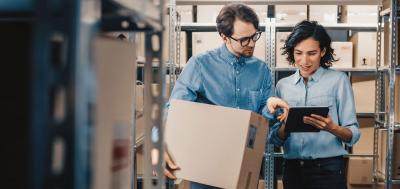
SIPOC diagram is a useful visual tool that helps to define the inputs and outputs of a business process. It also allows team members to identify gaps or improvements in business operations.
The sipoc diagram is often a part of the DMAIC process improvement cycle, which is a framework used for creating a business process that can be improved through analysis and continuous improvement. It helps teams and sponsor agree on project boundaries and the scope of a project, along with Key Process Input Variables and Key Process Output Variables.
What is SIPOC?
The SIPOC Diagram is a simple, easy-to understand visual representation of inputs and out-puts for a particular business process. Its primary purpose is to help the team understand and analyze the business process at a high level, providing a clear picture of the steps that are needed to transform inputs into desired outputs.
What is history of sipoc diagrams?
The sipoc diagram dates back to the 1980s as part of a total quality management approach (TQM), and the Six Sigma model for business process improvement. It has since been widely used in lean-manufacturing and business process improvement programmes, as it's an effective tool for streamlining, identifying improvements, and improving communications between stakeholders.
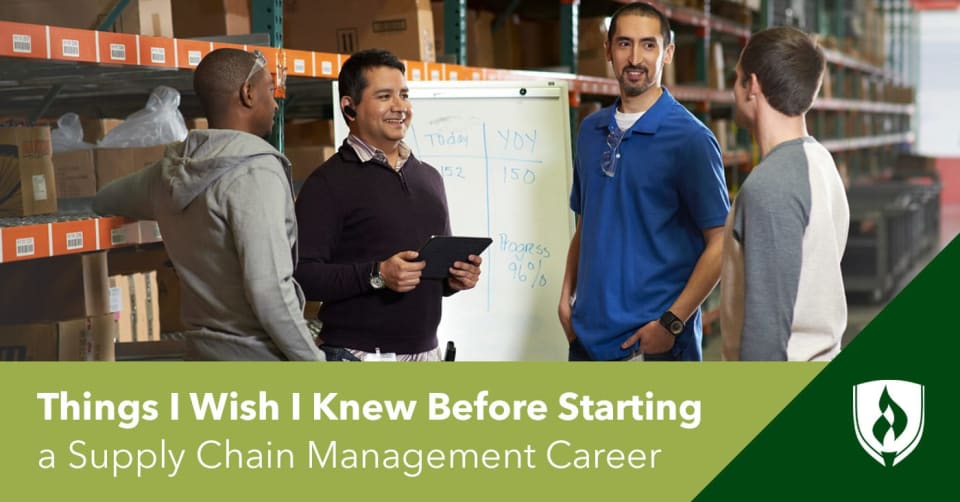
How to Make SIPOCs
To begin, you must first choose the process that you want to analyze. This will help your team and you focus on the important areas.
You'll then need to determine the inputs required to run the process and who supplies them. List all the suppliers and their contact info, as well as the raw materials each one provides to the process.
List all clients, internal and outside, who will receive the product or service. This will help you to make sure that your company provides high-quality services and products.
Inputs This is the very first section on a SIPOC and it contains all the requirements for material or information. Materials can be tangible goods like products, or they can be informational, such a report.
Outputs - This is the next section of the SIPOC diagram. It's usually a listing of the products, completed actions, or services that result from the process. Outputs should reflect what customers expect and should meet customer needs.
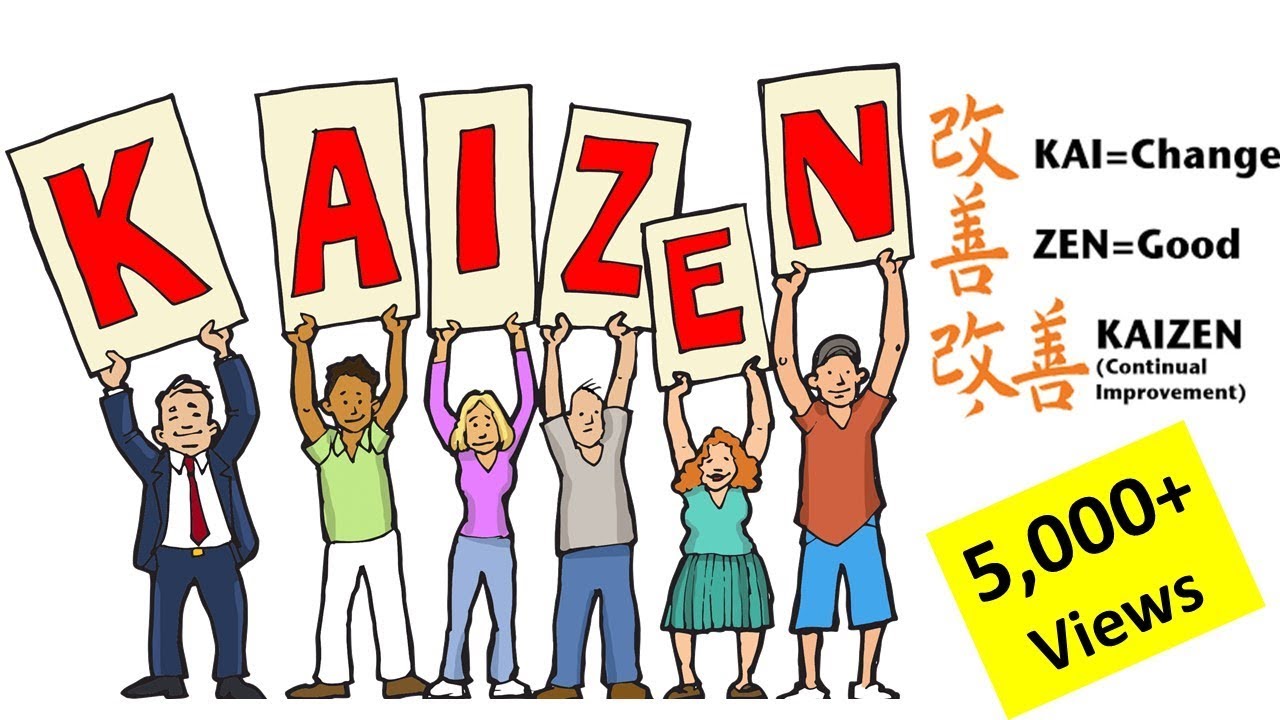
Customers: This final section of the SIPOC diagram identifies customers, both inside and outside the organization. This can include maintenance teams, line operators and internal and external clients.
A SIPOC diagram is a powerful visual tool that can be used to improve business processes and improve overall communication between all stakeholders. It's easy to create and is a great way to get team members to understand the business processes that are being examined. Use a template which includes the main components of the diagram such as inputs, outputs. By using a diagram template, you can save time by drawing the diagram quickly.
FAQ
Is it possible to automate certain parts of manufacturing
Yes! Yes. Automation has been around since ancient time. The Egyptians invented the wheel thousands of years ago. Today, robots assist in the assembly of lines.
There are many applications for robotics in manufacturing today. These include:
-
Robots for assembly line
-
Robot welding
-
Robot painting
-
Robotics inspection
-
Robots that produce products
Manufacturing could also benefit from automation in other ways. For example, 3D printing allows us to make custom products without having to wait for weeks or months to get them manufactured.
What jobs are available in logistics?
There are many kinds of jobs available within logistics. Here are some examples:
-
Warehouse workers - They load and unload trucks and pallets.
-
Transportation drivers - They drive trucks and trailers to deliver goods and carry out pick-ups.
-
Freight handlers - They sort and pack freight in warehouses.
-
Inventory managers - They oversee the inventory of goods in warehouses.
-
Sales representatives - They sell products to customers.
-
Logistics coordinators - They plan and organize logistics operations.
-
Purchasing agents are those who purchase goods and services for the company.
-
Customer service representatives are available to answer customer calls and emails.
-
Shipping clerks – They process shipping orders, and issue bills.
-
Order fillers - They fill orders based on what is ordered and shipped.
-
Quality control inspectors (QCI) - They inspect all incoming and departing products for potential defects.
-
Others - There are many other types of jobs available in logistics, such as transportation supervisors, cargo specialists, etc.
How can manufacturing reduce production bottlenecks?
Production bottlenecks can be avoided by ensuring that processes are running smoothly during the entire production process, starting with the receipt of an order and ending when the product ships.
This includes planning to meet capacity requirements and quality control.
The best way to do this is to use continuous improvement techniques such as Six Sigma.
Six Sigma management is a system that improves quality and reduces waste within your organization.
It seeks to eliminate variation and create consistency in your work.
What are the four types in manufacturing?
Manufacturing is the process that transforms raw materials into useful products. Manufacturing involves many activities, including designing, building, testing and packaging, shipping, selling, service, and so on.
What is the importance of logistics in manufacturing?
Logistics are an essential component of any business. They help you achieve great results by helping you manage all aspects of product flow, from raw materials to finished goods.
Logistics also play a major role in reducing costs and increasing efficiency.
Statistics
- In the United States, for example, manufacturing makes up 15% of the economic output. (twi-global.com)
- It's estimated that 10.8% of the U.S. GDP in 2020 was contributed to manufacturing. (investopedia.com)
- Many factories witnessed a 30% increase in output due to the shift to electric motors. (en.wikipedia.org)
- [54][55] These are the top 50 countries by the total value of manufacturing output in US dollars for its noted year according to World Bank.[56] (en.wikipedia.org)
- Job #1 is delivering the ordered product according to specifications: color, size, brand, and quantity. (netsuite.com)
External Links
How To
How to use Lean Manufacturing in the production of goods
Lean manufacturing is a management style that aims to increase efficiency and reduce waste through continuous improvement. It was developed by Taiichi Okono in Japan, during the 1970s & 1980s. TPS founder Kanji Takoda awarded him the Toyota Production System Award (TPS). Michael L. Watkins published the "The Machine That Changed the World", the first book about lean manufacturing. It was published in 1990.
Lean manufacturing can be described as a set or principles that are used to improve quality, speed and cost of products or services. It is about eliminating defects and waste from all stages of the value stream. The five-steps of Lean Manufacturing are just-in time (JIT), zero defect and total productive maintenance (TPM), as well as 5S. Lean manufacturing focuses on eliminating non-value-added activities such as rework, inspection, and waiting.
Lean manufacturing not only improves product quality but also reduces costs. Companies can also achieve their goals faster by reducing employee turnover. Lean manufacturing has been deemed one of the best ways to manage the entire value-chain, including customers, distributors as well retailers and employees. Lean manufacturing can be found in many industries. Toyota's philosophy is a great example of this. It has helped to create success in automobiles as well electronics, appliances and healthcare.
Five basic principles of Lean Manufacturing are included in lean manufacturing
-
Define Value - Identify the value your business adds to society and what makes you different from competitors.
-
Reduce Waste - Eliminate any activity that doesn't add value along the supply chain.
-
Create Flow - Make sure work runs smoothly without interruptions.
-
Standardize and simplify - Make your processes as consistent as possible.
-
Building Relationships – Establish personal relationships with both external and internal stakeholders.
Although lean manufacturing has always been around, it is gaining popularity in recent years because of a renewed interest for the economy after 2008's global financial crisis. Many companies have adopted lean manufacturing methods to increase their marketability. According to some economists, lean manufacturing could be a significant factor in the economic recovery.
Lean manufacturing has many benefits in the automotive sector. These include better customer satisfaction and lower inventory levels. They also result in lower operating costs.
It can be applied to any aspect of an organisation. Lean manufacturing is most useful in the production sector of an organisation because it ensures that each step in the value-chain is efficient and productive.
There are three main types in lean manufacturing
-
Just-in-Time Manufacturing (JIT): This type of lean manufacturing is commonly referred to as "pull systems." JIT is a method in which components are assembled right at the moment of use, rather than being manufactured ahead of time. This strategy aims to decrease lead times, increase availability of parts and reduce inventory.
-
Zero Defects Manufacturing (ZDM),: ZDM is a system that ensures no defective units are left the manufacturing facility. If a part is required to be repaired on the assembly line, it should not be scrapped. This is true even for finished products that only require minor repairs prior to shipping.
-
Continuous Improvement: Continuous Improvement aims to improve efficiency by continually identifying problems and making adjustments to eliminate or minimize waste. Continuous improvement involves continuous improvement of processes and people as well as tools.