
The field of manufacturing engineering often goes by the name production engineering. This type of engineering shares many similarities with other engineering disciplines. This area of engineering is a great way to find your niche and be a part of the company's success. These engineers are able to ensure that a product or service meets high quality standards.
Your job duties
The job of a production engineer involves coordinating and analyzing the production process, from design to implementation. This position requires meticulous attention to detail as well as a commitment for the safety of the workplace. Production engineers are responsible for ensuring that companies maintain high quality standards, environmental safety, as well as evaluating existing production activities in order to find ways to improve.
A production engineer is a person who helps companies produce products quickly and efficiently. They might be asked to examine and analyze existing production processes or they may concentrate on one part of the production process. They may also train production workers and adjust software.
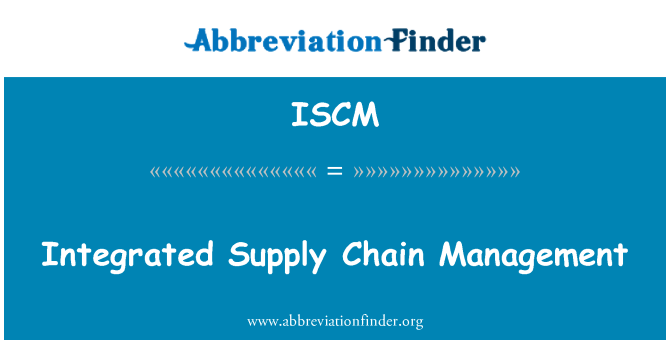
The job demands excellent communication skills. An engineer must be capable of explaining complex engineering concepts in an easy-to-understand manner. This is because engineering requires complex calculations and math. To determine the cost of finished products or to solve manufacturing problems, a production engineer might use equations.
Education is required
The first step toward a career as a production engineer is to acquire a bachelor's degree in manufacturing or industrial engineering. Employers may prefer to have a master's degree especially for positions in research-oriented manufacturing. A proficiency in one or two specialized areas is also helpful.
Industrial engineers use their creativity and analytical skills to improve the efficiency of production processes. They work to reduce waste and find new ways to utilize equipment, materials, and people more efficiently. They must also have good communication skills, as they must be able to explain complex processes to non-technical audiences. Good communication skills also involve being able to listen carefully and fully understand the views and opinions of others.
During the degree program, manufacturing engineers receive hands-on training. Safety regulations and procedures will be covered. They will need to apply for a Professional Engineer licence issued by National Society of Professional Engineers. This license is essential because it shows employers and clients that your credentials are valid. It is also important that you renew your license according state requirements.
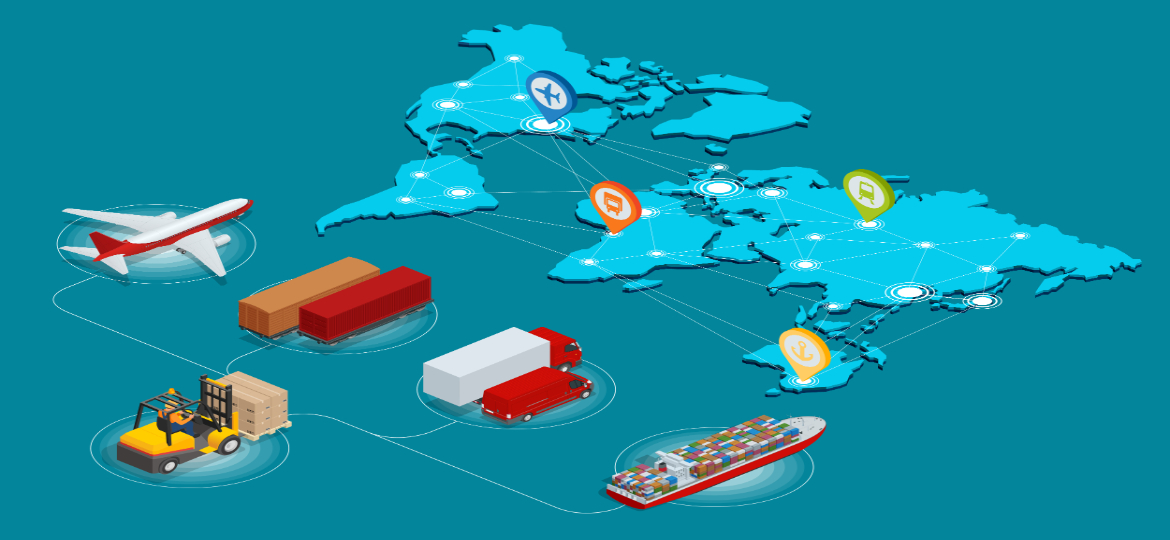
Salary
The salary of a producer engineer will vary depending on the company and where you live. Production engineers usually work in an office environment. However they may occasionally travel to production sites to inspect machinery, improve processes and perform other tasks. Some production engineers are self-employed, while others work for larger companies. Production engineers are expected not only to earn a good salary but also to finish their work promptly.
Production engineers work in collaboration with other professionals to ensure the safety and quality of the final product. They also work closely alongside designers to ensure efficient production processes. In some cases, they may be responsible for maintaining safety standards in the factory and training workers about proper safety procedures. This job description isn't exhaustive, but it gives an idea of the duties and responsibilities of a production engineer.
The salary of a production engineer depends on his or her level of experience. An entry-level production engineer can expect to make around Rs2.5 lakhs a year. Mid-level engineers could earn Rs3.8 Lakhs. In the meantime, production engineers with experience can expect to earn up to Rs6.1 million annually.
FAQ
What is the responsibility of a production planner?
Production planners make sure that every aspect of the project is delivered on-time, within budget, and within schedule. They make sure that the product and services meet client expectations.
What are the responsibilities for a manufacturing manager
Manufacturing managers must ensure that manufacturing processes are efficient, effective, and cost-effective. They should be aware of any issues within the company and respond accordingly.
They must also be able to communicate with sales and marketing departments.
They should be informed about industry trends and be able make use of this information to improve their productivity and efficiency.
What skills is required for a production planner?
Being a production planner is not easy. You need to be organized and flexible. You must also be able to communicate effectively with clients and colleagues.
How can overproduction in manufacturing be reduced?
Better inventory management is key to reducing excess production. This would decrease the time that is spent on inefficient activities like purchasing, storing, or maintaining excess stock. This would allow us to use our resources for more productive tasks.
One way to do this is to adopt a Kanban system. A Kanban board can be used to monitor work progress. A Kanban system allows work items to move through several states before reaching their final destination. Each state represents a different priority level.
When work is completed, it can be transferred to the next stage. It is possible to keep a task in the beginning stages until it gets to the end.
This allows for work to continue moving forward, while also ensuring that there is no work left behind. Managers can see how much work has been done and the status of each task at any time with a Kanban Board. This allows them the ability to adjust their workflow using real-time data.
Lean manufacturing, another method to control inventory levels, is also an option. Lean manufacturing seeks to eliminate waste from every step of the production cycle. Anything that doesn't add value to the product is considered waste. The following are examples of common waste types:
-
Overproduction
-
Inventory
-
Unnecessary packaging
-
Materials in excess
These ideas will help manufacturers increase efficiency and lower costs.
What are the four types of manufacturing?
Manufacturing is the process by which raw materials are transformed into useful products through machines and processes. It can involve many activities like designing, manufacturing, testing packaging, shipping, selling and servicing.
Statistics
- [54][55] These are the top 50 countries by the total value of manufacturing output in US dollars for its noted year according to World Bank.[56] (en.wikipedia.org)
- (2:04) MTO is a production technique wherein products are customized according to customer specifications, and production only starts after an order is received. (oracle.com)
- Job #1 is delivering the ordered product according to specifications: color, size, brand, and quantity. (netsuite.com)
- You can multiply the result by 100 to get the total percent of monthly overhead. (investopedia.com)
- According to the United Nations Industrial Development Organization (UNIDO), China is the top manufacturer worldwide by 2019 output, producing 28.7% of the total global manufacturing output, followed by the United States, Japan, Germany, and India.[52][53] (en.wikipedia.org)
External Links
How To
How to Use 5S to Increase Productivity in Manufacturing
5S stands as "Sort", Set In Order", Standardize", Separate" and "Store". Toyota Motor Corporation invented the 5S strategy in 1954. This methodology helps companies improve their work environment to increase efficiency.
This method has the basic goal of standardizing production processes to make them repeatable. This means that every day tasks such cleaning, sorting/storing, packing, and labeling can be performed. These actions allow workers to perform their job more efficiently, knowing what to expect.
There are five steps that you need to follow in order to implement 5S. Each step is a different action that leads to greater efficiency. By sorting, for example, you make it easy to find the items later. You arrange items by placing them in an order. Then, after you separate your inventory into groups, you store those groups in containers that are easy to access. Labeling your containers will ensure that everything is correctly labeled.
This requires employees to critically evaluate how they work. Employees must understand why they do certain tasks and decide if there's another way to accomplish them without relying on the old ways of doing things. In order to use the 5S system effectively, they must be able to learn new skills.
In addition to improving efficiency, the 5S system also increases morale and teamwork among employees. They feel more motivated to work towards achieving greater efficiency as they see the results.