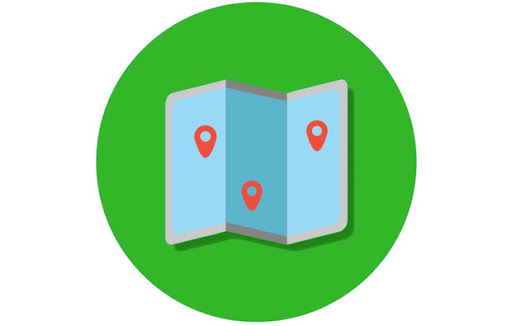
National Institute of Standards and Technology, which was founded in 1901 is one of the oldest US physical science laboratories. Its mission is to improve the quality of life and the productivity of American industries through science and technology. NIST, located in Gaithersburg (Maryland), is a part of the United States Department of Commerce. The NIST staff collaborates with federal agencies to develop standards and metrics that will improve productivity, economic security, and facilitate trade. NIST is an important partner in improving the U.S.'s industrial competitiveness as well as quality assurance.
NIST's mission aims to improve quality of life through scientific and technological innovation, the development and maintenance of national standards for physical measurement, as well as the promotion of innovation in U.S. industries. NIST has two locations in Gaithersburg, Maryland, and Boulder, Colorado. NIST creates standards, metrics, as well as best practices. NIST also researches to develop the technological infrastructure within the U.S.
The National Institute of Standards and Technology (NIST) was originally conceived as a metrology agency. In its early days, the Bureau of Standards concentrated on solving national problems related to science, technology and commerce. A variety of industries were served by standards, including electronics as well as electrical safety and automobile brake systems. The Bureau of Standards also operated a facility to produce optical glass, and worked on multiple problems during World War I.
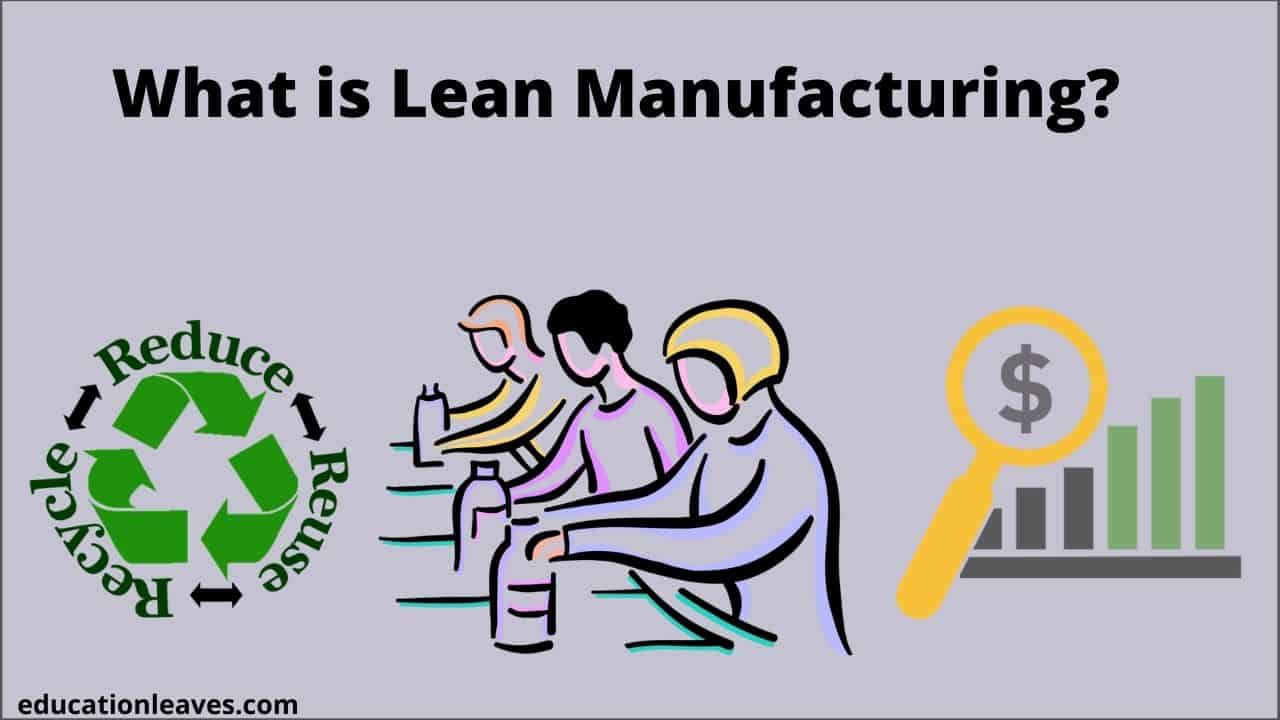
NIST also provides standards, metrics, best practices, and guidelines for a wide range of industries such as electronics, computers and transportation. NIST assists the industry to create procedures to improve manufacturing production. NIST also creates Federal Information Processing Standards (or FIPS), which are approved and maintained by the Secretary of Commerce.
Journal of Research of National Institute of Standards and Technology (official scientific journal of the National Institute of Standards and Technology) is also published by National Institute of Standards and Technology. The Nature Index contains information about NIST's research outputs. NIST is currently the largest North American research center.
1988 saw the National Bureau of Standards (NBS), reorganized under the name NIST. The name was meant to reflect NBS’s wide-ranging mission. On August 23, 1988, the Omnibus Trade and Competitiveness Act of88 was passed. It expanded NBS’s technical expertise and gave NIST more responsibilities. The law also explicitly affirmed traditional measurement services.
NIST will provide full-service measurement services. It will also extend its technology assistance and coordination of state extension services to federal technology transfer programs. It will expand its reach by working with existing delivery partners. It will also hold workshops on technological topics to ensure NIST resources are efficiently used.
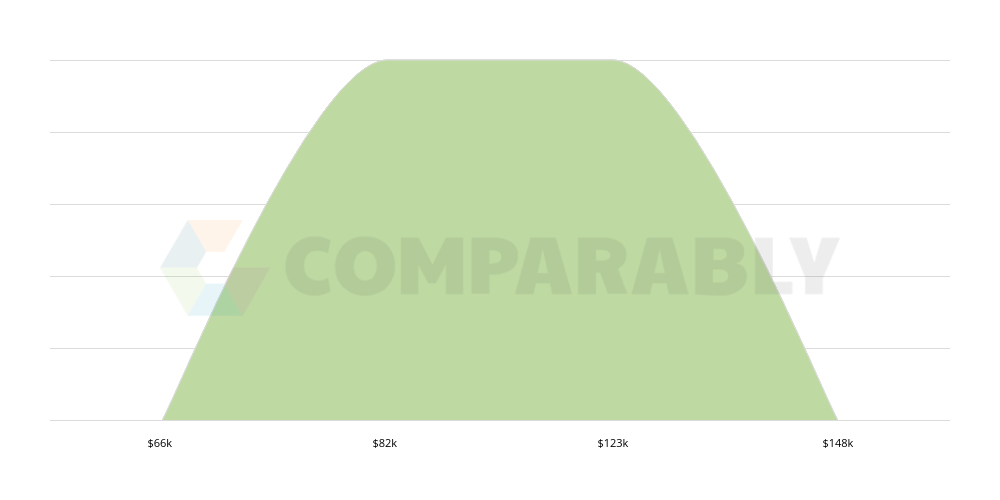
NIST will continue as a strategic partner to improve U.S. industrial competivity by providing American industries with technology, standards and best-practices. NIST helps federal agencies develop cost-effective programs. It has a strong focus on national security. Although its recommendations are not binding on the private sector, they provide a foundation for federal agencies.
FAQ
What are the 7 Rs of logistics?
The acronym 7R's for Logistics stands to represent the seven basic principles in logistics management. It was developed and published by the International Association of Business Logisticians in 2004 as part of the "Seven Principles of Logistics Management".
The acronym is composed of the following letters.
-
Responsible – ensure that all actions are legal and don't cause harm to anyone else.
-
Reliable: Have faith in your ability or the ability to honor any promises made.
-
Use resources effectively and sparingly.
-
Realistic – Consider all aspects, including cost-effectiveness as well as environmental impact.
-
Respectful - Treat people fairly and equitably
-
Responsive - Look for ways to save time and increase productivity.
-
Recognizable - Provide value-added services to customers
How can we increase manufacturing efficiency?
First, we need to identify which factors are most critical in affecting production times. We must then find ways that we can improve these factors. If you don’t know where to begin, consider which factors have the largest impact on production times. Once you've identified them, try to find solutions for each of those factors.
What skills should a production planner have?
To become a successful production planner, you need to be organized, flexible, and able to multitask. It is also important to be able communicate with colleagues and clients.
What are the four types of manufacturing?
Manufacturing refers the process of turning raw materials into useful products with machines and processes. It can involve many activities like designing, manufacturing, testing packaging, shipping, selling and servicing.
How can manufacturing reduce production bottlenecks?
Production bottlenecks can be avoided by ensuring that processes are running smoothly during the entire production process, starting with the receipt of an order and ending when the product ships.
This includes both planning for capacity and quality control.
The best way to do this is to use continuous improvement techniques such as Six Sigma.
Six Sigma can be used to improve the quality and decrease waste in all areas of your company.
It emphasizes consistency and eliminating variance in your work.
What can I do to learn more about manufacturing?
Hands-on experience is the best way to learn more about manufacturing. If that is not possible, you could always read books or view educational videos.
What is the responsibility of a logistics manager?
Logistics managers make sure all goods are delivered on schedule and without damage. This is done by using his/her experience and knowledge of the company's products. He/she must also ensure sufficient stock to meet the demand.
Statistics
- According to the United Nations Industrial Development Organization (UNIDO), China is the top manufacturer worldwide by 2019 output, producing 28.7% of the total global manufacturing output, followed by the United States, Japan, Germany, and India.[52][53] (en.wikipedia.org)
- In 2021, an estimated 12.1 million Americans work in the manufacturing sector.6 (investopedia.com)
- In the United States, for example, manufacturing makes up 15% of the economic output. (twi-global.com)
- It's estimated that 10.8% of the U.S. GDP in 2020 was contributed to manufacturing. (investopedia.com)
- According to a Statista study, U.S. businesses spent $1.63 trillion on logistics in 2019, moving goods from origin to end user through various supply chain network segments. (netsuite.com)
External Links
How To
How to use the Just-In Time Method in Production
Just-intime (JIT), which is a method to minimize costs and maximize efficiency in business process, is one way. This is where you have the right resources at the right time. This means that only what you use is charged to your account. Frederick Taylor was the first to coin this term. He developed it while working as a foreman during the early 1900s. After observing how workers were paid overtime for late work, he realized that overtime was a common practice. He concluded that if workers were given enough time before they start work, productivity would increase.
The idea behind JIT is that you should plan ahead and have everything ready so you don't waste money. It is important to look at your entire project from beginning to end and ensure that you have enough resources to handle any issues that may arise. You will have the resources and people to solve any problems you anticipate. You won't have to pay more for unnecessary items.
There are many JIT methods.
-
Demand-driven: This type of JIT allows you to order the parts/materials required for your project on a regular basis. This will allow you to track how much material you have left over after using it. This will allow to you estimate the time it will take for more to be produced.
-
Inventory-based: This is a type where you stock the materials required for your projects in advance. This allows you to forecast how much you will sell.
-
Project-driven : This is a method where you make sure that enough money is set aside to pay the project's cost. Once you have an idea of how much material you will need, you can purchase the necessary materials.
-
Resource-based: This is the most common form of JIT. Here, you allocate certain resources based on demand. You might assign more people to help with orders if there are many. If there aren't many orders, you will assign fewer people.
-
Cost-based: This is a similar approach to resource-based but you are not only concerned with how many people you have, but also how much each one costs.
-
Price-based: This approach is very similar to the cost-based method except that you don't look at individual workers costs but the total cost of the company.
-
Material-based: This approach is similar to cost-based. However, instead of looking at the total cost for the company, you look at how much you spend on average on raw materials.
-
Time-based: This is another variation of resource-based JIT. Instead of focusing on the cost of each employee, you will focus on the time it takes to complete a project.
-
Quality-based: This is yet another variation of resource-based JIT. Instead of thinking about how much each employee costs or how long it takes to manufacture something, you think about how good the quality of your product is.
-
Value-based JIT is the newest form of JIT. This is where you don't care about how the products perform or whether they meet customers' expectations. Instead, you're focused on how much value you add to the market.
-
Stock-based is an inventory-based system that measures the number of items produced at any given moment. This method is useful when you want to increase production while decreasing inventory.
-
Just-in-time planning (JIT): This is a combination JIT and supply-chain management. It refers to the process of scheduling the delivery of components as soon as they are ordered. It reduces lead times and improves throughput.