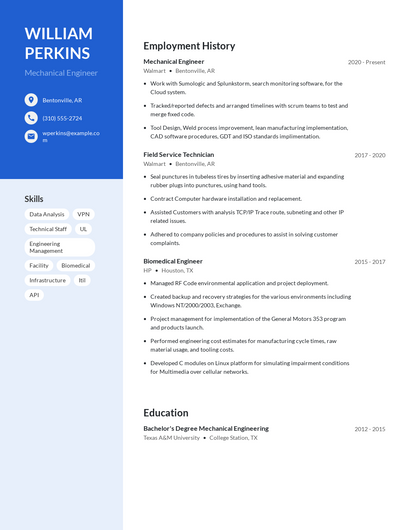
The food manufacturing industry employs many professionals and managers. Top executives organize and make decisions about production. Industrial production managers direct the day-to-day operation of a manufacturing plant. Marketing, public relations and sales managers oversee marketing, promotional and sales programs.
Jobs in the food manufacturing industry
New York has many jobs in food manufacturing. The top three occupations include bakers, food batchmakers, and packaging and filling machine operators. These occupations make up just about half of all food manufacturing jobs in the state. Food manufacturing employment increased across the state in seven out 10 labor markets.
A rising number of food manufacturing jobs is correlated with a improving job market. In February, there was a 3.8% unemployment rate, the lowest point in more than ten years. The largest increase in food manufacturing employment was in the nondurable goods industry, with companies hiring 16,000 more workers.

Average salaries for workers in this industry
Workers in food manufacturing earn an average of $26,000 to $52,000 annually, while the highest-paid earn $52,000 annually. This range is higher for people with more experience. The lowest earners make less than $26,000 each year. Food Factory Workers' salaries are not as high as other jobs in the manufacturing sector, but they are generally within the same range.
In the last few years, average wages have increased in this industry. The manufacturing industry plays a vital role in our economy. But it's not an industry that is isolated. Workers' lives are affected by the economic sector. It is therefore important to learn how these sectors relate to one another.
Localities with the greatest number of workers
In 2013, three New York State labor market areas were home to food manufacturing firms: the Finger Lakes (the Southern Tier), and Western New York (the Western New York). Combined, these three regions employed almost half the food manufacturing workforce. These regions saw high concentrations of food production. The highest average wages were found in the Hudson Valley Southern Tier, Western New York and Western New York.
Food processing requires skilled labor. Food manufacturing companies have difficulty finding skilled workers because of the lack of workers in certain areas. Not only is it hard to find people to work in distribution trucks and other lower-level positions, but it's also becoming increasingly difficult to fill more senior positions. Career site CareersInFood.com has revealed that there have been 12% more open positions in food manufacturing in the past year than the previous 24 months, and 37% more in the last 24.
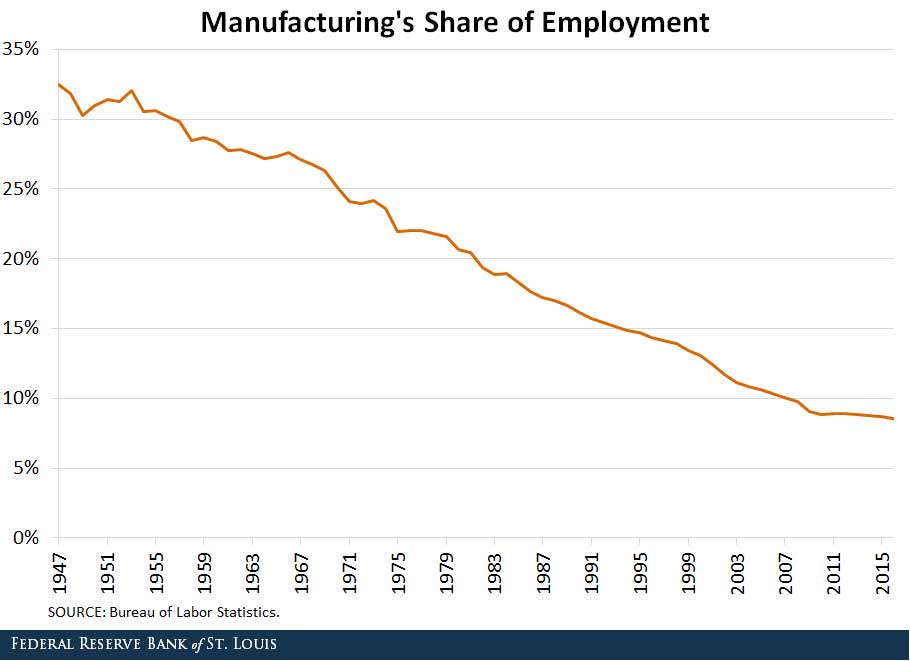
Number of workers in the industry
According to the Bureau of Labor Statistics, the number of workers in the food manufacturing industry increased by 7.200 in February, a growth of over 1% from January. This month marks the third consecutive month with job gains in this industry. However, it is still struggling to recover from several headwinds. The COVID-19 pandemic, a labor shortage, and the global recession have all affected the industry's employment. According to the Bureau of Labor Statistics the industry employed 40.700 people in February.
New York State saw an increase in food manufacturing firms by 8% from 2003 to 2013. The four largest growth areas in New York State's labor market were the Southern Tier (Hudson Valley) and the Southern Tier (Tier 1).
FAQ
Can we automate some parts of manufacturing?
Yes! Yes. The wheel was invented by the Egyptians thousands of years ago. Nowadays, we use robots for assembly lines.
There are many applications for robotics in manufacturing today. These include:
-
Automation line robots
-
Robot welding
-
Robot painting
-
Robotics inspection
-
Robots that create products
Automation can be applied to manufacturing in many other ways. 3D printing, for example, allows us to create custom products without waiting for them to be made.
How can manufacturing overproduction be reduced?
It is essential to find better ways to manage inventory to reduce overproduction. This would reduce the time needed to manage inventory. This will allow us to free up resources for more productive tasks.
Kanban systems are one way to achieve this. A Kanban board, a visual display to show the progress of work, is called a Kanban board. Kanban systems allow work items to move through different states until they reach their final destination. Each state represents a different priority level.
If work is moving from one stage to the other, then the current task can be completed and moved on to the next. It is possible to keep a task in the beginning stages until it gets to the end.
This allows work to move forward and ensures that no work is missed. Managers can monitor the work being done by Kanban boards to see what is happening at any given time. This information allows them to adjust their workflow based on real-time data.
Lean manufacturing, another method to control inventory levels, is also an option. Lean manufacturing focuses on eliminating waste throughout the entire production chain. Waste includes anything that does not add value to the product. There are several types of waste that you might encounter:
-
Overproduction
-
Inventory
-
Unnecessary packaging
-
Materials in excess
Manufacturers can increase efficiency and decrease costs by implementing these ideas.
What is the importance of logistics in manufacturing?
Logistics are an integral part any business. They can help you achieve great success by helping you manage product flow from raw material to finished goods.
Logistics play an important role in reducing costs as well as increasing efficiency.
What is the job of a manufacturer manager?
A manufacturing manager has to ensure that all manufacturing processes work efficiently and effectively. They should also be aware of any problems within the company and act accordingly.
They should also be able communicate with other departments, such as sales or marketing.
They should be up to date on the latest trends and be able apply this knowledge to increase productivity and efficiency.
What is the responsibility of a production planner?
Production planners make sure that every aspect of the project is delivered on-time, within budget, and within schedule. They also ensure the quality of the product and service meets the client's requirements.
How can manufacturing efficiency be improved?
First, identify the factors that affect production time. Next, we must find ways to improve those factors. If you don’t know how to start, look at which factors have the greatest impact upon production time. Once you have identified them, it is time to identify solutions.
What are the requirements to start a logistics business?
A successful logistics business requires a lot more than just knowledge. Good communication skills are essential to effectively communicate with your suppliers and clients. You need to understand how to analyze data and draw conclusions from it. You will need to be able handle pressure well and work in stressful situations. To improve efficiency, you must be innovative and creative. Strong leadership qualities are essential to motivate your team and help them achieve their organizational goals.
You must be organized to meet tight deadlines.
Statistics
- According to a Statista study, U.S. businesses spent $1.63 trillion on logistics in 2019, moving goods from origin to end user through various supply chain network segments. (netsuite.com)
- According to the United Nations Industrial Development Organization (UNIDO), China is the top manufacturer worldwide by 2019 output, producing 28.7% of the total global manufacturing output, followed by the United States, Japan, Germany, and India.[52][53] (en.wikipedia.org)
- In 2021, an estimated 12.1 million Americans work in the manufacturing sector.6 (investopedia.com)
- It's estimated that 10.8% of the U.S. GDP in 2020 was contributed to manufacturing. (investopedia.com)
- (2:04) MTO is a production technique wherein products are customized according to customer specifications, and production only starts after an order is received. (oracle.com)
External Links
How To
How to Use the Just In Time Method in Production
Just-intime (JIT), which is a method to minimize costs and maximize efficiency in business process, is one way. It's a way to ensure that you get the right resources at just the right time. This means that you only pay for what you actually use. Frederick Taylor, a 1900s foreman, first coined the term. He saw how overtime was paid to workers for work that was delayed. He decided to ensure workers have enough time to do their jobs before starting work to improve productivity.
JIT is an acronym that means you need to plan ahead so you don’t waste your money. You should also look at the entire project from start to finish and make sure that you have sufficient resources available to deal with any problems that arise during the course of your project. If you expect problems to arise, you will be able to provide the necessary equipment and personnel to address them. This way, you won't end up paying extra money for things that weren't really necessary.
There are many JIT methods.
-
Demand-driven JIT: You order the parts and materials you need for your project every other day. This will allow to track how much material has been used up. You'll also be able to estimate how long it will take to produce more.
-
Inventory-based: This type allows you to stock the materials needed for your projects ahead of time. This allows for you to anticipate how much you can sell.
-
Project-driven: This is an approach where you set aside enough funds to cover the cost of your project. When you know how much you need, you'll purchase the appropriate amount of materials.
-
Resource-based JIT: This is the most popular form of JIT. Here you can allocate certain resources based purely on demand. If you have many orders, you will assign more people to manage them. If there aren't many orders, you will assign fewer people.
-
Cost-based: This approach is very similar to resource-based. However, you don't just care about the number of people you have; you also need to consider how much each person will cost.
-
Price-based: This is similar to cost-based but instead of looking at individual workers' salaries, you look at the total company price.
-
Material-based is an alternative to cost-based. Instead of looking at the total cost in the company, this method focuses on the average amount of raw materials that you consume.
-
Time-based: Another variation of resource-based JIT. Instead of focusing only on how much each employee is costing, you should focus on how long it takes to complete your project.
-
Quality-based JIT is another variant of resource-based JIT. Instead of thinking about the cost of each employee or the time it takes to produce something, you focus on how good your product quality.
-
Value-based JIT: One of the most recent forms of JIT. In this case, you're not concerned with how well the products perform or whether they meet customer expectations. Instead, you're focused on how much value you add to the market.
-
Stock-based: This is an inventory-based method that focuses on the actual number of items being produced at any given time. It's useful when you want maximum production and minimal inventory.
-
Just-intime (JIT), planning is a combination JIT management and supply chain management. It is the process of scheduling components' delivery as soon as they have been ordered. This is important as it reduces lead time and increases throughput.