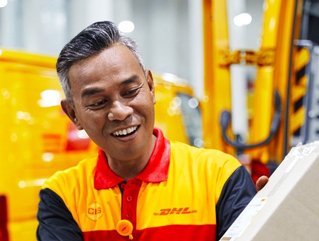
Amazon is seeking Supply Chain Managements with proven track records and senior leadership experience to oversee strategic cross-functional operations. These positions will oversee projects to support new products and operations while working closely with business teams around the world. They will develop cross-functional project teams and manage large-scale projects across multiple organizations.
Manager, Supply Chain and Purchasing
Amazon Purchasing and Supply chain managers have a range of responsibilities. They are responsible for driving cost savings and optimizing processes. These responsibilities also require strong analytical and negotiation skills, as well as strong communication skills.
The ideal candidate for this position is a self-starter who has strong communication and attention to detail. He or she should be able work independently, meet tight deadlines and manage their workload well.
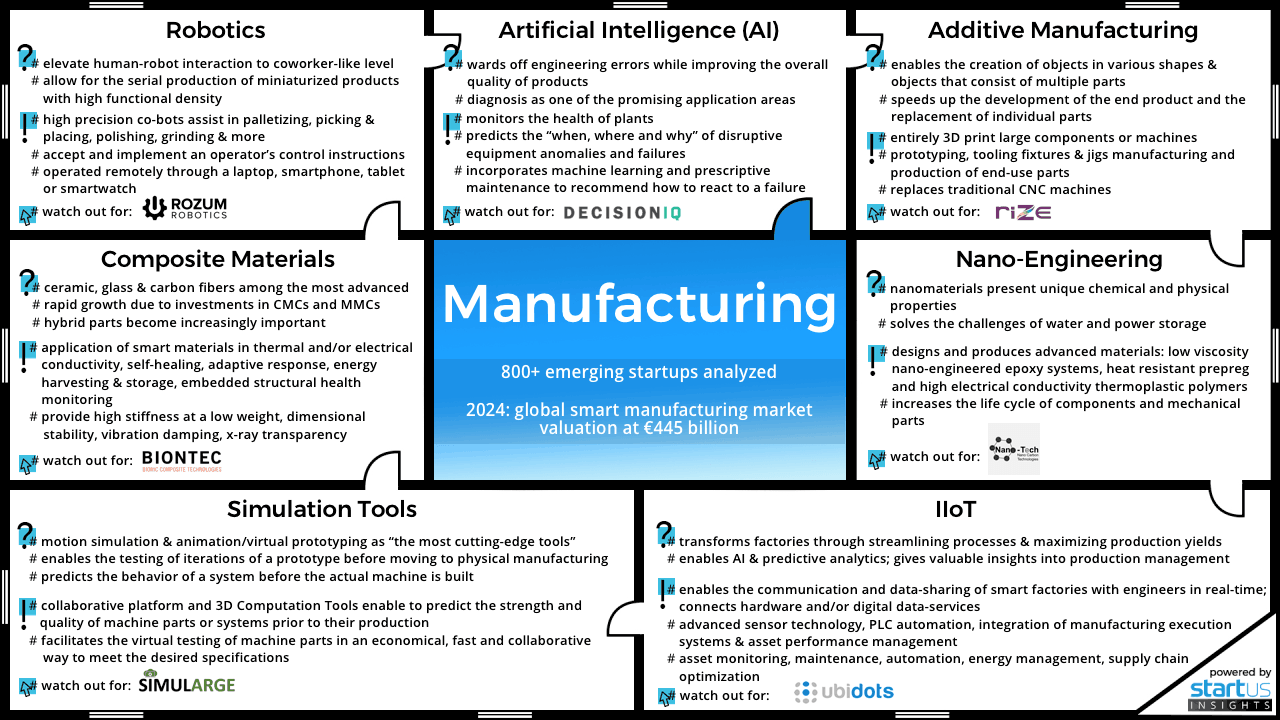
Cost analyst
Amazon's supply chains are an integral part of its success. It involves all aspects of fulfillment, transportation, and forecasting. It requires a highly analytical person with a passion for details. This person will use data analytics to make sense of the company's operations. An analyst will work closely with global stakeholders to interpret data, draw conclusions and make recommendations. For their analysis they might use MS Excel or SQL.
Amazon's supply chain has been one of the most innovative around. Amazon is investing heavily in warehouse technology and trucking capabilities. Amazon is also investing in drones as well as cargo planes.
Program manager
Amazon supply chain program manager jobs require high levels of knowledge in logistics, supply chain planning, and manufacturing. The successful candidate will also have the ability to work in a team and take data-driven decisions. The successful candidate will also need to develop and maintain systems and processes for scale and quality control as well as risk management.
The salary for a Supply Chain Program manager varies greatly depending on the location. Some people earn more than $168,000 per year while others make as low as $52,500. On average, Program managers earn between $87,500 and $127,500 annually. However, salaries can vary by nearly $40,000 depending on the region in which they work and the amount of experience they have.
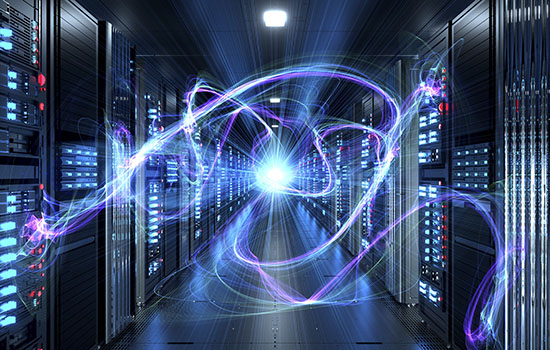
Warehouse manager
Warehouse management positions are in high demand and they are growing in demand. Although there are no requirements for warehouse managers, most employers prefer employees with experience. Although a bachelor's degree does not guarantee employment, it can increase your chances of landing a job.
Warehouse managers have many responsibilities, including customer service and inventory management. They also have an impact on shippers' and operators' experience. They manage the supply chain performance and create initiatives to increase efficiency. They have the opportunity to work with several Amazon teams, and to be exposed to their operations.
FAQ
What are the products and services of logistics?
Logistics are the activities involved in moving goods from point A to point B.
They cover all aspects of transportation, such as packing, loading, transporting and unloading.
Logisticians ensure that products reach the right destination at the right moment and under safe conditions. Logisticians help companies improve their supply chain efficiency by providing information about demand forecasts and stock levels, production schedules, as well as availability of raw materials.
They monitor shipments in transit, ensure quality standards, manage inventories, replenish orders, coordinate with suppliers and other vendors, and offer support services for sales, marketing, and customer service.
How does manufacturing avoid bottlenecks in production?
The key to avoiding bottlenecks in production is to keep all processes running smoothly throughout the entire production cycle, from the time you receive an order until the time when the product ships.
This includes both quality control and capacity planning.
Continuous improvement techniques such Six Sigma are the best method to accomplish this.
Six Sigma is a management system used to improve quality and reduce waste in every aspect of your organization.
It is focused on creating consistency and eliminating variation in your work.
What is the distinction between Production Planning or Scheduling?
Production Planning (PP), is the process of deciding what production needs to take place at any given time. Forecasting demand is one way to do this.
Scheduling refers to the process of allocating specific dates to tasks in order that they can be completed within a specified timeframe.
What is the job of a manufacturer manager?
A manufacturing manager must ensure that all manufacturing processes are efficient and effective. They should also be aware and responsive to any company problems.
They must also be able to communicate with sales and marketing departments.
They should be up to date on the latest trends and be able apply this knowledge to increase productivity and efficiency.
What skills are required to be a production manager?
Production planners must be flexible, organized, and able handle multiple tasks. You must also be able to communicate effectively with clients and colleagues.
What is the responsibility of a production planner?
A production planner makes sure all project elements are delivered on schedule, within budget, as well as within the agreed scope. They also ensure that the product/service meets the client’s needs.
What types of jobs can you find in logistics
There are many jobs available in logistics. Here are some:
-
Warehouse workers – They load, unload and transport pallets and trucks.
-
Transportation drivers – These drivers drive trucks and wagons to transport goods and pick up the goods.
-
Freight handlers, - They sort out and pack freight in warehouses.
-
Inventory managers – They manage the inventory in warehouses.
-
Sales reps - They sell products and services to customers.
-
Logistics coordinators: They plan and manage logistics operations.
-
Purchasing agents are those who purchase goods and services for the company.
-
Customer service representatives - Answer calls and email from customers.
-
Shipping clerks: They process shipping requests and issue bills.
-
Order fillers - These people fill orders based on what has been ordered.
-
Quality control inspectors: They inspect outgoing and incoming products for any defects.
-
Other - Logistics has many other job opportunities, including transportation supervisors, logistics specialists, and cargo specialists.
Statistics
- You can multiply the result by 100 to get the total percent of monthly overhead. (investopedia.com)
- [54][55] These are the top 50 countries by the total value of manufacturing output in US dollars for its noted year according to World Bank.[56] (en.wikipedia.org)
- According to the United Nations Industrial Development Organization (UNIDO), China is the top manufacturer worldwide by 2019 output, producing 28.7% of the total global manufacturing output, followed by the United States, Japan, Germany, and India.[52][53] (en.wikipedia.org)
- Many factories witnessed a 30% increase in output due to the shift to electric motors. (en.wikipedia.org)
- In 2021, an estimated 12.1 million Americans work in the manufacturing sector.6 (investopedia.com)
External Links
How To
Six Sigma: How to Use it in Manufacturing
Six Sigma can be described as "the use of statistical process control (SPC), techniques to achieve continuous improvement." Motorola's Quality Improvement Department developed it at their Tokyo plant in Japan in 1986. Six Sigma's main goal is to improve process quality by standardizing processes and eliminating defects. Since there are no perfect products, or services, this approach has been adopted by many companies over the years. Six Sigma seeks to reduce variation between the mean production value. If you take a sample and compare it with the average, you will be able to determine how much of the production process is different from the norm. If this deviation is too big, you know something needs fixing.
Understanding how variability works in your company is the first step to Six Sigma. Once you've understood that, you'll want to identify sources of variation. Also, you will need to identify the sources of variation. Random variations are caused by human errors. Systematic variations can be caused by outside factors. Random variations would include, for example, the failure of some widgets to fall from the assembly line. You might notice that your widgets always fall apart at the same place every time you put them together.
Once you have identified the problem, you can design solutions. It might mean changing the way you do business or redesigning it entirely. You should then test the changes again after they have been implemented. If they don't work, you will need to go back to the drawing boards and create a new plan.