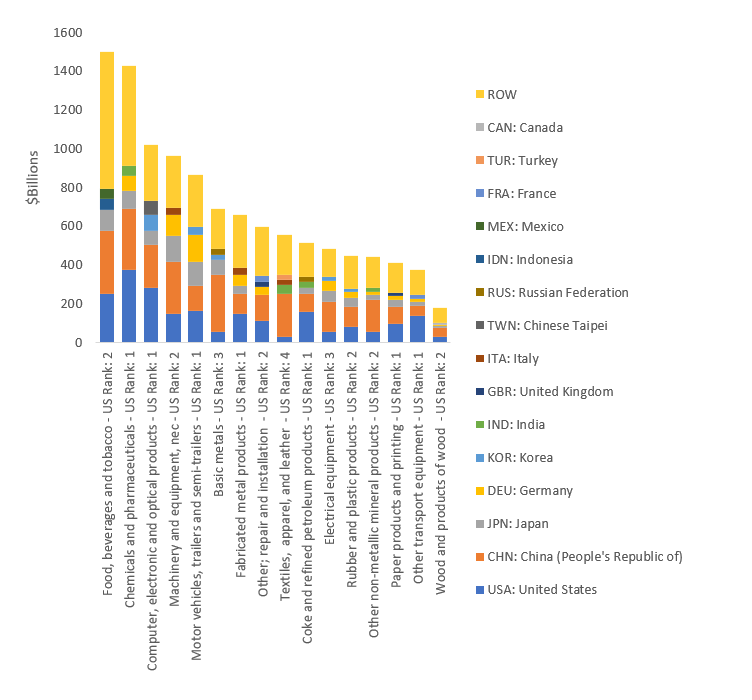
It is important that you include all the duties in the job description to attract the best people for transport and logistic jobs. These duties may include ordering raw materials or filling out company paperwork. This can make the job description more appealing but it could also lead to the hiring of the wrong person. This can be a problem for both your business and your customers. It also means that you have to spend time and money training the new employee.
Job description
Logistics and transport professionals work in many industries to move goods and people from one place to the next. Some professionals work in shipping. Others may be involved with road maintenance. This job involves monitoring traffic congestion and ensuring products are safe. This field requires that workers adapt to changing business requirements and work in multiple locations.
An effective job description should focus on the required skills and training needed for a particular job. However, it should also reflect the company's culture. The job description should state whether the position will be permanent, temporary, or self-employed.
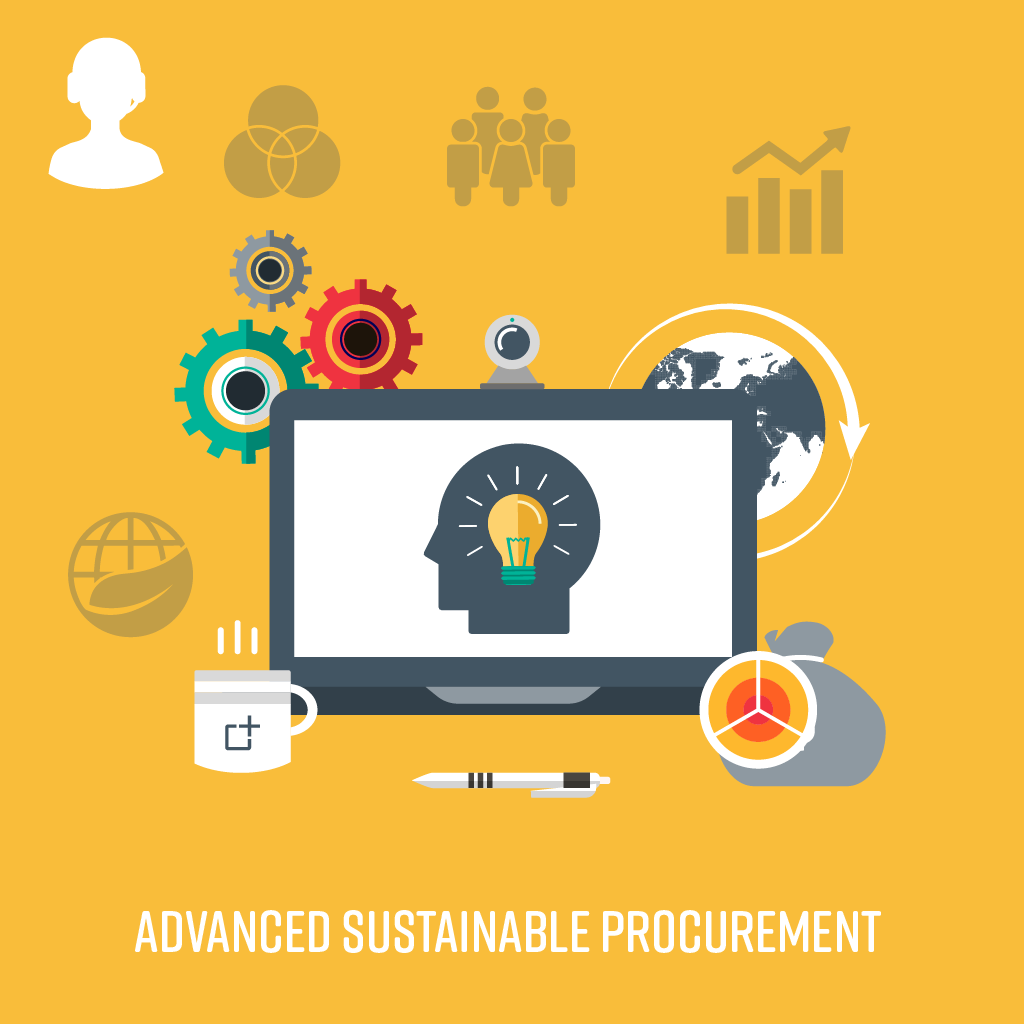
Salary
You can find a wide range of jobs in transportation and logistics, starting at entry level to more senior positions. Salary levels can vary depending on experience and industry. The average salary for entry-level positions is $40,000 annually. However, these salaries can rise and there is room to grow.
Transportation and logistics careers offer a wide range of salaries, with some being more lucrative than others. Although entry-level salaries might be lower than other fields, experienced workers can earn significantly more. Some companies offer in house training, or even pay for graduate education.
Requirements
Logistics and transportation jobs are highly sought-after in many industries. They require high levels of expertise. The primary goal of these jobs is to ensure that goods are delivered on time and at the lowest cost. Therefore, it is important for companies that they recruit the right staff. While junior staff may not need any prior training, those wishing to take up a senior position should have relevant qualifications, such as a Supply Chain Practitioner Advanced Apprenticeship, or Chartered Institute of Logistics and Transport accredited certifications.
A degree in transportation and logistics is an important step to take if you want to pursue a career in this field. There are many courses that can help you improve your skills and knowledge. For new entrants in the field, the Chartered Institute of Logistics and Transport UK offers a Level 2-certificate in Transport and Logistics. A graduate recruitment program, offered by large logistics companies, can provide valuable work experience.
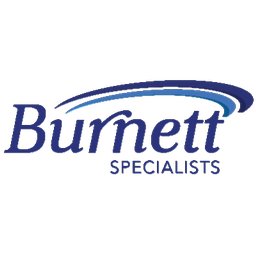
Localities
The career opportunities in logistics and transport are varied. Many of these jobs require the ability to plan and evaluate different distribution methods. These jobs require advanced analytical thinking and the ability handle complex data. It is also important to have good communication skills. You may need to travel to remote areas for some jobs. There are many graduate training programs in logistics and transport that will equip you with the skills necessary to be successful in this field. Some of these programmes will also provide you with paid internships.
Transport and logistics occupations are in great demand. They are expected to increase by 3% from 2019-2029, the same as the national median. However, certain jobs are expected to see higher growth than the average, such as commercial and airline pilots. Other jobs in this sector include driver/sales workers and delivery truck drivers.
FAQ
What is manufacturing and logistics?
Manufacturing refers to the process of making goods using raw materials and machines. Logistics manages all aspects of the supply chain, including procurement, production planning and distribution, inventory control, transportation, customer service, and transport. Manufacturing and logistics can often be grouped together to describe a larger term that covers both the creation of products, and the delivery of them to customers.
Do we need to know about Manufacturing Processes before learning about Logistics?
No. No. However, knowing about manufacturing processes will definitely give you a better understanding of how logistics works.
How can I find out more about manufacturing?
Practical experience is the best way of learning about manufacturing. But if that is not possible you can always read books and watch educational videos.
What is production management?
Production Planning is the creation of a plan to cover all aspects, such as scheduling, budgeting. Location, crew, equipment, props and other details. This document ensures that everything is prepared and available when you are ready for shooting. This document should include information about how to achieve the best results on-set. This includes location information, crew details, equipment specifications, and casting lists.
First, you need to plan what you want to film. You may have already chosen the location you want, or there are locations or sets you prefer. Once you have identified your locations and scenes it's time to begin figuring out what elements you will need for each one. For example, you might decide that you need a car but don't know exactly what model you want. If this is the case, you might start searching online for car models and then narrow your options by selecting from different makes.
After you have chosen the right car, you will be able to begin thinking about accessories. Do you need people sitting in the front seats? You might also need someone to help you get around the back. Perhaps you would like to change the interior colour from black to white. These questions will help you determine the exact look and feel of your car. Another thing you can do is think about what type of shots are desired. You will be filming close-ups and wide angles. Perhaps you want to show the engine or the steering wheel? These details will help identify the exact car you wish to film.
Once you have established all the details, you can create a schedule. You can create a schedule that will outline when you must start and finish your shoots. You will need to know when you have to be there, what time you have to leave and when your return home. Everyone knows exactly what they should do and when. It is possible to make arrangements in advance for additional staff if you are looking to hire. You don't want to hire someone who won't show up because he didn't know.
When creating your schedule, you will also need to consider the number of days you need to film. Some projects can be completed in a matter of days or weeks. Others may take several days. While creating your schedule, it is important to remember whether you will require more than one shot per day. Shooting multiple takes over the same location will increase costs and take longer to complete. If you aren't sure whether you need multiple shots, it is best to take fewer photos than you would like.
Another important aspect of production planning is setting budgets. You will be able to manage your resources if you have a realistic budget. You can always lower the budget if you encounter unexpected problems. However, you shouldn't overestimate the amount of money you will spend. You'll end up with less money after paying for other things if the cost is underestimated.
Production planning can be a complex process. However, once you know how everything works together it will become easier to plan future projects.
What is the difference between Production Planning, Scheduling and Production Planning?
Production Planning (PP) is the process of determining what needs to be produced at any given point in time. Forecasting demand is one way to do this.
Scheduling refers the process by which tasks are assigned dates so that they can all be completed within the given timeframe.
What does manufacturing mean?
Manufacturing Industries is a group of businesses that produce goods for sale. Consumers are those who purchase these products. These companies employ many processes to achieve this purpose, such as production and distribution, retailing, management and so on. These companies produce goods using raw materials and other equipment. This includes all types of manufactured goods, including food items, clothing, building supplies, furniture, toys, electronics, tools, machinery, vehicles, pharmaceuticals, medical devices, chemicals, and many others.
Statistics
- According to a Statista study, U.S. businesses spent $1.63 trillion on logistics in 2019, moving goods from origin to end user through various supply chain network segments. (netsuite.com)
- (2:04) MTO is a production technique wherein products are customized according to customer specifications, and production only starts after an order is received. (oracle.com)
- [54][55] These are the top 50 countries by the total value of manufacturing output in US dollars for its noted year according to World Bank.[56] (en.wikipedia.org)
- You can multiply the result by 100 to get the total percent of monthly overhead. (investopedia.com)
- Job #1 is delivering the ordered product according to specifications: color, size, brand, and quantity. (netsuite.com)
External Links
How To
Six Sigma in Manufacturing
Six Sigma is defined as "the application of statistical process control (SPC) techniques to achieve continuous improvement." It was developed by Motorola's Quality Improvement Department at their plant in Tokyo, Japan, in 1986. Six Sigma's main goal is to improve process quality by standardizing processes and eliminating defects. Since there are no perfect products, or services, this approach has been adopted by many companies over the years. Six Sigma's primary goal is to reduce variation from the average value of production. This means that you can take a sample from your product and then compare its performance to the average to find out how often the process differs from the norm. If the deviation is excessive, it's likely that something needs to be fixed.
Understanding how variability works in your company is the first step to Six Sigma. Once you have a good understanding of the basics, you can identify potential sources of variation. This will allow you to decide if these variations are random and systematic. Random variations happen when people make errors; systematic variations are caused externally. These are, for instance, random variations that occur when widgets are made and some fall off the production line. If however, you notice that each time you assemble a widget it falls apart in exactly the same spot, that is a problem.
Once you identify the problem areas, it is time to create solutions. The solution could involve changing how you do things, or redesigning your entire process. Once you have implemented the changes, it is important to test them again to ensure they work. If they don't work you need to rework them and come up a better plan.