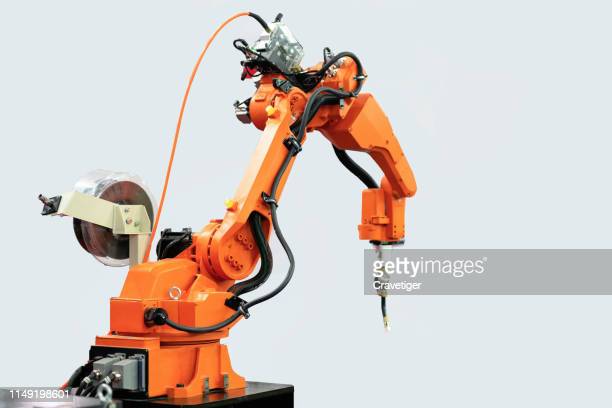
Supply chain certification can prove you are an expert on the subject. A credential, such as the CSCP, will make you more valued by your employer and help you stand out among your peers. It will also ensure that your organization remains competitive in today's economy. These are just a few of the many benefits of becoming certified in supply chain management.
CSCP is an end-to-end supply chain certification
The CSCP certification is a valuable credential for supply chain professionals because it provides a broader understanding of the supply chain and helps the candidate to visualize the entire process. End-to end supply chain activities can be complex. The CSCP certificate tests the candidate’s skills in coordinating these activities and integrating them. Companies are looking to hire supply chain professionals who will add value at every point of the supply-chain.
The CSCP certification exam consists eight modules. These modules cover critical aspects of supply chain management. The exam questions are split into two sections. The first three focus on curriculum knowledge. The last two parts are to test the candidates' ability to prepare for the final exam. A pass is defined as a score between 200 and 350 points. Scores of 300 or greater are considered passing. Scores below 300 are considered failing.
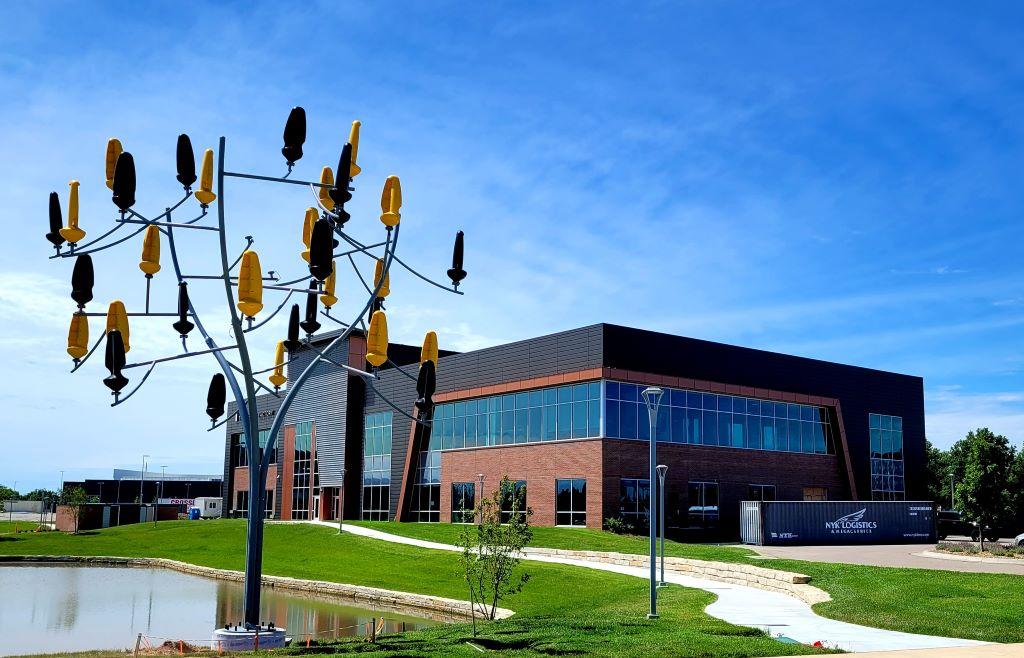
CPSM is a specialized supply chain certification
The CPSM credential, which stands for Certified Professional in Supply Management (Certified Professional in Supply Management), has been a well-respected and highly respected supply management certification. The Institute for Supply Management is the largest supply-management association in the globe. CPSM certification is internationally recognized.
The CPSM certification represents excellence in supply management. It includes three modules that test your advanced knowledge and skills. Earning this certification will allow supply management professionals to implement supply chain strategies throughout an organization. The certification program takes anywhere from six to twelve months. Successful candidates must renew their credential every three years.
CSCP requires four-year undergraduate degree
A CSCP certificate, or Certified Supply Chain Professional (or Certified Supply Chain Professional), shows that an individual's supply chain management knowledge and skills are advanced. This credential differentiates one from their peers and proves that they have the expertise in their field. For those who are interested in obtaining this certification, there are many options available.
Three years of experience in the workplace and a bachelor's degree are required for the CSCP exam. Afterward, students must accrue 75 professional development points every five years to maintain their certification. For students to retake an exam, they must earn another 75 point.
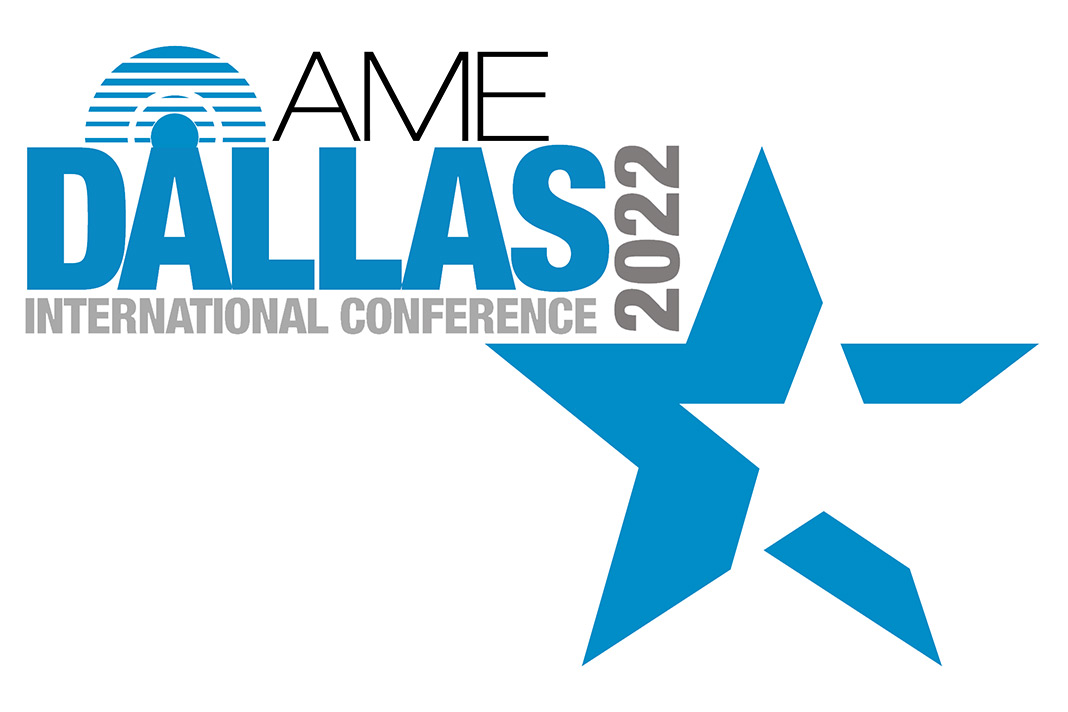
Supply chain certification requires a retake fee
The multiple-choice online certification exam Certified Supply Chain Fundamentals is available. The test is available online and contains 50 multiple choice questions. To be eligible for certification, you must score 70% on the test. Retake fees are $450 USD.
To be eligible for the exam, you must have worked in a decision-making position. A decision-making position is any job where you are responsible for controlling processes or defining tasks. This could include a supervisory or management position. You can also apply for the Supplier Quality Professional exam if you have any other ASQ certifications.
FAQ
Are there any Manufacturing Processes that we should know before we can learn about Logistics?
No. No. It is important to know about the manufacturing processes in order to understand how logistics works.
How can we improve manufacturing efficiency?
The first step is to determine the key factors that impact production time. We then need to figure out how to improve these variables. If you aren't sure where to begin, think about the factors that have the greatest impact on production time. Once you have identified them, it is time to identify solutions.
How can manufacturing avoid production bottlenecks
To avoid production bottlenecks, ensure that all processes run smoothly from the moment you receive your order to the time the product ships.
This includes both quality control and capacity planning.
Continuous improvement techniques like Six Sigma are the best way to achieve this.
Six Sigma is a management method that helps to improve quality and reduce waste.
It is focused on creating consistency and eliminating variation in your work.
How is a production manager different from a producer planner?
The major difference between a Production Planner and a Project Manager is that a Project Manager is often the person responsible for organizing and planning the entire project. While a Production Planner is involved mainly in the planning stage,
What are the 7 Rs of logistics.
The 7R's of Logistics is an acronym for the seven basic principles of logistics management. It was developed by the International Association of Business Logisticians (IABL) and published in 2004 as part of its "Seven Principles of Logistics Management" series.
The acronym is composed of the following letters.
-
Responsible - ensure that all actions taken are within legal requirements and are not harmful to others.
-
Reliable - Have confidence in your ability to fulfill all of your commitments.
-
Be responsible - Use resources efficiently and avoid wasting them.
-
Realistic – Consider all aspects, including cost-effectiveness as well as environmental impact.
-
Respectful – Treat others fairly and equitably.
-
Be resourceful: Look for opportunities to save money or increase productivity.
-
Recognizable: Provide customers with value-added service
Statistics
- You can multiply the result by 100 to get the total percent of monthly overhead. (investopedia.com)
- Many factories witnessed a 30% increase in output due to the shift to electric motors. (en.wikipedia.org)
- According to a Statista study, U.S. businesses spent $1.63 trillion on logistics in 2019, moving goods from origin to end user through various supply chain network segments. (netsuite.com)
- It's estimated that 10.8% of the U.S. GDP in 2020 was contributed to manufacturing. (investopedia.com)
- Job #1 is delivering the ordered product according to specifications: color, size, brand, and quantity. (netsuite.com)
External Links
How To
How to use the Just In-Time Production Method
Just-intime (JIT), a method used to lower costs and improve efficiency in business processes, is called just-in-time. This is where you have the right resources at the right time. This means that your only pay for the resources you actually use. Frederick Taylor first coined this term while working in the early 1900s as a foreman. He noticed that workers were often paid overtime when they had to work late. He decided to ensure workers have enough time to do their jobs before starting work to improve productivity.
JIT is an acronym that means you need to plan ahead so you don’t waste your money. Also, you should look at the whole project from start-to-finish and make sure you have the resources necessary to address any issues. You'll be prepared to handle any potential problems if you know in advance. You won't have to pay more for unnecessary items.
There are several types of JIT techniques:
-
Demand-driven: This is a type of JIT where you order the parts/materials needed for your project regularly. This will let you track the amount of material left over after you've used it. It will also allow you to predict how long it takes to produce more.
-
Inventory-based: You stock materials in advance to make your projects easier. This allows you predict the amount you can expect to sell.
-
Project-driven: This method allows you to set aside enough funds for your project. Knowing how much money you have available will help you purchase the correct amount of materials.
-
Resource-based JIT: This type of JIT is most commonly used. This is where you assign resources based upon demand. You will, for example, assign more staff to deal with large orders. If you don’t have many orders you will assign less people to the work.
-
Cost-based: This is the same as resource-based except that you don't care how many people there are but how much each one of them costs.
-
Price-based pricing: This is similar in concept to cost-based but instead you look at how much each worker costs, it looks at the overall company's price.
-
Material-based is an alternative to cost-based. Instead of looking at the total cost in the company, this method focuses on the average amount of raw materials that you consume.
-
Time-based JIT: A variation on resource-based JIT. Instead of focusing on the cost of each employee, you will focus on the time it takes to complete a project.
-
Quality-based JIT: Another variation on resource-based JIT. Instead of looking at the labor costs and time it takes to make a product, think about its quality.
-
Value-based: This is one of the newest forms of JIT. You don't worry about whether the products work or if they meet customer expectations. Instead, you focus on the added value that you provide to your market.
-
Stock-based: This is an inventory-based method that focuses on the actual number of items being produced at any given time. This is used to increase production and minimize inventory.
-
Just-in time (JIT), planning: This is a combination JIT/supply chain management. This refers to the scheduling of the delivery of components as soon after they are ordered. It is essential because it reduces lead-times and increases throughput.