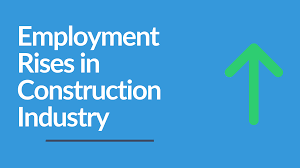
Amazon is seeking Supply Chain Managements with proven track records and senior leadership experience to oversee strategic cross-functional operations. These positions will work closely with business teams worldwide and oversee new products, operations, and projects. They will create cross-functional teams to manage large-scale project management across multiple organizations.
Manager of the purchasing and supply chain
An Amazon Purchasing and supply chain manager has a variety of duties and responsibilities, including driving cost savings, optimizing processes, mitigating risk, and establishing consistent service offerings across the globe. These duties require strong negotiation and analytical skills.
The ideal candidate for this position is a self-starter who has strong communication and attention to detail. She or he should also be able to work autonomously, meet tight deadlines, and manage her workload effectively.
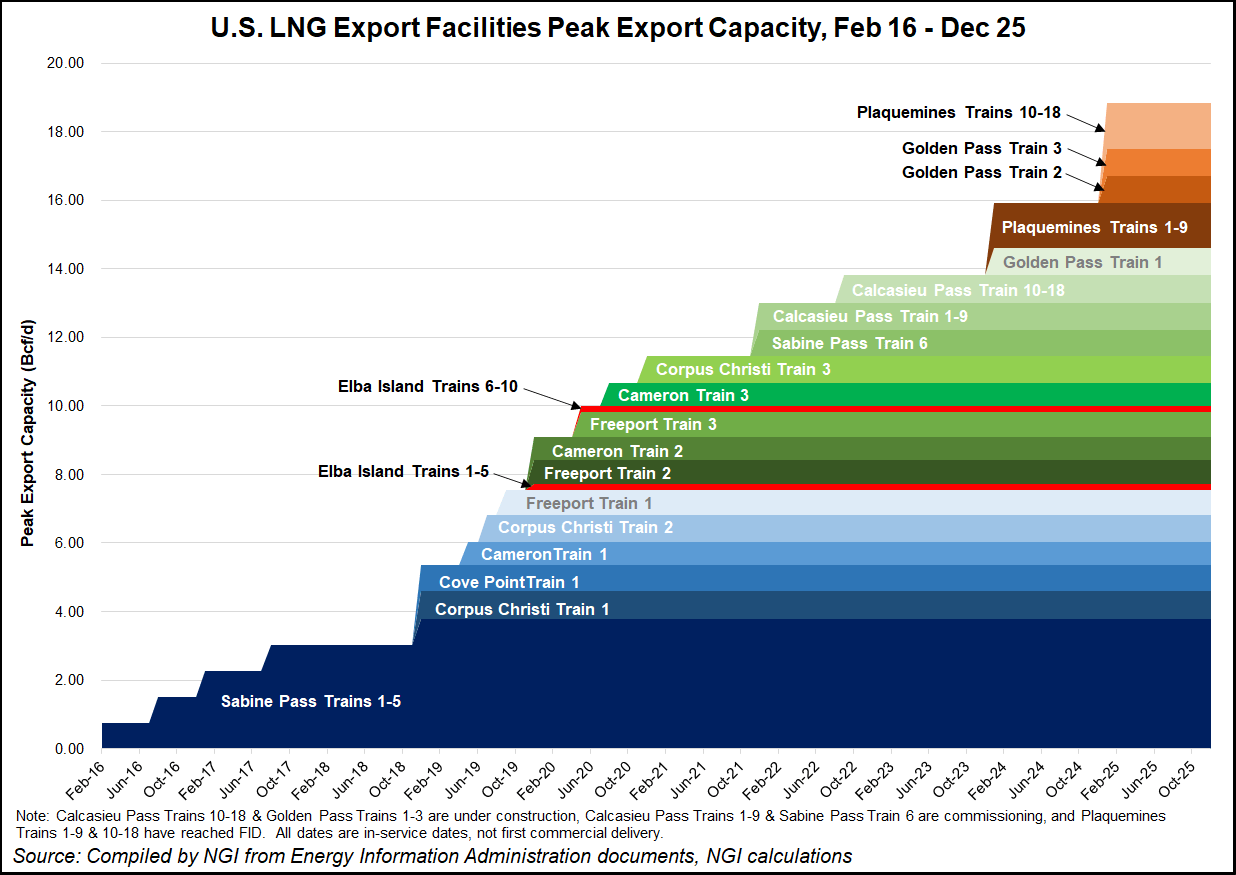
Cost analyst
Amazon's supply chain plays an important role in its success. It covers fulfillment, transportation, as well forecasting. You must be a skilled analyst with a passion to detail. The person will use data analysis to help understand the company's operation. This analyst will interact with global stakeholders to interpret data and draw conclusion. For their analysis, they can use MS Excel (or SQL).
Amazon's supply chain is among the most innovative in the entire world. Amazon is continually investing in warehouse technology, trucking capabilities, and more. Amazon is also expanding its investments in drones, cargo planes, and other technologies.
Program manager
Program manager Amazon supply chain jobs require a high level of knowledge in the areas of supply chain planning, manufacturing, and logistics. In addition, a successful applicant will be able to integrate across a team and make data-driven decisions. Additionally, the successful applicant will be required to manage and build systems and processes for quality control, scale, and risk management.
The salary of a Supply Chain Program Director varies depending upon the city where the job is located. Some people earn more than $168,000 per year while others make as low as $52,500. On average, Program managers earn between $87,500 and $127,500 annually. Salary ranges can vary from $87,500 to $127,500 depending on the location they are working in and their level of experience.
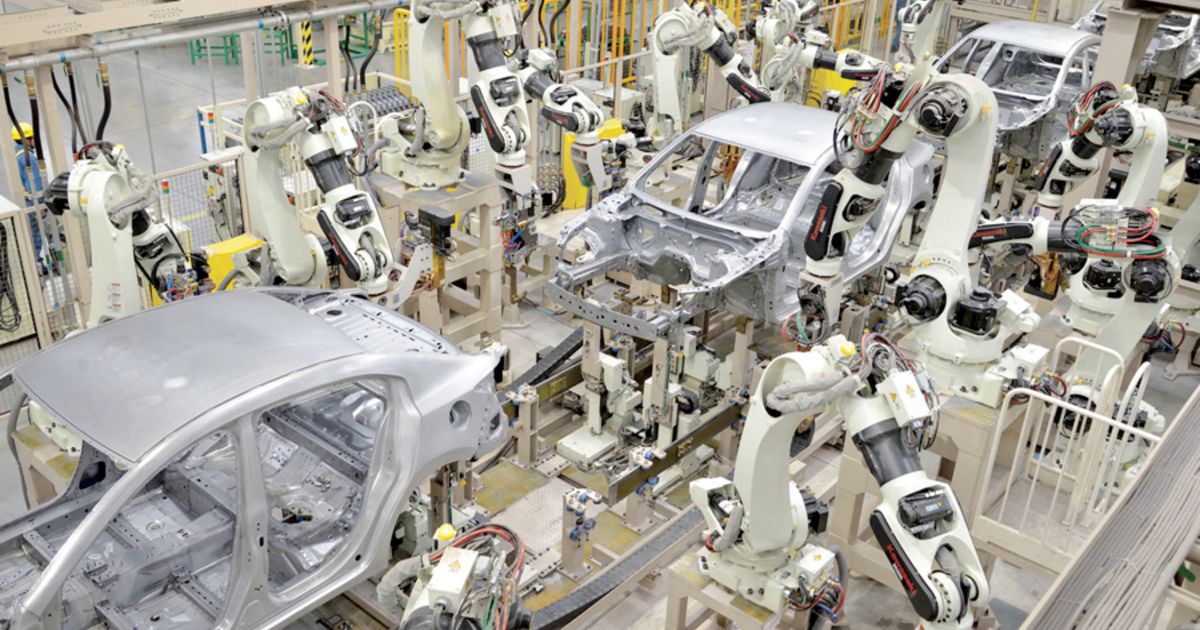
Warehouse manager
Warehouse management positions are in high demand and they are growing in demand. Although there is no requirement for a warehouse manager to have a degree, employers will prefer someone with some experience. While a bachelor's degree is not necessary for this job, it will increase your chances to get a job.
Warehouse managers have many responsibilities, including customer service and inventory management. They also have a huge impact on the experience for shippers and operators. These people are responsible for ensuring the success of the entire supply chain. They also develop efficiency-enhancing initiatives. They also have the chance to work alongside multiple Amazon teams to gain exposure to their operations.
FAQ
What's the difference between Production Planning & Scheduling?
Production Planning (PP) refers to the process of determining how much production is needed at any given moment. Forecasting and identifying production capacity are two key elements to this process.
Scheduling involves the assignment of dates and times to tasks in order to complete them within the timeframe.
What do we need to know about Manufacturing Processes in order to learn more about Logistics?
No. No. Knowing about manufacturing processes will help you understand how logistics works.
What are the jobs in logistics?
There are many kinds of jobs available within logistics. Here are some:
-
Warehouse workers - They load and unload trucks and pallets.
-
Transportation drivers - They drive trucks and trailers to deliver goods and carry out pick-ups.
-
Freight handlers, - They sort out and pack freight in warehouses.
-
Inventory managers – They manage the inventory in warehouses.
-
Sales reps - They sell products and services to customers.
-
Logistics coordinators - They organize and plan logistics operations.
-
Purchasing agents - They buy goods and services that are necessary for company operations.
-
Customer service representatives – They answer emails and phone calls from customers.
-
Shipping clerks - They process shipping orders and issue bills.
-
Order fillers: They fill orders based off what has been ordered and shipped.
-
Quality control inspectors (QCI) - They inspect all incoming and departing products for potential defects.
-
Others - There is a variety of other jobs in logistics. These include transportation supervisors and cargo specialists.
How can manufacturing reduce production bottlenecks?
The key to avoiding bottlenecks in production is to keep all processes running smoothly throughout the entire production cycle, from the time you receive an order until the time when the product ships.
This includes both planning for capacity and quality control.
Continuous improvement techniques such Six Sigma can help you achieve this.
Six Sigma is a management system used to improve quality and reduce waste in every aspect of your organization.
It is focused on creating consistency and eliminating variation in your work.
What is the role of a production manager?
Production planners ensure all aspects of the project are delivered within time and budget. They make sure that the product and services meet client expectations.
How can I find out more about manufacturing?
Practical experience is the best way of learning about manufacturing. You can read books, or watch instructional videos if you don't have the opportunity to do so.
What does it take to run a logistics business?
You need to have a lot of knowledge and skills to manage a successful logistic business. Effective communication skills are necessary to work with suppliers and clients. It is important to be able to analyse data and draw conclusions. You must be able and able to handle stress situations and work under pressure. To improve efficiency, you must be innovative and creative. You will need strong leadership skills to motivate and direct your team members towards achieving their organizational goals.
It is important to be organized and efficient in order to meet tight deadlines.
Statistics
- Many factories witnessed a 30% increase in output due to the shift to electric motors. (en.wikipedia.org)
- It's estimated that 10.8% of the U.S. GDP in 2020 was contributed to manufacturing. (investopedia.com)
- (2:04) MTO is a production technique wherein products are customized according to customer specifications, and production only starts after an order is received. (oracle.com)
- According to the United Nations Industrial Development Organization (UNIDO), China is the top manufacturer worldwide by 2019 output, producing 28.7% of the total global manufacturing output, followed by the United States, Japan, Germany, and India.[52][53] (en.wikipedia.org)
- Job #1 is delivering the ordered product according to specifications: color, size, brand, and quantity. (netsuite.com)
External Links
How To
How to use Lean Manufacturing in the production of goods
Lean manufacturing is a management system that aims at increasing efficiency and reducing waste. It was created in Japan by Taiichi Ohno during the 1970s and 80s. He received the Toyota Production System award (TPS), from Kanji Toyoda, founder of TPS. Michael L. Watkins published the book "The Machine That Changed the World", which was the first to be published about lean manufacturing.
Lean manufacturing is often described as a set if principles that help improve the quality and speed of products and services. It is about eliminating defects and waste from all stages of the value stream. Lean manufacturing is also known as just in time (JIT), zero defect total productive maintenance(TPM), and five-star (S). Lean manufacturing is about eliminating activities that do not add value, such as inspection, rework, and waiting.
Lean manufacturing can help companies improve their product quality and reduce costs. Additionally, it helps them achieve their goals more quickly and reduces employee turnover. Lean manufacturing can be used to manage all aspects of the value chain. Customers, suppliers, distributors, retailers and employees are all included. Lean manufacturing is widely used in many industries. Toyota's philosophy has been a key driver of success in many industries, including automobiles and electronics.
Lean manufacturing includes five basic principles:
-
Define Value - Determine the value that your business brings to society. Also, identify what sets you apart from your competitors.
-
Reduce Waste - Remove any activity which doesn't add value to your supply chain.
-
Create Flow. Ensure that your work is uninterrupted and flows seamlessly.
-
Standardize and simplify – Make processes as repeatable and consistent as possible.
-
Build Relationships- Develop personal relationships with both internal as well as external stakeholders.
Lean manufacturing is not a new concept, but it has been gaining popularity over the last few years due to a renewed interest in the economy following the global financial crisis of 2008. Many businesses have adopted lean production techniques to make them more competitive. According to some economists, lean manufacturing could be a significant factor in the economic recovery.
Lean manufacturing is now becoming a common practice in the automotive industry, with many benefits. These include improved customer satisfaction, reduced inventory levels, lower operating costs, increased productivity, and better overall safety.
The principles of lean manufacturing can be applied in almost any area of an organization. Because it makes sure that all value chains are efficient and effectively managed, Lean Manufacturing is particularly helpful for organizations.
There are three types principally of lean manufacturing:
-
Just-in-Time Manufacturing: Also known as "pull systems", this type of lean manufacturing uses just-in-time manufacturing (JIT). JIT refers to a system in which components are assembled at the point of use instead of being produced ahead of time. This strategy aims to decrease lead times, increase availability of parts and reduce inventory.
-
Zero Defects Manufacturing - ZDM: ZDM focuses its efforts on making sure that no defective units leave a manufacturing facility. Repairing a part that is damaged during assembly should be done, not scrapping. This applies to finished products, which may need minor repairs before they are shipped.
-
Continuous Improvement: Continuous Improvement aims to improve efficiency by continually identifying problems and making adjustments to eliminate or minimize waste. It involves continuous improvement of processes, people, and tools.