any time if you experience unexpected problems. However, you shouldn't overestimate the amount of money you will spend. If you underestimate how much something costs, you'll have less money to pay for other items.
Planning production is a tedious process. Once you have a good understanding of how everything works together, planning future projects becomes easy.
What are my options for learning more about manufacturing
Experience is the best way for you to learn about manufacturing. You can read books, or watch instructional videos if you don't have the opportunity to do so.
Why is logistics so important in manufacturing?
Logistics are essential to any business. They enable you to achieve outstanding results by helping manage product flow from raw materials through to finished goods.
Logistics play a key role in reducing expenses and increasing efficiency.
Is automation important in manufacturing?
Automation is essential for both manufacturers and service providers. It allows them to offer services faster and more efficiently. They can also reduce their costs by reducing human error and improving productivity.
Statistics
- You can multiply the result by 100 to get the total percent of monthly overhead. (investopedia.com)
- Job #1 is delivering the ordered product according to specifications: color, size, brand, and quantity. (netsuite.com)
- According to the United Nations Industrial Development Organization (UNIDO), China is the top manufacturer worldwide by 2019 output, producing 28.7% of the total global manufacturing output, followed by the United States, Japan, Germany, and India.[52][53] (en.wikipedia.org)
- In 2021, an estimated 12.1 million Americans work in the manufacturing sector.6 (investopedia.com)
- According to a Statista study, U.S. businesses spent $1.63 trillion on logistics in 2019, moving goods from origin to end user through various supply chain network segments. (netsuite.com)
External Links
How To
How to use 5S to increase Productivity in Manufacturing
5S stands in for "Sort", the "Set In Order", "Standardize", or "Separate". Toyota Motor Corporation developed the 5S method in 1954. It assists companies in improving their work environments and achieving higher efficiency.
This approach aims to standardize production procedures, making them predictable, repeatable, and easily measurable. This means that every day tasks such cleaning, sorting/storing, packing, and labeling can be performed. Through these actions, workers can perform their jobs more efficiently because they know what to expect from them.
There are five steps to implementing 5S, including Sort, Set In Order, Standardize, Separate and Store. Each step involves a different action which leads to increased efficiency. Sorting things makes it easier to find them later. When you arrange items, you place them together. Once you have separated your inventory into groups and organized them, you will store these groups in easily accessible containers. Finally, when you label your containers, you ensure everything is labeled correctly.
Employees must be able to critically examine their work practices. Employees must understand why they do certain tasks and decide if there's another way to accomplish them without relying on the old ways of doing things. They will need to develop new skills and techniques in order for the 5S system to be implemented.
In addition to improving efficiency, the 5S system also increases morale and teamwork among employees. They are more motivated to achieve higher efficiency levels as they start to see improvement.