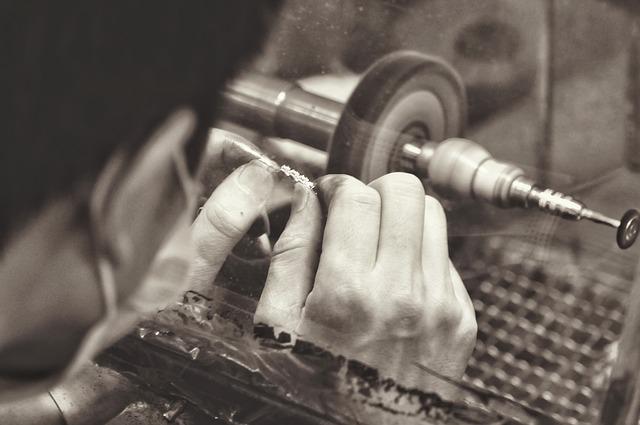
Towson University can be found on Maryland's eastern coast. This business school has won international recognition. Towson University is one of a few institutions that has been accredited by AACSB International as well as the Association to Advance Collegiate Schools of Business. Students who have achieved these certifications are recognized by businesses as having the right skills to succeed.
As one of the nation's top public universities, Towson has received recognition for its undergraduate business program. U.S. News & World Report ranked this business program among the best in the country. The school's high graduation rate was also acknowledged. The College of Business and Economics aims to provide students with the skills and tools they need for success. It is a prominent business program in Maryland and one of the largest in Maryland.
The business school also provides students with an entrepreneurship program, which teaches students how to identify new opportunities, develop strategies, and bring innovations to life. Towson also offers internship opportunities. Internships allow students to get valuable experience in the real workplace.
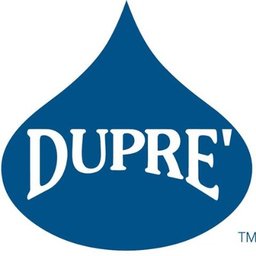
Towson University's business school offers students a bachelor's degree in business administration. Students must maintain a minimum GPA of 2.7 in each of the required courses to be eligible for this program. Students who are accepted may take the required courses to complete their major. Students can also choose to specialize in leadership, management, entrepreneurship or international business.
Students have the opportunity to intern at real businesses. It is a great way to get valuable experience. Students can choose to work for a variety companies in the Northeastern area. B-Local Mid-Atlantic partners with the school to allow students to work at local businesses. These internships give students valuable experiences and the chance to use what they have learned in the classroom.
International Business Concentration: This concentration requires students take courses in international business, international organizational behavior and multinational management. Students must also complete a capstone course in strategic management that allows them the opportunity to create solutions for real companies.
The core component of the business school curriculum is the Sellinger Experiential Learning Lab. This lab helps students learn data analysis, executive leadership decision making and research skills. To help students understand the business world, the lab makes use of Bloomberg terminals as well as other technological tools.
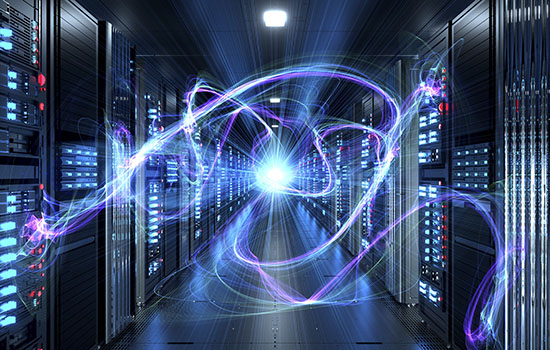
Towson University's management course helps students transform from analyst to integrator. Through the program, students learn how to analyze data, evaluate trends, and develop strategies. This program prepares students to work in finance, management, or business development. Students are also challenged in the development of new product concepts. Students learn how best to market their products.
Towson's business school offers a leading program to prepare students for careers as managers and financial analysts. The school's faculty members are outstanding scholars who are active in business and scholarly research. Faculty also serve as caring mentors, and advisers.
FAQ
What are the responsibilities of a logistic manager?
Logistics managers make sure all goods are delivered on schedule and without damage. This is done by using his/her experience and knowledge of the company's products. He/she should make sure that enough stock is on hand to meet the demands.
How can I find out more about manufacturing?
You can learn the most about manufacturing by getting involved in it. However, if that's not possible, you can always read books or watch educational videos.
What is the difference between Production Planning and Scheduling?
Production Planning (PP), or production planning, is the process by which you determine what products are needed at any given time. Forecasting and identifying production capacity are two key elements to this process.
Scheduling is the process of assigning specific dates to tasks so they can be completed within the specified timeframe.
Statistics
- You can multiply the result by 100 to get the total percent of monthly overhead. (investopedia.com)
- Job #1 is delivering the ordered product according to specifications: color, size, brand, and quantity. (netsuite.com)
- (2:04) MTO is a production technique wherein products are customized according to customer specifications, and production only starts after an order is received. (oracle.com)
- According to the United Nations Industrial Development Organization (UNIDO), China is the top manufacturer worldwide by 2019 output, producing 28.7% of the total global manufacturing output, followed by the United States, Japan, Germany, and India.[52][53] (en.wikipedia.org)
- [54][55] These are the top 50 countries by the total value of manufacturing output in US dollars for its noted year according to World Bank.[56] (en.wikipedia.org)
External Links
How To
Six Sigma: How to Use it in Manufacturing
Six Sigma is "the application statistical process control (SPC), techniques for continuous improvement." Motorola's Quality Improvement Department, Tokyo, Japan, developed it in 1986. The basic idea behind Six Sigma is to improve quality by improving processes through standardization and eliminating defects. Many companies have adopted Six Sigma in recent years because they believe that there are no perfect products and services. The main goal of Six Sigma is to reduce variation from the mean value of production. If you take a sample and compare it with the average, you will be able to determine how much of the production process is different from the norm. If it is too large, it means that there are problems.
Understanding the nature of variability in your business is the first step to Six Sigma. Once you understand this, you can then identify the causes of variation. This will allow you to decide if these variations are random and systematic. Random variations happen when people make errors; systematic variations are caused externally. If you make widgets and some of them end up on the assembly line, then those are considered random variations. If however, you notice that each time you assemble a widget it falls apart in exactly the same spot, that is a problem.
Once you've identified where the problems lie, you'll want to design solutions to eliminate those problems. The solution could involve changing how you do things, or redesigning your entire process. To verify that the changes have worked, you need to test them again. If they don't work you need to rework them and come up a better plan.