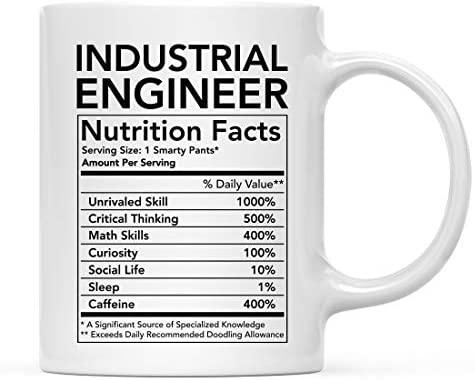
It can be daunting to enter the logistics industry. Before you can get your job, you may need to take additional courses or do internships. There are many entry level jobs in logistics that will help you get started.
These positions usually require an associate's or bachelor's degree. You will gain a deeper understanding of the supply chain. Having a degree will also help you qualify for professional certifications. Online courses can also be offered in specialized fields. Sometimes, reimbursements may be available for graduate programs.
You can find entry level jobs in many industries, including logistics. You can work in oil and gas production, aerospace manufacturing, or freight transport. There are many opportunities to work internationally in a variety industry.
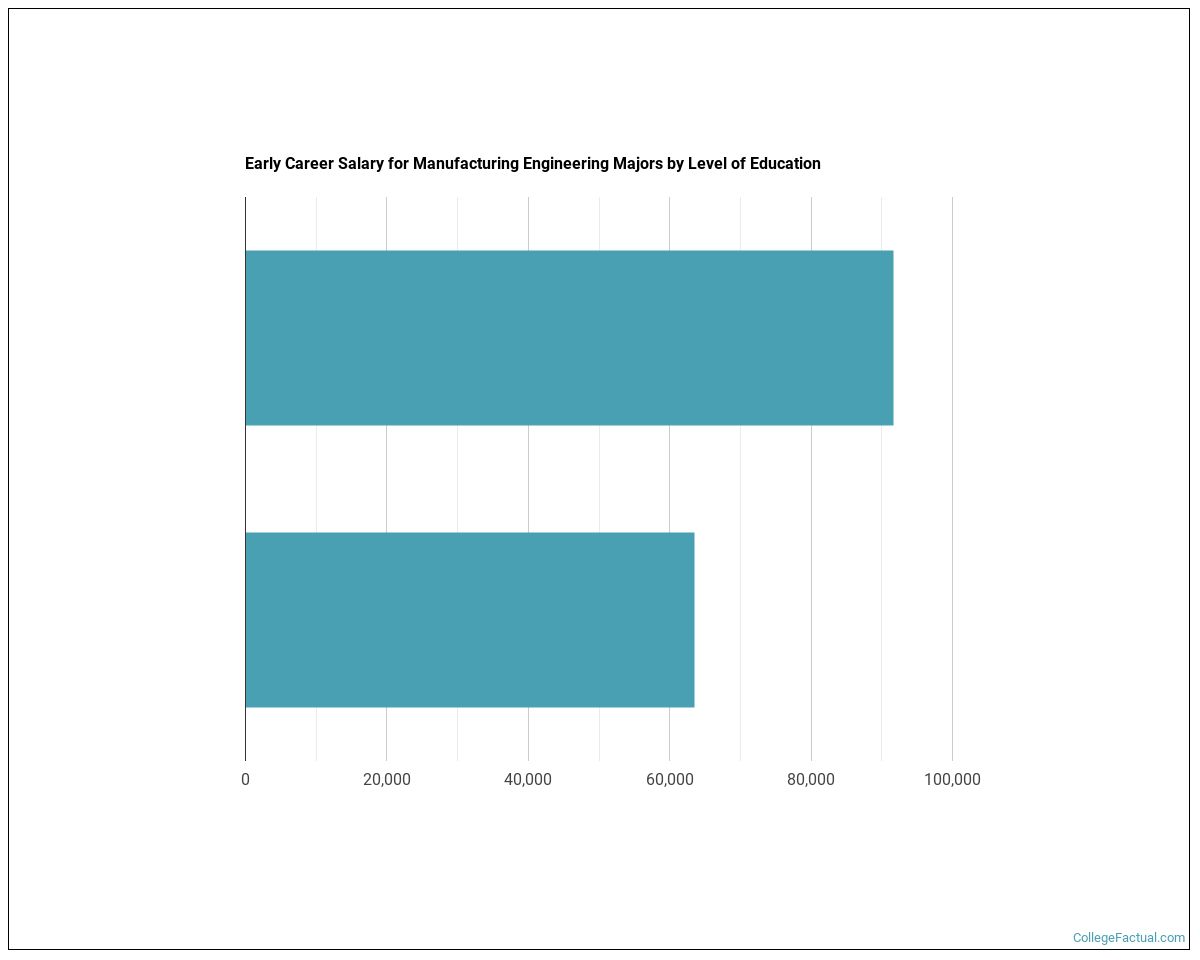
Logistics professionals are able to use both their intellects and both their hands to solve problems. They are skilled at creating sustainable supply chains. They can also influence the decision-making process at both the operational and executive levels. While the job can be hard, it can also offer great rewards. The logistics industry is growing rapidly in a booming economy.
Logistics workers need to have strong leadership and management skills. They must also be able communicate well. They will also need to be proficient with specialized software systems. They might be responsible for finding storage space close to shipping ports. They may also ensure that goods get cleared at customs.
The logistics industry is constantly evolving. New technologies and business models are changing the way the industry operates. It is essential to be able to comprehend these changes. A bachelor's will make you a more versatile logistics professional. This degree will also allow you to develop a professional network. Participation in industry conferences and seminars is also possible. A recognized institution may also grant a degree.
There are also a variety of administrative jobs, which require strong communication and analytical skills. Some roles are within the company while others involve customers, suppliers, and other business functions.
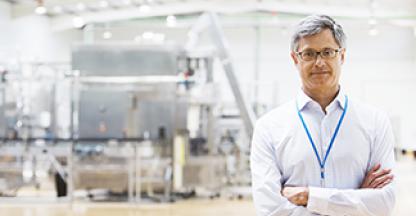
A membership in an industry association is a great way to get started in logistics. You can find information about professional certifications, industry news, and job board listings at these organizations. They may also be able to help you find a mentor. Some organizations even offer graduate fellowships.
A lot of countries offer vocational certifications which don't require any previous logistics experience. These certifications can be especially valuable to companies that own their own transport fleets. Businesses with in-house transportation fleets are also able to obtain a Certificate for Professional Competence in Road Transport Operations.
You can find entry level jobs in logistics all over the country. There are many online resources available to job seekers. You can also use your social network to help you.
FAQ
Are there any Manufacturing Processes that we should know before we can learn about Logistics?
No. No. It is important to know about the manufacturing processes in order to understand how logistics works.
What are the essential elements of running a logistics firm?
You need to have a lot of knowledge and skills to manage a successful logistic business. Good communication skills are essential to effectively communicate with your suppliers and clients. You need to understand how to analyze data and draw conclusions from it. You must be able and able to handle stress situations and work under pressure. In order to innovate and create new ways to improve efficiency, creativity is essential. You will need strong leadership skills to motivate and direct your team members towards achieving their organizational goals.
It is also important to be efficient and well organized in order meet deadlines.
Are there ways to automate parts of manufacturing?
Yes! Automation has been around since ancient times. The Egyptians discovered the wheel thousands and years ago. Robots are now used to assist us in assembly lines.
Robotics is used in many manufacturing processes today. They include:
-
Automated assembly line robots
-
Robot welding
-
Robot painting
-
Robotics inspection
-
Robots create products
Automation could also be used to improve manufacturing. 3D printing is a way to make custom products quickly and without waiting weeks or months for them to be manufactured.
What is the job of a logistics manger?
A logistics manager makes sure that all goods are delivered on-time and in good condition. This is achieved by using their knowledge and experience with the products of the company. He/she should make sure that enough stock is on hand to meet the demands.
What are the 4 types manufacturing?
Manufacturing refers to the transformation of raw materials into useful products by using machines and processes. It includes many different activities like designing, building and testing, packaging, shipping and selling, as well as servicing.
What does manufacturing industry mean?
Manufacturing Industries are companies that manufacture products. Consumers are the people who purchase these products. This is accomplished by using a variety of processes, including production, distribution and retailing. They manufacture goods from raw materials using machines and other equipment. This includes all types of manufactured goods, including food items, clothing, building supplies, furniture, toys, electronics, tools, machinery, vehicles, pharmaceuticals, medical devices, chemicals, and many others.
What does it mean to warehouse?
A warehouse is an area where goods are stored before being sold. It can be indoors or out. It may also be an indoor space or an outdoor area.
Statistics
- Job #1 is delivering the ordered product according to specifications: color, size, brand, and quantity. (netsuite.com)
- In 2021, an estimated 12.1 million Americans work in the manufacturing sector.6 (investopedia.com)
- You can multiply the result by 100 to get the total percent of monthly overhead. (investopedia.com)
- In the United States, for example, manufacturing makes up 15% of the economic output. (twi-global.com)
- Many factories witnessed a 30% increase in output due to the shift to electric motors. (en.wikipedia.org)
External Links
How To
How to use the Just In-Time Production Method
Just-in-time (JIT) is a method that is used to reduce costs and maximize efficiency in business processes. It allows you to get the right amount resources at the right time. This means you only pay what you use. Frederick Taylor was the first to coin this term. He developed it while working as a foreman during the early 1900s. After observing how workers were paid overtime for late work, he realized that overtime was a common practice. He realized that workers should have enough time to complete their jobs before they begin work. This would help increase productivity.
JIT is about planning ahead. You should have all the necessary resources ready to go so that you don’t waste money. Look at your entire project, from start to end. Make sure you have enough resources in place to deal with any unexpected problems. You can anticipate problems and have enough equipment and people available to fix them. This will prevent you from spending extra money on unnecessary things.
There are many JIT methods.
-
Demand-driven: This is a type of JIT where you order the parts/materials needed for your project regularly. This will allow for you to track the material that you have left after using it. This will allow you to calculate how long it will take to make more.
-
Inventory-based: This is a type where you stock the materials required for your projects in advance. This allows you to predict how much you can expect to sell.
-
Project-driven: This approach involves setting aside sufficient funds to cover your project's costs. Knowing how much money you have available will help you purchase the correct amount of materials.
-
Resource-based JIT: This is the most popular form of JIT. This is where you assign resources based upon demand. For instance, if you have a lot of orders coming in, you'll assign more people to handle them. If there aren't many orders, you will assign fewer people.
-
Cost-based: This is a similar approach to resource-based but you are not only concerned with how many people you have, but also how much each one costs.
-
Price-based: This approach is very similar to the cost-based method except that you don't look at individual workers costs but the total cost of the company.
-
Material-based is an alternative to cost-based. Instead of looking at the total cost in the company, this method focuses on the average amount of raw materials that you consume.
-
Time-based JIT: A variation on resource-based JIT. Instead of focusing on the cost of each employee, you will focus on the time it takes to complete a project.
-
Quality-based: This is yet another variation of resource-based JIT. Instead of thinking about how much each employee costs or how long it takes to manufacture something, you think about how good the quality of your product is.
-
Value-based JIT: One of the most recent forms of JIT. This is where you don't care about how the products perform or whether they meet customers' expectations. Instead, your focus is on the value you bring to the market.
-
Stock-based is an inventory-based system that measures the number of items produced at any given moment. This method is useful when you want to increase production while decreasing inventory.
-
Just-in time (JIT), planning: This is a combination JIT/supply chain management. This refers to the scheduling of the delivery of components as soon after they are ordered. This is important as it reduces lead time and increases throughput.