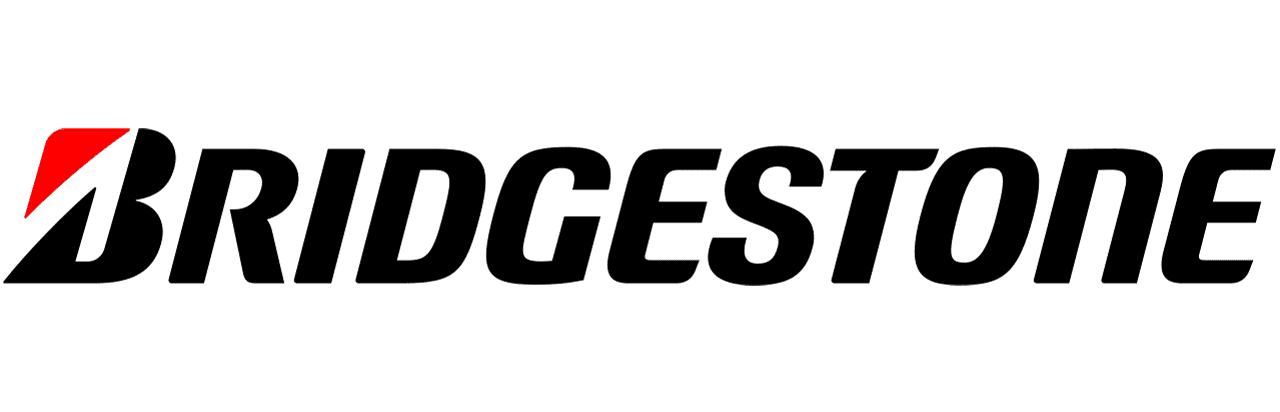
Supply chain analytics courses will help you to find your next career or improve your skills in order to keep up with changes in business. It is an essential part of every organization's operations. Organizations can meet customer expectations by using the tools they use to gather and analyze data.
Supply chain analytics courses teach you to interpret voluminous data to make sense of it and to discover patterns that can be used to inform future decisions. It can help you to identify the most effective course of action. This will allow you to make faster and more accurate decision. It can also increase your working capital. It can help you to identify the inventory levels required to provide the services that your customers want. It can also help you to mitigate possible risks.
There are always new developments in the global marketplace, so it is important to keep up with current trends. Data is being used by many companies to improve the efficiency of their supply chain. It can also help forecast future demand. This course shows you how data mining and predictive analysis can be used to analyze your supply chain. These techniques are useful for developing inventory policies, forecasting future demand, and performing predictive maintenance.
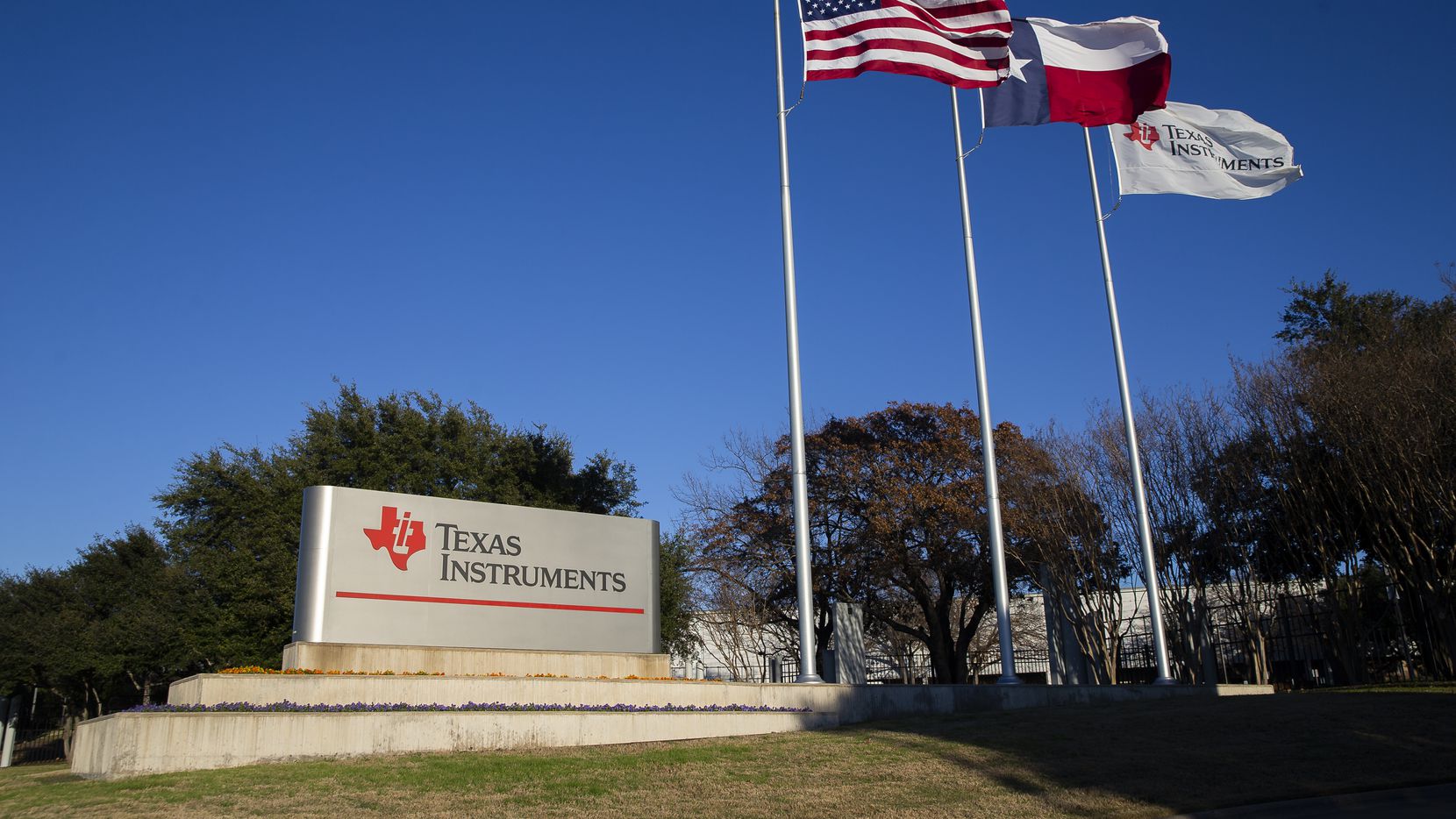
The course also explains the components of supply chains and how they can be combined in order to create an integrated system. This includes the logistics planning and export-import procedures as well as containerisation. It also covers shipping scheduling, inventory management, air cargo management, and shipment management. The course also covers data cleansing and visualization.
Machine learning, which uses algorithms and data to create patterns from data, is also included in the course. This is particularly important in the supply chain sector. It is used for customer segmentation and can be used in conjunction with Python to create predictive models.
Furthermore, this course covers ethics and key drivers of supply-chain management. It also provides information on supplier selection and inventory management. It explains the importance of flexibility and innovation.
The supply chain analytics courses will give you an understanding of why data-driven decision making is so important in today’s business environment. It can help you make better decisions, which can reduce costs and increase efficiency. It also gives you the ability to analyze your data to find new ways to improve your organization. This can improve your company's bottom line and it is an important part of any supply-chain management course.
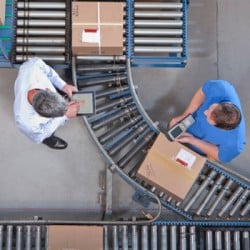
Faculty who have extensive experience in supply chain management will be teaching the course. It will provide an overview and teach you how to select the right technology for your requirements. You will also learn about the various models involved in supply chain management. This includes the inventory management model. You will also learn about the most common software tools that are used to analyze data, and how to use them to improve supply chain efficiency.
FAQ
What does the term manufacturing industries mean?
Manufacturing Industries are companies that manufacture products. Consumers are those who purchase these products. These companies employ many processes to achieve this purpose, such as production and distribution, retailing, management and so on. They create goods from raw materials, using machines and various other equipment. This covers all types of manufactured goods including clothing, food, building supplies and furniture, as well as electronics, tools, machinery, vehicles and pharmaceuticals.
What can I do to learn more about manufacturing?
The best way to learn about manufacturing is through hands-on experience. However, if that's not possible, you can always read books or watch educational videos.
What are manufacturing and logistic?
Manufacturing is the production of goods using raw materials. Logistics covers all aspects involved in managing supply chains, including procurement and production planning. Manufacturing and logistics are often considered together as a broader term that encompasses both the process of creating products and delivering them to customers.
What are the requirements to start a logistics business?
To be a successful businessman in logistics, you will need many skills and knowledge. Effective communication skills are necessary to work with suppliers and clients. It is important to be able to analyse data and draw conclusions. You will need to be able handle pressure well and work in stressful situations. You must be creative and innovative to develop new ideas to improve efficiency. You will need strong leadership skills to motivate and direct your team members towards achieving their organizational goals.
You must be organized to meet tight deadlines.
What are the 7 Rs of logistics management?
The 7R's of Logistics is an acronym for the seven basic principles of logistics management. It was developed and published by the International Association of Business Logisticians in 2004 as part of the "Seven Principles of Logistics Management".
The following letters form the acronym:
-
Responsible – ensure that all actions are legal and don't cause harm to anyone else.
-
Reliable: Have faith in your ability or the ability to honor any promises made.
-
It is reasonable to use resources efficiently and not waste them.
-
Realistic – consider all aspects of operations, from cost-effectiveness to environmental impact.
-
Respectful - treat people fairly and equitably.
-
Reliable - Find ways to save money and increase your productivity.
-
Recognizable is a company that provides customers with value-added solutions.
Statistics
- According to a Statista study, U.S. businesses spent $1.63 trillion on logistics in 2019, moving goods from origin to end user through various supply chain network segments. (netsuite.com)
- It's estimated that 10.8% of the U.S. GDP in 2020 was contributed to manufacturing. (investopedia.com)
- According to the United Nations Industrial Development Organization (UNIDO), China is the top manufacturer worldwide by 2019 output, producing 28.7% of the total global manufacturing output, followed by the United States, Japan, Germany, and India.[52][53] (en.wikipedia.org)
- You can multiply the result by 100 to get the total percent of monthly overhead. (investopedia.com)
- [54][55] These are the top 50 countries by the total value of manufacturing output in US dollars for its noted year according to World Bank.[56] (en.wikipedia.org)
External Links
How To
Six Sigma and Manufacturing
Six Sigma is defined as "the application of statistical process control (SPC) techniques to achieve continuous improvement." Motorola's Quality Improvement Department created Six Sigma at their Tokyo plant, Japan in 1986. Six Sigma's basic concept is to improve quality and eliminate defects through standardization. In recent years, many companies have adopted this method because they believe there is no such thing as perfect products or services. The main goal of Six Sigma is to reduce variation from the mean value of production. This means that if you take a sample of your product, then measure its performance against the average, you can find out what percentage of the time the process deviates from the norm. If the deviation is excessive, it's likely that something needs to be fixed.
Understanding how variability works in your company is the first step to Six Sigma. Once you have this understanding, you will need to identify sources and causes of variation. These variations can also be classified as random or systematic. Random variations occur when people make mistakes; systematic ones are caused by factors outside the process itself. You could consider random variations if some widgets fall off the assembly lines. If however, you notice that each time you assemble a widget it falls apart in exactly the same spot, that is a problem.
Once you have identified the problem, you can design solutions. You might need to change the way you work or completely redesign the process. After implementing the new changes, you should test them again to see if they worked. If they don't work, you will need to go back to the drawing boards and create a new plan.