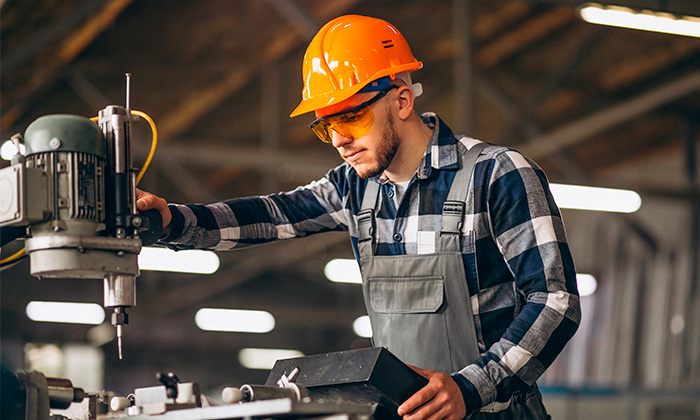
Visual management involves the transmission of information via visual signals. This process helps to increase efficiency and clarity, as information is instantly recognized. There are several types of visual control, including: process control charts, FIFO lane, and Lean daily management board. Here are some examples. You can also read about visual control in Lean manufacturing. Learn more. This is a great method to help your company get on the right track with lean manufacturing.
Lean manufacturing
One of the many methods used for visual management in lean manufacturing is the use of Andon, a Japanese word for status-display visualization. This allows workers and supervisors to see the work-in-progress, process flow, as well as other important information. Visual management allows for easy labeling of workspaces and materials as well as parts, finished goods, or waste. It helps to streamline processes and identify inefficiencies. These are just a few of the benefits that visual management can bring to lean manufacturing.
Lean methodologies require visible tools for visual control. Clear visual signals help supervisors and operators identify waste, improve process flow, and avoid errors. It can also reduce safety risks. By looking at floor markings or other visual indicators, forklift drivers can ensure they are in the right place. Workers can work more efficiently by using visual management when lean manufacturing is used. Visual management can reduce waste as well as minimize safety risks.
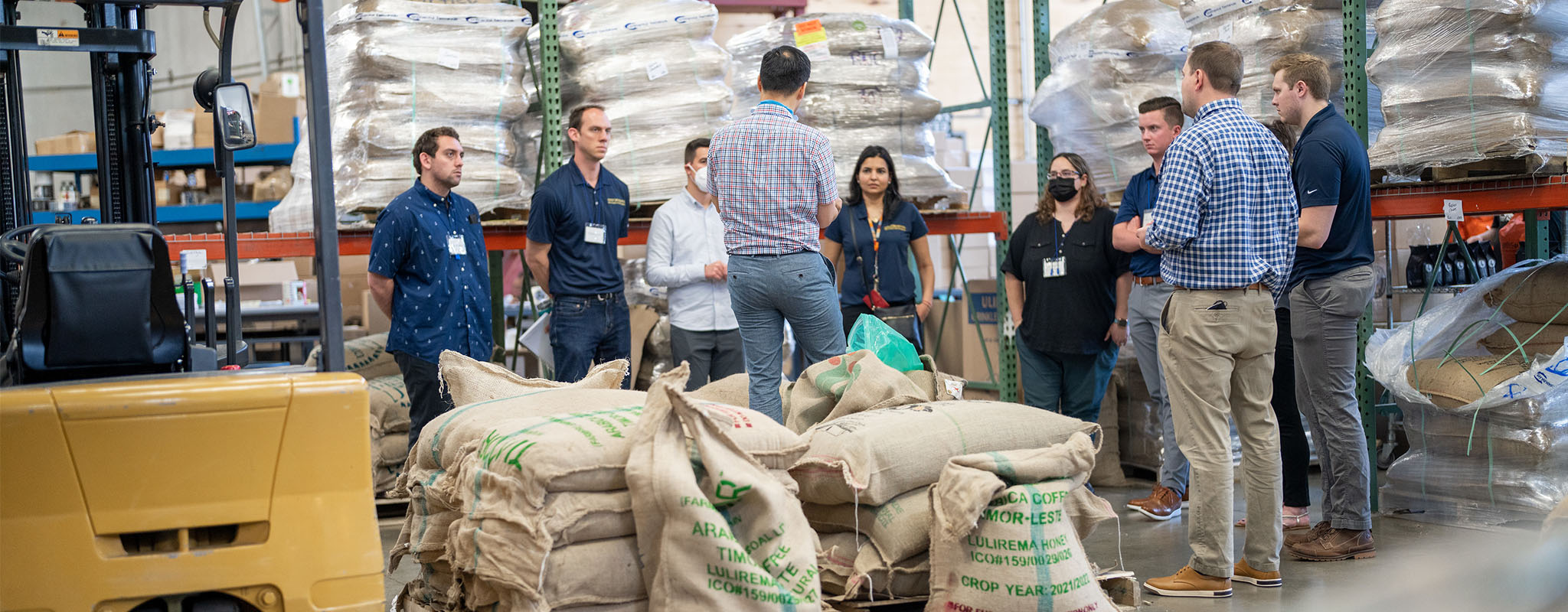
Process control charts
Process control charts can be an effective tool to visualize performance metrics, set a baseline for future improvements, and improve output. They are a way for managers, operators, and all other stakeholders to communicate and agree on common causes and the best path forward. Because of their unusual patterns of variation, these charts can be very useful in identifying out-of-control processes. These charts can be useful for visual management as they are easy to create and can be used in order to visualize any system or process.
A control chart's primary purpose is to monitor the process' performance over time. These charts display the sequence of samples and measurements that allow managers to determine whether or not the process is stable. These charts can also be used as an analytical tool to spot potential problems and offer solutions. An operator can use the centerline of the control charts to compare the process's performance against its baseline. The control limits usually have three standard deviations from the centerline.
FIFO lane
FIFO lanes are a way to increase system throughput and utilization. You can think of a factory line or a fast food counter. Many of you will have been frustrated by the long lines that can be formed to get your food. The FiFo lane helps you manage the flow of work by establishing priority in queues by using visual management. You can create these lanes by using paint lines, marking roller conveyors or clearly marking shelves. Process A would send the first job to the first position in a FIFO lane. The next job would be taken into the next available position.
Time registration is one way to improve FIFO lane visual control. Employees can track the date and time that carts are placed in a FIFO lane by recording the time and date. Some employees use digital clocks to count the number of products immediately after putting them in the FIFO lane. You can also install whiteboard stickers to write down times on carts. These stickers can be used by downstream employees to write down times on carts.
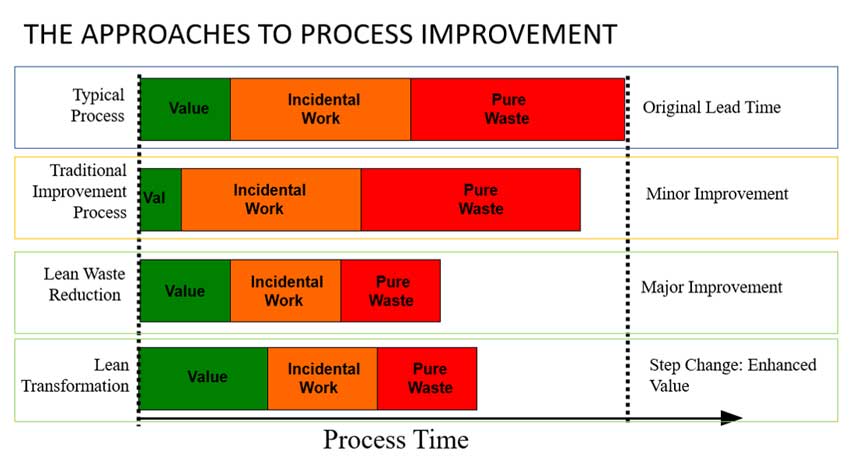
Lean daily management board
A multidisciplinary team created the Lean Daily Management Board based on five predetermined metrics. These were patient outcomes, documentation compliance, employee engagement and productivity. Each day, the team met to review each area's progress. To verify every daily activity, the team used a checklist. They used a problem solving instrument to deal with any unexpected events. The initial data collected in January 2014 noted a medication scan rate of 75% and a fall rate of 1.32/1000 patient days. However, these data did not pertain to patient care or continuing education.
Rather than simply looking at a process' performance over a long period of time, daily management makes it visible and enables managers to respond to problems as they occur. Poor performers do not want to be required to do more. By making stretching work visible, the poor performers have to account for the extra time and effort they have to spend on the work. Although daily management is not intended to be punitive it does point out inefficient and ineffective processes. People issues should not be ignored by those who can't point to a problem in a process.
FAQ
What are the essential elements of running a logistics firm?
To run a successful logistics company, you need a lot knowledge and skills. You must have good communication skills to interact effectively with your clients and suppliers. It is important to be able to analyse data and draw conclusions. You must be able manage stress and pressure under pressure. In order to innovate and create new ways to improve efficiency, creativity is essential. You will need strong leadership skills to motivate and direct your team members towards achieving their organizational goals.
To meet tight deadlines, you must also be efficient and organized.
Why automate your warehouse
Automation has become increasingly important in modern warehousing. E-commerce has increased the demand for quicker delivery times and more efficient processes.
Warehouses must adapt quickly to meet changing customer needs. To do so, they must invest heavily in technology. The benefits of automating warehouses are numerous. These are just a few reasons to invest in automation.
-
Increases throughput/productivity
-
Reduces errors
-
Accuracy is improved
-
Safety Boosts
-
Eliminates bottlenecks
-
Allows companies scale more easily
-
Increases efficiency of workers
-
Provides visibility into everything that happens in the warehouse
-
Enhances customer experience
-
Improves employee satisfaction
-
It reduces downtime, and increases uptime
-
High quality products delivered on-time
-
Human error can be eliminated
-
This helps to ensure compliance with regulations
What are the jobs in logistics?
There are many jobs available in logistics. Here are some:
-
Warehouse workers – They load, unload and transport pallets and trucks.
-
Transportation drivers: They drive trucks and trailers and deliver goods and make pick-ups.
-
Freight handlers are people who sort and pack freight into warehouses.
-
Inventory managers: They are responsible for the inventory and management of warehouses.
-
Sales reps - They sell products and services to customers.
-
Logistics coordinators - They organize and plan logistics operations.
-
Purchasing agents: They are responsible for purchasing goods and services to support company operations.
-
Customer service representatives are available to answer customer calls and emails.
-
Shippers clerks - They process shipping order and issue bills.
-
Order fillers - They fill orders based on what is ordered and shipped.
-
Quality control inspectors are responsible for inspecting incoming and outgoing products looking for defects.
-
Other - Logistics has many other job opportunities, including transportation supervisors, logistics specialists, and cargo specialists.
What does it mean to warehouse?
A warehouse, or storage facility, is where goods are stored prior to being sold. It can be indoors or out. In some cases, it may be a combination of both.
How can manufacturing excess production be decreased?
Better inventory management is key to reducing excess production. This would reduce the amount of time spent on unnecessary activities such as purchasing, storing, and maintaining excess stock. We could use these resources to do other productive tasks.
This can be done by using a Kanban system. A Kanban board, a visual display to show the progress of work, is called a Kanban board. Work items are moved through various states to reach their destination in a Kanban system. Each state represents a different priority level.
To illustrate, work can move from one stage or another when it is complete enough for it to be moved to a new stage. If a task is still in its beginning stages, it will continue to be so until it reaches the end.
This helps to keep work moving forward while ensuring that no work is left behind. With a Kanban board, managers can see exactly how much work is being done at any given moment. This data allows them adjust their workflow based upon real-time data.
Lean manufacturing can also be used to reduce inventory levels. Lean manufacturing focuses on eliminating waste throughout the entire production chain. Anything that does not contribute to the product's value is considered waste. Here are some examples of common types.
-
Overproduction
-
Inventory
-
Packaging not required
-
Overstock materials
These ideas will help manufacturers increase efficiency and lower costs.
How can efficiency in manufacturing be improved?
The first step is to determine the key factors that impact production time. We must then find ways that we can improve these factors. If you don’t know where to begin, consider which factors have the largest impact on production times. Once you have identified them, it is time to identify solutions.
What are the responsibilities of a manufacturing manager
A manufacturing manager must ensure that all manufacturing processes are efficient and effective. They should be alert for any potential problems in the company and react accordingly.
They should also know how to communicate with other departments such as sales and marketing.
They should also be aware of the latest trends in their industry and be able to use this information to help improve productivity and efficiency.
Statistics
- According to the United Nations Industrial Development Organization (UNIDO), China is the top manufacturer worldwide by 2019 output, producing 28.7% of the total global manufacturing output, followed by the United States, Japan, Germany, and India.[52][53] (en.wikipedia.org)
- (2:04) MTO is a production technique wherein products are customized according to customer specifications, and production only starts after an order is received. (oracle.com)
- You can multiply the result by 100 to get the total percent of monthly overhead. (investopedia.com)
- It's estimated that 10.8% of the U.S. GDP in 2020 was contributed to manufacturing. (investopedia.com)
- In the United States, for example, manufacturing makes up 15% of the economic output. (twi-global.com)
External Links
How To
How to Use lean manufacturing in the Production of Goods
Lean manufacturing refers to a method of managing that seeks to improve efficiency and decrease waste. It was developed in Japan during the 1970s and 1980s by Taiichi Ohno, who received the Toyota Production System (TPS) award from TPS founder Kanji Toyoda. Michael L. Watkins published the original book on lean manufacturing, "The Machine That Changed the World," in 1990.
Lean manufacturing, often described as a set and practice of principles, is aimed at improving the quality, speed, cost, and efficiency of products, services, and other activities. It is about eliminating defects and waste from all stages of the value stream. Just-in-time (JIT), zero defect (TPM), and 5S are all examples of lean manufacturing. Lean manufacturing seeks to eliminate non-value added activities, such as inspection, work, waiting, and rework.
Lean manufacturing can help companies improve their product quality and reduce costs. Additionally, it helps them achieve their goals more quickly and reduces employee turnover. Lean manufacturing has been deemed one of the best ways to manage the entire value-chain, including customers, distributors as well retailers and employees. Lean manufacturing can be found in many industries. Toyota's philosophy is a great example of this. It has helped to create success in automobiles as well electronics, appliances and healthcare.
Five fundamental principles underlie lean manufacturing.
-
Define Value - Identify the value your business adds to society and what makes you different from competitors.
-
Reduce Waste - Eliminate any activity that doesn't add value along the supply chain.
-
Create Flow. Ensure that your work is uninterrupted and flows seamlessly.
-
Standardize & Simplify - Make processes as consistent and repeatable as possible.
-
Build Relationships - Establish personal relationships with both internal and external stakeholders.
Although lean manufacturing has always been around, it is gaining popularity in recent years because of a renewed interest for the economy after 2008's global financial crisis. Many companies have adopted lean manufacturing methods to increase their marketability. According to some economists, lean manufacturing could be a significant factor in the economic recovery.
Lean manufacturing, which has many benefits, is now a standard practice in the automotive industry. These include better customer satisfaction and lower inventory levels. They also result in lower operating costs.
Any aspect of an enterprise can benefit from Lean manufacturing. However, it is particularly useful when applied to the production side of an organization because it ensures that all steps in the value chain are efficient and effective.
There are three types of lean manufacturing.
-
Just-in-Time Manufacturing (JIT): This type of lean manufacturing is commonly referred to as "pull systems." JIT refers to a system in which components are assembled at the point of use instead of being produced ahead of time. This approach is designed to reduce lead times and increase the availability of components. It also reduces inventory.
-
Zero Defects Manufacturing (ZDM),: ZDM is a system that ensures no defective units are left the manufacturing facility. Repairing a part that is damaged during assembly should be done, not scrapping. This also applies to finished products that need minor repairs before being shipped.
-
Continuous Improvement (CI): CI aims to improve the efficiency of operations by continuously identifying problems and making changes in order to eliminate or minimize waste. Continuous Improvement involves continuous improvement of processes.