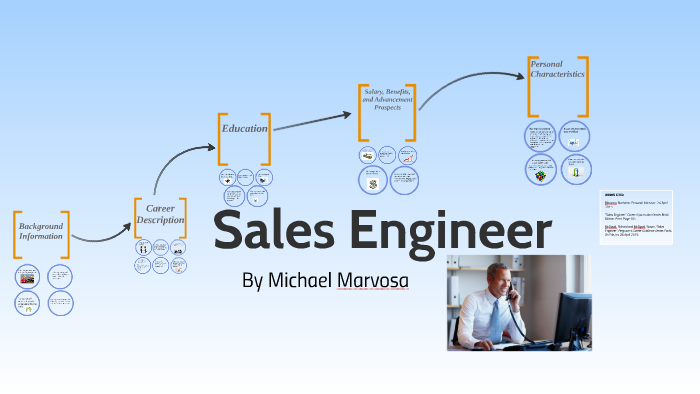
In order to stay in business, companies must continue to look for ways to improve. There are many ways that a business can improve its operations, from productivity to communication and operations.
Operational Excellence is a management method that aims to improve every aspect of a company's operation. This includes reducing wastage, improving processes and creating efficient workflows in order to boost efficiency.
The term operational excellence is derived from the management theory of scientific management, which originated in the 18th century and was influenced by the likes of Adam Smith, Frederick Winslow Taylor and Henry Ford. It is a process that takes years to implement and requires a lot of trial and error, but it is worth the effort.
What is operational excellence?
According to the Institute for Operational Excellence, operational excellence is the ability to monitor product and information flow within an organization. The Institute for Operational Excellence defines operational excellence as the ability to monitor product and information flow within an organization.
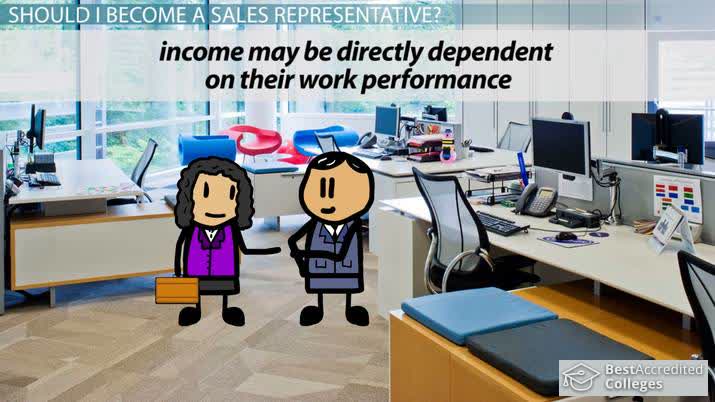
To create a culture that is based on operational excellence, a cultural change is needed. Building trust with employees is a long-term process that takes time. It also involves a new leadership style, and a different behavior. However, it is incredibly important to achieve long-term success.
What Is the Role of Operational Excellence Staff?
The operational excellence team is responsible for implementing strategy within the organization. Their responsibilities involve overseeing improvement processes, participating in cross functional project teams, defining metrics and monitoring them, cultivating culture and mentoring operational excellence leaders.
They may also lead projects based on improvement methodologies such as Six Sigma and Kaizen. These methods have the potential to be extremely effective in improving efficiency. But they require highly trained staff in areas like project management and business analytics.
How to Create an Operational Excellence Plan
A plan of operational excellence must include a set of methodologies that will enable you to achieve your goals in the shortest time possible. This is especially true if you are looking to reduce waste, improve your workflows or enhance your customer experience.
To track your progress, you can use different KPIs. These should be relevant and achievable for your employees in order to inspire them to strive to achieve excellence.
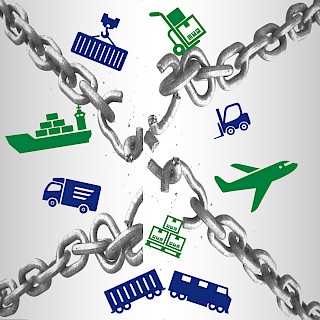
The use of these tools will make sure that your operation is as efficient and as cost-effectively as possible. The tools also allow you to collect feedback from your staff on the front lines so that you may continue to improve.
How to Measure Your Operational Excellence Goals
Most directors of operations will use a combination of financial and operational data at a high level, along with qualitative information from employee and customer surveys. This will give them an accurate picture of where they stand and how close they come to achieving their targets.
The reason for this is that operational excellence can be found at all levels of the organization. Therefore, it's essential to have individual targets set by each member of your team. For example, a Director of Operations needs to have a profit target around what they spend on people, while a project manager should have their own targets around billable and non-billable work. It is possible to measure operational excellence across the entire business and ensure that costs are balanced with revenue.
FAQ
What skills should a production planner have?
Being a production planner is not easy. You need to be organized and flexible. It is also important to be able communicate with colleagues and clients.
What is production plan?
Production Planning is the creation of a plan to cover all aspects, such as scheduling, budgeting. Location, crew, equipment, props and other details. It is important to have everything ready and planned before you start shooting. This document should include information about how to achieve the best results on-set. This includes information on shooting times, locations, cast lists and crew details.
It is important to first outline the type of film you would like to make. You may have already chosen the location you want, or there are locations or sets you prefer. Once you have identified your locations and scenes, you can start working out which elements you require for each scene. One example is if you are unsure of the exact model you want but decide that you require a car. If this is the case, you might start searching online for car models and then narrow your options by selecting from different makes.
Once you have found the right vehicle, you can think about adding accessories. Do you need people sitting in the front seats? Maybe you need someone to move around in the back. Perhaps you would like to change the interior colour from black to white. These questions will help you determine the exact look and feel of your car. The type of shots that you are looking for is another thing to consider. Do you want to film close-ups, or wider angles? Maybe you want to show your engine or the steering wheel. These things will help you to identify the car that you are looking for.
Once you have established all the details, you can create a schedule. You can use a schedule to determine when and where you need it to be shot. Each day will include the time when you need to arrive at the location, when you need to leave and when you need to return home. Everyone will know what they need and when. Hire extra staff by booking them ahead of time. You should not hire anyone who doesn't show up because of your inaction.
It is important to calculate the amount of filming days when you are creating your schedule. Some projects only take one or two days, while others may last weeks. It is important to consider whether you require more than one photo per day when you create your schedule. Multiple shots at the same location can increase costs and make it more difficult to complete. If you aren't sure whether you need multiple shots, it is best to take fewer photos than you would like.
Budget setting is an important part of production planning. Setting a realistic budget is essential as it will allow you to work within your means. If you have to reduce your budget due to unexpected circumstances, you can always lower it later. However, it is important not to overestimate the amount that you will spend. You will end up spending less money if you underestimate the cost of something.
Production planning is a detailed process. But, once you understand the workings of everything, it becomes easier for future projects to be planned.
What does it mean to warehouse?
A warehouse, or storage facility, is where goods are stored prior to being sold. It can be either an indoor or outdoor space. Sometimes, it can be both an indoor and outdoor space.
How important is automation in manufacturing?
Not only is automation important for manufacturers, but it's also vital for service providers. It enables them to provide services faster and more efficiently. In addition, it helps them reduce costs by reducing human errors and improving productivity.
What type of jobs is there in logistics
Logistics can offer many different jobs. These are some of the jobs available in logistics:
-
Warehouse workers - They load trucks and pallets.
-
Transportation drivers - They drive trucks and trailers to deliver goods and carry out pick-ups.
-
Freight handlers - They sort and pack freight in warehouses.
-
Inventory managers: They are responsible for the inventory and management of warehouses.
-
Sales representatives: They sell products to customers.
-
Logistics coordinators are responsible for organizing and planning logistics operations.
-
Purchasing agents - They buy goods and services that are necessary for company operations.
-
Customer service representatives – They answer emails and phone calls from customers.
-
Shipping clerks – They process shipping orders, and issue bills.
-
Order fillers - They fill orders based on what is ordered and shipped.
-
Quality control inspectors – They inspect incoming and outgoing products to ensure that there are no defects.
-
Others – There are many other types available in logistics. They include transport supervisors, cargo specialists and others.
Statistics
- It's estimated that 10.8% of the U.S. GDP in 2020 was contributed to manufacturing. (investopedia.com)
- Job #1 is delivering the ordered product according to specifications: color, size, brand, and quantity. (netsuite.com)
- [54][55] These are the top 50 countries by the total value of manufacturing output in US dollars for its noted year according to World Bank.[56] (en.wikipedia.org)
- (2:04) MTO is a production technique wherein products are customized according to customer specifications, and production only starts after an order is received. (oracle.com)
- In 2021, an estimated 12.1 million Americans work in the manufacturing sector.6 (investopedia.com)
External Links
How To
How to use 5S to increase Productivity in Manufacturing
5S stands for "Sort", "Set In Order", "Standardize", "Separate" and "Store". Toyota Motor Corporation developed the 5S method in 1954. It allows companies to improve their work environment, thereby achieving greater efficiency.
This approach aims to standardize production procedures, making them predictable, repeatable, and easily measurable. This means that daily tasks such as cleaning and sorting, storage, packing, labeling, and packaging are possible. Workers can be more productive by knowing what to expect.
Implementing 5S involves five steps: Sort, Set in Order, Standardize Separate, Store, and Each step requires a different action, which increases efficiency. If you sort items, it makes them easier to find later. Once you have placed items in an ordered fashion, you will put them together. Next, organize your inventory into categories and store them in containers that are easily accessible. Make sure everything is correctly labeled when you label your containers.
Employees will need to be more critical about their work. Employees need to be able understand their motivations and discover alternative ways to do them. To implement the 5S system, employees must acquire new skills and techniques.
In addition to increasing efficiency, the 5S method also improves morale and teamwork among employees. They feel more motivated to work towards achieving greater efficiency as they see the results.